Robots and Modula automated storage systems: Speed, efficiency, reliability, safety
In the era of Industry 4.0, robotic automated storage systems are proving their worth, particularly when high performance in warehouse logistics is required. Let’s take a closer look at the characteristics and advantages of robotics in goods storage and management systems.
Robot systems and types
A robotic storage system combines automated management systems with robotic solutions to boost the speed and efficiency of a handling process. Robots can lift heavy loads safely and never tire from doing so.
There are two types of robots that are employed with Modula automated storage systems: Cartesian and anthropomorphic.
Cartesian robots are also referred to as linear robots because they use the Cartesian linear system to handle goods. That is, they move in a straight line along the three axes of x, y, and z. While this means that Cartesian robots are limited to movement within predefined work boundaries, they are capable of precise handling, even in limited spaces.
Anthropomorphic robots – usually in the form of mechanical arms for warehouse logistics – have greater overall flexibility and a human-like hand. They are able to reach areas that are difficult to access or are on various levels.
Advantages of robotic automated storage systems
Employing robotics in automated storage systems provides several advantages, specifically:
- improved production quality and predictability
- improved work organization
- shared picking duties between humans and robots when necessary
- improved working conditions (repetitive actions and heavy loads)
- applicability for different industries and environments
- increased safety in the workplace
- adequate distancing between operators (particularly important during Covid-19 and any ongoing pandemic conditions)
- better implementation of reverse logistics
Integrating a robot into an automated storage system
Modula has developed storage systems able to work in synergy with robots to optimize goods management and picking processes.
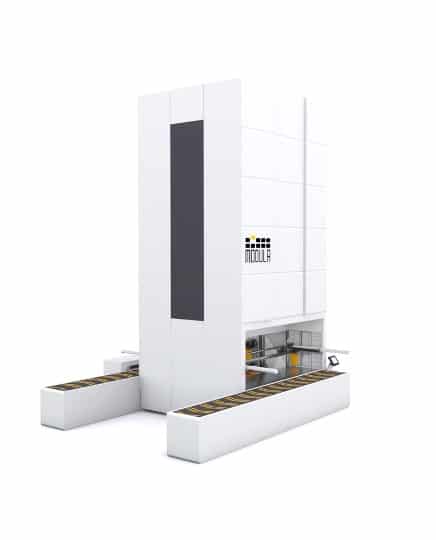
Modula storage systems can also interface with anthropomorphic robots. The robot is usually installed inside a robotic cell permanently located in front of the Modula storage system or mounted on a track to serve more than one storage system. In particular cases, the robot can be mounted on a manually or autonomously driven vehicle.
The proper functioning of the robot requires both the WMS license (which integrates the interface with a software protocol accessing the robot’s PLC memory or on server socket mode) and a robot kit installed in the electrical panel for the management of electrical signals. The combination of Modula storage systems and anthropomorphic robots is the ideal solution for handling boxes. They also can be used for “each picking” operations in which single items are picked from a specific container. Often used in distribution centers, this implementation simplifies order preparation and optimizes efficiency.
Companies that have chosen Modula’s robotic storage systems
Many companies from different sectors have integrated robots into their automated storage systems with very good results. Here are a couple of examples.
Modula robotic automated storage systems for Ford Motor Company Valencia
Ford Motor has a plant in Spain located on the outskirts of Valencia with a workforce of 8,000 and runs its production 24 hours a day, 7 days a week. Managing space and supplies has always been critical. Occasional interruptions due to parts not being in the production lines at the right time became a problem. So Ford looked for storage and handling solutions to ensure that the components necessary for production were always available.
The company installed three Modula storage systems with integrated anthropomorphic robot arms in the engine production line to guarantee production continuity. The robotic storage systems are used to handle components within the production area and as a buffer, serving also as intermediate storage areas in the event of downtime due to a malfunction in the production line.
Modula robotic automated storage systems for Speroni S.p.A.
Speroni S.p.A. is an Italian manufacturer of pumps, electric pumps, and pressure units, with a daily production capacity of over 3,000 units. To increase productivity and improve product quality, Speroni developed a fully automatic work cell within its production area, which enables the storage of both unfinished and finished pieces. Speroni decided to install a Modula storage system integrated with an anthropomorphic robot to serve the production line.
Its main function is to work 24/7 as a buffer storage area. In this way, it is possible to store a greater quantity of semi-finished and finished components and enable the workstation to operate autonomously even for long periods of time. This translates into greater flexibility in production operations and better work conditions for personnel.
Configuring a robotic automated storage system for your facility
Each robotic automated storage system is made up of three clearly different components that can be used according to specific needs: the automated storage system, the robot, and the WMS software. Modula can guide you in choosing the robotic storage system best suited for your needs.
For further information about Modula vertical and horizontal storage systems and about the solutions for integrating robots into them, contact us. One of our consultants can help you consider options to boost the speed and efficiency of your production while providing the safety and reliability that robots are known for.