What Is Case Picking? [Methods, Benefits & Best Practices]
If you work in a beverage distribution facility or manage an eCommerce fulfillment center, you’ll likely notice that case picking plays an important role in efficiently handling large volumes of orders.
In this article, we’ll explain what exactly case picking is, along with the types of case picking methods and how Modula can help optimize your picking process.
What Is Case Picking?
Case picking is the process of selecting and handling full cases of products from storage locations in a warehouse or distribution center to fulfill customer orders more efficiently.
It’s the middle ground between piece picking (selecting individual items) and pallet picking (selecting full pallets of products).
In case picking, a warehouse operator utilizes a list to select entire boxes or cartons from inventory shelves, which are then placed onto pallets or carts for shipping.
Case Picking vs. Pallet Picking
Case picking involves selecting individual cases or cartons from shelves, pallet positions or carton flow — a type of shelving that utilizes a gravity-fed, rear-loading design.
This method is ideal for fulfilling orders that require large quantities of a single product but not enough to need a full pallet.
On the other hand, pallet picking is the process of moving entire pre-packed pallets of a single product from a rack or floor storage.
It is efficient for large bulk orders, such as wholesale restocking, as it allows for quick movement using forklifts.
Types of Case Picking Methods
Order picking is a labor-intensive process that accounts for up to 55% of the total operating costs in a warehouse or distribution center.
Warehouse operators can execute this process using different methods, each tailored to specific operational needs and efficiencies.
The four common types of case picking methods include:
Piece Picking
Piece picking, or split case picking, is the process of selecting individual products, one at a time.
Piece picking is ideal for smaller warehouse operations or orders with different items that don’t require large quantities.
In this method, the picker completes one order at a time by visiting each aisle, making it a time-consuming process.
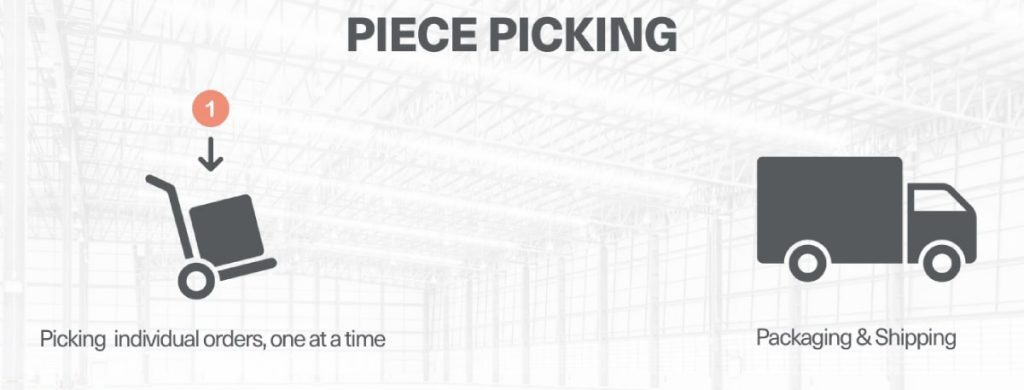
Batch Picking
Batch picking is a strategy that groups orders into “batches” based on similar SKUs and characteristics, such as product types, order size or delivery locations.
With this strategy, pickers handle a batch of similar orders simultaneously, selecting the same SKU for multiple orders at once.
Batch picking can help minimize travel time and improve efficiency. It is ideal for facilities with high-volume operations.
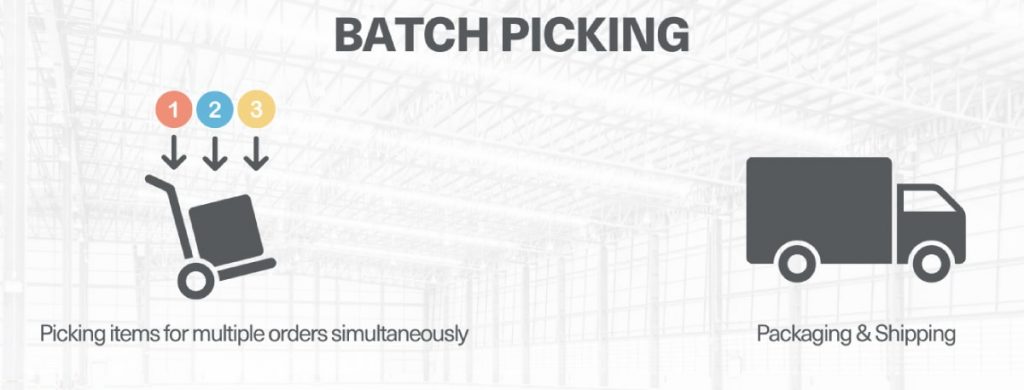
Zone Picking
Zone picking is a strategy in which employees are assigned specific areas of the warehouse to pick items. The warehouse is divided into zones based on factors like item category or picking needs.
This organization optimizes the picking process by organizing inventory and making it easier for pickers to access inventory.
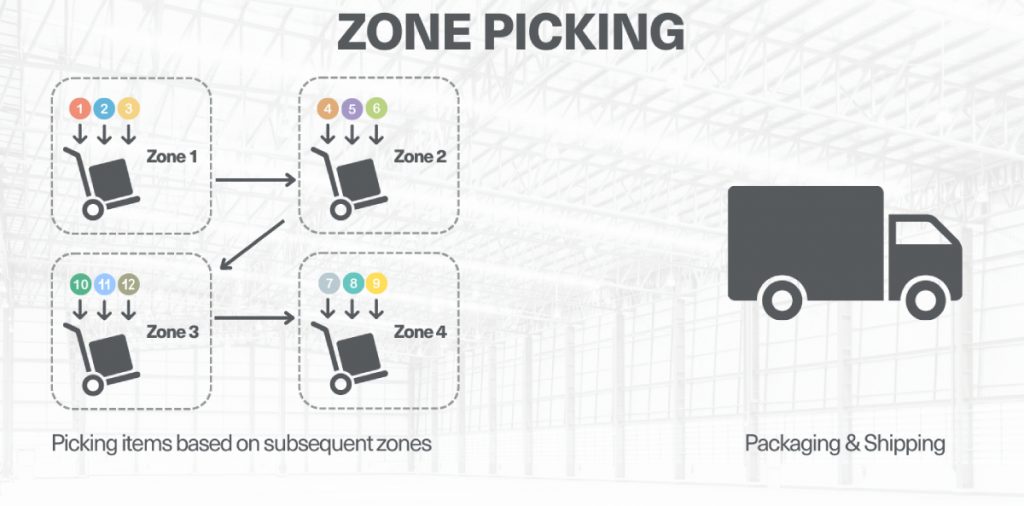
Wave Picking
Wave picking is a strategy in which warehouse operators focus on picking multiple orders within a specific timeframe, grouping them together based on factors like order type, shipping schedules, or product locations.
This method maximizes efficiency by coordinating the picking process to reduce travel time and optimize the use of labor and equipment.
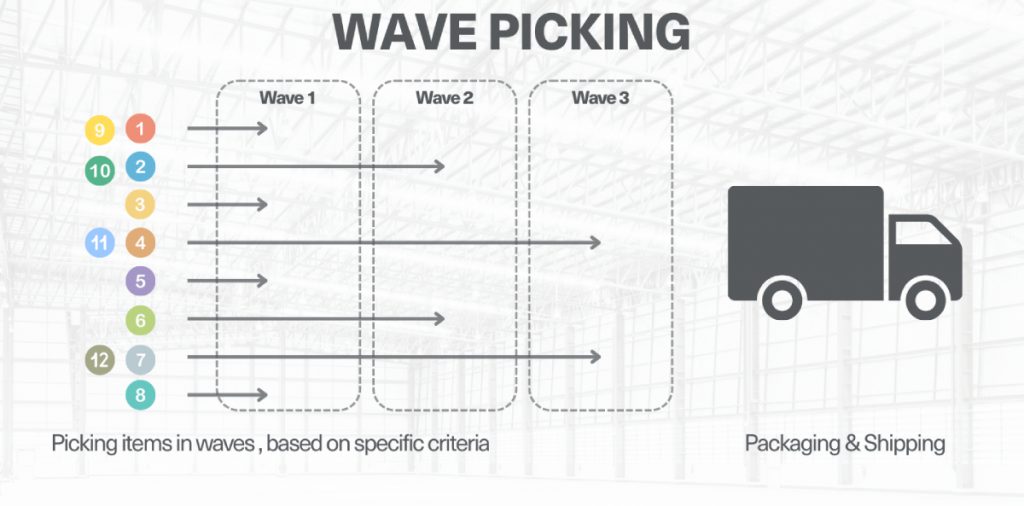
Cluster Picking
Cluster picking is a warehouse picking strategy in which a single picker collects items for multiple orders simultaneously using a multi-compartment cart or trolley.
In this method, the picker travels throughout the warehouse once, picking items for several orders and placing them into different compartments or bins on their cart.
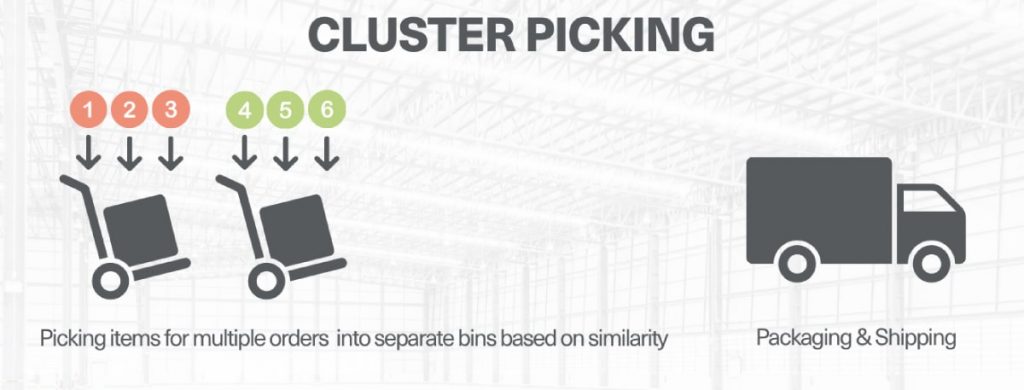
Key Benefits of Case Picking
Case picking allows you to:
- Boost warehouse picking productivity: Case picking optimizes the picking process by allowing warehouse employees to manage multiple items in a single motion. This method significantly speeds up the order fulfillment process, as pickers move less frequently between individual items.
- Reduce storage space per item: When you store and pick cases rather than individual SKUs, warehouses can better utilize vertical and horizontal space. This compact storage method reduces the footprint needed for inventory, allowing for more items to be stored in the same amount of space and improving the organization and accessibility of goods.
- Reduce overall cost per unit: Case picking lowers labor costs by reducing the time spent on each pick. In addition, condensed storage fosters sustainability by decreasing warehousing expenses such as lighting, heating and cooling. These efficiencies lead to substantial savings per unit, making operations more cost-effective and enhancing profitability.
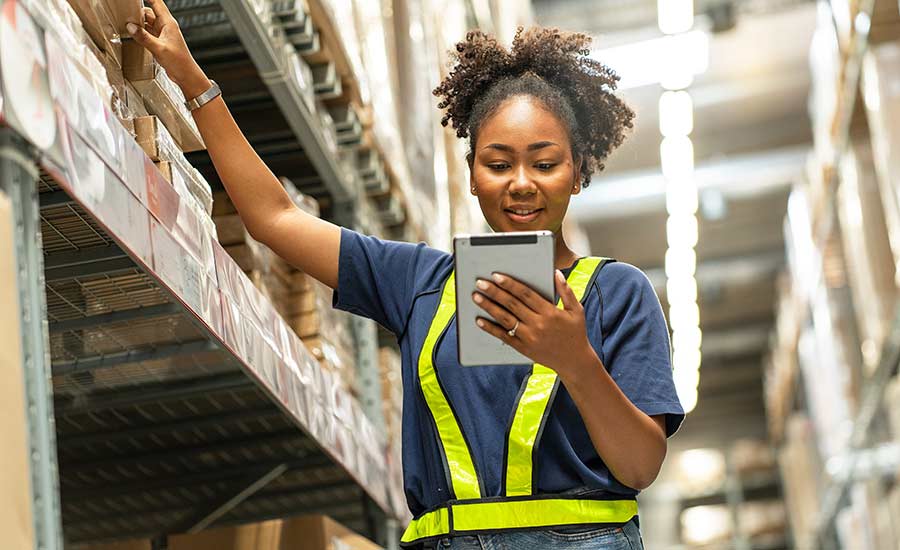
How to Maximize Your Case Picking Operations
Now that you understand the benefits of case picking, we’ll walk you through how you can incorporate this picking strategy into your warehouse operations.
Set Up a Receiving Process
Establish a receiving and inspection process that enhances visibility of shipments, contents and schedules and improves communication with dock staff about shift activities and expectations.
Set specific delivery times with shippers, aim for quick unloading, and promptly inspect, sort, classify and stage goods for replenishment or storage to make sure items quickly reach their destinations.
This approach keeps order picking seamless, prevents bottlenecks and boosts overall efficiency.
Consider Ergonomics
Design picking stations and workflows with ergonomics in mind to reduce physical strain on workers and other warehousing hazards, such as slips, trips and falls.
To ensure ergonomics in your warehouse operations:
- Make sure to store inventory at appropriate heights, usually at waist to shoulder level, to minimize the need for bending or stretching
- Use ergonomic tools and equipment, such as scissor lift tables, lift tables and pallet stackers
- Implement practices that minimize repetitive movements to enhance worker comfort and productivity
Choose Your Storage Method by Item
Choose the most efficient storage method based on the characteristics of each item, such as size, weight and demand frequency.
Utilize methods like fixed location storage for high-demand items and dynamic or random location storage for lower-demand items to maximize space and improve picking efficiency.
Optimize Packaging and Labeling
Ensure that cases are properly labeled and packaged to facilitate faster picking and reduce errors.
Clear, consistent labeling helps pickers quickly identify the correct cases, while efficient packaging reduces the need for repacking or adjusting cases during the picking process.
This speeds up operations and enhances order accuracy and customer satisfaction.
Have a Consolidation Area
Warehouse operations using zone picking, where pickers simultaneously gather items for multiple orders, need a dedicated area to sort and consolidate these picks into individual orders.
Equipping your consolidation area with both static and automated equipment can improve space utilization and boost productivity.
Incorporate Scan Verification
Utilize automatic identification and data collection (AIDC) technologies, like handheld or fixed-location RF scanners and camera-based imagers, to instantly validate items by scanning barcodes.
Scanning verification dramatically increases accuracy compared to manually entering product codes or visually checking SKU numbers.
These devices can read codes on pick lists, single units, cases, pallets, totes and storage positions, ensuring that workers pick the correct item for the order. This approach reduces human picking errors and speeds up the process, potentially eliminating the need for later quality checks.
Minimize Walking Time
Optimize your warehouse layout to reduce the walking distance for pickers.
For example, place high-demand items closer to packing stations and implement zone picking to minimize the travel time needed.
Warehouse operators can also utilize picking technology, such as voice picking systems, to help guide them to the most efficient routes.
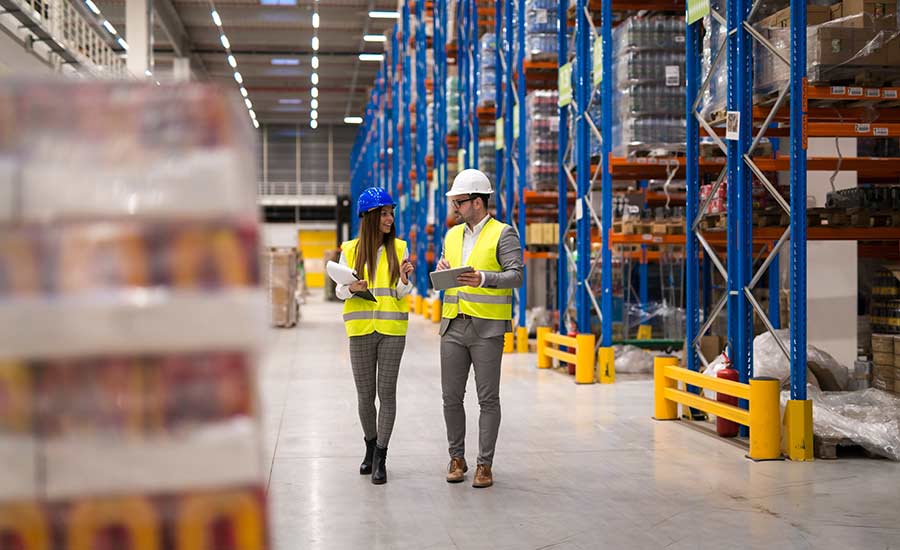
Prioritize Timely Replenishment
Maintain consistent stock levels to prevent picking delays. Implement an automated replenishment system that alerts you when inventory is low.
For example, use sensors in picking bins to automatically reorder stock when quantities fall below a set level, ensuring that popular items are always available.
Establish Warehouse Key Performance Indicators (KPIs)
Measure and analyze specific metrics to drive improvements. Track metrics, such as the rate of returns (due to picking errors) and average pick time.
Regularly review these KPIs in team meetings to discuss performance and set actionable targets, such as reducing average pick time by 10% over the next quarter.
Leverage a Warehouse Management System (WMS)
Use a warehouse management system (WMS) to optimize picking routes and reduce errors. A WMS analyzes orders and determines the most efficient path based on the locations of items.
In addition, a WMS accounts for real-time inventory levels, ensuring that pickers are directed to bins that are adequately stocked, which in turn minimizes backtracking and delays.
Collaborate with a 3PL (Third-Party Logistics) Provider
A 3PL (Third-Party Logistics) provider can offer advanced warehouse management solutions, provide additional resources during peak seasons and implement best practices that improve efficiency, especially if you’re scaling your operations.
For example, a 3PL can integrate their own automated warehouse picking solutions or offer insights into layout optimization that reduces travel time and accelerates the picking process.
Consider Using Warehouse Technology
Implement automated storage and retrieval systems (ASRS) to enhance the efficiency of your picking operations.
These systems automate the storage and retrieval of items, significantly reducing manual labor and minimizing picking errors.
In addition, AS/RS can optimize space usage and improve inventory management by automatically adjusting storage locations based on frequency of use and other factors.
At Modula, we offer the following automated case picking solutions to help you further generate order efficiency, accuracy and reliability:
- Put to Light System: Speed up the picking process and improve the picking accuracy for large batch orders. Modula’s Put to Light System features an OLED configurative display and directs operators using a scanner and LED lights, showing exactly where to place items.
- Modula Picking Station: Leveraging the Put to Light system, this station facilitates batch picking and order consolidation. It enhances accuracy through options for scanning or touch light validation.
- Modula Picking Cart: This mobile cart is equipped with shelves, wheels, and Put to Light controllers, along with battery backup and Wi-Fi connectivity. It features five configurable displays and supports both scan and touch validation, significantly boosting speed and precision in picking operations.
- Modula Picking App: Designed to optimize picking and replenishment, this mobile app allows operators to manage tasks on-the-go and monitor processes in real-time, ensuring continuous operations.
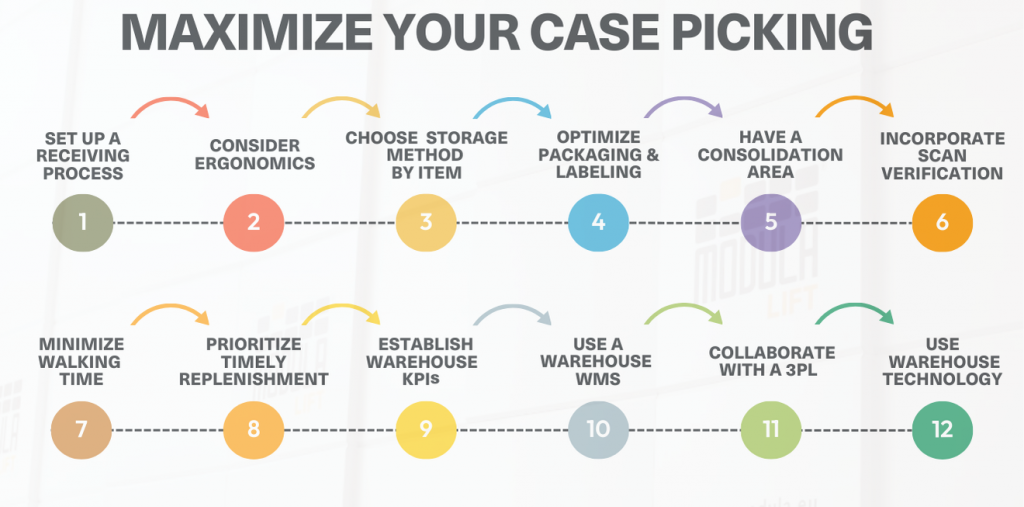
Manual vs. Automated Case Picking
When comparing manual versus automated case picking, each method offers distinct advantages depending on your warehouse needs:
Manual Case Picking
- Flexibility: Manual picking can adapt quickly to changes in inventory or order types without the need for reprogramming or system adjustments.
- Lower Initial Costs: Manual case picking requires less upfront investment compared to installing automated systems.
- Potential Oversight: Manual picking allows for human judgment in handling delicate or irregularly shaped items, potentially reducing damage during the picking process.
Automated Case Picking
- Boost Efficiency: Automated systems can operate continuously, eliminating breaks and fatigue, which significantly boosts productivity.
- Consistency and Accuracy: Automation reduces the risk of human error, ensuring that orders are accurately picked, and inventory levels are accurately maintained.
- Reduced Labor Costs: Over time, the use of automated picking can significantly reduce the need for manual labor, decreasing overall labor costs.
Implementing automated solutions into your warehouse can be highly beneficial, particularly for high-volume environments.
However, manual picking might still be suitable for smaller operations or those with highly variable order types.
Wrapping Up on How Modula Solutions Can Improve Case Picking Efficiency
At Modula, we can automate your picking process to significantly reduce or even eliminate mispicks, while enhancing speed and accuracy.
Our range of solutions, from Put to Light systems to automated storage and retrieval systems, boosts efficiency across your warehouse operations.
Contact our team to explore how our picking solutions can fulfill your operational needs.