What Is Logistics and Supply Chain Management? [+ Key Differences Explained]
Supply Chain Management vs. Logistics: What’s the Difference?
Supply chain management and logistics share a lot in common, but they also have some key differences.
While logistics focuses on the movement and storage of goods, supply chain management takes a broader view, coordinating everything from sourcing raw materials to production, transportation, and final delivery.
Getting a clear picture of what each one involves can help companies fine-tune their operations, establish a competitive advantage and lead in profitability.
In this guide, we will
- Clarify the roles of logistics and supply chain management
- Highlight the benefits of managing both effectively
- Show how the right tools, like a WMS, can optimize your entire operation
Understanding Logistics and Supply Chain Management
Logistics and supply chain management (SCM) is the process of managing the efficient movement and storage of goods and services from their origin to final destination.
This includes tasks such as receiving, managing inventory, transportation, warehousing and distribution to ensure that products are delivered to the right person at the right time.
What Is Logistics?
Logistics is a segment of the supply chain that focuses on planning, executing, and controlling the movement and storage of goods, services, and related information.
The main goal is to ensure that the right product reaches the right place, at the right time, in the right condition, and at the right cost.
Logistics typically includes two key areas:
This process is categorized into two types:
- Inbound logistics manages goods coming into a business
- Outbound logistics handles the delivery of inventory to customers
What Is Supply Chain Management?
Supply chain management (SCM) is the broader concept. It involves It involves coordinating all activities across suppliers, manufacturers, distributors, and retailers to improve efficiency and meet customer needs.
Supply chain managers work across multiple functions and organizations to ensure that products are produced, moved, and delivered as expected in terms of quality, cost, and timing.
Difference Between Logistics and Supply Chain?
Logistics focuses on internal processes like inventory storage and transportation. It’s about managing the flow of goods within a company or between immediate partners.
Supply chain management goes beyond that. It covers the full journey of a product, from sourcing raw materials to manufacturing, distribution, and final delivery. It also emphasizes collaboration between all stakeholders involved.
Think of it this way: logistics is like the machinery that moves parts within a factory, while supply chain management oversees the entire production line from sourcing raw materials to delivering the finished product to the consumer.
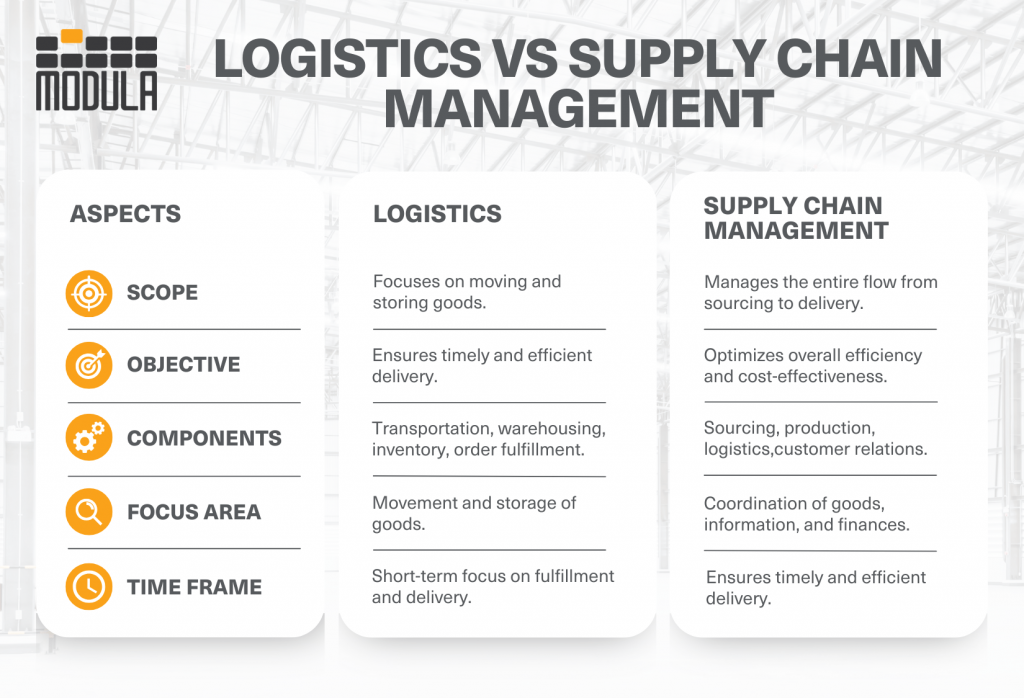
Logistical Components of the Supply Chain
Supply chain logistics are pivotal for orchestrating the flow of goods and services. They guarantee that each component facilitates the seamless transition of materials and finished products through different stages of the supply chain.
Supply chain logistics include:
- Inventory status: Tracking inventory in real time helps support better business decisions. For example, when warehouse managers monitor stock levels accurately, they can adjust production and purchasing plans to avoid stockouts or excess inventory.
- Storage: Effective storage ensures the right amount of supplies are maintained at optimal locations, balancing supply and demand to prevent excess or insufficient stock.
- Warehousing: This involves overseeing daily warehouse operations, including receiving, storage, picking, packing and shipping activities.
- Material handling: Material handling encompasses storage, security and the transfer of goods through manufacturing, distribution and delivery.
- Unitization: Unitization consolidates multiple smaller units into a larger one to enhance warehouse efficiency, speed up packaging and arranging and improve handling and transportation.
- Inventory control: This integrates storage and warehousing strategies to manage the types and quantities of stock. Inventory control utilizes inventory management formulas to predict demand accurately. For instance, using techniques like Economic Order Quantity (EOQ) can help you determine the ideal amount of inventory to order and when inventory replenishment is needed, reducing inventory carrying costs and minimizing the risk of excess inventory.
- Packaging: Proper packaging protects your inventory from damage during transit and strategically reduces shipping costs.
- Transportation: This component manages the transportation of goods along the supply chain, either to the next facility or directly to customers. It utilizes vehicles such as cars, trains, trucks, airplanes and ships tailored to the delivery route and cargo type.
Key Benefits of Managing Logistics
Given the significance of moving goods for generating cash flow, it’s clear that effectively managing this process through logistics is crucial for any business.
The way logistics are managed can significantly impact a company’s financial health, either by improving it or posing challenges.
Better Supply Chain Visibility
Effective logistics management increases transparency across the supply chain. This allows businesses to better manage costs, identify efficiencies, detect issues, plan for demand and seize new opportunities, such as expanding into new markets and building stronger partnerships with suppliers.
Lower Operating Costs
Logistics management reduces overhead by cutting shipping costs and minimizing warehouse space requirements through proactive inventory control.
Customer Satisfaction
Accurate and swift order delivery improves the customer experience, which is essential for securing repeat customers.
To paint a better picture, happy customers are more likely to become loyal advocates for your brand. They often share their positive experiences through word-of-mouth or social media, attracting new customers and increasing your brand’s visibility.
Inventory Control
Effective logistics management helps prevent losses by ensuring accurate inventory counts and tracking stock in real time, especially since 24% of consumers report being unable to purchase items due to stockouts.
Logistics management is vital for preventing losses by maintaining precise inventory counts and closely monitoring stock movements and locations.
Drive Business Growth
Demand forecasting facilitates business growth by accurately predicting inventory needs and optimizing procurement and transportation.
Adopting logistics management best practices allows companies to efficiently scale operations to meet growing customer demands.
Improved Flexibility and Agility
Efficient logistics systems allow businesses to quickly adapt to changing market demands, seasonal fluctuations, or unexpected disruptions.
This agility provides a competitive edge by maintaining consistent service levels and customer satisfaction.
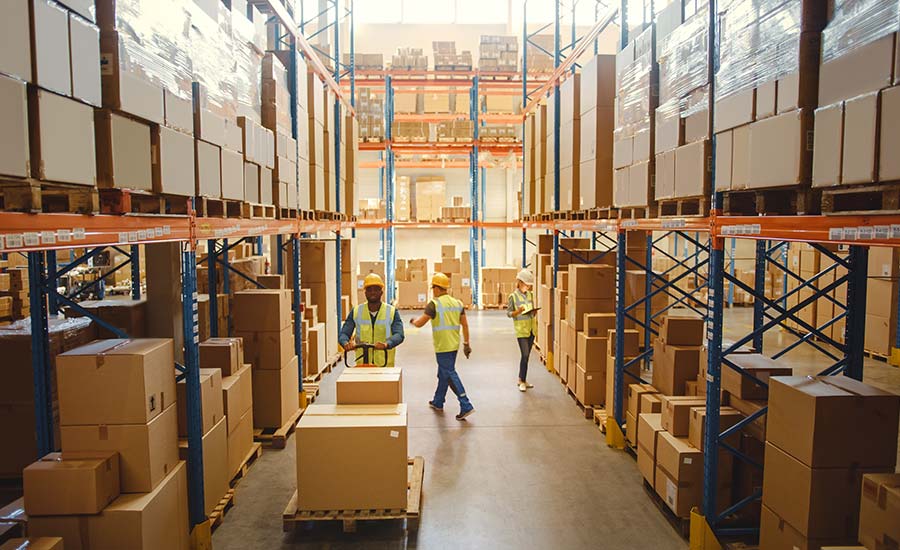
How Can Modula’s WMS Improve Your Logistics and Supply Chain Management?
A warehouse management system (WMS) is a type of software that enables companies to manage and control daily warehouse operations from the moment goods and materials enter a distribution or fulfillment center until they’re dispatched.
A warehouse management system significantly enhances logistics and supply chain management by offering several key benefits:
- Improved inventory accuracy: A WMS tracks each item from entry to exit. This ensures data accuracy and prevents overstocking or stockouts. It also provides real-time insights into inventory levels, order status, and productivity, enabling managers to quickly address operational challenges.
- Efficient space utilization: A WMS optimizes storage locations based on item size, weight and access frequency, maximizing space and reducing overhead costs.
- Increased labor productivity: A WMS directs and guides your warehouse pickers to optimal pick locations, reducing travel time and increasing efficiency. It can also assign tasks based on priority and worker availability to improve workflow.
- Better demand forecasting: Integrated analytics and reporting tools can help warehouse managers understand trends, anticipate demand changes and make informed decisions about inventory levels.
- Reduced operational expenses: A WMS lowers labor costs and minimizes errors, such as mispicks, that cause returns or additional shipping charges.
- Compliance and documentation: A WMS maintains compliance with regulations by tracking detailed inventory movements and automates the creation of shipping and customs documents, reducing manual labor and error risks.
To further streamline your operations, pair your warehouse management system with Modula’s vertical lift modules (VLMs).
These automated storage and retrieval systems (ASRS) maximize storage density, reduce floor space requirements and significantly enhance retrieval times. This allows for faster, more accurate order processing and increased productivity in your warehousing operations.