15 Types of Warehouse Robotics For Optimal Efficiency
Robots are proving their worth in high-speed warehouse operations by boosting productivity, keeping your employees safe and optimizing space in your facility.
We’ll share all you need to know about warehouse robotics, including the types, benefits and the order fulfillment processes they can help with. Plus, we’ll introduce you to our automated warehouse robots at Modula.
What Are Warehouse Robotics?
Warehouse robotics are machines that can perform different warehouse tasks, such as storing, retrieving and transporting inventory.
They can increase efficiency by taking the fastest possible route in the warehouse when transporting goods and improve employee safety by operating in hazardous environments.
Types of Warehouse Robots
Advancements in the warehousing industry have brought about specialized robots for different warehouse tasks.
The most common types of warehouse robotics include:
Autonomous Mobile Robots (AMRs)
Autonomous mobile robots (AMRs) are sophisticated robots that can independently navigate your warehouse, eliminating the need for human intervention. AMRs utilize advanced technologies, such as machine learning, artificial intelligence and sensors to plan and adjust their routes in real-time.
They can also manage unforeseen challenges, whether it’s avoiding unanticipated crowds or evading falling objects.

Automated Guided Vehicles (AGVs)
Automated guided vehicles (AGVs) are warehousing robots that follow predetermined paths using a combination of sensors, markers and lasers for accurate navigation and movement.
Unlike AMRs, AGVs rely on fixed routes and guidance from warehouse operators to function. They also have less adaptability to unexpected changes in their surroundings.
Automated Guided Carts (AGCs)
Automated guided carts (AGCs) are robots that leverage predefined paths to transport inventory. They are equipped with magnetic tape, radio frequency identification (RFID) tags and sensors to navigate the warehouse and detect obstacles.
Unlike AGVs, AGCs can only carry lighter loads, due to their lower profile and smaller chassis.
Automated Storage and Retrieval Systems (ASRS)
Automated storage and retrieval systems (ASRS) are computer-controlled systems designed to automatically store and retrieve items from storage areas within the warehouse.
When integrated with a warehouse management system (WMS), automated storage and retrieval systems can identify the inventory that needs to be retrieved.
These systems include vertical lift modules, horizontal carousels, tote shuttles, mini-loaders and unit loaders.
Collaborative Robots (Cobots)
Collaborative robots, also known as cobots, are advanced robotic systems that can work alongside humans in the warehouse.
Unlike traditional robots, cobots have sensors and safety features, such as power and force limits.
Cobots can perform various warehouse tasks, such as conducting quality checks and packing products.

Unmanned Aerial Vehicles (UAV)
Unmanned aerial vehicles (UAVs), or warehouse drones, are aerial robots that can retrieve items and capture high-quality images of inventory. Equipped with sensors and cameras, they can fly on their own or be controlled by warehouse staff.
Thanks to their speed and size, UAVs can travel through narrow warehouse aisles, making them ideal to scan inventory.
Goods-to-Person (GTP) Robots
Goods-to-person (GTP) robots are warehousing robots that deliver selected items to warehouse operators, eliminating the need to navigate warehouse aisles just to find and pick goods.
GTP robots include stacker cranes and conveyor belts. These robots are particularly efficient in large warehouses, as they can handle larger volumes of orders.
Palletizing and Depalletizing Robots
Palletizing robots are equipped with a robotic arm and product gripper to lift and position items with precision, adapting to different size and weight variations.
These robots assess each item’s placement and securely arrange items using sensors and sophisticated programming.
On the other hand, depalletizing robots unpack pallets, efficiently reversing the stacking process. By automating these tasks, these robots save operators time, reduce the risk of item damage and maximize storage capacity.
Sorting Robots
Sorting robots use a combination of sensors, computer vision, and machine learning algorithms to identify, categorize and arrange items with precision.
Equipped with adaptable grippers and conveyance systems, they can efficiently sort products. This technology not only enhances operational efficiency but also reduces human error and labor costs.
Automated Labeling Robots
Automated labeling robots are warehousing robots that can help warehouse operators automatically place the label in the right spot on the package.
They are equipped with precision applicators to place labels on the desired spot every time. These robots also have sensors and cameras to detect the product’s position and orientation, so they can adjust the label application accordingly.
Packaging Robots
Packaging robots are warehousing robots that can help ensure products and pallets are securely wrapped for transport and storage, providing consistent wrapping tension, all while reducing manual labor and material waste.
They are equipped with load sensors to determine the weight and stability of the pallet and turntables to rotate the pallet or product, ensuring even wrapping from all sides.
Case Erectors
Case erectors are warehousing robots that can help automate the process of forming flat cardboard sheets into boxes, to prepare them for packaging.
These robots are equipped with grippers to pick and maneuver flat cardboard sheets, along with conveyor belts that push the packages forward to a tape dispenser, sealing the bottom of the cardboard case.
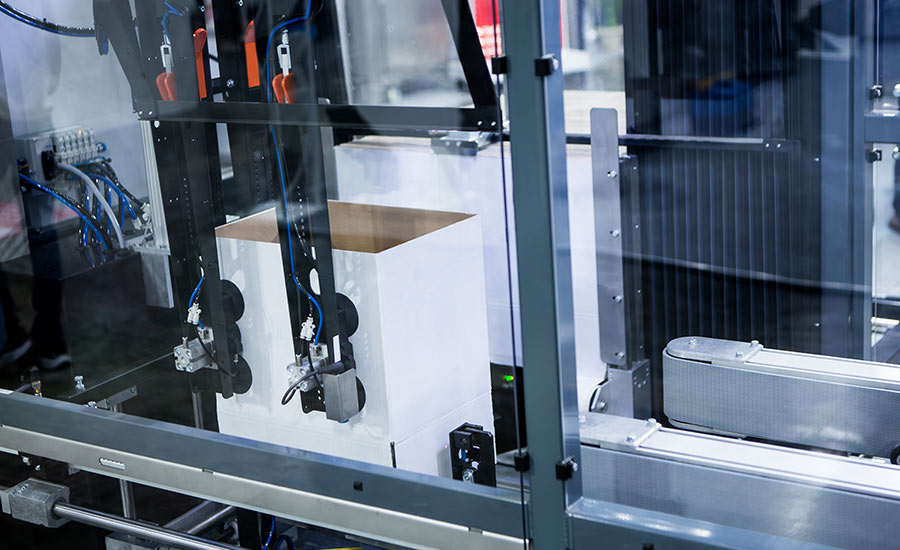
Cleaning Robots
Cleaning robots are warehousing robots that can help maintain cleanliness and hygiene standards in a facility, ensuring a safer and more efficient work environment.
They are equipped with rotating brushes, vacuum systems and sensors to detect dirt and obstacles, and drops.
Cleaning robots include floor scrubbing robots, vacuuming robots and disinfection robots.
Security Robots
Security robots are warehousing robots that can help enhance the security of a warehouse by providing continuous surveillance and immediate alerts when unauthorized access, potential breaches, or other unusual activities are detected.
They are equipped with motion and sound sensors and cameras, offering 360-degree views, night vision and even thermal imaging for comprehensive surveillance.
Anthropomorphic Robots
Anthropomorphic robots are automated warehouse pickers that can mimic human-like movements and functions, making them versatile for warehouse tasks that require a more human approach, such as picking and placing small parts.
The design of these robots is inspired by the human body, enabling them to handle objects, tools and operations with similar dexterity and adaptability as a human worker.
They are equipped with human-like hands, enabling them to perform a wide range of motion. They are also equipped with advanced sensors, cameras and machine learning algorithms.
Integration of Artificial Intelligence in Warehouse Robotics
Artificial Intelligence (AI) plays a pivotal role in advancing warehouse robotics by enabling machines to perform tasks that traditionally required human intelligence. AI allows robots to learn from data, adapt to new situations, and improve their performance over time. In warehouse operations, AI-powered robots can handle complex tasks such as sorting, picking, and packing with higher accuracy and efficiency. For instance, AI algorithms enable robots to identify patterns in order fulfillment processes, optimizing routes and reducing the time taken to complete tasks. By integrating AI, warehouses can achieve greater operational efficiency, reduce errors, and enhance overall productivity.
Collaborative Robots (Cobots) in Warehousing
Collaborative robots, or cobots, are designed to work alongside human workers, enhancing productivity and safety in warehouse environments. Unlike traditional robots that operate in isolated zones, cobots can share workspace with humans, assisting in tasks such as picking, packing, and transporting goods. They are equipped with advanced sensors and machine learning algorithms to navigate dynamic environments and interact safely with human counterparts. The adoption of cobots allows warehouses to combine human dexterity and decision-making capabilities with robotic efficiency, leading to optimized operations and reduced labor costs.
Case Studies of Warehouse Robotics Implementation
Several companies have successfully integrated robotics into their warehouse operations, yielding notable improvements in efficiency and productivity. For example, Walmart has partnered with Symbotic to automate its distribution centers, utilizing AI-powered robotics to enhance supply chain operations. This collaboration aims to modernize warehouse processes, resulting in faster and more accurate order fulfillment.
Similarly, Amazon has introduced various robots in its warehouses to assist with tasks such as sorting and transporting packages. Robots like Proteus and Sparrow work alongside human employees, reducing physical strain and improving overall operational efficiency.
What Do Warehouse Robots Do?
Warehouse robotics can manage inventory checks, assist warehouse operators with picking tasks and more.
Depending on the type of robot you implement, warehouse robots can help with:
- Sorting: Robots with grippers, such as cobots, can pick items and place them on conveyor belts, sorting goods based on size and dimensions. They can quickly move items from incoming shipments to specific bins or conveyors.
- Loading and unloading: Robots that can handle heavy inventory with adaptive grippers can automatically load and unload items from shipment trucks.
- Transportation: AMRs and AGVs can move inventory from one location to another within the warehouse with minimal human intervention.
- Inventory management: UAVs are equipped with cameras to scan inventory. They can travel warehouse aisles to scan barcodes and QR codes to assess stock levels. In addition, some warehouse drones are equipped with infrared cameras to capture thermal information, identify heat signatures and monitor temperature-sensitive goods.
- Picking: Automated storage and retrieval systems are designed to automatically retrieve items from shelves or bins and bring them to the warehouse operator, reducing their time and effort to manually pick inventory.
- Packaging: Anthropomorphic robots can pack items into boxes or other containers. They can adapt to different item sizes and shapes, ensuring that items are packed securely and efficiently. These robots can also seal and label orders.
Benefits of Warehouse Robotics
Warehouse robots provide a wide range of benefits, from increasing safety to improving efficiency. Moreover, the integration of robotics in warehouses significantly enhances inventory management accuracy. Automated systems can conduct regular inventory counts and updates, ensuring real-time data accuracy and reducing discrepancies. This leads to better stock control and minimizes the risk of stockouts or overstocking.
Warehouse robotics allow you to:
- Boost productivity: Warehouse robots can work 24/7 without needing a break, speeding up the order fulfillment process.
- Maximize storage space: Advanced robotic systems, like automated storage and retrieval systems, can be designed to utilize vertical space, reducing the warehouse footprint.
- Improve employee safety: Warehouse robots can reduce the risk of injuries (like overexertion) by minimizing or even eliminating manual tasks, such as lifting heavy objects.
- Boost scalability: Robots can be reprogrammed or repurposed for different tasks as warehouse needs change.
- Quick installation: Warehouse robotic solutions are highly customizable, enabling quick implementation within existing warehouse facilities
- Improve reverse logistics: Warehouse robots can quickly sort and process returned goods, reducing the time needed for product refunds or exchanges. UAVs can also inspect returned goods for damages more accurately than humans.
Warehouse Robotics Best Practices
Warehouse robotics best practices encompass detailed planning, precise integration, and meticulous management to maximize efficiency and streamline operations.
Evaluate your current operations and identify tasks that robots can manage, such as palletizing or picking.
For example, if your data shows high labor costs in picking, consider using automated guided vehicles (AGVs) for this task.
This can help you optimize labor allocation, reduce human error and speed up order fulfillment.
You can also forecast future demand and assess how scalable robotic solutions, such as modular robotic systems, can adapt to accommodate your inventory as order volumes increase.
Seamlessly integrating your warehouse robots with your existing WMS can help you optimize your inventory management.
For example, robots with scanning capabilities can automatically update inventory levels in the WMS in real-time as they pick, place, and move items.
This reduces the likelihood of human error and ensures that inventory records are always accurate.
In addition, robots can use data from your WMS to identify the best storage locations for items based on how often they are accessed and other factors. This can lead to more efficient use of space and faster retrieval times.
Leverage training modules that include practical sessions on operating robotic equipment, as this teaches your employees how to program and troubleshoot common issues with warehouse robots.
In addition, conduct quarterly workshops to refresh their skills and introduce new robotic features or updates.
Implementing these training programs will enhance your staff’s proficiency and confidence in managing robotic systems, leading to increased productivity and reduced downtime in your warehouse operations.
Implementing strict safety protocols while using warehouse robotics can help you ensure the well-being of your employees, prevent accidents and comply with industry regulations.
To establish strict safety protocols in your warehouse:
- Designate robotic operation zones within your warehouse using physical barriers or floor markings to prevent unauthorized access and improve safety
- Perform monthly safety audits to evaluate the interaction between robots and human workers
- Place emergency stop mechanisms at strategic locations throughout your warehouse to quickly deactivate robots when needed
Equip robots with sensors that track performance metrics, such as operational speed and error rates, and use this data to refine their routing algorithms and reduce bottlenecks.
This can help you optimize workflows, improve overall efficiency, and increase the throughput of your warehouse operations.
Consider investing in sustainable warehouse robots that are equipped with energy-saving modes and can operate on renewable energy to help reduce your warehouse’s carbon footprint.
For example, Modula’s Vertical Lift Modules (VLMs) and Horizontal Carousels (HCs) only consume energy when an operator activates them to deliver a tray of items.
Otherwise, they remain in a low-energy dormant state, consuming minimal electricity when not in use.
Arrange bi-annual strategic review meetings with your robotics vendors to discuss system performance, potential upgrades and innovations that could benefit your operations.
Secure a service level agreement (SLA) that guarantees regular maintenance checks, software updates, and 24/7 technical support.
A service level agreement (SLA) is a formal contract between your company and your robotics vendors that outlines the specific services the vendor agrees to provide.
Automated Warehouse Robots at Modula
At Modula, we provide automated warehouse solutions that improve efficiency, boost productivity, increase picking accuracy, enhance inventory management and maximize warehouse space across industries.
Our solutions include:
Modula Vertical Lift Modules
The Modula Vertical Lift Module (VLM) is a computer-controlled warehouse robot that efficiently stores your inventory vertically, allowing you to save up to 90% of warehouse space.
We offer two models — Modula Lift and Modula Slim. Each model uses minimal floor area by leveraging the height of your warehouse.
Modula Horizontal Carousels
For warehouses with low ceilings, look no further than the Modula Horizontal Carousel (HC).
The HC features rotating bins on an oval track that automatically deliver inventory to your warehouse operators. It reduces labor costs, increases efficiency and enhances inventory accuracy in both production and distribution environments.
The Modula HC allows you to:
- Store heavy items with a 1,200 lb payload
- Easily pinpoint the SKU and quantity of items to pick
- Enhance picking accuracy to nearly 99% using clear visual aids
- Avoid carrying heavy items and reaching extreme heights or depths during picking
- Boost productivity by removing unnecessary warehouse travel for inventory selection
Modula Robotic Integrations
Modula’s products can easily integrate with different types of robots to further optimize warehouse processes.
We offer two robot integrations:
- Modula’s integration with autonomous mobile robots (AMRs) improves picking tasks, offering the flexibility for partial or fully automated solutions.
- Modula VLMs can utilize a robot interface to integrate with human-like robots and automate cumbersome warehouse tasks like picking, while boosting efficiency.
Check out the video below to see our robot integration in action:
FAQs About Warehouse Robotics
Still have questions we didn’t cover? Find more details below about warehouse robotics.
Are warehouse robots safe to work alongside humans?
Yes. Robots are safe to work alongside humans, as they are equipped with safety features, including emergency stop buttons, collision detection sensors and safety guards.
How do warehouse robots navigate the facility?
Warehouse robots use a combination of sensors, software, and other technologies to navigate the facility.
Here are some common methods and systems employed by warehouse robots for navigation:
- Laser guided navigation: Robots utilize laser scanners to detect their surroundings. The laser data, when matched with a pre-mapped layout of the warehouse, allows the robot to determine its position and travel to its destination.
- Vision systems: Robots can identify objects, paths and obstacles using cameras. Advanced vision systems, combined with machine learning, can even recognize specific items or hazard signs in the warehouse.
- Magnetic tape or RFID: Robots, such as AGVs, follow magnetic tapes or tracks embedded in the floor. Others may use RFID tags placed in strategic locations to guide their route.
Can warehouse robots operate in any environment?
Warehouse robots are primarily designed for indoor environments with controlled conditions.
However, specialized modules, such as storage solutions for controlled environments, can manage extreme cold, heat or high humidity without an effect on their battery performance, sensors and electronic components.
How do you maintain warehouse robots?
Maintaining warehouse robots requires different steps to ensure they are in good working condition.
- Perform physical inspections: Regularly check the robot for visible signs of wear, damage or misalignment by inspecting the wires, joints, end effectors, wheels or tracks.
- Install software updates: Like any computerized system, robots require periodic software updates to fix bugs and boost their performance.
- Regularly clean the robots: Dust, dirt, and debris can affect sensors, cameras and mechanical parts. Regularly cleaning these parts ensures optimal efficiency.
- Lubricate the robots: Mechanical joints and moving parts may need periodic lubrication to reduce wear and tear and ensure smooth movement.
- Inspect the power systems: Ensure that charging systems, cords and connections are in good condition. Faulty power systems can lead to inefficient robot operation or sudden shutdowns.
At Modula, we offer top rated automated storage and retrieval systems to optimize your warehouse space, boost efficiency and meet changing consumer demands.
Contact our material handling experts for advice on the best storage fit for your warehouse. We’ll perform a warehouse audit to guide you to the right choice.