25 Warehouse Best Practices To Improve Warehouse Operations
Warehousing Best Practices for Productivity
Batch picking or multi-order picking is a method that allows your operators to pick multiple batches or orders at the same time.
This picking method can help reduce the number of trips your warehouse employee has to make. Instead of retrieving items for a single order, your employee can gather items for multiple orders in a single pass.
To implement batch picking:
- Create a picking list or a document that lists the items that need to be retrieved, along with the location and quantity
- Integrate a warehouse management system to further streamline the process by grouping similar items together
Utilize Wave Picking
Wave picking or cluster picking is a picking method in which your employees simultaneously pick orders based on shipping deadlines, eliminating unnecessary warehouse travel.
Unlike batch picking in which the employee picks orders based on same items and quantity, wave picking focuses on shipping dates — making it the ideal picking method for orders with tight shipping deadlines.
With this picking method, your employee receives a picking list, which includes priority orders that need to be picked and sent over to packing. The employee then picks the goods, which includes 4-12 orders per wave.
To implement wave picking:
- Assign a warehouse picker for each order
- Group orders based on priority shipping, carrier or like products
- Create a pick list that includes 4-12 orders per warehouse picker
Offer Employee Incentives
Provide your employees with incentives, such as bonuses, health benefits and additional vacation days to enhance morale, and support ongoing learning, which can in turn increase productivity.
For example, you can implement points-based recognition programs in which employees earn points for achieving specific milestones, demonstrating exceptional performance or taking part in professional development activities.
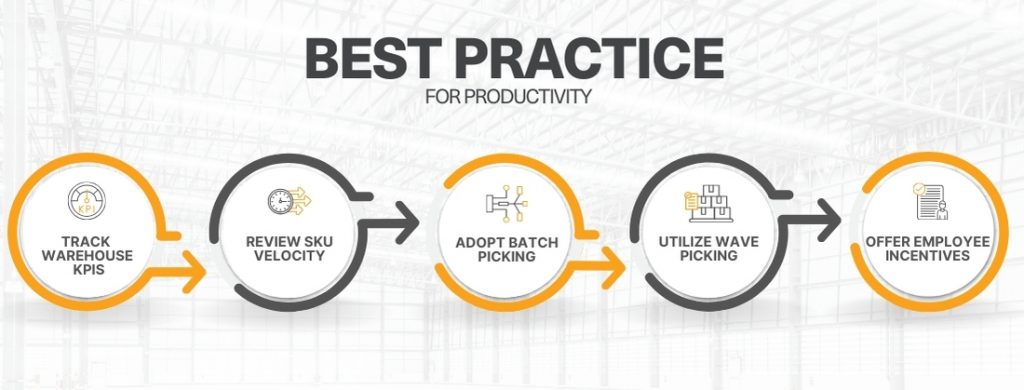
Warehousing Best Practices for Inventory Management
Efficient inventory management is key for your warehouse operations, as it ensures that the right products are available at the right time, facilitating order fulfillment and optimizing warehouse space utilization.
Warehouse best practices to better manage your inventory include:
Utilize Warehouse Kitting
Warehouse kitting is the process of packing individual yet related SKUs into a single package for distribution and sale.
It can help optimize inventory tracking, reduce the number of individual items that need to be monitored and maximize space utilization in your facility.
For example, if your business sells a line of skincare products, a cleanser, toner and moisturizer can be grouped into a skincare kit, stored and picked together.
Protect Inventory
Safeguarding your goods from theft can help ensure you have consistent stock levels, a reliable supply chain for uninterrupted business operations and prevent financial losses.
To protect your inventory:
- Conduct regular inventory audits to quickly detect any discrepancies
- Install security cameras at entry and exit points
- Implement access controls, ensuring only authorized personnel can access storage areas
Utilize Barcode and RFID Systems
Utilizing barcode and RFID systems can help provide real time tracking of goods throughout the supply chain, ensuring accurate inventory counts and reducing human error in manual entry.
For example, when an item with a barcode or RFID tag enters or leaves your warehouse, its status is automatically updated in the inventory management system, eliminating the potential risk of miscounts that often arise during manual inventory tracking.
Implement a Standard Returns Management Process
Returns management is the process of handling and overseeing product returns from customers in an organized and efficient manner.
Implementing a standard returns management process can help ensure that returned products are promptly accounted for and inspected, then either restocked, repaired, recycled or disposed of.
This approach minimizes the time goods remain idle, allowing you to maintain accurate stock levels.
To implement a returns management process:
- Assign dedicated personnel to manage and process returns. This ensures that returns are handled promptly and are not overshadowed by other warehouse activities.
- Create a procedure for inspecting returned items. Determine the reason for the return, check the item’s condition and decide whether it should be refurbished or should be disregarded.
Utilize a Warehouse Management System
A warehouse management system (WMS) is an advanced solution that optimizes warehouse tasks, from order processing and space utilization to inventory management and labor management.
A WMS allows you to improve inventory accuracy, optimize storage allocation and ensure timely order fulfillment.
The Modula WMS is a complete inventory management software, ideal for both Modula’s automated storage systems and traditional warehouses (more on this below!).
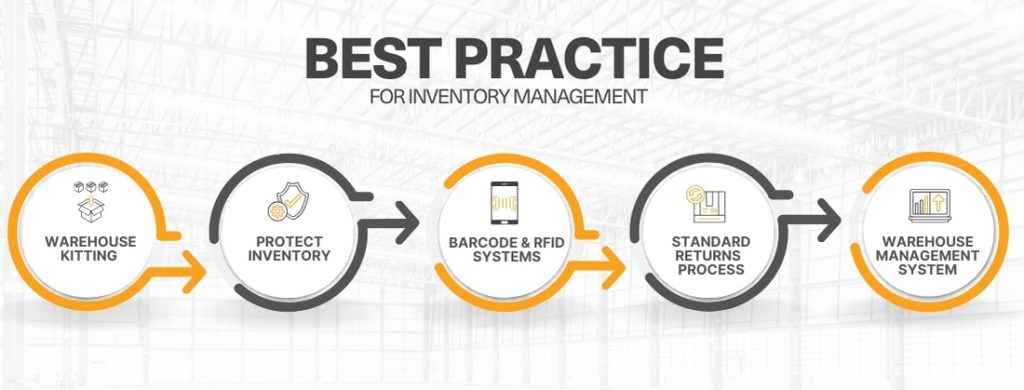
Warehousing Best Practices for Organization
Warehouse organization can help ensure item accessibility, optimize space utilization and boost overall productivity.
Warehouse best practices to improve your warehouse organization include:
Rethink Your Warehouse Layout
A strategic warehouse layout design can help you optimize storage space, ensure that inventory is easily accessible, minimize unnecessary employee movement and accommodate your facility’s future growth or changes in demand.
To ensure a strategic warehouse layout:
- Consider wave picking by arranging goods to reduce the travel time for your warehouse pickers
- Design your layout in a way that allows for changes and adjustments. For example, consider using mobile shelving units that can be moved as needed to optimize space.
- Leave room for potential expansion or new equipment
Keep Warehouse Aisles Clear
Maintaining clear warehouse aisles is crucial for your employees’ safety and operational efficiency.
Keeping your warehouse aisles clear can help you facilitate quicker inventory retrieval, improve equipment and staff movement and minimize workplace accidents.
Utilize Containers, Cabinets and Drawers
Whether it’s storing small parts or grouping items into categorized inventory, storage containers, cabinets and drawers allow your warehouse employees to maintain an organized and clutter-free environment.
To utilize containers, cabinets and drawers in your warehouse, identify the type of container needed and store products based on their size.
Maximize Your Existing Warehouse Space
A recent report found that companies in the United States will need 330 million square feet of additional warehouse space by 2025 to keep up with the uptick in eCommerce demand.
Instead of moving to a bigger warehouse, maximize your available space to help you save money.
To optimize your current warehouse space, use mobile shelving units and consider cross-docking, in which incoming goods are directly transferred to outbound gates, minimizing storage time.
In addition, you can utilize vertical lift modules (VLMs) to take advantage of your existing ceiling height to optimize your space. VLMs are automated vertical storage systems that only use a minimum footprint of your warehouse (more on this below!)
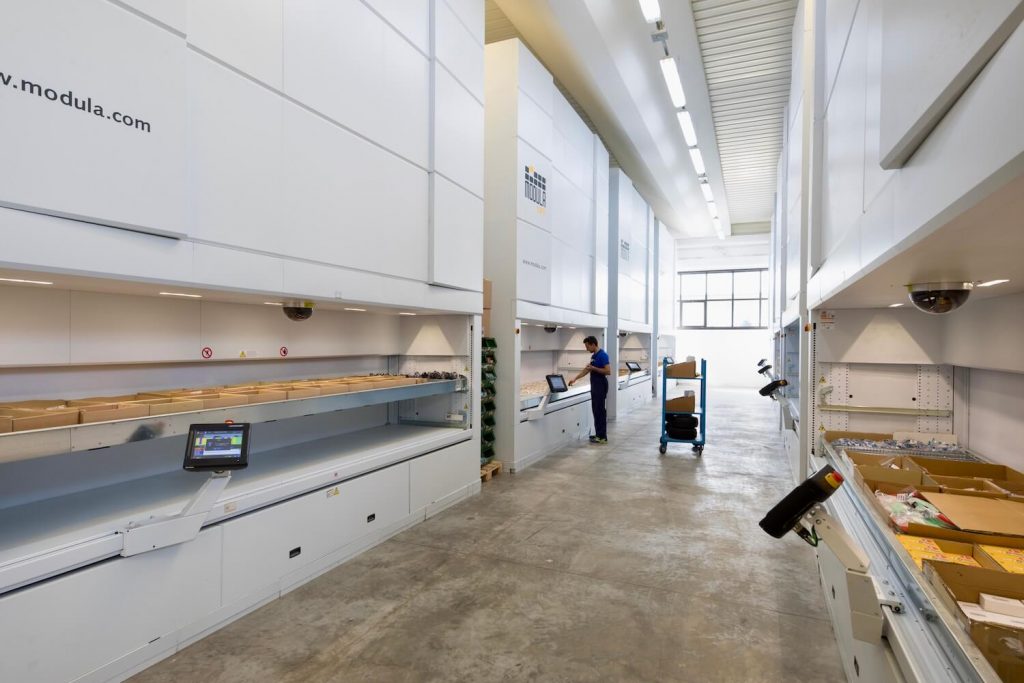
Leverage Warehouse Consolidation
Warehouse consolidation is the process of combining orders in one logistics facility, allowing you to reduce inventory handling and minimize transportation costs.
To implement warehouse consolidation, analyze your current warehouse operations, distribution points and transportation routes.
Identify redundancies and inefficiencies that can be eliminated through consolidation. For example, if you have multiple warehouses serving overlapping regions, you might find that transporting goods between these facilities is causing delays and increasing costs.
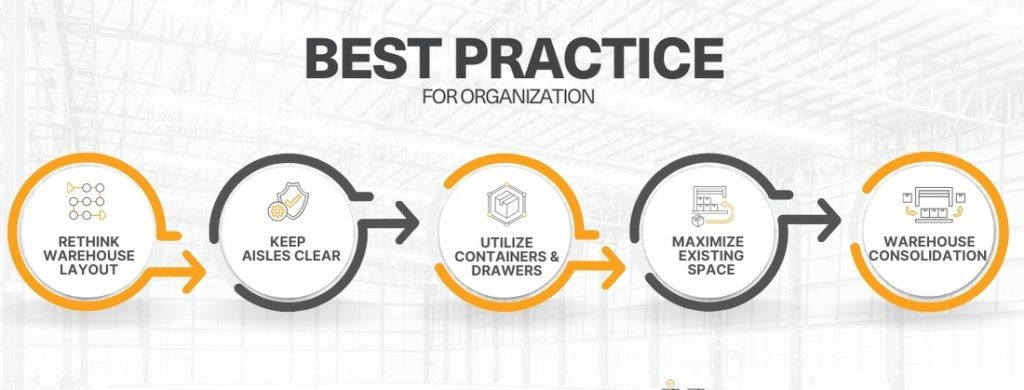
Warehousing Best Practices for Picking Accuracy
Picking accuracy is key for your warehouse operations, as it directly impacts customer satisfaction, reduces returns and minimizes costly errors.
Warehouse best practices to improve your picking accuracy include:
Conduct Regular Warehouse Audits
Conducting regular warehouse audits can help you make sure that inventory locations are properly labelled, verify that SKUs are stored in their designated spots and analyze the frequency of picking errors to address bottlenecks.
By addressing these issues, you can reduce the number of mispicks and ultimately, enhance customer satisfaction.
To conduct regular warehouse audits:
- Examine past picking error reports and logs
- Make sure pick lists and order slips are clear and easy to understand
- Document your findings and analyze the data to identify patterns or areas that consistently result in picking errors
Perform Cycle Counting
Cycle counting is the process of verifying stock levels against your inventory records, often conducted on a monthly or quarterly basis.
By catching discrepancies early, cycle counting maintains accurate stock levels and enhances inventory accuracy.
Establish Picking Routes
Establishing picking routes can help minimize travel time when navigating products and ensure goods are picked in the most efficient sequence, reducing mispicks.
To implement efficient picking routes:
- Identify high-demand items and make sure they are easily accessible
- Consolidate items that are frequently ordered together, so your warehouse pickers don’t have to travel throughout the entire warehouse for commonly paired items
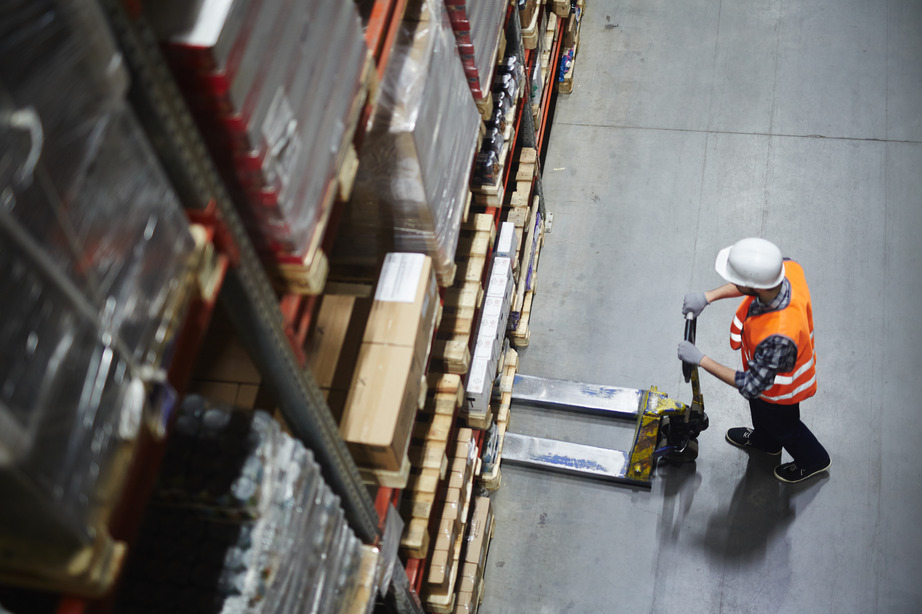
Implement Pick to Light Technology
Pick to light is an automated warehouse picking system that utilizes light displays to guide your warehouse operators to the correct picking locations.
This order picking technology boosts picking speed and improves picking accuracy.
When an order is processed, the relevant storage bin or shelf lights up, displaying the quantity needed for the order. Once your warehouse operator picks the item, they confirm the action — typically by pressing a button — and the light turns off.
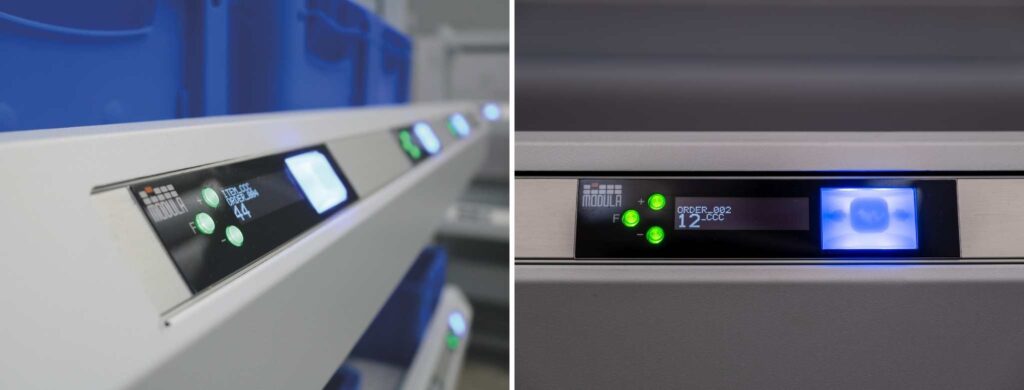
Utilize Voice Picking
Voice picking is a type of assisted picking system that utilizes voice commands to guide your warehouse pickers to the right item, increasing productivity and boosting picking speed.
Instead of relying on paper lists or handheld devices, pickers wear headsets that connect to a voice-directed system. The system verbally communicates the location of the items and how many items should be picked.
As your warehouse pickers move through the facility, they verbally confirm the actions they’ve taken, ensuring real time picking accuracy and hands-free operation.
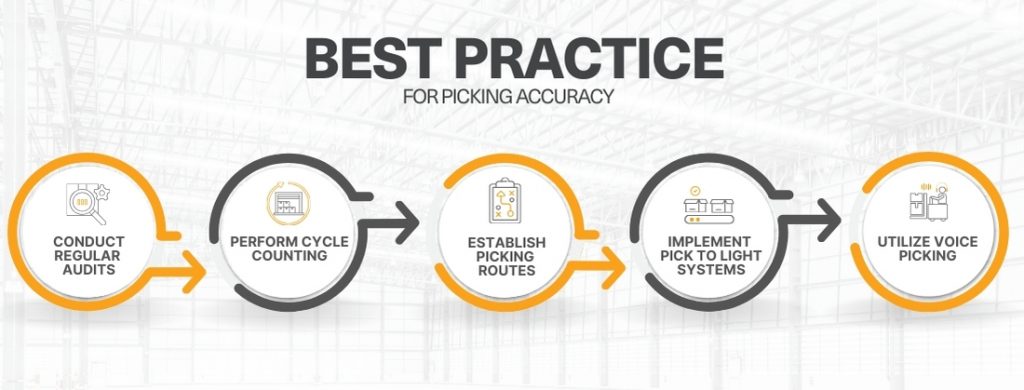
Warehousing Best Practices for Employee Safety
Ensuring a safe workplace is not only important for your employees, but for your brand’s reputation and your bottom line.
Warehouse best practices to improve safety in your warehouse include:
Implement Ergonomic Pick Locations
A warehouse employee’s routine often includes collecting items from hard-to-reach areas and lifting heavy products, which can lead to overexertion injuries.
Implementing ergonomic pick locations can help your warehouse employees reduce strain and minimize potential workplace accidents.
By designing thoughtful pick locations, you can make sure that frequently accessed items are within easy reach.
To create an ergonomic environment in your warehouse:
- Educate your employees on proper lifting techniques
- Store items strategically by placing heavy items below waist level and storing frequently picked items at eye level
- Integrate ergonomic modules and lifts to deliver items to your warehouse operators at a comfortable height
Implement Proper Lighting
Implementing proper lighting can help reduce the risks of accidents and mishaps caused by poor visibility.
Well-lit areas can help prevent trips, falls and collisions by ensuring that your employees can clearly see obstacles and floor markings.
To implement proper lighting:
- Install LED lights for energy efficiency and high bay lighting fixtures for areas with high ceilings
- Consider installing motion sensor lights in areas that are infrequently used
- Install backup emergency lighting systems that activate during power outages to ensure safe evacuation in case of emergencies
Utilize Signs and Labels
Use signs and labels in your warehouse to note safety hazards and make sure employees take proper precautions.
Signs throughout your warehouse can include those for exit doors, machine safety directions, protective gear, and product labels to emphasize harmful chemicals.
To utilize signs and labels throughout your warehouse:
Make sure signs are clear and easy to understand with readable text
Use universally recognized symbols, such as a flame for flammable materials or a pedestrian silhouette for pedestrian pathways, to reinforce the message
Standardize signs through color coordination — for example, use red for safety warnings and yellow for traffic signs
Provide Employee Training
Providing employee training can help equip employees with the knowledge to recognize potential hazards, understand safety standards and become familiar with emergency response procedures.
To provide employee training:
- Implement various training methods, whether classroom sessions, hands-on training or simulation exercises.
- Schedule regular intervals for training to make sure new employees are trained and existing employees are updated about key information.
- Use incident reports or realistic examples to highlight the importance of safety practices. For example, discuss a past incident in which a lack of personal protective equipment (PPE) led to an injury, and illustrate the consequences of not adhering to safety protocols.
Utilize Predictive Maintenance
Predictive maintenance utilizes machine learning and analytics to predict when warehouse equipment will need repairs, allowing you to boost safety, reduce downtime and save on equipment costs.
Without timely maintenance, warehouse equipment poses a risk to employee safety.
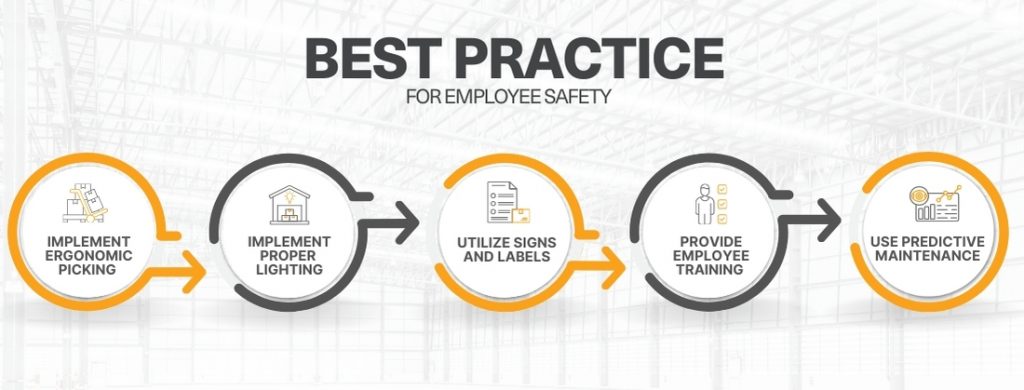
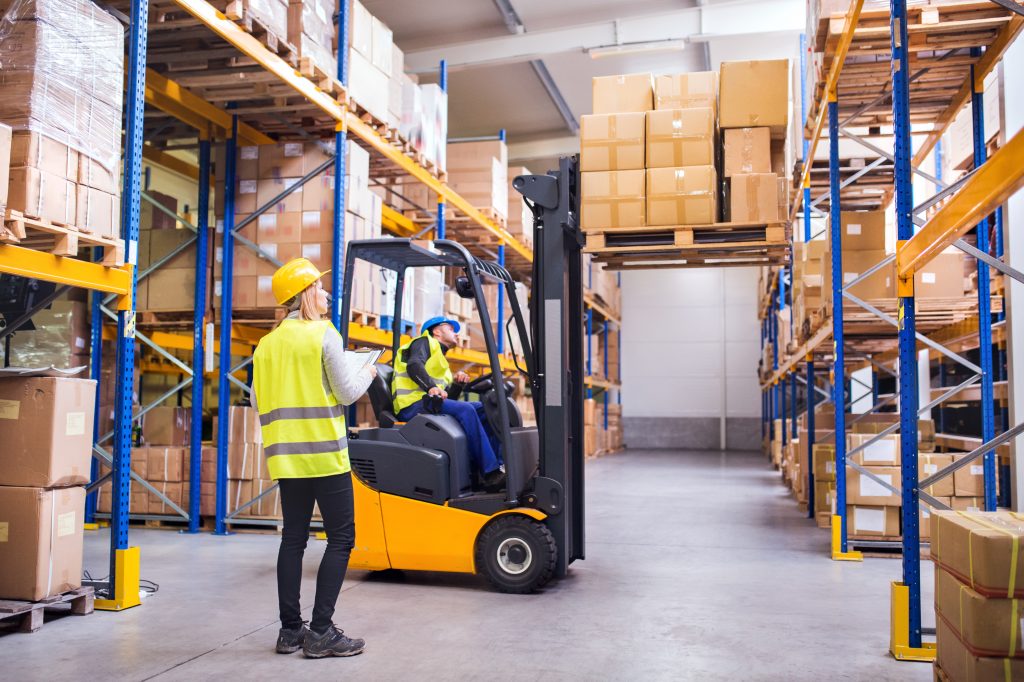
Modula’s Automated Solutions for Warehouse Management
1.Modula Vertical Lift Modules
2. Modula Horizontal Carousels
3. Modula Warehouse Order Picking Solutions
4. Modula Warehouse Management System
Manage inventory, assign tasks, gain insights into your stock levels in real-time and manage employee access with our Warehouse Management System.
Seamlessly integrate the Modula WMS with Modula Vertical Lift Modules and your local ERP for a comprehensive solution.
At Modula, our automated solutions can help you implement warehouse management best practices and optimize operations across the board.
From our advanced picking solutions to smart storage options, you can improve productivity, picking accuracy, safety and organization at your facility, with Modula.