What is Material Handling? Principles, Benefits & Equipment
While warehouses are known to be busy work environments with constant movement, they don’t have to be chaotic or labor-intensive, as long as the proper systems are in place.
With an organized material handling system and specialized equipment, warehouse operators can increase productivity and efficiency while keeping employees safe from potential accidents and streamlining the movement of goods from one stage to the next.
But what is material handling exactly, and what does it entail?
We’re about to find out. In this article, we’ll cover all you need to know about material handling, including how it’s implemented into the supply chain, the types of equipment used and the benefits of integrating it into your warehouse.
Plus, we’ll share how our automated solutions fit into the material handling puzzle to help streamline your warehouse operations.
What is Material Handling?
Material handling is the movement of materials and goods from one location to another. It includes protecting, storing, and controlling the materials, from manufacturing to distribution.
Material handling can be used across industries, but is typically utilized in warehousing, where goods need to be securely stored, retrieved, and shipped.
Material handling equipment utilizes manual, semi-automated, and automated equipment to assist the movement and storage of materials within the warehouse.
Types of Material Handling Equipment
Material handling equipment is grouped into four main categories: storage and handling, bulk material, industrial trucks and engineered systems. Let’s take a look at each one.
1. Storage and Handling Equipment
Storage and handling equipment secures your goods while they aren’t being used or waiting for the next stage in the supply chain process.
Storage and handling equipment can keep materials for short or long periods of time, depending on your warehouse’s needs.
Storage and handling equipment includes:
- Pallet racks: Vertical structures made of steel framing with connectors and beams to store products
- Shelves, bins and drawers: Shelves, drawers and bins within shelving units store smaller materials.
- Mezzanines: Wooden, steel or fiberglass raised platforms that create additional storage
- Stacking frames: Equipment that stores and stacks numerous pallets and racks
2. Bulk Handling Material Equipment
Bulk handling material equipment stores, controls and transports loose form materials in large quantities.
Loose form materials can include liquid, food and minerals, such as stones and rocks, and metal items, such as bolts and nails.
Bulk handling equipment includes:
- Conveyor belts: Two or more belts and pulleys to transport products from one location to another
- Stackers: Equipment that loads and unloads heavy materials and places them onto stockpiles or storage for bulk materials
- Reclaimers: Reclaimers are used to pick out materials from stockpiles
- Bucket elevators: Designed for handling and lifting large amounts of bulk materials through the system
- Hoppers: Funnel-shaped equipment used to dump or pour loose form materials into containers
3. Industrial Trucks
Industrial trucks are vehicles that transport goods and materials within your warehouse and are also utilized to load or unload heavy objects.
There are several different types of industrial trucks. Some have forks or a flat surface to lift products, while others need additional equipment for lifting. Industrial trucks can range from small, hand-operated machines to large, drivable equipment.
Industrial trucks include:
- Forklifts: Industrial trucks that raise and lower goods in short distances
- Hand trucks: Also called dollies, industrial trucks are manually pushed by hand and consist of two wheels and a small ledge to carry goods
- Pallet Trucks: Also known as pallet jacks, pallet trucks are designed to lift and move pallets
- Sideloaders: Industrial trucks that go through narrow aisles, and load and unload goods from the machine’s sides
- Order pickers: These machines safely lift operators, allowing them to access hard-to-reach materials on high shelves
4. Engineered Systems
Engineered or automated systems are solutions that incorporate technology supported by computers and robots to store and transport goods
An automated system is generally made out of several units, controlled by a management software application.
Engineered systems include:
- Autonomous mobile robots (AMRs): Sophisticated robots that navigate their environment independently, without the need for human intervention
- Automated storage and retrieval systems (AS/RS): Computer-controlled solutions that keep and retrieve goods in the warehouse
- Automated guided vehicles (AGVs): Guided robots that require a human operator to navigate their environment
This is where Modula comes in. At Modula, we provide the most advanced automated storage and retrieval systems to increase productivity and accuracy throughout your warehouse.
Our Vertical Lift Modules, Horizontal Carousels and Order Picking Solutions are designed to optimize space, reduce errors and speed up operations to create a seamless material handling process, from start to finish — more on this below!
GF MACHINING SOLUTIONS: Vertical Storage Units Fully Integrated with ERP and Modula WMS.
Benefits of Material Handling
An effective material handling system allows your company to have the necessary stock in smaller spaces where possible, reduce time spent on internal operations (such us transport and picking), control inventory in real-time, reduce operational costs and optimize the overall flow of goods in your facility.
From preventing workplace accidents to saving you money, here are four reasons why material handling is key to implement in your warehouse.
1. Prevents Workplace Accidents
According to a recent survey, overexertion is the most disabling United States workplace accident in 2021, with falls and being struck by an object ranking second and third, respectively.
With materials handling systems and the proper equipment, employees aren’t required to lift heavy items and reach high storage areas.
2. Improves Employee Satisfaction
Job discomfort causes frustration, low morale and loss of motivation in employees.
By utilizing materials handling systems, employees are released from labor-intensive (for example, lifting heavy items) and monotonous tasks that will help them reduce stress levels and achieve overall satisfaction with work.
3. Increases Productivity and Efficiency
Want your employees to focus on more pressing tasks such as quality control assurance?
Material handling equipment can help your employees transport, locate, and pick inventory, allowing them to be more competent and productive with other tasks.
4. Saves You Money
According to a 2019 report, the worldwide expenditure of warehousing companies is tallied at a whopping €300 billion each year.
To prevent spending more on equipment damage, invest in quality solutions and educate your employees on the proper equipment maintenance.
How is a Materials Handling System Implemented Throughout the Supply Chain?
From manufacturing to distribution, material handling is key to ensure your materials and goods are safely transported from one stage of the supply chain to the next.
Here’s how material handling is implemented in the supply chain:
- Manufacturing: Material handling is used to move and manage inbound shipments within storage areas or a warehouse.
- Transportation: Material handling is used to place goods on pallets for easier transportation to warehouse storage areas.
- Storage: Material handling is used to safely offload goods to designated storage areas or shelves while they wait for distribution.
- Distribution: Material handling is used to load goods onto trucks (for example, using forklifts) that will be delivered to retailers, wholesalers or customers.
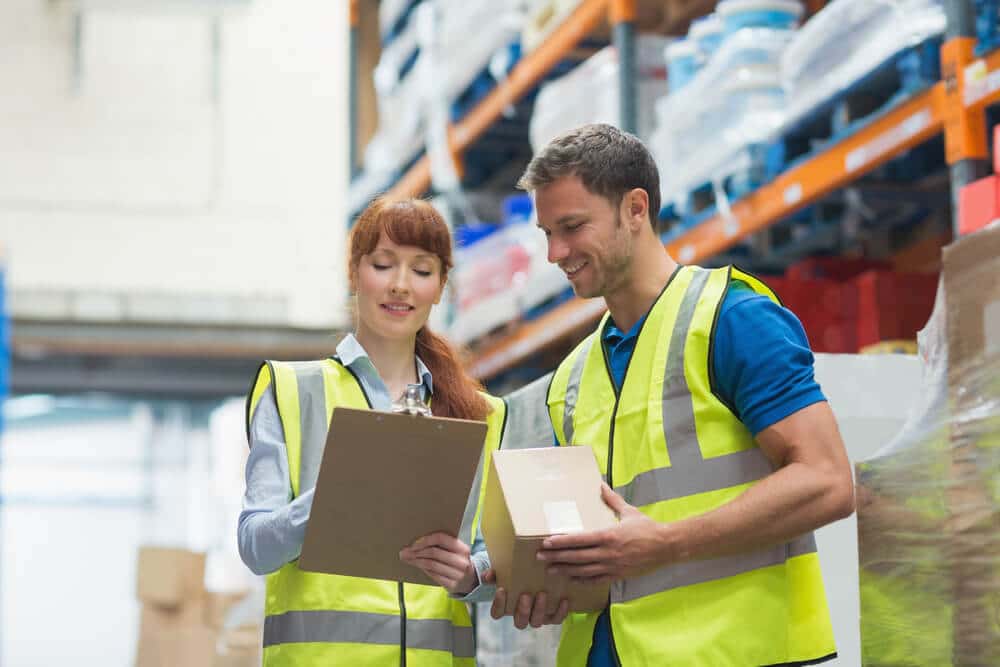
10 Material Handling Principles to Streamline Your Operations
Researchers and professionals at the Material Handling Institute created a document containing the 10 principles of material handling to create a safer and more productive materials handling system.
From reducing unnecessary manual work to maximizing available space and tracking inventory in real-tine, Modula’s automated solutions are designed to help you adhere to these principles to streamline your warehouse operations.
1. Planning: Establish a clear plan for your material handling system. Your plan should identify which materials will be transported, which equipment will be used and where your materials will be stored.
2. Standardization: Standardize your process and equipment to achieve predictable results while considering flexibility. For example, if you have boxes of the same size, your team should anticipate future changes regarding box sizes, so you can choose equipment that can efficiently transport smaller or larger boxes in the future.
3. Work: Reduce unnecessary work by using equipment that will minimize or eliminate repetitive tasks.
4. Ergonomics: Acknowledge your employees’ restrictions and capabilities by investing in ergonomic equipment to ensure safety in the workplace.
5. Unit load: Utilize unit loads such as containers and pellets to reduce effort and walking time in the warehouse.
6. Space Utilization: Organize your warehouse to maximize your available warehouse space. You can ensure your warehouse is organized by clearing warehouse aisles from clutter, stacking inventory to utilize vertical height and grouping products in the same category.
7. System: Integrate tracking tools so you can quickly identify materials and products at every stage of the system.
8. Environment: Use equipment that will reduce energy consumption and prevent greenhouse gas emissions. For example, using an electric forklift is more sustainable than using a liquid-propane powered truck.
9. Automation: Implement automation in warehouse processes such as picking and retrieval to lower costs and boost employee productivity.
10. Life Cycle Cost: Utilize a comprehensive analysis of life cycle costs on material handling equipment to ensure durability and sustainability. Consider different criteria, including programming, installation, setup, operation, repair and maintenance, reuse value and disposal.
How Modula’s Solutions Contribute To A Seamless Material Handling Process
At Modula, we take material handling to the next level using the most advanced automated storage and retrieval systems. Our automated solutions boost accuracy and productivity, improve employee safety and reduce storage space requirements.
Modula Vertical Lift Modules
Modernize your warehouse operations by going vertical with two options:
- Modula Lift is the optimal storage solution for industrial materials, spare parts and components for every industry and workplace environment
- Modula Slim is the ideal solution for warehouses with minimal floor space requiring flexible storage options
Our Vertical Lift Modules allow you to:
- Keep your employees safe by eliminating the challenges of reaching high and low areas
- Improve efficiency by retrieving the items needed from a small number of VLM stations
- Safeguard your products by storing them in an enclosed setting that only designated employees can access
- Increase productivity thanks to picking speeds of 300 lines per hour
- Lower operational cost as well as employee cost
- Anticipate requirements and offer the possibility for future growth
- Pay off the investment rapidly, with an ROI anywhere from six to 18 months
Modula Horizontal Carousels
Modula Horizontal Carousels turbocharge your warehouse operations when ceiling height is limited.
Our Horizontal Carousels allow you to:
- Facilitate quick and accurate picking operations with put-to-light systems and barcode readers
- Increase picking rates of up to 550 lines per hour for each warehouse operator
- Monitor picking operations in real-time thanks to automation
- Find and retrieve goods quickly with Modula’s digital Copilot

Modula Warehouse Management Solutions
Pair your automated storage systems with our warehouse management solutions to boost productivity, accuracy and efficiency.
Warehouse management solutions offer better control over inventory tracking, materials handling, process analysis and preventive maintenance guidance.
Our smart solutions allow you to operate in multi-order and batch modes to increase productivity without compromising your order fulfillment process for larger than usual orders.
Modula Cloud is a support and remote warehouse management platform that collects data from your AS/RS wherever they are in your warehouse.
With Modula Cloud, you can:
- Manage and monitor your warehouse operations in real-time, 24/7
- Gather your data in an easy-to-navigate online portal
Key Takeaways on Material Handling
More than just the movement of goods and products, material handling is a crucial element in your warehouse operation because it provides a standardized process of handling and transportation from manufacturing to distribution.
At Modula, our automated solutions are designed to integrate into each stage of the supply chain and help you follow the key principles of material handling to ensure a seamless operation.
Take your material handling to the next level with the most advanced storage and retrieval systems from Modula.