Kitting Process 101: Process, Benefits, and How to Automate It
Kitting in a Warehouse Explained: Key Takeaways
Have you ever purchased a new gadget, and it came neatly packed with all the accessories – charger, cable, manual – in one box? That’s kitting in action.
In a warehouse, kitting is an inventory management strategy that involves grouping related items and shipping them as a single unit. It’s used to improve order accuracy, reduce handling time, and optimize space and labor, making it a valuable process for warehouse operations.
In a warehouse, Kitting is an inventory management technique that can help your company increase revenue, reduce costs and enhance customer satisfaction.
In this guide, we will:
- Cover the common types of kitting
- Walk you through the step-by-step process of kitting
- Introduce automated kitting systems at Modula can help further optimize your warehouse operations
What is Kitting in a Warehouse?
Warehouse kitting (also known as inventory kitting or product kitting) is the process of combining multiple individual but related SKUs into one assembled kit that is stored, picked, and shipped together.
Common examples include:
- A hardware kit for assembling furniture
- A laptop bundled with a charger and accessories
- A surgical kit with all required medical instruments
- This process simplifies fulfillment by allowing pickers to handle fewer SKUs per order, resulting in faster operations and fewer errors.
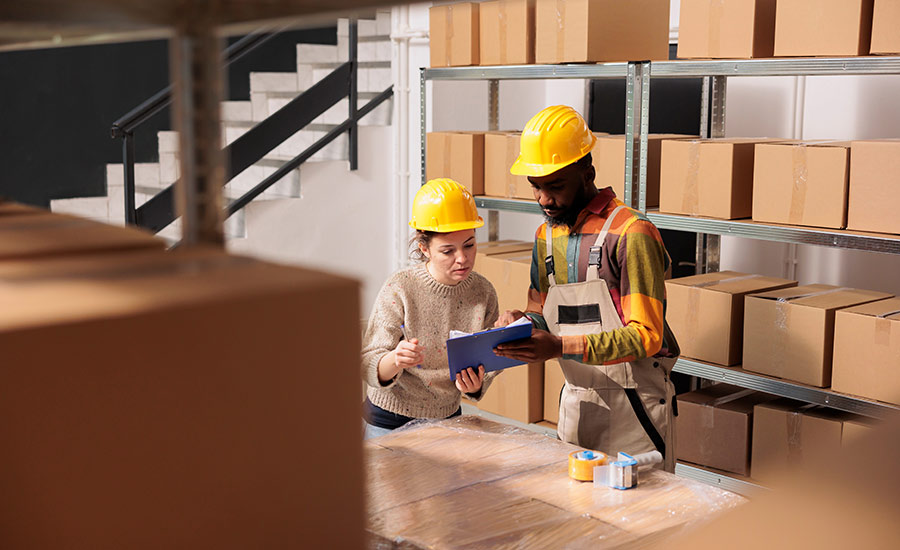
Kitting vs. Bundling: What’s the Difference?
While the terms kitting and bundling are often used interchangeably, there’s a stark difference between the two.
- Kitted items are individual yet complementary goods that are packed into a single kit and are sold as one unit.
- Bundling, on the other hand, is a sales strategy that combines multiple products sold together at a discounted price, encouraging customers to buy additional items they might not have purchased individually.
Kitting vs. Assembly
Kitting and assembly are related processes but serve different functions within a warehouse.
- Kitting: Kitting involves gathering individual, complementary items and bundling them into a single package, often to simplify order fulfillment or prepare for further assembly.
- Assembly: Assembly, on the other hand, refers to the process of taking different components and putting them together to create a finished product. Unlike kitting, which is about preparing sets of parts, assembly is the physical construction of the product.
Common Types of Kitting
There are several types of kitting commonly used in warehouse and manufacturing environments:
- Order Kitting: Items needed for a specific customer order are gathered and bundled together to fulfill the order efficiently. For example, assembling a kit containing a laptop, mouse, keyboard, and charger for a customer who ordered a computer bundle.
- Assembly Kitting: Bundling components required for a specific assembly or manufacturing process. This helps streamline production by ensuring that all necessary parts are available. An example is creating kits containing screws, nuts, and washers for assembling furniture.
- Promotional Kitting: Creating kits for marketing or promotional purposes. Items are bundled into promotional packages, such as including samples or discount coupons. For example, a kit containing a free sample of a new product along with a promotional coupon.
- Replenishment Kitting: Creating kits used to restock specific inventory locations, such as assembling cleaning supplies to restock janitorial closets in different areas of a warehouse.
- Subscription Box Kitting: Assembling kits for regular subscription services. Items are packaged based on customer preferences for monthly subscription boxes, such as beauty products or snacks.
The Warehouse Kitting Process: Step by Step
So how does kitting in a warehouse work exactly?
Determine Which SKUs You’ll Include in the Kit
First, identify your goals to determine which individual items your warehouse employee will include in the kit.
Use data analysis to identify products that are frequently bought together to ensure that your kitting decisions are effective.
Ask yourself the following questions:
- Do you want to improve sales revenue or meet seasonal demands? Kit products that are typically purchased together.
- Do you want to increase your customer’s average order value? Kit new products together with fast-moving items.
- Do you want to prevent overstocking? Offload slow-moving items by kitting them with more popular, fast-moving products.
Identify Who Will Assemble the Kit
Your warehouse operators can either pre-assemble the kits or you can outsource the assembly and kitting services to a 3PL provider that will ship and label the final SKU.
Outsourcing to a 3PL can save labor costs and time but may reduce control over quality and speed compared to in-house assembly.
Assign a New SKU
Next, your warehouse operators assign a new SKU number to the kit. This will help monitor sales and inventory.
This helps streamline inventory management by allowing you to track only the kit’s SKU instead of individual product SKUs, simplifying labeling and monitoring processes.
Pick and Assemble the Kit
In this step, your warehouse operators locate the SKUs they’ll need to piece together the kit.
Picking aids, such as warehouse management systems, barcode readers and picking carts, can help them navigate their way around the facility to locate the accurate picking areas.
Once your warehouse operator utilizes piece picking or case picking, they can now pre-assemble the kits, which will then be ready for storage.
If you have an automated warehouse, your operators can use automated storage and retrieval systems (ASRS) to help store and batch-pick multiple kits into totes or bins.
Ship the Kits to Customers
Once the orders arrive, your warehouse operators can ship kitted items as a single order to your customers. This streamlines the delivery process and reduces shipping costs.
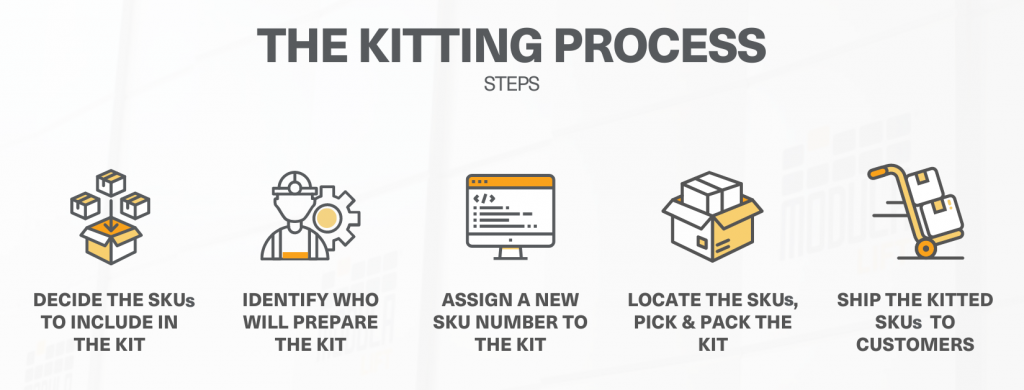
Benefits of Kitting in a Warehouse
From maximizing existing warehouse space to preventing overstock, here are five reasons why kitting in a warehouse is paramount to streamlining warehouse operations.
Saves Warehouse Space
Warehouse space is at a premium. In the United States, it can cost up to $8 per square foot in 2021 alone.
When you consolidate individual products into kits, you can optimize space in warehouse facilities and distribution centers by storing goods together. This saves floor space and eliminates the need to move to a bigger warehouse.
Pro tip: Need more space-saving ideas? Read our guide to organizing your warehouse to maximize your warehouse space!
Reduces Travel Time
Part of a warehouse employee’s day-to-day activities is locating and picking items in the facility.
With pre-assembled kitted goods, operators aren’t required to locate and pick multiple SKUs when an order comes in.
Warehouse operators just pick the kitted products, with the help of picking aids, then head to the shipping area, resulting in a much faster and efficient picking.
Cuts Shipping and Packing Costs
Shipping can be costly, and it’s only set to rise. One solution? Utilizing warehouse kitting to minimize shipping costs.
Warehouse kitting allows you to ship multiple items in one package (compared to frequently shipping individual items), saving you shipping space and reducing materials cost like package fillers and packing tape
Improves Sales Revenue
Whether it’s a travel kit full of essentials or buy one, get half off on a shampoo and conditioner set, kitted items can turn even the most logical consumer into a giddy shopaholic.
In fact, a study by the University of London found that consumers are most likely to purchase a BOGO deal when seeing the word “free,” even when they only need one of the bundled items.
Warehouse kitting allows you to boost sales and increase your customer’s average order value (AOV) — a metric that monitors the average amount spent.
Offload Slow-Moving Inventory
Do you have slow-moving inventory sitting on your warehouse shelves?
Whether it’s miscalculated consumer demand or ineffective marketing, slow-moving goods can result in overstocking (and expired perishable goods!) which can hurt your overall profitability.
With warehouse kitting, retailers can sell slow-moving inventory when bundled with popular, fast-moving items.
(Speaking of inventory, read our blog about warehouse inventory management best practices!)
How To Automate your Warehouse Kitting Process With Modula’s Automated Kitting Equipment
While kitting in a warehouse can help you save valuable space, prevent overstock and more, it requires warehouse operators to manually navigate multiple storage aisles and pick individual goods to form a kitted order.
This manual approach to warehouse kitting is tedious, labor-intensive and can be prone to human mistakes — which is where we come in.
At Modula, our cutting-edge automated solutions transform your material handling and streamline your warehouse kitting, thanks to advanced storage, picking and inventory management systems.
An efficient fulfillment process increases company profit and customer satisfaction.
Let’s dive right into our solutions.
Modula Vertical Lift Modules
Say goodbye to low-density static shelving that wastes floor space and requires employees to travel through warehouse aisles.
Enhance warehouse kitting by allowing operators to easily find and receive individual SKUs.
A simple touch of the intuitive Copilot controller or scan of a barcode allows inventory to be delivered to your warehouse operators so they can pack kitted inventory faster.
Available in three models, our automated vertical lift modules are easy to use and built using a space-saving design.
- Modula Lift: Our most popular vertical lift module. The Modula Lift can dramatically reduce your space requirements by up to 90% while boosting picking speeds, efficiency and accuracy.
- Modula Slim: The most compact vertical lift module available on the market. The Modula Slim utilizes the same next-level storage technology as with the Modula Lift, but in a much smaller footprint.
- Modula’s Climate Control & Clean Room: Designed to store materials in environments subject to temperature variations, Modula’s controlled atmosphere storage systems protect products from temperature variations and contaminants
- Modula Next: Vertical lift modules (VLMs) that combine space-saving efficiency with the precision and control of industrial vending machines
- Modula Flexibox: Designed to process up to 180 bins per hour, Modula Flexibox is the smart solution for fast-moving industries needing high-performance picking without compromising on flexibility.
Modula vertical lift modules allow you to reduce labor and operational costs and receive kitted inventory automatically, with the user-friendly Copilot controller.
Modula Horizontal Carousels
If you’re working in a low ceiling environment, our Modula horizontal carousels are the ideal solution when you need efficient and accurate high-speed picking.
Store your kitted items on bins mounted on an oval track that rotate horizontally. Inventory will then be delivered to your warehouse picker automatically.
See the Modula Horizontal Carousel in action:
Modula horizontal carousels allow you to reconfigure shelf spacing for your kitted items to meet seasonal demands. In addition, you can improve your picking accuracy by up to 99% with our visual aids, such as Put to Light Systems and barcode readers.
Modula Warehouse Picking Order Solutions
Pair your AS/RS with our picking solutions to ensure that your kitted items can be accurately located and picked at all times.
Whether it’s reducing warehouse picking errors or meeting seasonal demands, our Modula picking order solutions can boost your picking efficiency and accuracy.
Easy to install and intuitive to operate, our warehouse picking order solutions are ideal for improving your batch and multi-order processing.
See our order picking solutions in action:
Our Modula Warehouse Order Picking Solutions include:
- Modula Picking Cart for moving inventory to and from different areas within your warehouse
- Mobile Picking Station for processing large volume orders in a shorter amount of time
- Modula Put to Light for guiding your employees to the accurate picking location or station
- Modula Mobile Picking App for managing your picking operations no matter where you are, with a touch of your tablet or smartphone
Modula Warehouse Management
Monitor and track your kitted inventory whether on-site or on the go.
At Modula, we provide a wide array of next-level remote support, warehouse management and analytics solutions.
Easy to set up and use, our Modula warehouse management solutions can seamlessly integrate with your existing ERP, MRP, WMS and DMS platforms.
See our warehouse management solutions order picking solutions in action:
We offer two Warehouse Management System solutions:
- Module WMS Base: Ideal for thriving warehouses or scalable warehouse footprints
- Modula WMS Premium: End-to-end warehouse management solutions
Our Advanced Modula WMS solutions offer
- End-to-end inventory monitoring and control
- Unrivalled picking and replenishment accuracy and efficiency
- Unparalleled automation, dramatically reducing labor-intensive paper and manual processes
Wrapping Up on Kitting in a Warehouse
Kitting in warehouse settings is a smart way to reduce waste, optimize picking, and meet customer expectations efficiently.
Whether you’re assembling components for production or bundling items for retail, kitting can streamline your workflow—especially when supported by automated systems.
At Modula, we offer a full suite of automated solutions to make kitting easier, faster, and more accurate.
Ready to rethink your kitting strategy?
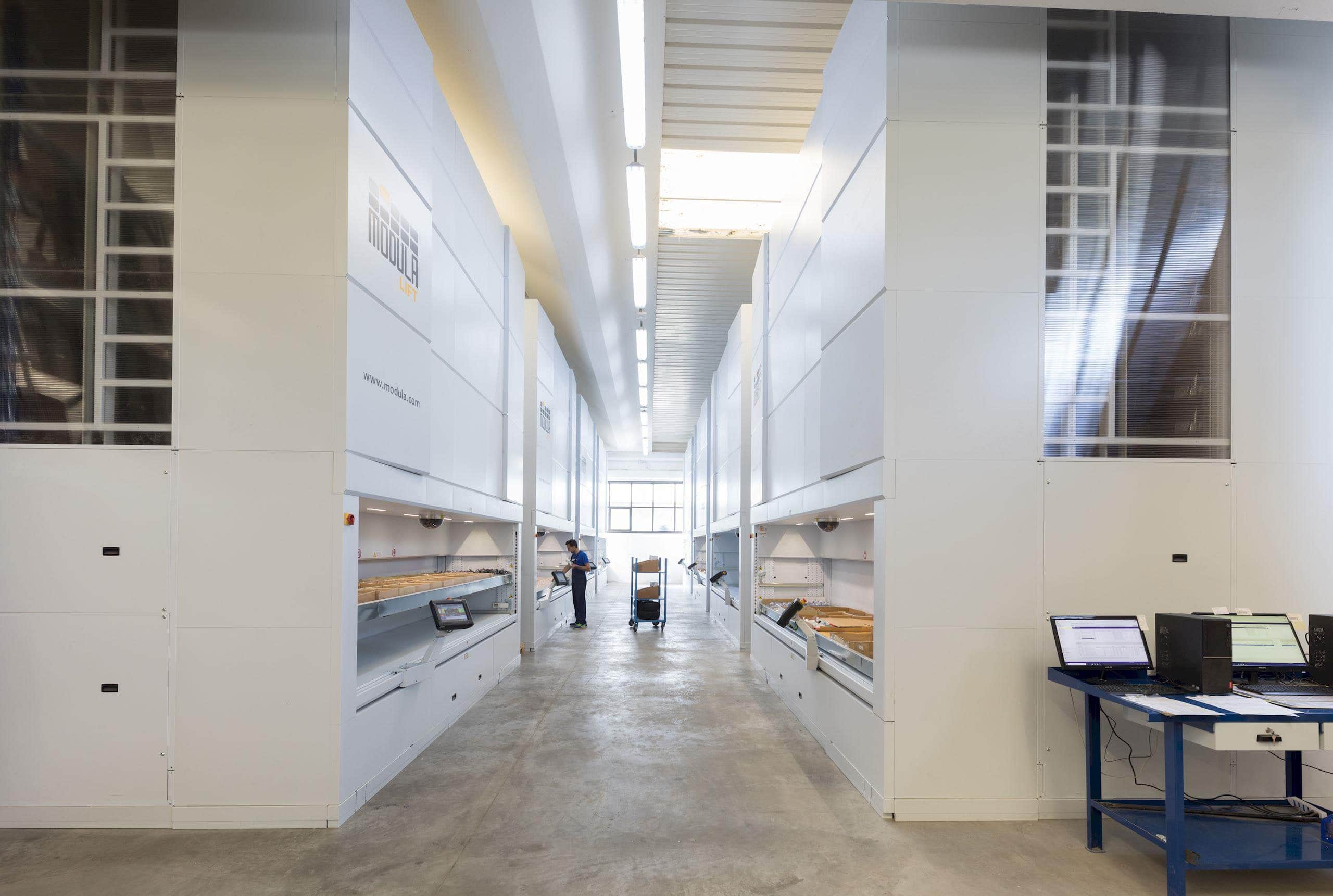
Automate your kitting with Modula
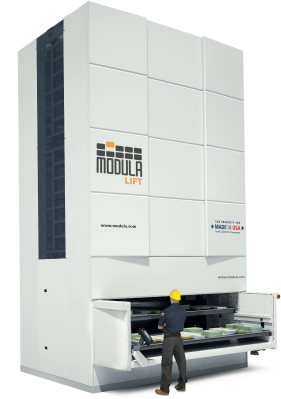