The Order Fulfillment Process In 7 Steps + Best Practices for Efficiency
Order fulfillment is the process of receiving goods and shipping them to your customers within the expected timeline, yet its importance extends far beyond this basic function.
Today’s well-informed customers have high expectations, and the secret to winning them over begins in the warehouse — with a streamlined order fulfillment process.
In this article, we’ll cover all you need to know about order fulfillment, including types, the step-by-process, best practices and more.
Plus, we’ll introduce how Modula’s automated solutions can help you streamline order fulfillment, enhance picking accuracy, and ultimately boost customer satisfaction.
What is Order Fulfillment?
Order fulfillment is the process of receiving new orders and delivering them accurately within the expected timeline.
This process begins with receiving and sorting inventory and concludes with shipping orders to your customers.
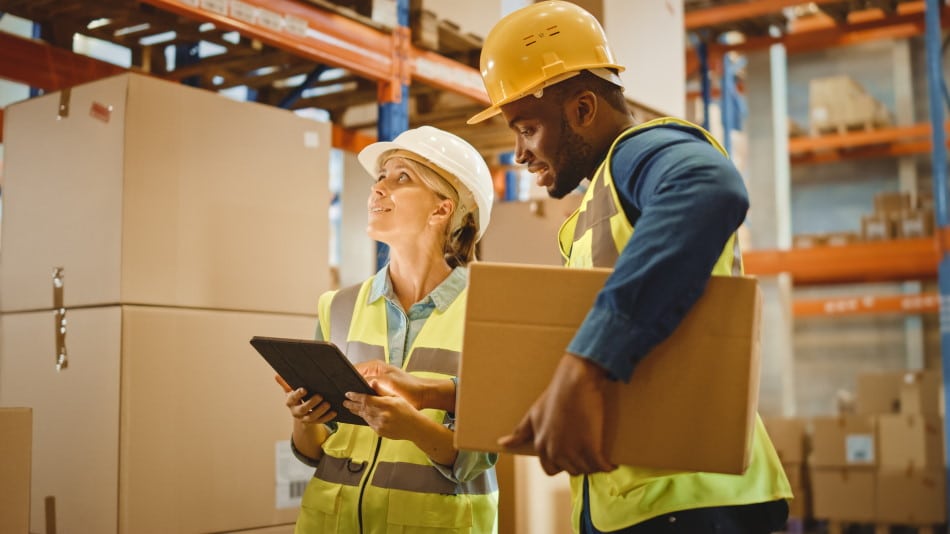
4 Types of Order Fulfillment
The best type of order fulfillment for your business depends on factors such as your industry, your volume, and budget. The four most common types include:
Dropshipping
With the dropshipping method, you rely on a third-party supplier to provide items and manage your inventory.
Here’s how dropshipping works:
- Your customer places an order
- Your warehouse operator hands over the order details to your supplier
- Your supplier fulfills the order by shipping the product directly to your customer
While dropshipping is common among start-up companies, large brands also use this method. Online retail giant Amazon, for example, allows third party suppliers to utilize dropshipping when filling customer orders.
In-house Order Fulfillment
In-house order fulfillment requires you to use your own employees to manage the order fulfillment process from start to finish, allowing you to have full control over your operation.
This method works well for small startups, where orders are typically placed in small volumes. While cost-effective, this method can be time-consuming.
However, if your startup scales into a bigger company, you can transition to outsourced order fulfillment or even hybrid order fulfillment to accommodate a larger operation.
Outsourced Order Fulfillment
Outsourced order fulfillment is handled by a third-party logistics (3PL) provider.
This method is especially beneficial if you lack storage space or access to qualified employees.
While it sounds similar to dropshipping, the difference between the two is that with an outsourced method, you are managing your inventory through your logistics partner, and not through vendors.
Hybrid Order Fulfillment
As the name implies, hybrid order fulfillment is a mix between keeping things in-house and outsourcing to a logistics partner.
If you need more flexibility with your order fulfillment process or if your company is undergoing sudden and rapid growth, hybrid order fulfillment might be the right method for you.
This method works best for companies that:
- Offer customized items that need to be pre-assembled in-house
- Sell expensive or large items that can’t be stored in-house
- Sell slow-moving (“C” product) items
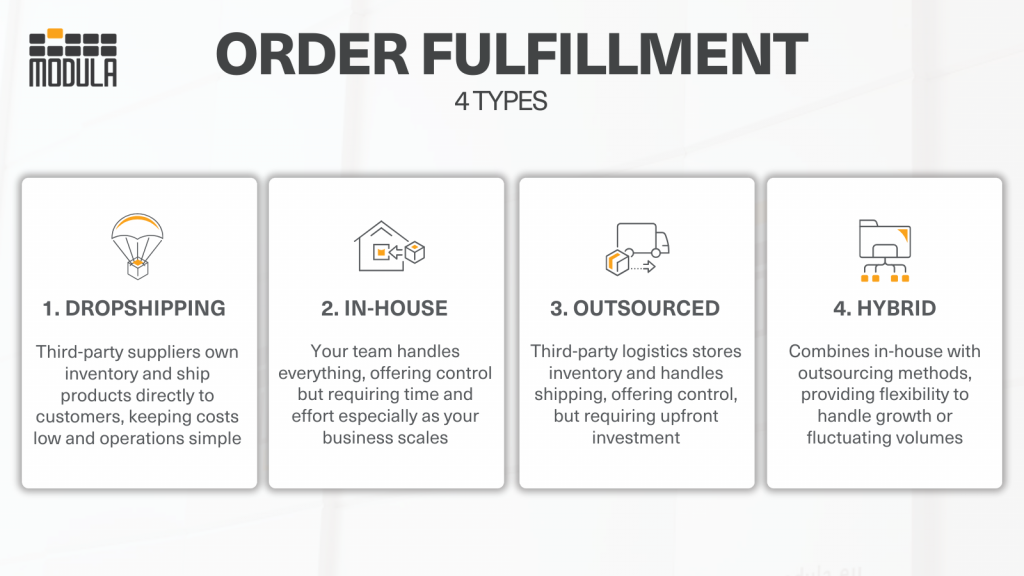
The Order Fulfillment Process
From receiving inventory to managing returned items, here is a step-by-step guide to the order fulfillment process.
1. Receiving
Receiving your inventory is the first step in the order fulfillment process. In this step, your warehouse operator identifies your inventory, typically with a barcode reader.
Next, your warehouse operator will document the inventory with the help of a warehouse management system, before storing each item in its proper location.
At Modula, our warehouse inventory management systems interface with almost all Enterprise Resource Planning (ERP) and Dealer Management Systems (DMS) systems to ensure the receiving process is quick and accurate.
2. Storing
Next, your employees transport the inventory to its designated storage area using a forklift or conveyor. They store frequently picked items in sufficient quantities on automated storage systems for easy access.
Items that are picked less frequently can be placed in pallet racks or on warehouse storage racks.
However, a major drawback of conventional shelving and racks is their inefficient use of horizontal space. These systems occupy a significant portion of your facility’s footprint, forcing pickers to travel further in the warehouse.
3. Order Processing
Once a customer places an order, your warehouse operator checks the order for accuracy and confirms product availability.
This stage also involves updating inventory levels, processing payments, and generating shipping labels or packing slips. Utilizing a warehouse management system can streamline this by maintaining real-time inventory visibility.
4. Picking
It’s time to pick the goods. Though picking might seem simple, inaccuracies can lead to costly returns, disgruntled customers, and lost revenue.
Automated picking solutions enhance accuracy and boost warehouse efficiency. These systems range from barcode validation to advanced aids like laser pointers and LED bars.
5. Sorting
The next step involves grouping and sorting SKUs into their respective orders.
For individual orders, your warehouse operator picks and packs the product directly into its shipping package. For orders with multiple items, products are picked and placed into a designated tote until completion.
The items remain together until the packing and dispatch phase.
6. Packing
Once your employee has sorted the goods, it’s time to pack your customer’s orders.
They protect fragile orders with banding or bubble wrap and include delivery instructions, product dimensions and return labels with the order.
7. Shipping
Your warehouse employee then consolidates packages in the shipping area using conveyors, trolleys, forklifts or robots.
They are then sorted by carrier type and destination, allocating each shipment to a courier service, USPS, or freight forwarder.
After an order ships, it’s paramount to send out tracking updates regarding the shipping status and delivery dates.
8. Returns Processing
The National Retail Federation projects that total returns will increase to $890 billion in 2024, from an estimated $743 billion in 2023.
When handling a customer return, inspect each item for its quality and condition.
Based on this assessment, decide whether to restock the item in your inventory or place it in the store’s clearance section. This process ensures efficient management of returned products and helps maximize your revenue potential. According to the National Retail Federation, returned items accounted for estimated $428 billion in merchandise in 2020.
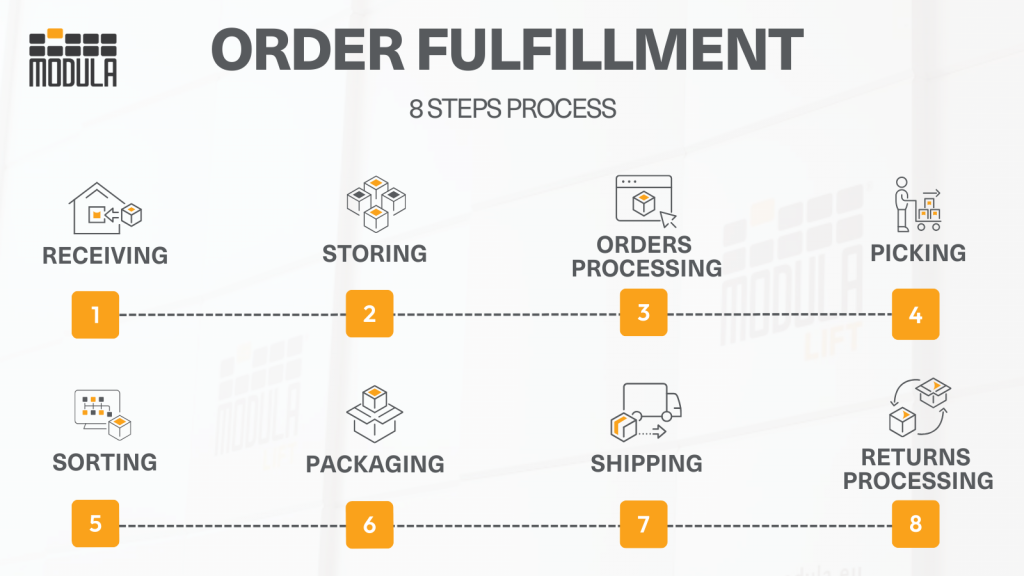
How Do You Choose the Right Order Fulfillment Strategy?
Choosing an order fulfillment strategy requires careful consideration of several key factors to align with your business’s operational capabilities and customer expectations.
Here’s how you can develop an effective order fulfillment strategy:
- Understand Your Consumer Base: Determine your customers’ expectations for delivery speed, cost and service so you can tailor your fulfillment strategy accordingly.
- Assess Your Product Type: Consider the specific needs of different products, such as perishable goods requiring faster shipping methods.
- Evaluate Your Order Volume and Scalability: Review your current order volumes and potential for future growth to ensure your strategy can handle demand fluctuations.
- Consider Geographic Distribution: If your consumer base is widespread, you may use multiple distribution centers to minimize shipping times and costs. For example, if your customers are primarily located in major metropolitan areas on both the East and West coasts, place distribution centers in New Jersey and California to reduce the distance to your primary markets.
- Choose Between In-house and Outsourced Fulfillment: Decide whether to manage fulfillment internally or outsource to 3PL providers.
- Analyze Costs: Evaluate all associated costs, including storage, labor, shipping, and technology, to maintain cost efficiency while providing high-quality service.
- Incorporate Sustainability: Consumers value sustainability and are willing to pay a 9.7% premium for it, despite concerns about the cost of living and inflation. To meet these expectations, integrate sustainable practices like eco-friendly packaging and optimized shipping routes.
- Leverage Technology and Integration: Use technology to manage inventory, process orders and track shipments efficiently through a reliable warehouse management system (WMS).
6 Best Practices for Order Fulfillment
Now that you know how the order fulfillment process works, here are some of the best practices you should use to streamline the process.
1. Automate Processes
Whether it’s picking the wrong item or misreading a packing slip, manual tasks are prone to human error, which can disrupt your order fulfillment process.
The solution? Automating processes within your warehouse.
To automate your order fulfillment process:
- Utilize automated order picking solutions to prevent mispicks
- Utilize automated storage solutions to organize inventory and streamline picking
2. Decrease Travel Time
Your warehouse operator’s travel time is paramount to the order fulfillment process. The more time they spend traveling throughout the warehouse, the less efficient the process becomes.
To reduce travel time:
- Store fast-moving items near shipping areas
- Utilize batch picking for slow-moving items
- Utilize picking aids such as pick-to-light or voice-assisted picking systems
- Automate material handling with conveyor belts and automated storage and retrieval systems (AS/RS)
3. Optimize Inventory Management
Accurately managing your inventory can help you reduce stockouts, manage costs and meet customer demands.
To better manage your inventory:
- Keep track of fast-moving items and replenish them when inventory is low
- Conduct regular inventory counts to ensure accuracy
- Utilize a warehouse management system to track stock levels, and manage and monitor the location and movement of inventory within your warehouse
- Track employee activity and restrict access to high value inventory
4. Keep Your Warehouse Organized
Organization is key to an efficient order fulfillment process.
To organize your warehouse:
- Store warehouse inventory according to demand, with hot-ticket items at the front and least popular items at the back
- Utilize labels and signs
- Group inventory using totes, bins and dividers
- Install an automated storage system to maximize floor space while keeping your inventory safe and secure
5. Optimize Your Returns Management Process
Identify methods to recycle inventory and improve customer satisfaction with a streamlined returns management process.
To optimize your returns management process:
- Designate a specific area for return items
- Establish a quality control team to receive, inspect and test return items
- Keep track of all returns, exchanges and refunds on your point of sale (POS) system
- Craft a return policy and state that all returns must be made within a specific timeframe
- Analyze return data to track and assess customer behavior
6. Offer Transparent Shipping Times
A recent survey found that 45% of online shoppers purchase from businesses that display anticipated delivery times from the get go.
Whether you’re facing seasonal demands or supply issues, giving your customers a head’s up about their package is paramount to meeting their expectations.
To maintain transparency regarding shipping and delivery:
- Provide an estimated time window for shipping at checkout
- Send an order tracking link to your customer as soon as its available
- If there’s a delay, send the customer an email as soon as possible, apologize for the delay, and provide an updated delivery window
Key Challenges of Order Fulfillment + Solutions
From demand planning to labor shortages, here are the top challenges of order fulfillment to prepare for, along with actionable solutions.
1. Demand Planning
From increased demand of turkeys and frozen pumpkin pies during Thanksgiving to beach balls and pool inflatables in the summer, predicting fluctuations in demand ahead of time can be a challenge.
To manage demand:
- Determine peak seasons by leveraging historical data
- Identify which items will be affected by seasonal demand
- Plan and order inventory before peak seasons occur
- Identify fast-moving goods and store them near the shipping area for easy access
2. Supply Chain Disruptions
As supply chain disruptions can be unpredictable, planning for them can be a challenge. But adjusting your strategy now can help lessen the impact of a disruption in the future.
To navigate supply chain disruptions:
- Localize your inventory
- Identify backup suppliers
- Create buffer storage
- Perform a supply chain vulnerability audit
3. Labor Shortages
The COVID-19 pandemic introduced a wide range of obstacles to order fulfillment, with labor shortage being the largest challenge.
To face labor shortages:
- Utilize automation to streamline time-consuming warehouse processes, such as storing and picking
- Optimize your workflows. For example, instead of traveling throughout your warehouse to pick goods, implement pick to light systems to speed up the process
How to Streamline Order Fulfillment with Modula Automated Solutions
At Modula, our automated solutions ensure a fast and accurate order fulfillment process. Regardless of the size of your operation, our solutions improve efficiency, picking accuracy and warehouse safety.
Our automated solutions include:
1. Modula Vertical Lift Modules
Modula’s vertical lift modules (VLMs) are fully automated vertical storage systems that take up a minimum footprint in your warehouse by taking advantage of high ceilings.
See the Modula VLM in action:
Modula Lift: the vertical storage system
Items can be stored up to 53 feet high in a safe and secure unit that automatically delivers them to an operator, with a touch of the user-friendly Copilot controller or the scan of a barcode.
This guarantees that the right part is delivered to the right person at the optimum ergonomic retrieval height.
2. Modula Horizontal Carousel
If your warehouse has a low ceiling, we’ve also got you covered.
With our Modula Horizontal Carousel, we provide you with a new level of performance, reliability and safety for high-speed picking operations where ceiling height is limited.
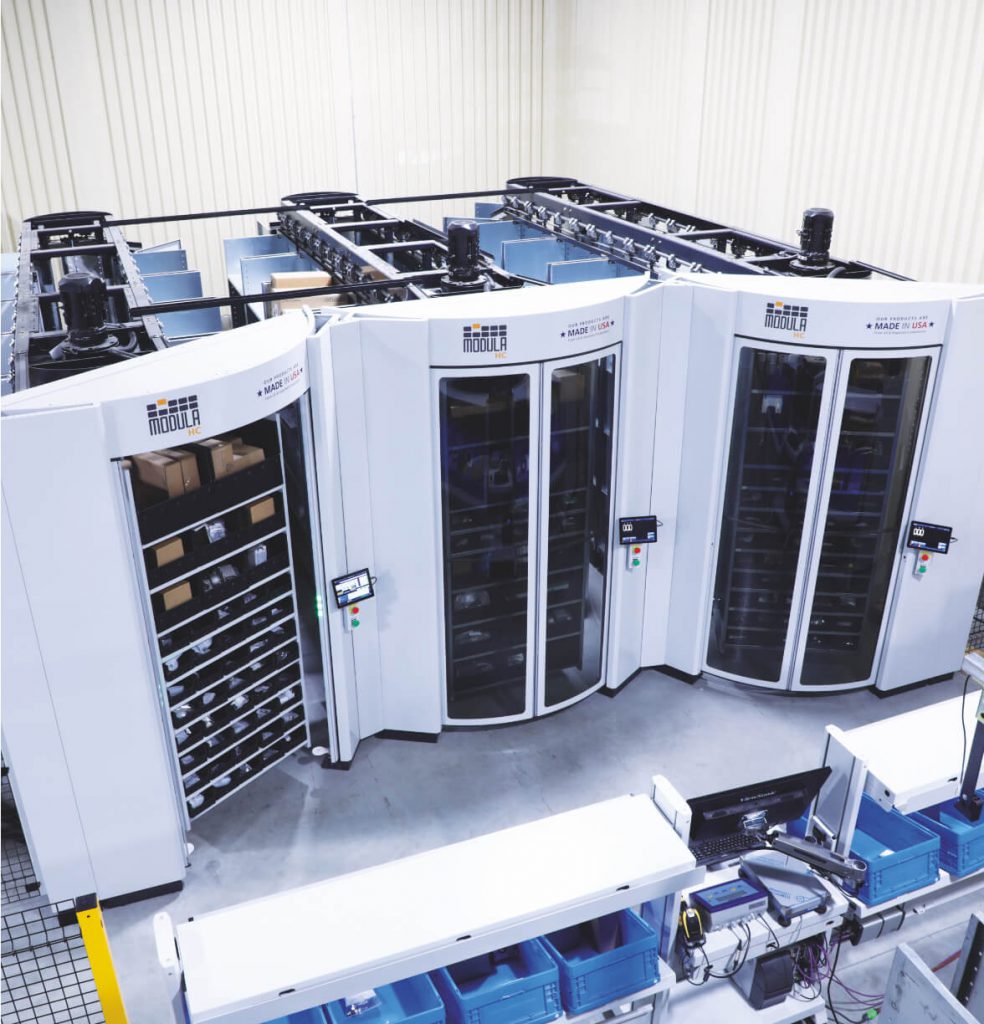
Just like our VLMs, the horizontal carousel can be used in combination with our picking solutions to achieve even higher picking performance.
3. Modula Order Picking Solutions
Easy to set up and intuitive to operate, our picking solutions are ideal for enhancing batch and multi-order processing.
See Modula’s picking solutions in action:
Modula presents the new picking solutions to automate and speed up warehouse operations
Our Modula Put to Light System is the perfect complement for our Put Cart and Put Station products.
Our smart system speeds up your throughput thanks to picking multiple orders simultaneously and helps you operate in batch or multi-order modes.
From minimizing picking errors and boosting labor efficiency to improving your inventory accuracy, you’ll never go back to using shipping lists or picking tickets.
4. Modula Warehouse Management Systems
Take your order fulfillment to the next level with our warehouse management solutions to boost productivity, accuracy and efficiency.
Our Warehouse Management Solutions allow you to gain control and visibility over your inventory, manage and monitor individual items, and keep track of orders, including order processing, shipping and delivery.
Key Takeaways on Order Fulfillment Processing
From minimizing picking errors and boosting labor efficiency to improving inventory accuracy, automated solutions play a key role in a streamlined order fulfillment process.
At Modula, our solutions allow you to meet and exceed your customer’s expectations, increase their satisfaction and run an efficient operation, from start to finish.