Essential Warehouse Equipment List [Types and Benefits]
Choosing the right mix of equipment is crucial for warehouses aiming to enhance efficiency, safety, and profitability.
In sectors where adapting swiftly to consumer demands and evolving business landscapes is the norm, the right warehouse equipment becomes the backbone of flexibility and scalability.
It ensures that operations can adjust as needed, scaling up or down without sacrificing performance or safety.
Warehouses — whether part of manufacturing facilities or standalone distribution centers — must be equipped with tools that not only meet current needs but also anticipate future challenges.
In this article, we will cover essential warehouse equipment categories, highlighting their benefits. Plus, we will introduce you to the advanced warehousing solutions offered by Modula.
What Is Warehouse Equipment?
Warehouse equipment encompasses a wide range of tools, machines, vehicles and storage solutions to facilitate inventory management, storage, retrieval and transportation of goods, within a warehouse setting.
This type of equipment allows you to optimize warehouse operations and improve efficiency, safety and productivity.
Types of Warehouse Equipment
Warehouses come in all shapes and sizes, but they all share a common purpose: to store and move inventory efficiently and protect goods during shipment.
To achieve this, warehouses rely on a variety of specialized equipment.
Here’s a list of warehouse equipment:
Storage Equipment
This category is pivotal to the smooth running of any warehouse operation and includes everything used to organize and store goods in the warehouse.
Storage systems can help warehouses maximize existing vertical or horizontal space and ensure inventory is accessible for easy retrieval.
The most common types of storage equipment within a warehouse include:
- Pallet racks: Stores bulky goods on pallets.
- Shelving: Ideal for organizing smaller items, parts, or boxes.
- Cantilever racks: Perfect for long and bulky items like lumber or pipes.
- Bins and Drawers: Organizes and stores small parts, tools, and other miscellaneous items.
- Lockers: Secures storage for valuables, personal belongings, or hazardous materials.
- Mezzanines: Creates additional storage space within the existing warehouse footprint by utilizing vertical space.
Material Handling Equipment
Material handling equipment encompasses any equipment used to move, store, control, and protect materials throughout the entire supply chain.
The most common types include:
- Forklifts: These vehicles lift, move, and stack heavy loads.
- Pallet jacks: Workers use these manual or powered tools to lift and move pallets over short distances within a warehouse.
- Order pickers: Human operators use these machines to retrieve, handle, and transport inventory in various warehouse tasks.
- Conveyor belts: These automated systems transport goods along a fixed path, enhancing efficiency by moving items from one point to another within the facility.
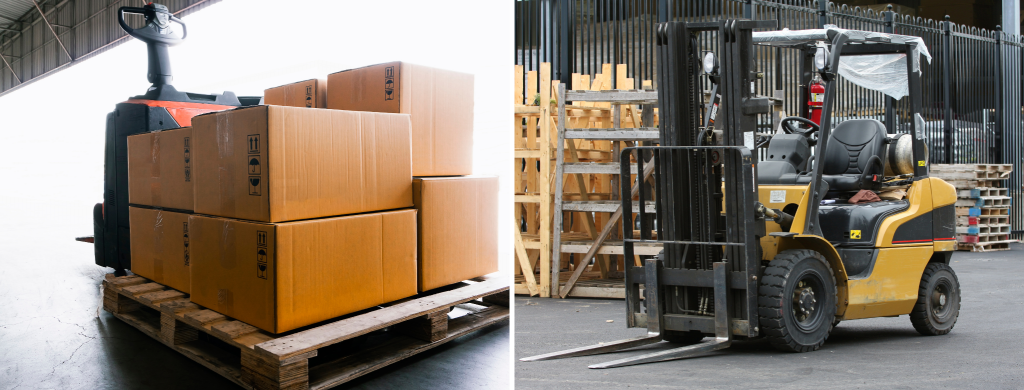
Dock Equipment
This type of equipment ensures the safe and efficient loading and unloading of goods to and from dock doors.
Common examples of dock equipment include:
- Dock boards and dock levelers: Bridges the gap between the warehouse floor and truck, making it easier to transfer goods.
- Loading ramps: Provides access from the warehouse to the vehicle, accommodating various heights and loads.
- Dock seals and shelters: Protects inventory from external contaminants, such as dust, moisture and insects, by creating a tight seal between the loading dock and the trailer.
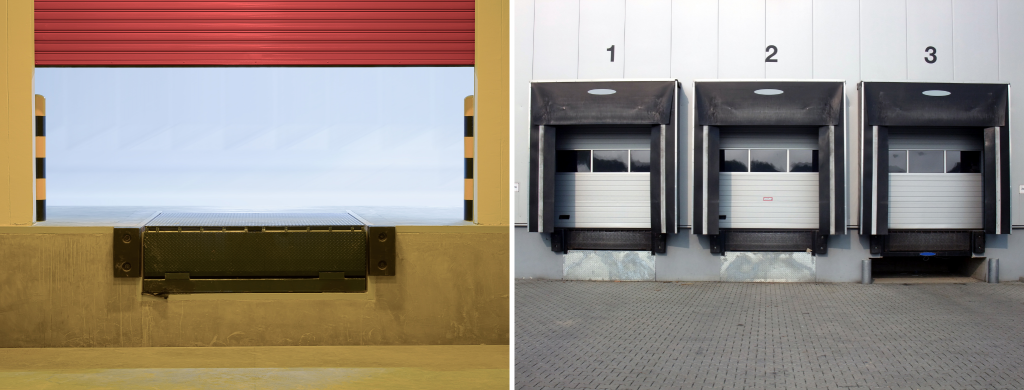
Packaging and Shipping Equipment
Packaging equipment allows you to enclose and protect inventory by placing it in containers for storage, distribution and shipment.
This type of equipment includes:
- Stretch wrap machines: Automatically wraps loads with stretch film to secure items for transport or storage.
- Labeling and Marking Systems: Applies labels and markers on goods for identification, tracking, and compliance with shipping regulations.
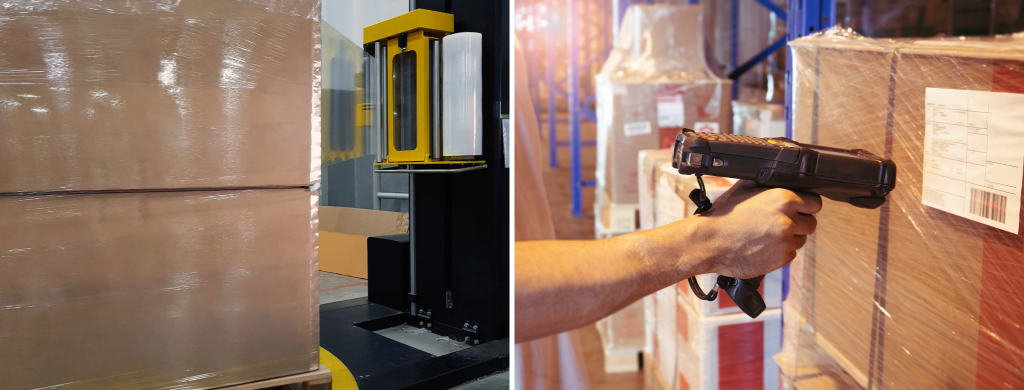
Safety and Security Equipment
Warehouse safety equipment refers to tools, devices, and solutions designed to protect employees, minimize the risk of accidents, and enhance overall safety within warehouse environments.
Here are some common types of warehouse safety equipment:
- Personal Protective Equipment (PPE): Includes helmets, gloves, eye protection, high-visibility clothing and safety footwear.
- Safety barriers and signs: Designate safe walking paths, highlight hazardous areas and communicate safety instructions.
- Fire safety equipment: This includes fire extinguishers, fire alarms and sprinkler systems
Warehouse Automation
Warehouse automation is an ever-evolving category that plays a key role in modernizing and streamlining warehouse operations. It encompasses various technologies that aim to reduce manual labor, enhance accuracy, and improve safety.
Warehouses automate routine tasks to handle more volume with greater efficiency, allowing them to respond quickly to market demands.
While some of these technologies overlap with other categories of warehouse equipment, such as material handling or storage, their distinct ability to automate processes sets them apart.
This category includes:
- Robotic picking systems: These robots are equipped with advanced camera or scanner systems to identify, locate and pick items on shelves or within designated bins. Picking robots can seamlessly collaborate with human pickers, assisting with high-volume tasks, or they can operate autonomously in dedicated picking zones.
- Automated Guided Vehicles (AGVs) and Autonomous Mobile Robots (AMRs): AGVs and AMRs are similar to self-driving carts that move items around the warehouse. They follow digital maps or sensors on the floor to go exactly where they need to, making the movement of goods faster and cutting down on the need for people to carry things.
- Automated Storage and Retrieval Systems (AS/RS): ASRS are high-density storage solutions that automatically place and retrieve items, optimizing space and speeding up operations. These warehouse equipment streamlines inventory management by integrating with Warehouse Management Systems (WMS) or Warehouse Execution Systems (WES). They encompass various automated solutions like tote shuttles, mini-loaders, unit-loaders, horizontal carousels, and vertical lift modules, each designed to optimize space and accelerate operations.
- Warehouse Management Systems (WMS): The WMS Software controls everything in the warehouse. It keeps track of inventory, manages orders, and makes sure everything runs smoothly from when an order comes in until it’s shipped out.
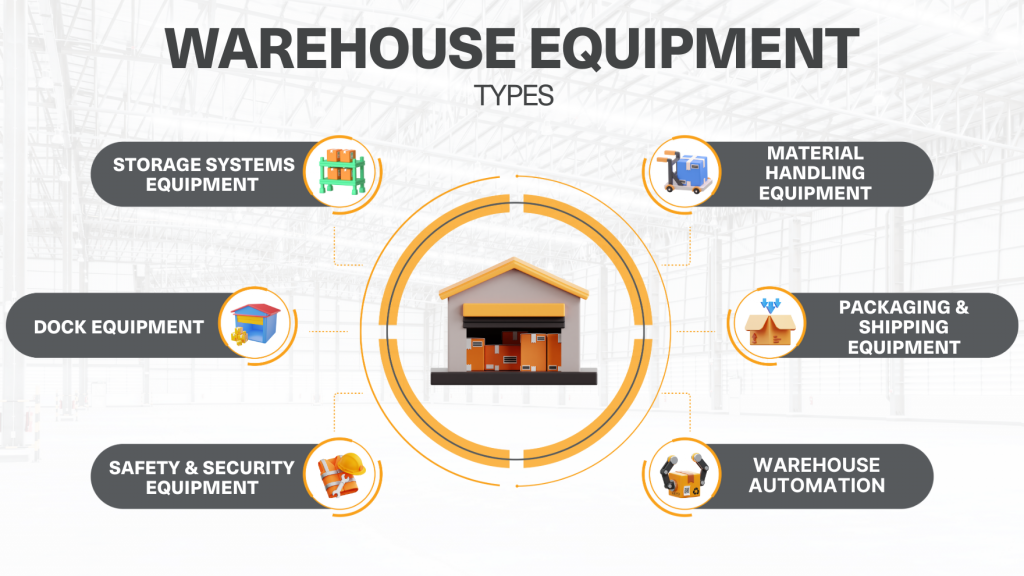
How to Choose Warehouse Equipment for Your Operations
Choosing the right warehouse equipment for your business allows you to maximize efficiency, boost productivity and significantly reduce handling times.
Here’s a comprehensive guide to help you make the right choice:
- Assess your needs: Evaluate and understand your warehouse operations to identify the types of SKUs your facility handles. Consider factors like the volume of goods and any specific requirements like temperature control or hazardous material storage. Do you need equipment for heavy lifting and large pallet movement? Or are you looking for solutions to store smaller, more fragile items that are prone to misplacement?
- Calculate space availability: Measure your warehouse space to understand how much room you have for equipment and how to maximize its use efficiently. For example, if your facility has limited floor space but with high ceilings, consider investing in vertical storage solutions, like automated vertical lift modules (VLMs).
- Consider scalability: Choose equipment that can grow with your business. Look for modular or adjustable options that can be expanded or reconfigured as needed.
- Prioritize safety: Select equipment that enhances safety in the workplace. Consider features like built-in safety guards, emergency stops and ergonomic designs.
- Evaluate technology integration: Opt for equipment that can integrate with your warehouse management system (WMS) to improve inventory accuracy and streamline operations.
- Compare costs and benefits: Analyze the cost of each equipment against its benefits. For example, mobile pallet racking has lower initial costs than vertical lift modules (VLMs), but VLMs can save up to 90% of floor space over traditional storage. This space efficiency can lead to long-term savings by increasing efficiency and cutting labor costs.
- Consider the environmental impact of each equipment: Choose equipment that is sustainable and environmentally friendly to reduce your carbon footprint and potentially save on energy costs.
- Plan the maintenance aspect: Understand the maintenance requirements of each equipment. Make sure you have the resources to keep it in optimal working condition or check if the supplier offers maintenance services.
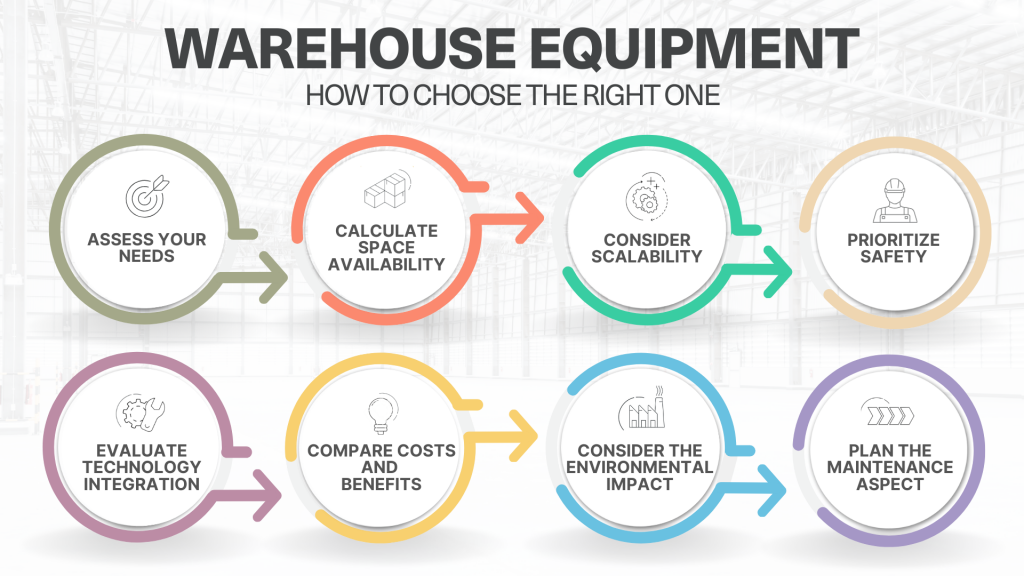
Benefits of Utilizing Warehousing Equipment
Warehouse equipment provides different benefits, including improved efficiency, better space utilization and enhanced safety.
Warehousing equipment allows you to:
Maximize Storage Space
Instead of moving to a bigger warehouse that can cost an estimated $8 per square foot, warehouse equipment can improve storage efficiency by optimizing your facility’s available space.
By using equipment like mezzanines, pallet racks and vertical storage solutions, warehouses can store more goods without sacrificing valuable floor space.
At Modula, our innovative automated storage solutions and retrieval systems (ASRS) can help you save floor space by consolidating operations into a smaller, more efficient footprint near areas where they are needed. This optimizes workflow and reduces the need for off-site storage.
Cut Costs
According to Cascade Energy, energy consumption is the second largest operating expense in refrigerated facilities, which is second to labor costs.
In warehouses related to food distribution and grocery stores, refrigeration accounts for about 50% of the total energy used. In addition, this percentage rises to 65–75% in facilities that are fully refrigerated.
By utilizing the right automated warehouse equipment, you can lower your overall expenses, on top of reducing your carbon dioxide emissions.
For example, Modula’s vertical lift modules and horizontal carousels only consume energy when your warehouse employees activate them. And when they’re not in use, they remain electrically dormant — consuming minimal energy. This feature can help you reduce electricity costs.
Boost Productivity
Automated systems like conveyors and sorting machines speed up the movement of goods, reducing manual labor and increasing throughput. This leads to faster order processing and delivery times.
Improve Employee Safety
Choosing and installing the right tools and equipment reduces workplace hazards, such as overexertion when reaching goods.
For example, safety barriers, anti-slip flooring and ergonomic lifting equipment can help protect employees from accidents and injuries.
At Modula, we offer the Modula Next, which operates on a goods-to-person principle. When an operator requests an item, it retrieves the tray with the item and delivers it to the picking bay at an ergonomic height.
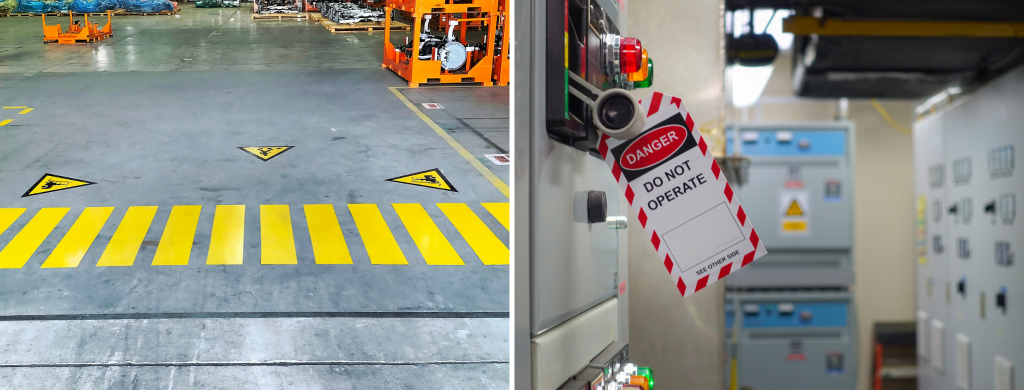
Gain Insights Into Real-Time Stock Levels
With sophisticated warehouse management systems, your business can maintain accurate inventory levels. Advanced WMS can also help minimize errors, further reducing overstock and preventing stockouts.
Modula’s Warehouse Management System (WMS) is designed to work smoothly with our advanced automated storage systems, ensuring an integrated and efficient management process.
It’s tailored to enhance operations with a simple interface for easy management and real-time inventory tracking.
Final Words on Warehouse Equipment
To recap, warehouse equipment includes various tools, machines, vehicles and storage options for managing, storing, retrieving and transporting goods.
Warehousing equipment can help optimize operations, enhance efficiency, safety and productivity.
To select the right equipment for your operations, consider factors such as the size and layout of your warehouse, the types of goods you handle, your inventory volume and specific storage needs.
In addition, evaluate the scalability of equipment to accommodate future growth and technological advancements to ensure long-term effectiveness and cost-efficiency.
At Modula, we provide cutting-edge automated solutions to help with your warehouse logistics.
Get in touch with our team to see how we can customize our technology for you. Our experts are here to offer tailored advice and solutions for your warehouse.