Leveraging Warehouse Sustainability with Automation
Automated order fulfillment in distribution and manufacturing can impact sustainability far beyond energy reduction and minimize carbon footprint. Yet many of these benefits – such as improved worker productivity and faster throughput – are often overlooked for how they contribute to a company’s overall sustainability goals.
An excellent example are the latest vertical lift modules and horizontal carousels, such as those designed by Modula, which support sustainability, while enabling inventory to be stored, picked, packed, and shipped with optimized performance.
Not too long ago, making decisions about a company’s sustainability was a fairly straightforward process for most facility managers. Switching to LED lighting, upgrading HVAC systems, and streamlining production by moving to a more integrated process controls architecture, were some of the initiatives a company may have undertaken in pursuit of improved sustainability.
But today it is different. For industrial and manufacturing companies, the integration of sustainability projects is more likely part of a broad-scoped strategy to optimize all facets of the business, from facility operations through process functions, manpower, and distribution. Such a strategy takes into consideration a company’s higher-level, long-term business goals. This may include communicating the organization’s awareness of its environmental impacts, its initiatives toward energy conservation, and its focus on healthy working conditions for employees by promoting a working environment that utilizes sustainable materials and processes.
Every business is facing the call to convert to sustainable business practices. A recent Kearney survey finding shows that 80% of buyers consider the environmental impacts of their purchases. Responding to this, manufacturers continue to build sustainable practices into their operations, creating value for their customers, themselves, and their stakeholders.
Distribution, and the Three Pillars of Warehouse Sustainability
This is particularly relevant with supply chain companies. According to the Council of Supply Chain Management Professionals State of Logistics Report 2022, “Industrial, manufacturing and logistics companies, as primary consumers of energy and a major historic source of carbon emissions in the global economy, must play a leading role in partnership with sustainability. Better synchronized supply chains, aligned to shared sustainability goals, are essential to reaching greenhouse gas reduction targets.”
Transporting goods is a big contributor to global carbon emissions, but warehouses, particularly refrigerated warehouses, are some of the most energy-intensive industrial facilities on the planet. Energy consumption represents the second highest operating expense in refrigerated facilities, trailing only labor costs, according to industrial energy management firm, Cascade Energy. In food distribution and grocery warehouses, refrigeration uses about 50% of total energy use and 65–75 % in fully refrigerated facilities.
As warehouses seek to reduce the cost and environmental impact of their distribution operations, while faced with upscaling to meet growth targets, three solutions should always be evaluated:
1) Maximizing the use of space to reduce the need for storage and the energy use it requires;
2) Automating manual processes that will permit goods to be moved more rapidly and safely through the facility, minimizing energy use and carbon emissions;
3) Optimizing the design and function of automated material handling systems for operational efficiency.
Essentially, these initiatives would progress the Three Pillars of Sustainability, which form the foundation of sustainability goals. Those being:
a) Environmental Pillar – initiatives that reduce the carbon footprint of the business;
b) Social Pillar – initiatives promoting the wellbeing, health, and safety of employees and customers;
c) Economic Pillar – initiatives that ensure businesses can thrive while making these positive impacts.
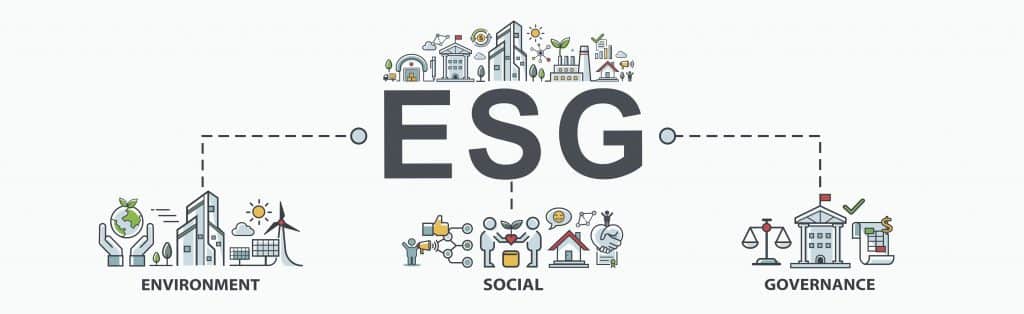
Order Fulfillment for Warehouse Sustainability
Embodying these factors is order fulfillment. No sector of distribution has seen as much metamorphosis over the past two decades in support of sustainability as automated goods-to-person picking solutions for fulfillment of light goods in small-quantity orders.
This makes sense when you consider the high-input human element at play in the traditional person-to-goods picking process used to prepare assembly line kitting requests, ship spare parts, and store and retrieve finished orders. In such an inventory model, pickers walk, or move a picking cart or lift truck, to rack and floor locations, and manually pick parts or finished goods. Items stored on racking or shelving, or in drawers, lead to slow process flows where time is mainly spent locating and retrieving items to fill orders. An activity that is energy and labor-consuming. (See graphic below)
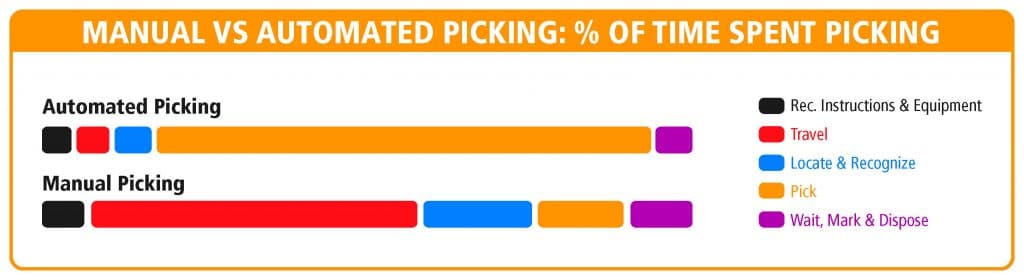
The true benefit of automated goods-to-person order fulfillment is that it allows inventory to be stored in a highly condensed low-footprint space, and then picked and packed with the operator remaining relatively stationary. Pickers are efficient when they are picking, not walking or trying to locate products. Goods-to-person technology presents considerable opportunities for embracing warehouse sustainability.
To better put this into context, we will examine two automated goods-to-person systems that significantly leverage sustainability, and how they fit in with the Three Pillars of Sustainability: The latest vertical lift module (VLM) and horizontal carousel (HC) from Modula – a company which has been designing and manufacturing automated storage and picking solutions for manufacturing and distribution for more than 30 years. Capable of handling thousands of different SKUs, these VLMs and HCs allow inventory to be stored, picked, and packed with a very high level of efficiency while integrating many aspects supporting sustainability.
VLMs and HCs – Environmental Warehouse Sustainability
With automated fulfillment systems like the Modula VLMs and HCs, the Environmental factors are generally most recognized and associated with sustainable benefits. Here are some of these systems’ key Environmental factors supporting sustainability.
VLMs and HCs – Social Warehouse Sustainability
The benefits of wellbeing, health, and safety for personnel operating the VLM and HC are Social sustainability factors that are less well recognized, but nevertheless, very welcomed. Here are the key Social sustainability benefits afforded by these VLMs and HCs.
Vertical Lift Module – Ergonomic Workstation
VLMs and HCs – Economic Warehouse Sustainability
The remaining pillar is Economic sustainability – initiatives that ensure businesses can thrive while making these positive impacts. With Modula VLMs and HCs, these benefits are immediate and ongoing. Following are some of the key benefits.
Sustainable Distribution and Manufacturing
A growing number of companies are treating sustainability as a critical objective in their strategy and operations to increase growth and global competitiveness. This trend has reached well beyond the small niche of those who traditionally positioned themselves as “green”. It now includes the most prominent businesses across a multitude of industry sectors.
Sustainable changes should focus not only on equipment, processes, and the environment, but also on the people working within these environments, and how their employee experience can be improved.