What Is a PPE Vending Machine? Types, Benefits & FAQs
Personal protective equipment (PPE) is an important tool in any facility to protect your employees from potential hazards and injuries during their workday.
Occupational safety is a critical concern for all companies. In fact, the U.S. Bureau of Labor Statistics recorded 5,486 fatal work injuries in the United States in 2022.
Maintaining an adequate stock of PPE in your facility can help you reduce the risk of these injuries, ensure compliance with safety regulations and create a more secure working environment for your employees.
We’ll explain all you need to know about PPE vending machines, from their types to their benefits, and share our latest storage solution at Modula that can safely store and dispense your inventory.
What Is Personal Protective Equipment (PPE)?
Personal Protective Equipment, or PPE, refers to a variety of items designed to protect workers from hazards that could cause injuries or illnesses while performing job-related duties.
These hazards can be physical, chemical, biological, electrical, mechanical or any other source of potential injury.
PPE includes, but is not limited to, items like helmets, gloves, eye protection, high-visibility clothing, safety footwear, earplugs or earmuffs, masks, respirators and protective clothing.
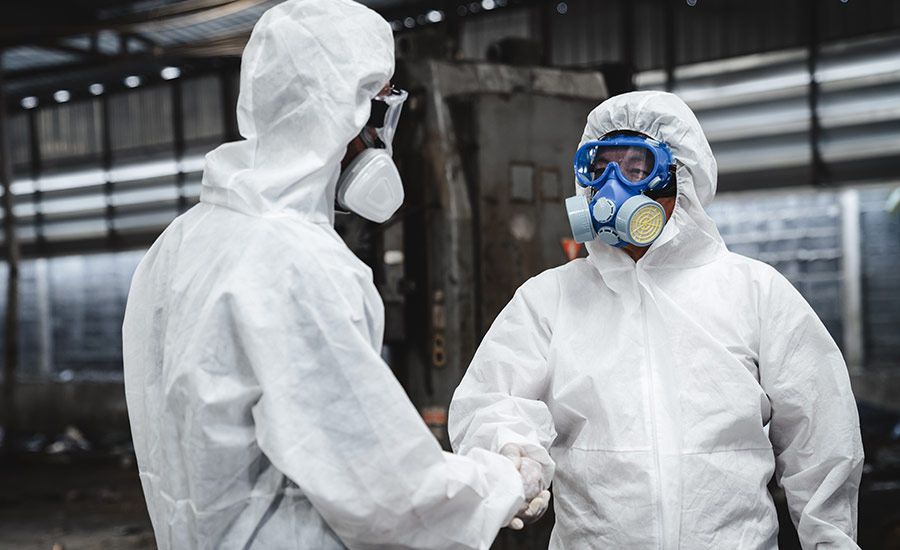
Types of PPE
There’s a wide range of PPE available, some of the most common include:
- Eye protection: safety glasses, goggles, face shields
- Hearing protection: earplugs, earmuffs
- Respiratory protection: respirators
- Hand protection: gloves
- Head protection: hard hats, bump caps
- Foot protection: safety shoes, boots
- Body protection: coveralls, aprons, vests
- Fall protection: safety harness, lanyards and lifelines
- Specialized PPE: thermal protective clothing, chemical suits
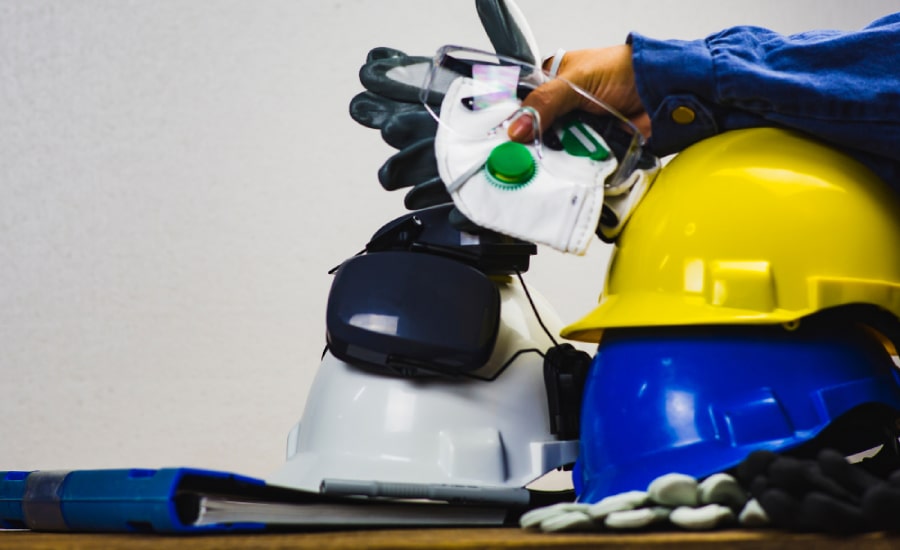
What Is a Personal Protective Equipment (PPE) Vending Machine?
A personal protective equipment (PPE) vending machine is an innovative system designed to dispense and manage PPE.
While this system is similar to regular vending machines, PPE vending machines offer employees a quick and easy access to protective gear in the workplace, such as in a warehouse.
Employees can use their ID cards, PINs or biometrics to obtain their personal protective equipment. This approach can help monitor the use of PPE, manage stock levels and foster accountability among your employees.
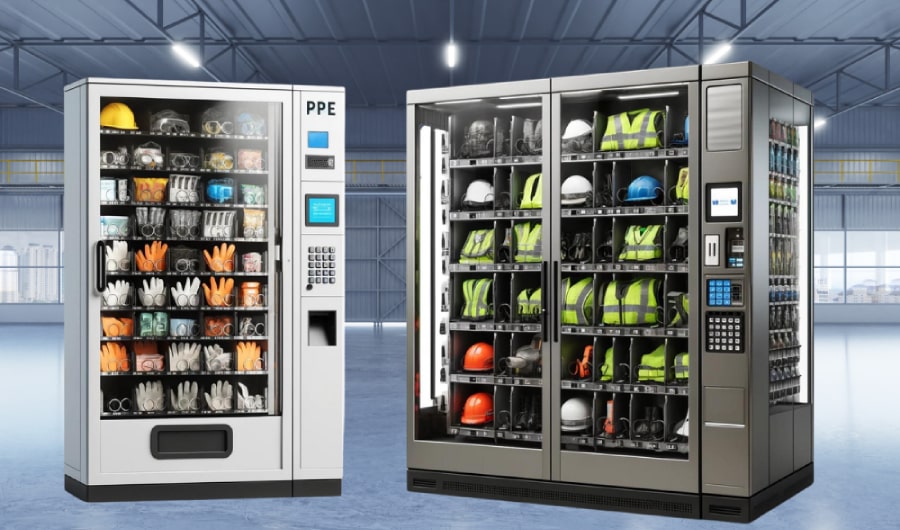
Types of PPE Vending Machines
Every type of PPE vending machine provides distinct benefits and features regarding SKU type and storage capacity.
The four types of PPE vending machines include:
Standard PPE Vending Machine
A standard PPE vending machine is a type of system that dispenses basic personal protective equipment, such as gloves, safety glasses, earplugs and masks.
They are ideal for workplaces that require standard PPE, such as offices, laboratories or schools.
Industrial-Grade Vending Machine
An industrial-grade vending machine is a type of system that dispenses goods in more demanding environments, such as factories or construction sites.
They offer a wider range of PPE, including heavier inventory, such as hard hats, safety harnesses and protective clothing.
Intelligent PPE Vending Machine
An intelligent PPE vending machine is a type of system that is equipped with advanced technologies, such as IoT connectivity, RFID, biometric scanners and real-time inventory tracking.
These machines can integrate with warehouse management systems to boost efficiency and control, while providing comprehensive usage data and user-specific access.
Customized Vending Machine
A customized vending machine is a system that can adapt to a workplace’s unique requirements, offering variations in size and storage capacity.
These machines are ideal for workplaces with specific safety gear requirements or unique operational needs, such as hazardous material handling or extreme temperature environments.
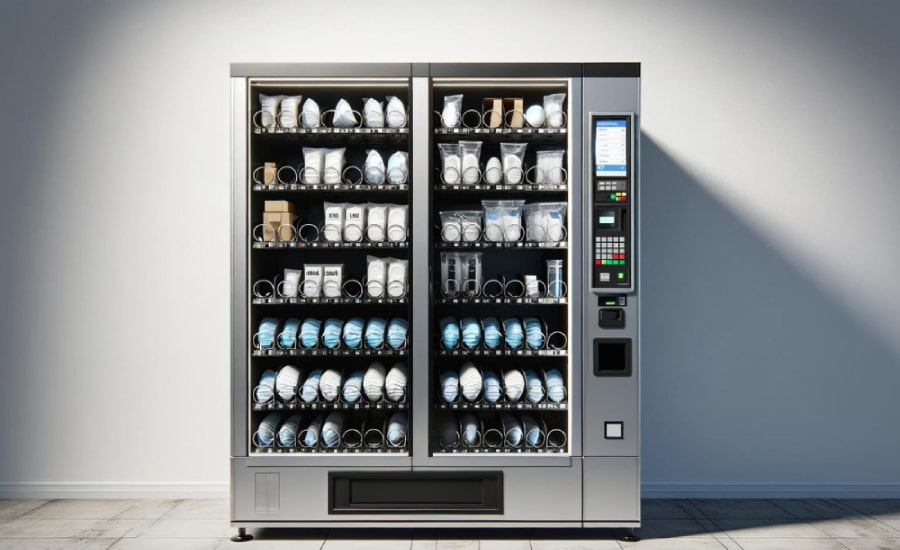
How Does a Personal Protective Equipment (PPE) Vending Machine Work?
A PPE vending machine offers a convenient way to distribute safety gear in the workplace.
Here’s a step-by-step overview of how vending machines for PPE typically work:
- Identification: Your warehouse employee proves their identity to access the vending machine. This can be done through various methods, such as swiping an ID card, entering a PIN or using biometric verification like a fingerprint scan. This ensures that only authorized personnel can access the PPE.
- Selection: Once identified, your warehouse employee can choose from a variety of PPE items available in the machine. PPE inventory can include gloves, masks, safety glasses or earplugs. The machine’s interface, which can be a touchscreen or button, allows users to select the item they need.
- Dispensing: The vending machine dispenses the PPE item. The item is typically stored in a compartment or slot and is released once the selection is made.
- Tracking and inventory management: The PPE vending machine actively tracks and manages inventory by recording which user takes an item, when they take it, and what item they dispense. This data is important for managing stock levels and understanding usage patterns. It helps keep the machine consistently stocked with the essential items and alerts supervisors or managers when certain goods are used more frequently.
- Restocking and maintenance: Regular maintenance and restocking of the machine are essential. The usage data helps determine which items need to be replenished. Maintenance ensures the machine functions properly and can dispense items.
Difference and Advantage of PPE Vending Machines compared to Modula Next
For warehouses and facilities that require the use of personal protective equipment, maintaining an efficient inventory is key to ensuring consistent availability of PPE, minimizing downtime and enhancing overall workplace safety and productivity.
At Modula, we offer automated storage solutions and warehouse management systems that can help maximize space efficiency and enhance inventory management in various industries.
The latest addition to our automated storage and retrieval systems (ASRS) lineup is the Modula Next, our Automated Industrial PPE Vending Machine
Modula Next is a vertical lift module (VLM) system designed for automated storage and retrieval of a wide range of items, including both general inventory and personal protective equipment (PPE).
While Modula Next and traditional industrial vending machines serve similar purposes of inventory management and distribution, there are several differences in their design, functionality and overall advantages.
Access Centralized Storage
Modula Next offers significantly higher storage capacity compared to traditional PPE vending machines.
Its vertical design maximizes storage density by utilizing the height of the available space. It can store many items in a relatively small, centralized location, making it easy for employees to find and access the gear they need.
This centralized approach saves time and ensures that PPE is stored in an organized and efficient manner, reducing clutter and potential inventory misplacement.
In addition, it significantly reduces the time spent by employees searching for PPE, streamlining their workflow and increasing overall productivity.
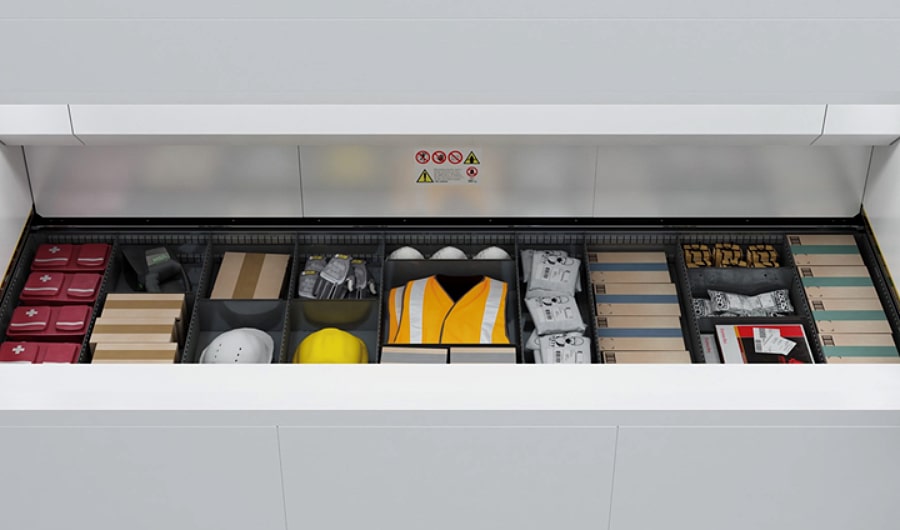
Maintain PPE Quality
Whether it’s for everyday tasks or work that requires exposure to hazardous chemicals, PPE must be clean and kept in good condition to ensure the safety and well-being of your employees.
By storing PPE in a controlled environment, Modula Next can help maintain the quality and integrity of your employees’ gear.
This controlled storage protects PPE from environmental factors, such as dust, moisture and direct sunlight, ensuring that inventory is in optimal condition when employees use them.
On the other hand, traditional PPE vending machines typically lack the controlled storage environment provided by Modula Next.
PPE items may be exposed to environmental elements and handling during the vending process, potentially compromising their quality over time.
Moreover, the limited space and compartmentalized design of vending machines may result in overcrowding or improper storage of PPE items, increasing the risk of damage or contamination.
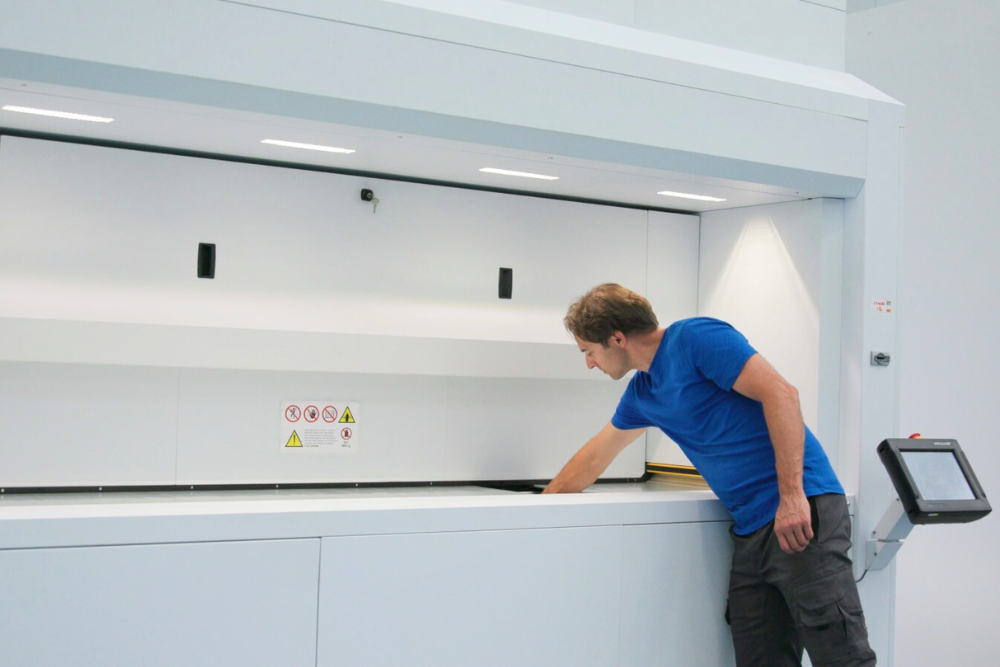
Gain Real-Time Inventory Tracking
With Modula Next, you can monitor PPE inventory in real-time to help you gain insights into accurate data regarding stock levels, usage patterns and restocking needs. Modula WMS logs each interaction, ensuring complete accountability and traceability.
In addition, real-time inventory tracking can help prevent costly PPE misplacement and ensures that the right equipment is available when needed.
On the other hand, traditional PPE vending machines typically offer limited inventory tracking capabilities.
While they may provide basic usage reports and item counts, they may lack real-time visibility and detailed insights. This can result in challenges such as stockouts, inefficient inventory management, and an increased risk of PPE shortages during critical times.
Ensure Scalability and Customization
Modula Next can store and distribute a wide range of items beyond PPE.
Its modular design allows for easy configuration and adaptation to accommodate various inventory needs, making it suitable for multiple industries and applications.
The compartments are easily adjustable to accommodate different items in terms of sizes or dimensions, or to accommodate changing inventory needs.
In contrast, PPE vending machines have limited scalability, as they are typically designed for a specific range of PPE items and may not easily adapt to changing inventory type or size.
While suitable for basic PPE distribution needs, they lack customization options for adjusting shelving heights or compartment sizes to accommodate different types of PPE or storage requirements.
Improve Employee Safety
By providing easy access to essential safety gear, Modula Next plays a key role in enhancing overall workplace safety.
This system ensures that your employees always have the necessary PPE at hand, reducing the risk of accidents, injuries and illnesses in the workplace.
In contrast, traditional PPE vending machines may offer limited accessibility to safety gear. While they provide a means for employees to obtain PPE items, they may not offer the same level of convenience and accessibility.
This could result in delays in accessing the necessary PPE, increasing the risk of accidents.
Secure PPE Inventory
Modula Next can help you secure your PPE inventory, allowing access only to authorized employees.
This security feature prevents unauthorized personnel from gaining access to your inventory, ensuring that goods are used appropriately and are always available for those who need them. It also helps maintain accountability among staff regarding PPE usage.
In contrast, traditional PPE vending machines may offer limited security measures. While they may require user authentication, such as PIN codes or employee badges, they may not provide the same level of control and accountability.
This could result in challenges such as unauthorized access to inventory or difficulties in tracking PPE usage accurately.
FAQs About PPE Vending Machines
Have more questions about PPE vending machines we didn’t cover? Find answers to the frequently asked questions below.
Where are PPE vending machines typically located?
PPE vending machines are usually placed in easily accessible areas within workplaces requiring PPE.
Common locations include manufacturing plants, construction sites, hospitals, laboratories and other industrial or healthcare settings.
The goal is to position these machines where workers can conveniently access PPE before entering hazardous areas or starting their work.
How do you stock and maintain PPE vending machines?
Stocking and maintaining PPE vending machines requires regularly replenishing the supply of safety gear and ensuring the machine is in good working condition.
This process typically includes monitoring inventory levels, refilling items that are low in stock and performing routine checks and predictive maintenance on your vending machine.
How much do PPE vending machines cost?
The cost of PPE vending machines can vary widely based on factors such as size, capacity, features (touchscreens or biometric scanners) and the type of PPE items they dispense.
Prices can range from a few thousand dollars for basic models to tens of thousands for advanced machines with more features.
In addition, consider costs associated with maintenance, restocking and potentially a subscription fee if the machine has software for inventory tracking.
At Modula, we provide advanced storage solutions and a comprehensive WMS to keep your maintenance inventory, including PPE, secure and readily available. Our system streamlines PPE management in your warehouse, ensuring efficient access and tracking.
Contact our team to discover how our solutions can be tailored to your operational needs.