30 Tips To Boost Warehouse Efficiency in 2024
An efficient warehouse is one that is organized, productive and cost-effective.
We’ll share 30 tips to help you improve warehouse efficiency, and introduce you to our automated solutions at Modula that can help you further streamline your warehouse operations.
What is an Efficient Warehouse?
Warehouse efficiency is an approach meant to optimize warehouse operations. It encompasses a wide range of solutions and best practices to boost productivity and reduce operational costs.
How To Measure Warehouse Efficiency
To effectively gauge how efficiently your warehouse is functioning:
- Conduct regular operational audits: Audits allow you to evaluate your warehouse processes and help you identify bottlenecks or potential risks. Schedule periodic audits, either internally or with third-party experts. Make sure these assessments examine processes, equipment, personnel, and technology.
- Establish KPIs for your warehouse: Key performance indicators (KPIs), such as receiving cycle time, put away productivity and space utilization, are quantifiable measures that can provide insights into the performance and productivity of your workers. These metrics allow you to identify bottlenecks, monitor progress and optimize overall warehouse performance.
- Track inventory accuracy: Make sure that your recorded inventory matches your physical stock to prevent discrepancies that can lead to costly stockouts or overstocks.
- Monitor equipment efficiency: Keep a log of equipment maintenance schedules, unexpected downtimes and the efficiency of machinery during operation. A detailed log will help you reduce equipment downtime and ensure tasks are performed optimally.
- Evaluate storage and layout efficiency: Periodically review your warehouse layout, while considering factors such as product demand, seasonality and inventory turnover. Adjust storage solutions when necessary to reduce travel time and make sure goods are easily accessible.
- Gather feedback from your warehouse employees: Hold regular feedback sessions or suggestion programs. By listening to your employees, you can identify and address warehouse issues.
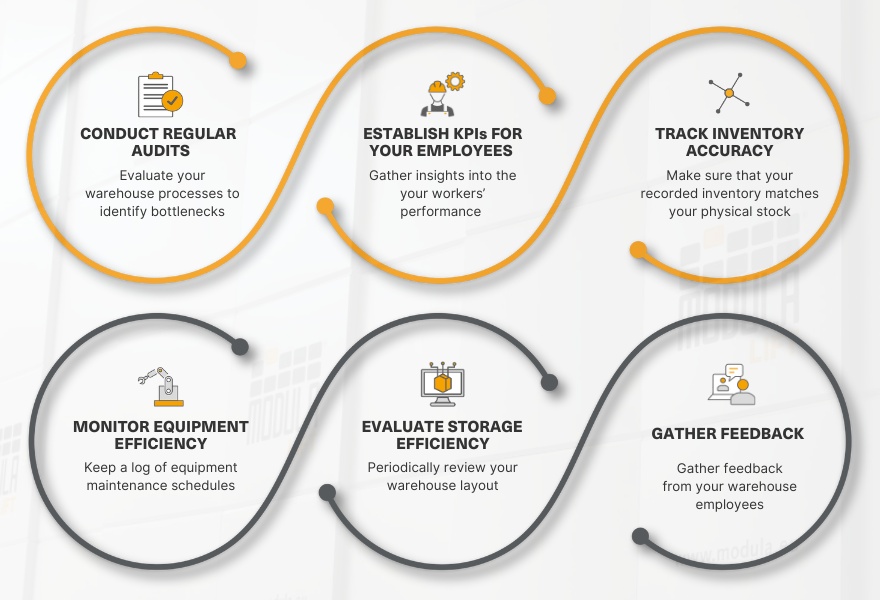
30 Expert Tips for Optimal Warehousing Efficiency
You can boost productivity and overall efficiency in your warehouse by refining workflows, automating tasks and cutting waste in time and resources.
If you’re wondering how, here are 30 warehouse efficiency tips you can leverage to boost your overall operations.
Eliminate Unnecessary Movements
Eliminating unnecessary movements can help optimize workflows and reduce the time it takes to complete tasks. To eliminate unnecessary movements in your warehouse, implement a strategic layout design.
For example, design your warehouse in a U-shape to ensure a seamless flow and reduce foot traffic, from receiving to shipping.
Maximize Your Warehouse Space
Making the most of your existing warehouse space means setting up a strategic layout and implementing smart storage solutions.
Optimize your warehouse space by investing in automated storage solutions like vertical lift modules (VLMs) and horizontal carousels (HC).
Both vertical and horizontal solutions can reduce warehouse space requirements by up to 90%.

Organize Your Workstations
Organizing your workstations can help minimize unnecessary movements, reduce the risk of errors, boost productivity and ensure that your workers can easily access the tools they need.
To organize your workstations, store SKUs based on how frequently they are used. For example, place high-frequency items closer to the workstation, while less frequently used items can be positioned slightly farther away.
Boost Picking Accuracy
Lack of accuracy in warehouse operations can lead to unhappy consumers and ultimately, lost revenue.
Guide your picking operators and tell them exactly what inventory to pull from each slot by leveraging automated warehouse picking robots and order picking solutions, including put to light systems, and picking aids such as voice picking technology.
Utilize Cross Docking
Cross docking is a warehouse strategy in which inventory is unloaded from incoming shipments and is immediately dispatched onto outbound shipments, without the need for long-term storage in your warehouse.
This warehouse strategy can help reduce the time and resources required for storing, retrieving and handling inventory.
Perform Cycle Counts
Cycle counting is a process in which goods are checked to match inventory records by conducting an inventory check — typically every month or quarter.
This process can help you identify inventory discrepancies early on to ensure accurate stock levels and boost inventory accuracy.
Identify the Ideal Order Picking Method
From single order to wave order picking, the order picking method that you choose is key to your warehouse operations, as quick and accurate order fulfillment is closely tied to customer satisfaction.
The method you select depends on how big your warehouse is, how much inventory you have and how many orders you get each day, among other factors.
For example, during Black Friday sales, consider utilizing batch picking to efficiently handle the increased order volume.
Conduct Inventory Forecasting
Inventory forecasting is the process of predicting the amount of goods required to meet future demand based on your historical sales data, current trends and external factors, such as seasonal changes.
Forecasting can help you prevent stockouts and overstocks.

Manage Inventory in Real-Time
If your warehouse stores a wide range of SKUs, monitoring your stock in real-time can help you make sure that you have the right products in the right quantities, at the right time.
Real-time inventory monitoring allows you to track stock levels and quickly identify when stock is running low, allowing you to replenish inventory before it runs out.
Implement Labels and Signs
Utilize product safety labels or hazard warning labels to notify your employees about potential hazards of warehouse equipment and tools — like an ongoing forklift operation.
To promote warehouse safety using labels and signs:
- Use color-coded signs that can be recognized from long distances to warn operators of potential danger
- Install signs at eye-level to make them noticeable
- Add floor markings using color-coded tape — for example, mark your floors with yellow and black lines to act as safety hazard markings
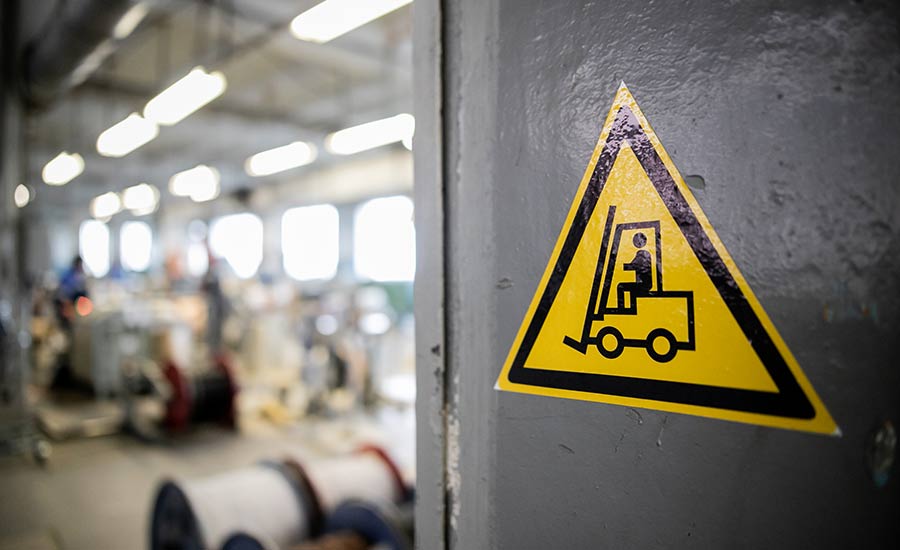
Conduct ABC Analysis
ABC analysis is an inventory management technique that prioritizes inventory items based on their significance, with the following categories:
- Class A inventory, which represents your most valuable items
- Class B inventory, which represents items that have a moderate impact on your inventory
- Class C inventory, which represents your least valuable items
Conducting an ABC analysis can help you optimize storage by keeping important items closer to picking areas, reducing retrieval times.
Leverage a Custom Inventory Replenishment Strategy
Leveraging a custom inventory replenishment strategy can help you tailor the restocking process to your specific needs, to ensure that your inventory levels are optimized for demand while minimizing excess stock and associated holding costs.
Let’s say you have a seasonal apparel business. You can set replenishment triggers based on the changing fashion trends and weather patterns, in which you’ll stock more winter wear before the cold season starts and reduce it before spring approaches.
Utilize Tracking Identification Technologies
Warehouse tracking identification technologies are tools designed to monitor your inventory and track shipped orders.
These technologies range from traditional barcoding systems to advanced RFID tags and Internet of Things (IoT) devices.
Tracking identification technologies include:
- Barcode scanning systems: As goods are packed, they are scanned using barcode scanners. Once an order is shipped, a final scan is done, updating the system that the order is on its way.
- Internet of Things (IoT) devices: Smart warehouses utilize IoT devices for monitoring facility conditions, like temperature for sensitive goods, and making sure these conditions are maintained during transit.
- Warehouse management system (WMS): A WMS is a solution that can help you manage products by gaining full visibility into your inventory. When an order is shipped, the WMS updates your system with the order status.

Utilize a Warehouse Management System
A warehouse management system is software that provides a bird’s eye view of your inventory. It enhances picking accuracy by suggesting optimal routes and offers real time inventory tracking.
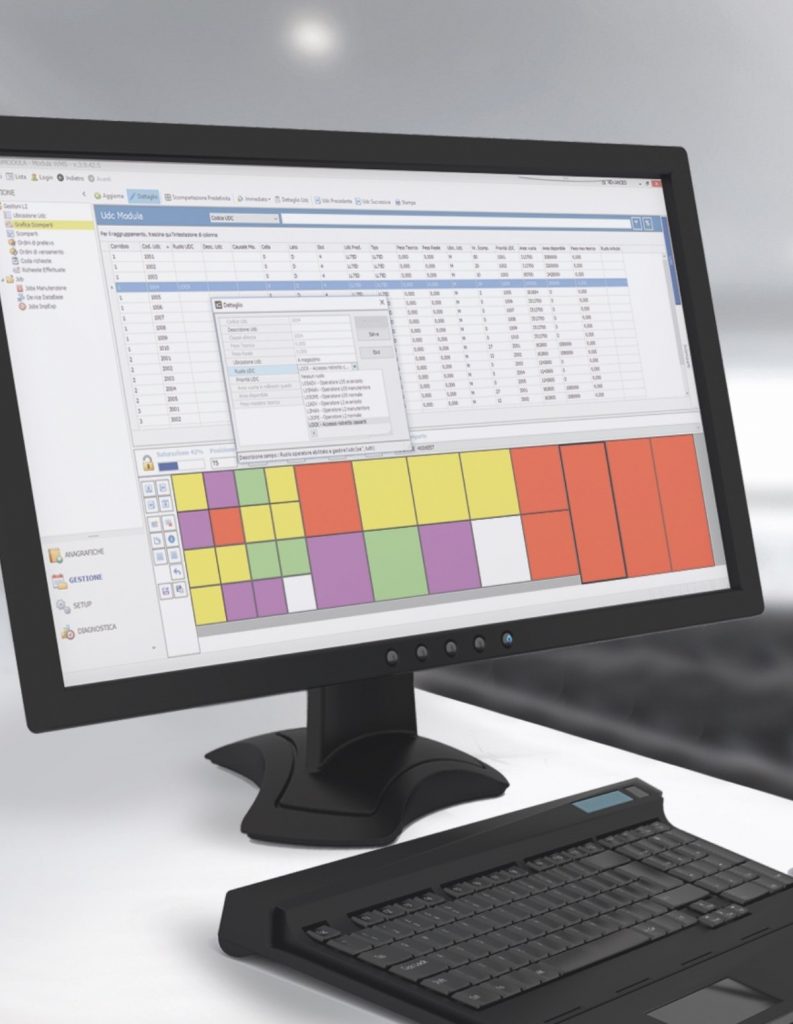
Utilize Warehouse Drones
Warehouse drones, also known as unmanned aerial vehicles, can help replenish your stock and manage inventory. Equipped with sensors and cameras, they can fly through warehouse aisles and scan barcodes or RFID tags to determine your stock levels.
Warehouse drones can also quickly and efficiently transport products from storage locations to picking areas, reducing the need for manual labor.
Take Advantage of Robots
Taking advantage of warehouse robots can help you reduce warehouse travel, automate repetitive tasks and optimize storage space.
Warehouse robots include automated guided vehicles (AGVs), autonomous mobile robots (AMRs), and automated picking robots.
Utilize Warehouse Slotting
Warehouse slotting is the process of arranging inventory in your warehouse to help you optimize storage space and improve picking efficiency.
To implement warehouse slotting, group inventory that is frequently picked together in a similar storage area and store bulky inventory away from small parts.
Boost Inventory Security
Boosting inventory security can help you improve your warehouse efficiency by minimizing losses due to theft, damage or misplacement, leading to reduced warehouse costs and more accurate stock levels.
To improve your inventory security:
- Implement access controls: Use biometric systems and PIN codes to limit access to your inventory
- Use surveillance systems: Install CCTV cameras to monitor warehouse activities
- Invest in alarm systems: Install alarms that can detect unauthorized access, during both operating and non-operating hours
Optimize Your Returns Process
Optimizing your returns process can help you improve your warehouse efficiency, as it reduces the time and resources spent on handling returned items.
To optimize your returns process, implement a clear returns policy and designate a specific area in the warehouse for returns.
Implement Lean Warehousing
Lean warehousing is an approach that removes unnecessary warehouse activities to reduce waste and boost productivity.
This approach can help improve your warehouse efficiency, as it reduces operational costs and ensures that resources are utilized strategically.
To practice lean warehousing:
- Implement continuous improvement by frequently reassessing and tweaking your operations for better results
- Embrace the “5S” methodology: Sort, Set in order, Shine, Standardize and Sustain to organize and maintain your warehouse space
- Reduce waste by identifying and eliminating non-value-added activities, such as unnecessary transport or waiting times
(Read our guide on lean warehousing to learn more about principles and best practices!)
Build a Sustainable Warehouse
A sustainable warehouse is a facility that incorporates eco-friendly practices, such as leveraging solar panels and implementing green roofing. These practices allow you to minimize waste and energy consumption in your facility.
To build a sustainable warehouse:
- Conduct an energy audit: Understand where your energy is consumed most in your facility and identify areas for improvement
- Install energy-efficient warehouse equipment: Opt for green technologies, such as LED lighting and energy-efficient HVAC systems
- Invest in insulation: Proper insulation can help regulate indoor temperatures, reducing heating and cooling costs
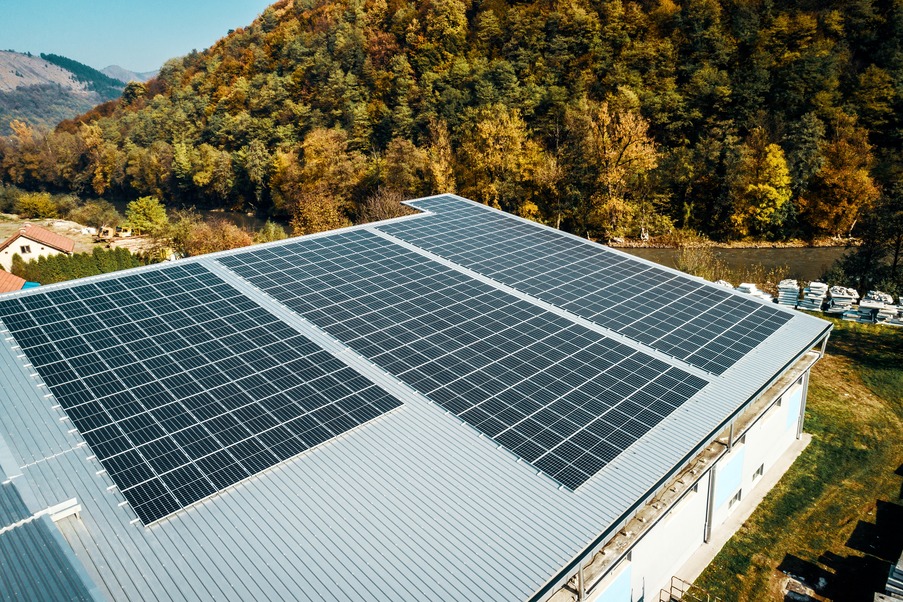
Prioritize Employee Safety
Workplace accidents, including falling, being struck by an object, or getting caught in equipment, can be extremely serious. Prioritizing employee safety can help improve your warehouse efficiency by boosting productivity, increasing morale and reducing downtime.
To prioritize employee safety in your warehouse operations, conduct training sessions on safety protocols and make sure your employees wear the appropriate PPE, such as helmets, safety glasses and high-visibility vests.

Cross-Train Employees
Cross-train your employees to reduce downtime, improve collaboration and minimize turnover costs.
For example, if your forklift operator is taking paid time off, a cross-trained employee can step in to make sure that shipments are processed on time.
Provide Detailed Warehouse Training
Make sure your warehouse employees know exactly how your equipment works and are able to effectively navigate your warehouse’s layout with end-to-end warehouse training.
Integrate AR and VR technologies into your warehouse training program to onboard employees regarding different warehouse processes.
For example, you can utilize a 360° VR headset to introduce your operators to picking locations before they even step foot into your facility.
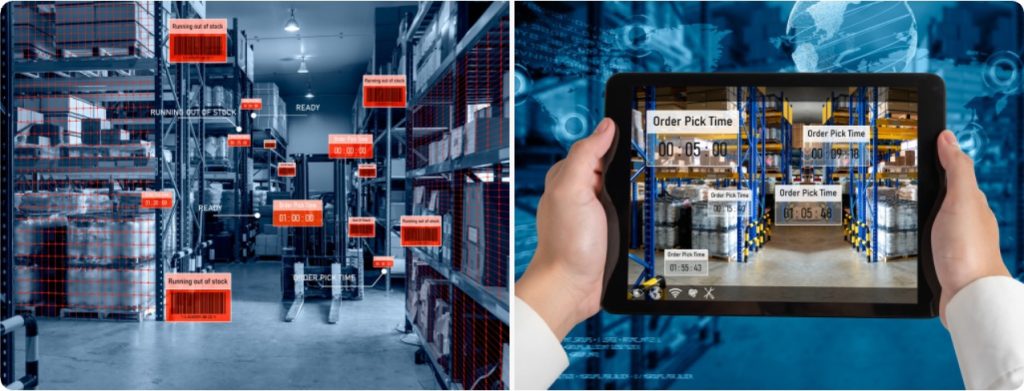
Utilize Gamification
Gamification is the process of applying game-design elements and principles, such as point scoring, competitions and achievements, to your warehouse operations.
By turning routine tasks into challenges or competitions, your employees are incentivized to improve their performance and develop a deeper sense of purpose in their roles.
To utilize gamification, introduce a leaderboard system where employees earn points for accurately picking items, achieving faster packing times or maintaining safety protocols.
Provide Employee Incentives
Offer employee incentives, such as monetary bonuses and health and wellness reimbursements, to boost employee morale, promote healthy competition and encourage continuous learning.
For example, implement a monthly bonus system for the top-performing teams in your warehouse.
Hire an Efficient Frontline Manager
Hiring an efficient frontline manager can help you allocate resources effectively and ensure that safety regulations are adhered to, minimizing accidents and disruptions.
For example, a skilled frontline manager can implement a rotating shift system, optimizing labor hours based on peak operation times.
Hire a Warehousing Expert
Hiring a warehousing expert can help you optimize storage layouts and implement efficient inventory management practices.
For example, an expert can redesign your warehouse layout to reduce the travel time for your warehouse pickers or introduce a just-in-time inventory system to reduce storage holding costs.
Collaborate With Suppliers
Collaborating with suppliers can help improve warehouse efficiency by ensuring timely deliveries, optimizing inventory levels and reducing lead times.
By sharing sales forecasts and inventory data with your suppliers, they can better anticipate your stock needs, leading to more accurate order quantities and delivery schedules.
Automated Solutions To Improve Warehouse Efficiency
As the pioneer of cutting-edge storage and inventory management solutions, Modula provides advanced innovations designed to optimize your warehouse operations and boost profitability.
At Modula, our automated solutions include:
Modula Vertical Lift Modules
Our vertical lift modules are fully automated vertical storage systems that use minimal floor space by taking advantage of high ceilings.
Modula vertical lift modules are available in three models:
- Modula Lift: Improve your warehouse efficiency and achieve up to 90% faster and more accurate picking with our most popular vertical lift module.
- Modula Slim: Experience the same efficiency of the Modula Lift in a sleeker, space-saving design — ideal for more compact storage spaces.
Modula Horizontal Carousels
A horizontal carousel is the ideal storage solution when ceiling height is limited.
The Modula HC enables you to optimize space, boost throughput, cut labor costs and simplify storage and retrieval with minimal labor.
Modula Order Picking Solutions
Our picking solutions enhance batch and multi-order processes. Integrate them with our storage solutions to ensure better order accuracy and efficiency.
Modula order picking solutions include:
- Modula Put to Light: Guides pickers to the right zone
- Mobile Picking Station: Speeds up bulk order processing
- Modula Picking Cart: Transports inventory within your warehouse
- Modula Mobile Picking App: Allows you to handle picking tasks anytime, anywhere
Modula Warehouse Management System
Improve inventory control, manage your goods, assign tasks, set access permissions and more with Modula’s Warehouse Management System.
Modula’s WMS improves the efficiency of your warehouse operations while providing clear visibility into your stock levels. It syncs with Modula Vertical Lift Modules and local ERP systems for an end-to-end warehouse solution.
Warehousing Efficiency Solutions: A Look at Our Modula Case Studies
From improving performance, efficiency, and safety to reducing space demands and inventory errors, our warehouse automation solutions provide measurable results for businesses across industries.
1. Dassault Falcon Jet
The challenge:
Dassault Falcon Jet, Dassault Aviation’s subsidiary, which has a distribution center for large aircraft parts and headquarters in Teterboro, NJ, was experiencing delivery issues.
Aircraft parts were taking too long to deliver and since they were using a traditional shelving warehouse system, picking errors were common. They needed automated solutions to cut back on the time it took to find the right parts.
The solution:
Dassault installed three 25-foot-tall Vertical Lift Modules. Thanks to these modules, Dassault’s employees can now find an aircraft part in less than a minute, compared to the five minutes it took when they were relying on manual pickers.
2. Innomed Inc.
The challenge:
Innomed Inc., a Georgia-based company that manufactures orthopedic surgical instruments, was facing storage issues that affected their lead time. They needed a permanent storage location for their expanding inventory of surgical instruments but they were unable to move to a bigger warehouse.
The solution:
To help accommodate their growing inventory of surgical instruments, the company installed four Modula Vertical Lift Modules in their warehouse. The modules streamlined their process accelerated their lead times, providing significant time savings in inventory stocking and order fulfillment.
3. GF Machining Solutions
GF Machining Solutions’ North American logistics hub offers overnight delivery to their North American customers. Due to growing demand, they needed to expand secure storage capabilities, while boosting speed and accuracy.
The solution:
Modula’s vertical lift modules helped GF Machining boost their floor capacity and efficiency. With more space, they were able to create new work zones, improving the overall flow on the floor.
They also utilized unique productivity features such as Dual Delivery Trays, which are equipped with a laser pointer and guided light bar. These solutions dramatically improved picking speed and accuracy.
At Modula, our automated solutions can help optimize your warehouse operations by boosting productivity, improving picking accuracy and ensuring your employees are safe, from the moment goods enter your facility until they are dispatched to consumers’ doorsteps.