What Is a Tote? [+ Its Key Role in Material Handling]
In any industrial or warehousing operation, a well-organized inventory is key to improving productivity, processes and ultimately, profitability. Even the smallest changes in how you store your products can affect your overall costs.
This is where warehouse totes, tote dividers and bins come in.
Warehouse totes, bins and tote dividers are the most common and straightforward methods for storing small—to medium-sized inventory.
But how exactly do these understated storage containers streamline warehouse operations? We’re here to explain.
In this article, we’ll share everything you need to know about totes, bins and dividers, including their benefits.
Plus, we’ll explain how you can use totes, bins and dividers in automated picking and storage solutions to streamline your warehouse operations.
What Is a Tote?
A tote is a container that stores warehouse materials and goods. These containers have wide openings, making it easy to access and organize products quickly and efficiently.
When your warehouse operator uses piece picking or case picking, totes are an effective solution for transporting and sorting items throughout the picking process.
Warehouse totes also help optimize material handling, which involves moving items from one place to another.
Totes can include plastic bulk bins, plastic agricultural cases and plastic liquid intermediate bulk containers.
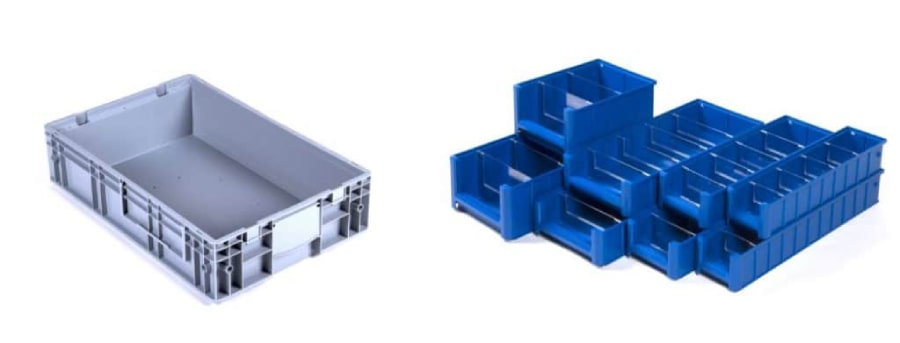
What Is the Difference Between a Tote and a Warehouse Bin?
A tote is an industrial sealable box that’s easily storable by folding it when it’s not in use. A warehouse bin, on the other hand, is a container with an open top.
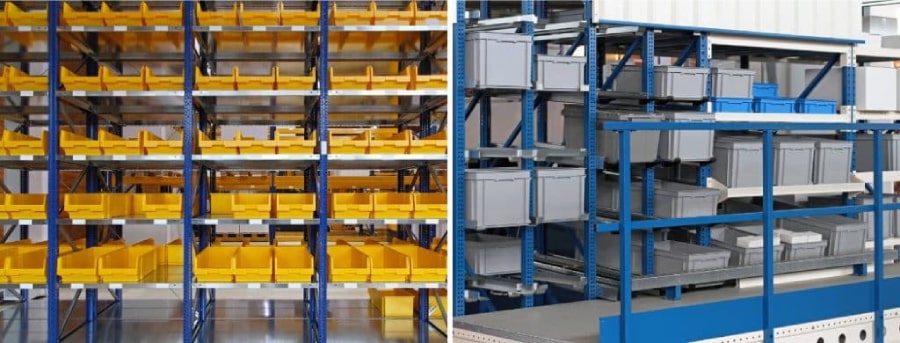
What Are Totes and Bins Made Of?
Typically, totes and bins are made of durable plastic or metal materials built to withstand oil spills and water. The most common materials are:
- Polyethylene plastic: The most popular thermoplastic material used to create plastic containers, bags, and bottles.
- Acrylonitrile butadiene styrene (ABS) plastic: A type of plastic that is lightweight and impact-resistant.
- Acrylic plastic: Also known as plexiglass, acrylic plastic resembles glass Polypropylene (PP) plastic — a type of plastic used in various industries, from automotive to textiles.
- Polyvinyl chloride (PVC) plastic: A type of durable thermoplastic material commonly used in pipes, medical devices, wires, and cable insulations.
- Aluminum: A type of lightweight material that doesn’t corrode and is suitable for a wide variety of environments.
- Steel and stainless steel: A highly durable, non-corrosive material that is both heat-durable and easily reclaimable.
What Are Tote Dividers?
Tote dividers are plastic pieces within a tote that create compartments for both item segregation and bundled storage.
Warehouse operations in the food and beverage industry commonly use tote dividers to indicate which items should be picked first, to ensure first-in first-out (FIFO) stock rotation.
The FIFO stock rotation method ensures that you place items in order of their use-by dates.
Benefits of Totes, Bins and Dividers for Material Handling
From organizing small items and kitted parts to providing better protection from contaminants, here are six key benefits of totes, bins and dividers for warehouse material handling.
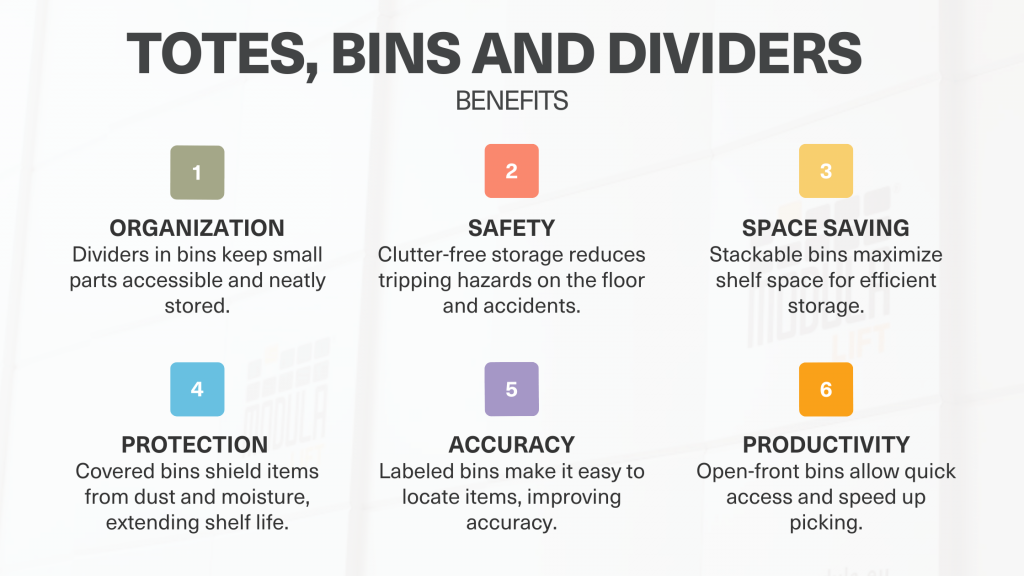
Better Organization
Bins and Totes with dividers come in various dimensions, shapes and materials, making them suitable for many applications.
Totes and bins are particularly efficient for storing small parts — warehouse items that are more likely to be misplaced and overlooked due to their size. Small parts include items like screws, bolts, minerals, bottle caps and medicine.
However, there is a wide selection of heavy-duty totes and bins in the market. Lighter than wooden or metal crates, they represent a great solution to store, handle and move heavier bulk products.
Reduced Workplace Accidents
A warehouse operator’s routine often includes moving around the facility, whether it’s receiving inventory or picking items ready to be shipped, which can lead to trips and falls if goods aren’t properly stored.
In fact, a study by the United States Bureau of Labor Statistics found 4.8 recorded injuries for every 100 full-time workers in the warehousing industry in 2019 alone.
Additional studies by the Princeton University Neuroscience Institute and National Institute of Mental Health found that clutter can affect a person’s ability to concentrate and respond, respectively.
So how do totes with dividers play a key role in preventing accidents? Totes and bins with dividers allow you to store goods in an efficient way, so you can keep your warehouse floor space clutter-free, eliminating tripping hazards
Maximized Storage
A recent report published by the Supply Chain Quarterly found that the U.S. will need to add 330 million square feet of warehouse space by 2025.
By using bins, dividers and totes, you can create additional levels of storage within a shelf or rack, to store more items within a space.
In addition, most bins and totes are stackable or collapsible, allowing you to further save warehouse space.
Maximized Storage
Inventory stored in open shelving can end up being exposed to dust, humidity, dirt and forklift fumes that contain carbon monoxide.
This exposure can shorten the shelf life of many products.
To provide better protection for your inventory, utilize totes with dividers that come with covers or lids.
Boosted Picking Accuracy
Bins and Totes with dividers enhance picking accuracy in your warehouse thanks to bar codes and alphanumeric codes that can be attached to the tote’s exterior.
Implementing a color-coded system in your warehouse allows your employees to identify products, locations and pallets associated with specific colors faster.
In addition, stock keeping units (SKUs) that are typically picked together can be stored next to each other for higher throughput.
Increased Productivity
Totes with dividers and bins with partially open fronts, also known as hopper-front containers, offer warehouse employees a clear view of the contents inside.
Even if they are stacked on top of each other, operators can still pick the item needed without opening the container or moving it from its location on the shelf.
This feature allows faster picking time and increased productivity.
How To Use Totes, Bins and Dividers in Automated Storage and retrieval solutions
At Modula, we offer automated picking and handling solutions that provide an efficient way to transport your warehouse totes and bins.
Here’s how you can utilize totes, bins and dividers within our automated solutions, to increase picking efficiency and accuracy and streamline your material handling.
Improve Manual Picking
Do you need help streamlining your manual picking process?
Our picking solutions transport your warehouse totes to picking locations automatically, eliminating the need for warehouse operators to manually move them from one area to another.
How it works: First, your warehouse operator picks an item from your vertical lift module (VLM) then places it directly into a warehouse tote carried by an autonomous mobile robot (AMR). The mobile robot then moves the warehouse tote to the consolidation area or the next picking zone.
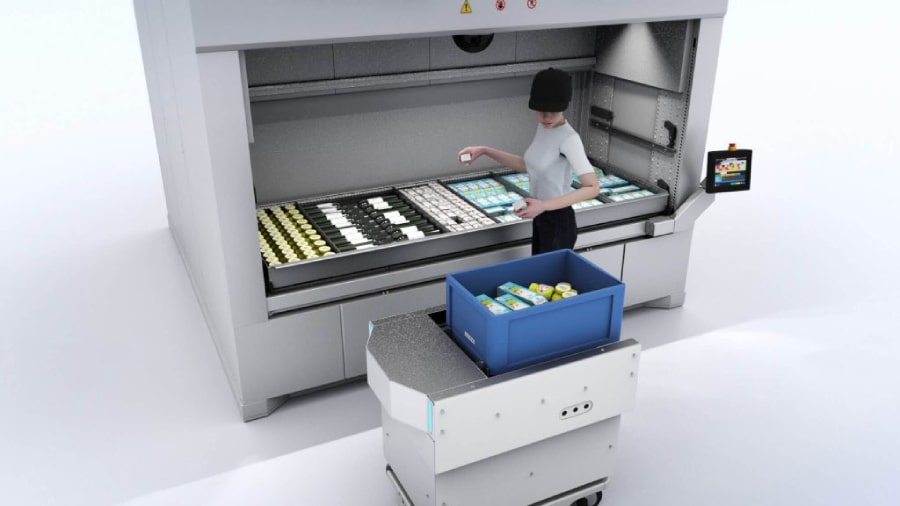
Have questions about AMRs? Check our guide on how autonomous mobile robots work!
Utilize Picking Carts
Do you need to pick multiple totes to fulfill batch orders? Our picking solutions, such as our put-to-light systems and picking cart, have you covered.
How it works: Modula’s picking cart is attached to an AMR, allowing multiple totes with dividers to be safely and quickly delivered to their next location.
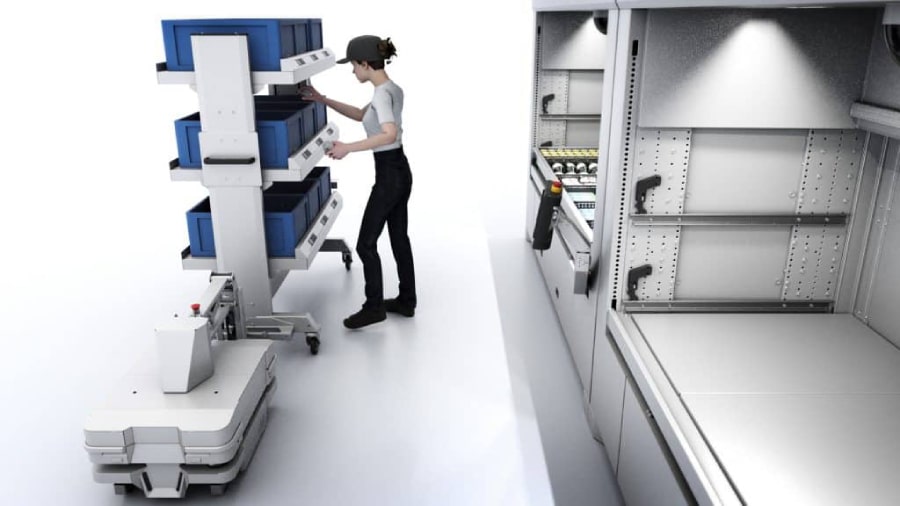
Fully Automate Single Tote Picking
If you want a fully automated solution to carry out your picking process from start to finish, look no further than our automated picking and handling solutions with Modula and MiR.
How it works: The AMR is equipped with a robotic arm and scans the QR Code in front of the picking bay to get the correct item. The robotic arm then picks the item directly from the VLM’s tray and puts it away into a warehouse tote on top of the robot.
Once the items are picked, the robot moves to the next destination to deliver the totes with dividers.
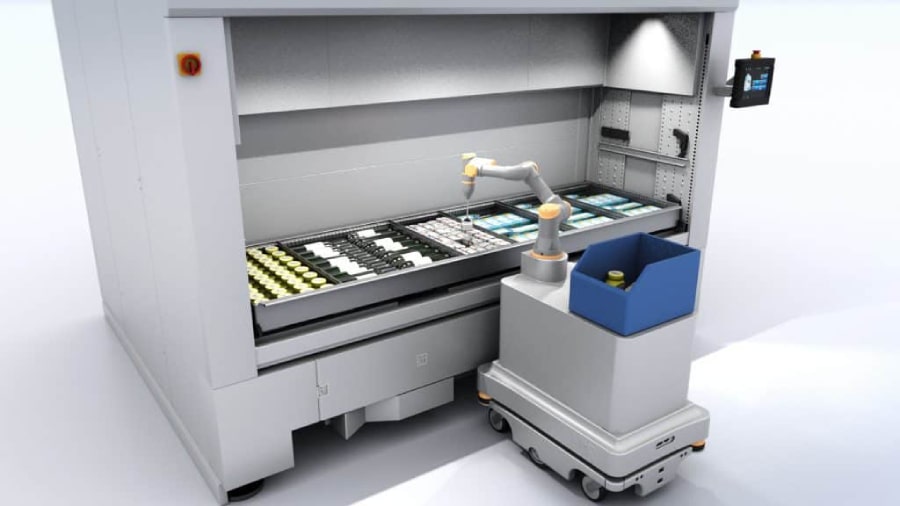
Fully Automate Multiple Tote Picking
Need help transporting your warehouse totes within your warehouse, but lacking enough manpower to do so? Our automated picking and handling solutions can help.
How it works: The robot heads to your VLM, scans the QR Code in front of the picking bay, picks the warehouse tote, then places it on the top module — a storage feature that lifts, picks, and puts away totes with dividers.
Once the robot picks the warehouse tote, it’s ready to transport it to the next picking location.
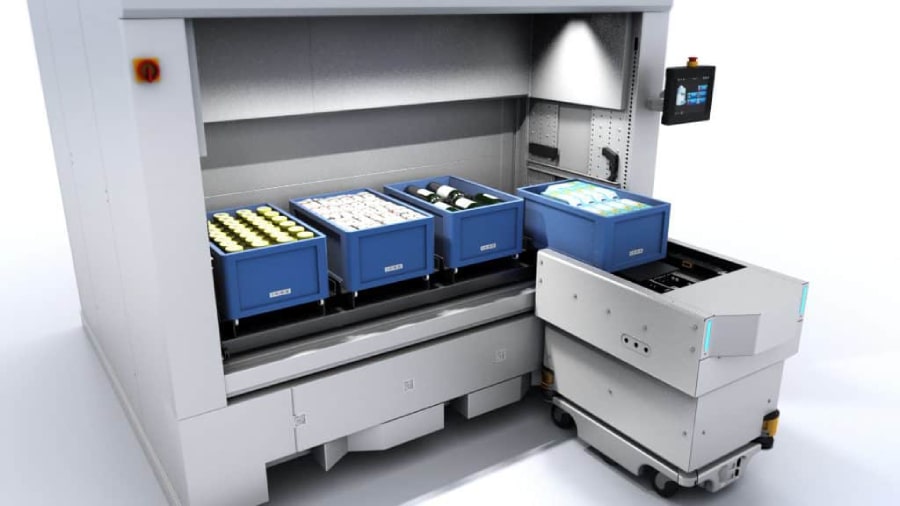
Check out our automated storage solutions and autonomous mobile robots in action below:
Modula Warehouse Picking Order Solutions
Need help transporting your totes with dividers with ease and accuracy?
Whether it’s reducing employee strain or utilizing fully automated solutions to boost your picking efficiency and accuracy, our order picking solutions will enhance the material handling process in your warehouse.
Our Modula Warehouse Order Picking Solutions include:
- Modula Picking Cart for moving inventory to and from different areas within your warehouse
- Mobile Picking Station for processing large volume orders in a shorter amount of time
- Modula Put to Light for guiding your employees to the accurate picking location or station
- Modula Mobile Picking App for managing your picking operations on the go, with a touch of your tablet or smartphone
Integrating Totes, Bins and Dividers With Modula Automated Storage Solutions
At Modula, our smart and innovative automated storage solutions can be easily configured to work with your totes and bins.
Modula Vertical Lift Modules with Totes, Bins and Dividers
From the chemical and pharmaceutical industry to the electronic and mechanical sectors, companies from different industries rely on vertical lift modules (VLMs) for storing and handling various product types.
Modula’s vertical storage solutions work as a vending machine in which inventory items are securely stored and retrieved.
Vertical storage solutions eliminate the need for your warehouse operator to walk between aisles to pull items from shelves. As a result, VLMs speed up the order-picking process.
From the smallest to the heaviest parts, everything is presented in the work opening where your operators have access to all materials — no bending or stretching required!
Each tray is a closed shelf that can be organized with partitions and dividers to create the locations needed. In addition, each tray can host warehouse totes and bins, as the size of the trays can be easily configured.
If the tote and bin sizes changes, the vertical lift module has a sensor that measures each newly loaded tray then automatically stores it in the first available storage space.
The VLM carefully stores trays above each other to maximize storage space.
The best part? The VLM can be operated by anyone, thanks to its user-friendly features.
Here’s a closer look at our Modula Lift:
Here’s a closer look at our Modula Lift:
Store your warehouse totes and bins in our Modula vertical lift modules:
- Modula Lift: Our most popular vertical lift module, the Modula Lift takes up a minimal footprint by utilizing your available ceiling height
- Modula Slim: The most compact VLM available on the market, the Modula Slim is ideal for warehouses with limited floor space
Modula Horizontal Carousels
Working Working with limited ceiling height? You can count on our Modula horizontal carousels to safely store your totes bins and dividers.
See our Modula horizontal carousel in action below:
The horizontal carousel consists of carriers (bins) which are mounted on an oval track that rotate horizontally and deliver stored goods to the picker.
Each bin shelf can be divided into totes, bins and partitions to create an efficient and well-organized storage space.
In both production and distribution settings, the horizontal carousel is extremely effective in saving space, reducing labor costs, increasing throughput and improving accuracy and inventory control.
Similar to the vertical lift module, shelf spacing can be easily adjusted to store different goods.
The horizontal carousel delivers the items directly to the operator, reducing handling times in both picking and replenishing tasks (there’s no walking back and forth to find and retrieve goods).
Thanks to visual picking aids, your warehouse operator can quickly identify the quantity requested and the item that should be picked.
Modula Special Applications
For warehouse totes and bins that need a reliable, safe and temperature-controlled environment for storage, look no further than Modula’s controlled environment storage solutions.
Our controlled environment storage systems are built to house products in environments that are dependent on temperature.
In addition, our controlled environment storage systems feature temperature variations that meet industry standards and regulations, and protect goods from contaminants.
Our controlled environment storage solutions are available in two models:
- Modula Climate Control: Our vertical lift module for controlled temperature and humidity
- Modula Clean Room: Our vertical lift module for clean room storage conditions
Check out our controlled environment storage solutions in action below:
Our Modula Climate Control solution allows you to:
- Control the temperature from +2°C to +25°C (+35 °F to +77°F)
- Control the humidity of ≥ 5%
- Get easy access to stored inventory
Our Modula Clean Room solution allows you to:
- Gain access to clean room classifications ranging from 6 to 8
- Comply with ISO 14644-1 standards
- Minimize exposure to contaminants, such as dust, dirt, particles, and germs
- Ensure minimal air particles within your storage room
Modula Next
The Modula Next is one of our latest ground-breaking automated storage and retrieval solutions that combines the space efficiency of VLMs with the precision and control of industrial vending machines.
When someone requests an item, the unit retrieves the specific tray that stores it and delivers the tray to the picking bay at an ergonomic height.
Unlike traditional VLMs, the Modula Next features a shuttering door system that only opens the compartment containing the requested item, ensuring unmatched precision in picking and replenishing.
Wrapping Up on What Is a Tote?
To recap, warehouse totes are plastic containers used to store warehouse goods and products.
On the other hand, bins are containers with an open top, and tote dividers are plastic partitions used within a plastic container to create compartments to improve storage and picking efficiency.
At Modula, we provide easy-to-install, intuitive automated solutions to streamline warehouse storage, improve picking efficiency and take your material handling to the next level.