Autonomous Mobile Robots 101: How They Work, Types & Benefits For Your Warehouse
As a result of the pandemic, supply chains in the United States are facing two distinct challenges: a lack of warehouse space to store a higher quantity of goods onshore, and a lack of warehouse workers to fulfill the operations.
While many companies across the country are struggling to find solutions, some are already benefitting from an all-in-one solution to both of these challenges: Autonomous mobile robots (AMR).
In this article, we’ll cover all you need to know about autonomous mobile robots, including how they work, the benefits of implementing them in your warehouse and our automated solutions that pair seamlessly with AMRs to increase productivity throughout your operation.
What Are Autonomous Mobile Robots (AMR)?
Autonomous mobile robots (AMR) are intelligent robots that can move around an environment independently, without the need for a human operator.
Not to be confused with autonomous guided vehicles (AGVs), which need pre-defined routes or the supervision of an operator, AMRs can navigate through their surroundings on their own.
Thanks to the intelligence and sophistication of AMRs, they’re able to:
- Perform tasks efficiently while taking the fastest possible route
- Evade collisions with fixed structures, including shelves, fixed installations and work stations
- Avoid impact with moving obstacles, including operators, warehouse employees and forklifts
How Do Autonomous Mobile Robots Work?
AMRs are wireless robots that use advanced technologies, including artificial intelligence, machine learning, and sensors for path arrangement to interpret and navigate through their environment.
AMRs can even handle unexpected situations, such as falling objects, boxes or unanticipated crowds.
How?
AMRs use sensors and cameras to determine navigation. They’re able to avoid collisions by stopping, slowing down or rerouting their path around unforeseen objects. After avoiding collision, they immediately resume their task.
3 Types of Autonomous Mobile Robots
From transporting and sorting goods to aiding in the picking process, there are three main types of AMRs, based on their purpose in your warehouse.
1. AMRs That Transport and Sort Goods
Automating the tasks of movement, sorting and handling of goods within your warehouse allows your employees to engage with other productive tasks without having to leave their work station.
AMR-based sortation is a great alternative to traditional sorters such as tilt-tray and cross-belt conveyor-based sortation systems.
They require a significantly smaller floor area, and, when equipped with robotic arms, they are also able to deliver, load, and unload materials with little to no human intervention, ideal for activities such as buffering and milk runs.
Moreover, as each mobile robot operates independently, these systems are easily scalable with additional robots introduced as and when they are needed to cope with peaks in demand. This benefit is now, more than ever, critical in retail and e-commerce operations.
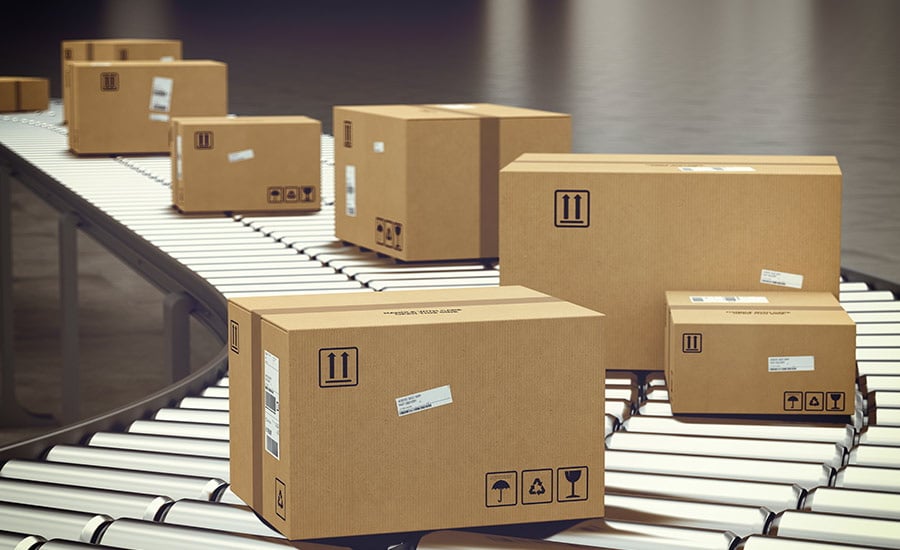
2. AMRs That Help With the Picking Process
AMRs significantly reduce travel time in the picking process while allowing your employees to be more productive with their time. The operating methods commonly applied to picking include:
- Area picking: Operators in the picking process are assigned to a warehouse area where items are stored. AMRs navigate the warehouse independently thanks to the interface that displays order information and details. When the AMR reaches a warehouse area for picking, your picking operators can look at the items indicated on the interface and place them into the tote attached to the robot. Once all of your required orders have been picked, the robot takes the items to the next zone for further picking or to the packaging or shipping area. This process is repeated with multiple AMRs operating and transporting to the different areas of the warehouse.
- Goods-to-person picking: With G2P or goods to person picking, the need to manually look for products in the warehouse can be eliminated. With G2P, operators are assigned to a picking station to prepare orders. Meanwhile, the AMR navigates through the shelves to find the exact item needed, then defines the shortest path to deliver it back to the operator, who simply places it into the tote that’s being prepared.
3. AMRs That Manage Inventory
Accurate and up-to-date inventory information is vital for seamless warehouse operation.
You can combine automated solutions to streamline your inventory activities.
For example, you can combine Radio Frequency Identification (RFID) with AMRs.
RFID wirelessly transfers item identification in the form of a unique serial number of a product, streamlining the process of identifying goods.
In addition, when you integrate your AMR with a warehouse management system, you can reduce human error, ensure real time data accuracy in order fulfillment and optimize employee productivity.
Benefits of Autonomous Mobile Robots Combined With Automated Storage and Retrieval Systems
From improving productivity to streamlining operations and reducing the need for additional employees, here are six benefits of autonomous mobile robots when combined with automated storage and retrieval systems.
1. Increase Storage Capacity
Most warehouses store goods in racks.
But think about the storage capacity you could gain by storing goods in a tower.
At Modula, we provide vertical storage and retrieval solutions that use a minimal footprint by taking advantage of your warehouse’s ceiling height.
AMRs work with vertical lift modules by picking items from the tower, then delivering them right to your picker or AMR who can take them to the packaging or shipping area.
2. Allow Employees to Focus on More Valuable Tasks
Global e-commerce sales jumped to a whopping $26.7 trillion in 2019.
When the global pandemic hit, shutdowns caused supply chain disruptions and labor shortages as people stayed home or quarantined, adding more pressure to the eCommerce industry.
Implementing AMRs is a solution companies can leverage to address the challenges of labor shortages, while also automating mundane tasks so employees can focus on other priorities.
3. Increase Employee Safety
A study by the U.S. Bureau of Labor Statistics found that there were 4.8 recorded injuries for every 100 full-time workers in the warehousing industry in 2019 alone.
AMRs can be used in the warehouse for tasks that could be dangerous or not possible for humans.
From accessing hazardous areas of the warehouse to performing physically demanding tasks such as passing through tight spaces, carrying dangerous loads and avoiding the risk caused by falling objects, AMRs can reduce warehouse injuries.
4. Improve Efficiency and Productivity
A 2018 poll by Gallup found that heightened employee engagement increases profits by 21%.
AMRs can support employees with picking, locating and moving inventory, allowing them to be more productive and efficient with other tasks.
Low-powered AMRs require less power to function, allowing them to recharge and minimize downtime.
5. Reduce Order Returns
A recent report found that a quarter of consumers return between 5% and 15% of items purchased online.
AMRs efficiently transport the exact items required for orders, streamlining the picking process and minimizing human error. As a result, they contribute to lower return rates by ensuring precise fulfillment of customer requests.
6. Improve Organization
With employees making their way around the warehouse, forklift trucks roaming, and shipments coming and going, the warehouse can be a chaotic environment.
A buildup of orders in your warehouse can cause clutter that clogs the dispatch area.
Mobile Industrial Robots (MiR), a Danish manufacturer of AMRs, have been collaborating with Modula vertical lift modules (VLMs) in numerous intralogistics projects to fix organization issues linked to lack of space and human resources.
The MiR AMRs are able to pick and retrieve packages from the VLM, helping to improve efficiency and keep the warehouse floor clutter-free.
Ultimately, advanced mapping technology and simultaneous location and mapping (SLAM) solutions allow AMRs to understand and adjust to their surroundings, no matter the environment or situation.
Automated Solutions at Modula
Combining autonomous mobile robots with our automated solutions at Modula helps further streamline the order fulfillment process.
Whether your operations are small or large-scale, our solutions improve picking accuracy, workflow efficiency and employee safety.
Modula’s vertical lift modules (VLMs) are fully automated vertical storage systems that take up a minimum footprint by storing items vertically to save space in your warehouse.
These vertical solutions allow for a large inventory of items to be quickly accessible while being stored in a safe environment and automatically delivered to your operators, with a simple scan of the barcode or a touch on the user-friendly Copilot controller.
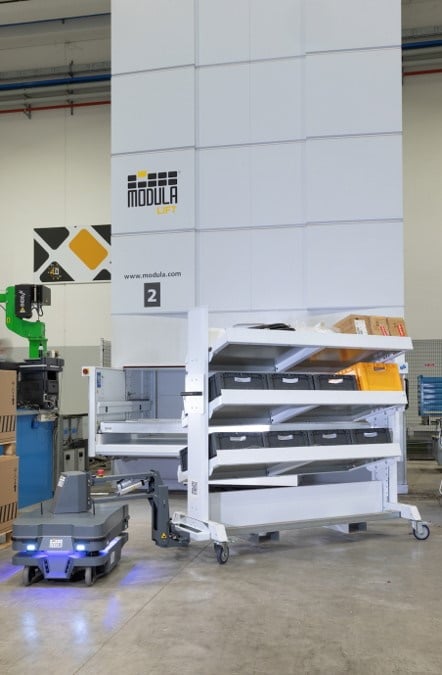
To increase accuracy, efficiency and productivity, our automated storage solutions can also be paired with our picking and warehouse software solutions.
Simple to set up, our picking solutions can help you boost picking accuracy while speeding up your throughput.
Expecting larger than usual orders? Our smart system allows you to operate in batch or multi-order modes, ensuring increased productivity without staggering the order fulfillment process.
For securely managing and monitoring your warehouse operations, Modula Cloud has you covered.
Modula Cloud is a remote warehouse management and support platform that gathers statistical data from your automated storage and retrieval systems regardless of their location.
Built-in and always on, the Cloud platform captures all of your data in an easy-to-navigate online portal from which you can securely monitor and manage your operations, from any device, anywhere in the world.
Wrapping Up On Autonomous Mobile Robots
Autonomous mobile robots (AMR) offer a streamlined solution for the warehousing industry. AMRs optimize warehouse operations and when combined with VLM’s, allow companies to store more items, access them faster, and significantly reduce the impact of the warehouse space and labor shortages.
Benefits you can expect when implementing autonomous mobile robots in your warehouse include:
- Increased storage capacity
- Employees can focus on more valuable tasks
- Increased employee safety
- Improved efficiency and productivity
- Reduced order returns
- Improved organization
At Modula, our reimagined storage and automated solutions can improve efficiency in your warehouse. Combining AMRs with other automated solutions, such as our Vertical Lift Module, can help increase accuracy and further streamline your operation.