What Is Warehouse Slotting? Types, Benefits & Best Practices
A recent report found that on average, the eCommerce industry is anticipated to grow by almost 27.15% between 2022 and 2027.
Due to this uptick in demand, warehouse managers are faced with the challenges of handling more inventory and getting shipments out the door faster, without expanding the workforce or increasing the warehouse’s footprint.
One solution to these challenges? Warehouse slotting.
We’ll share everything you need to know about warehouse slotting, including types and best practices, and introduce you to automated warehouse solutions at Modula to help streamline your warehouse operations, from inventory storage to picking and beyond.
What is Warehouse Slotting?
Warehouse slotting, also known as inventory slotting, is strategically organizing inventory in a warehouse or logistics facility to maximize space, improve picking efficiency and enhance material handling.
This process requires warehouse planners to strategically identify the most efficient location for inventory.
Warehouse slotting is typically organized by product type or stock-keeping unit (SKU) number.
Slotting Strategies: Fixed vs. Random and Macro vs. Micro
Warehouse slotting strategies can be categorized into two primary approaches: Fixed Slotting vs. Random Slotting and Macro Slotting vs. Micro Slotting.
Fixed Slotting vs. Random Slotting
Fixed slotting is an inventory slotting method used for products that have a permanent location.
On the other hand, instead of having a reserved slot, random slotting is an inventory slotting method used for products that are assigned to an available pick zone.
Typically, fixed slotting is reserved for fast-moving items, such as electronics, while random slotting is utilized for slow-moving items, such as seasonal decorations.
Macro Slotting vs. Micro Slotting
While macro slotting is the process of arranging the overall layout of a warehouse, including the strategic placement of pick zones, aisles and storage areas to optimize the flow of goods, micro slotting is the process of organizing the specific placement of items within these designated areas.
This includes the specific placement of goods on shelves or in bins, the orientation of items for easy access and the grouping of products based on size, dimensions, weight or frequency of use.
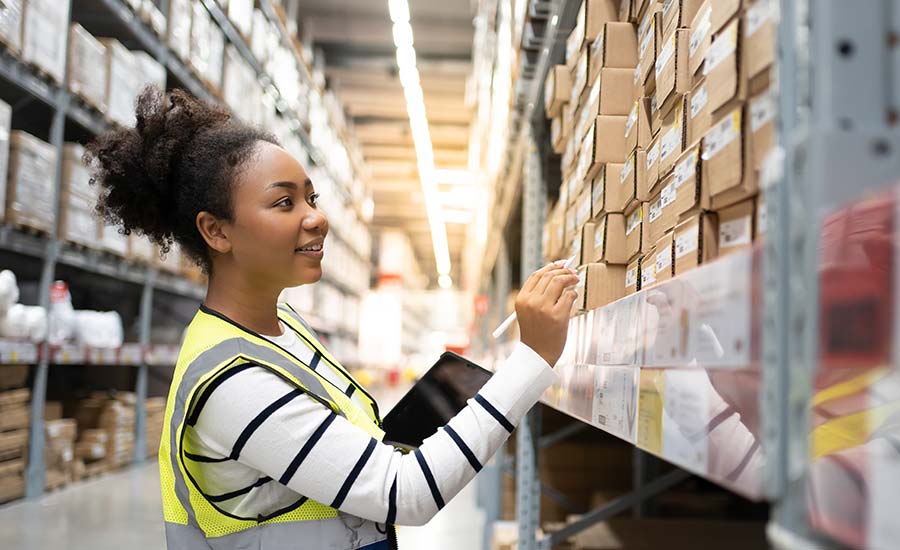
Data That Help You Set Up Warehouse Slotting
Clear benefits arise from developing an efficient warehouse slotting strategy, but where should you start?
Warehouse managers can use the supply chain data below to create a slotting process that can help optimize their facility.
- Product Velocity (Demand Frequency): Understanding how frequently each item is picked is essential for determining its optimal location. Fast-moving items should be placed in easily accessible areas to reduce travel time, while slower-moving items can be stored in less accessible locations.
- SKU data: This data identifies a product’s type and dimensions, allowing you to understand any special storage or handling needs.
- Order history: Order history is a record of all previous customer orders, outlining the specific items purchased, their costs, customer data and purchase dates.
- Item picking level: This information specifies whether picking occurs at the pallet, case or individual item level and indicates the storage medium used for picking.
Benefits of Warehouse Slotting
From minimizing travel time to increasing workplace safety, here are three ways warehouse slotting can improve your bottom line.
Optimize Warehouse Space
With efficient warehouse slotting, you can free valuable floor space in your facility and streamline operations in a more compact area.
Maximizing your existing space can lead to savings on expenses tied to a larger warehouse — especially as warehouse rental rates in the United States continue to skyrocket.
With warehouse slotting, you can also adapt more quickly and easily to changes in inventory levels or product lines and maintain operational efficiency without the need for constant physical adjustments.
Reduce Travel Time
With warehouse slotting, warehouse operators can store fast-moving inventory near the shipping area.
This reduces the travel time for warehouse employees, resulting in faster picking and stock replenishment, increasing overall productivity.
Increase Safety
If your goods aren’t properly stored, a warehouse can be a breeding ground for workplace injuries, from tripping over messy inventory to getting hit by falling items.
With a well-planned slotting strategy, you can optimize the flow of employees and machinery to avoid congested areas, reducing the chances of warehousing hazards and accidents.
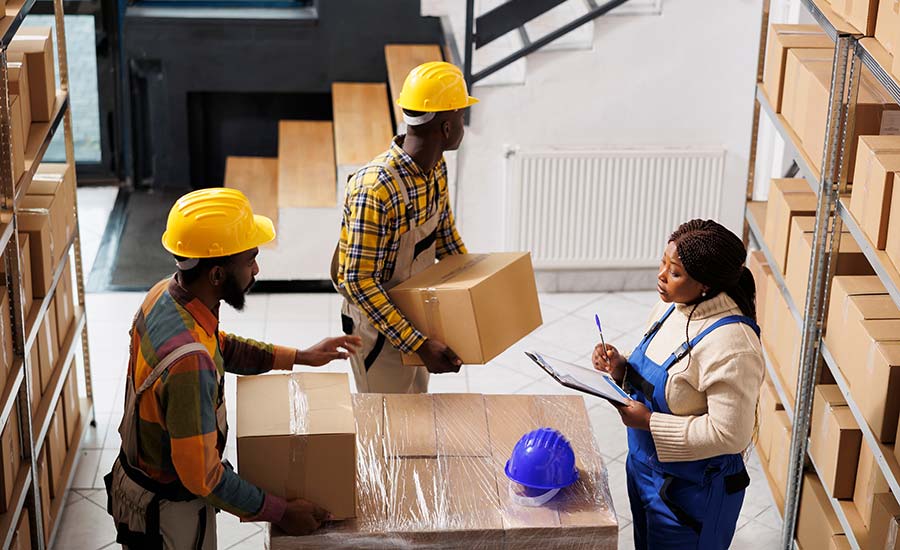
Inventory doesn’t sit idle — it acquires storage costs the longer it remains unshipped to customers.
Just-in-time inventory processes focus on maintaining minimal stock levels to reduce carrying costs — the expenses incurred by a business to store and manage inventory over time.
Warehouse slotting can help reduce these costs by boosting throughput. The faster your business processes inventory, the less time and money you spend on storage.
Warehouse Slotting Algorithms
Managing a warehouse involves considering several factors, especially when handling numerous SKUs and frequently shifting priorities.
One effective warehouse slotting method is the “ABC” algorithm.
Warehouse managers can categorize products by placing:
- Category A products, also known as high-value goods, in Category A locations. Items in group A are positioned closest to the door to optimize retrieval efficiency.
- Category B products, also known as medium-value goods, in Category B locations. After reserving the best locations for Category A references, place them in the most accessible and direct areas available in the warehouse, such as along main aisles or close to the loading docks.
- Category C products, which are the least valuable or in low demand, in Category C locations. Evaluate goods in this category to determine if their storage costs outweigh the profits. C products are usually placed in less accessible areas or at the back of the facility.
This approach can help determine item velocity using order history data, typically analyzing the SKUs of items ordered in the last 30 days.
Warehouse Slotting Optimization Best Practices
From slotting inventory by SKU to educating your employees about slotting procedures, here are 11 warehouse slotting best practices.
Organize Your Warehouse
Organizing your warehouse plays a key role in reducing travel time and ensuring that goods are easily accessible, as it streamlines the flow of operations and minimizes the physical effort required for stocking and picking.
Organization goes hand in hand with the principles of warehouse slotting, in which goods are strategically placed to optimize efficiency and accessibility.
To organize your warehouse:
- Utilize vertical space for storage to maximize your warehouse’s storage capacity
- Design your warehouse’s layout to streamline the flow of order fulfillment and improve bottlenecks and overall efficiency. For example, position the receiving area near storage areas to reduce the travel time.
- Periodically review and reorganize your warehouse layout to adapt to new products, seasonal shifts or changes in sales patterns
At Modula, our advanced automated storage solutions and retrieval systems help further optimize your inventory slotting thanks to advanced storage systems, like Modula Vertical Lift Modules (VLMs).
Modula’s VLMs are fully automated vertical storage systems that allow for a large inventory of goods to be quickly accessed while being stored in a safe and secure environment.
Working with limited ceiling height? Modula Horizontal Carousels (HC) are built to safely and efficiently store your warehouse inventory in one location.
Slot Inventory by SKU Velocity
From a sudden demand for beach balls in the summer to can’t-miss discounts during the holidays, seasonality can cause SKU velocity to change.
To compensate for spikes in demand, assess and create a stock distribution strategy to change inventory slotting layouts and achieve warehouse efficiency year-round.
To slot inventory by SKU velocity:
- Determine which products are or will be affected by seasonal demand
- Identify when peaks will occur
- Identify fast-moving items and place them near shipping area for easy access
- Consolidate SKUs that are frequently picked together in the same storage area
Slot Inventory by Zone or Equipment
Properly zoning each SKU, such as storing perishable goods in controlled environments, is key to efficient inventory management and safety.
To slot inventory by zone:
- Outline your warehouse picking zones
- Identify SKUs and their proper storage area — for example, keep perishable items in environmentally controlled areas and store flammable liquids in the flammable zone
In addition to slotting inventory by zone, you can optimize inventory slotting by storing goods close to each other based on the picking equipment used.
For example, items that require similar handling equipment, such as pallet jacks or forklifts, can be grouped together. This approach minimizes the time and effort needed for equipment operators to move between different types of machinery.
To slot inventory by picking equipment:
- Store heavy items in aisles that are close together
- Keep small parts in a different picking zone, away from heavy inventory
- If you use a forklift or scissor lift to pick inventory, make sure the storage aisles are wide enough to accommodate heavy machinery
Slot Inventory by Product Affinity Analysis
Product affinity analysis is the process of looking into consumer behavior to assess and identify which goods are commonly purchased together, then offering these items as a kit or bundle.
Examples of kitted or bundled items that can be sold together are ink cartridges and a printer or dry pasta and canned tomatoes.
To slot inventory by product affinity analysis, store bundled items next to each other
Slot Inventory by Special Storage Requirements
Slotting inventory by special storage requirements can help you optimize warehouse operations, enhance safety and improve inventory management.
To slot inventory by special storage requirements:
- Assess each item for its specific storage needs, such as temperature control or humidity levels.
- Allocate dedicated zones in the warehouse for different storage requirements. For example, create separate areas for refrigerated goods, dry storage and hazardous materials.
- Use specialized storage equipment and materials that cater to the needs of different goods. For example, use insulated containers for temperature-sensitive goods and spill containment pallets for liquids.
Modula clean rooms and temperature-controlled environments can store perishable goods and optimize your refrigerated picking zones.
All of our controlled environment storage systems feature temperature variations that meet industry standards and regulations, and protect goods from contaminants.
Rank Slots by Priority
Assign priority levels to each slot in your warehouse based on factors such as item size, weight and SKU velocity.
High-priority slots should also be easily accessible and located closer to the packing and shipping areas to make sure that the most frequently picked items can be accessed and dispatched with minimal delay.
To rank slots by priority:
- Regularly review sales figures and usage patterns to identify which items are transported more frequently and determine which items are high priority.
- Perform ABC analysis to categorize inventory into three groups: ‘A’ for high-value items with low frequency, ‘B’ for moderate value and frequency and ‘C’ for low-value but high-frequency items. This inventory management technique can help prioritize the placement of goods in your warehouse.
- Allocate slots based on their weight and size. For example, place large items in areas where they can be easily moved without blocking pathways. Allocate smaller inventory to higher shelves or compact storage units in which space can be optimized and items can be retrieved without physical strain.
Invest in a Warehouse Management System
An advanced warehouse management system can significantly enhance your slotting strategy, as it provides real time data on your inventory, tracks item movement and can suggest optimal slotting arrangements based on changing demand patterns and inventory levels.
Modula’s Warehouse Management System (WMS) is expertly engineered to seamlessly integrate with our cutting-edge automated storage and retrieval systems, creating a cohesive and efficient warehouse management experience.
Tailored to optimize and streamline operations, Modula’s WMS provides a user-friendly interface for effortless management and real time inventory monitoring.
Train Your Employees on Slotting Procedures
Educate your employees on slotting procedures to equip them with the skills needed for managing inventory and ensuring accurate placement and tracking.
To train your employees:
- Conduct workshops or training programs that cover the basics of slotting and the importance of accurate inventory placement and tracking.
- Provide on-the-job training to show employees the process of warehouse slotting. This can include demonstrations on how to manage different types of inventory and organize items based on their size, weight and SKU velocity.
- Pair new employees with experienced staff who can offer guidance and share best practices for efficient slotting and inventory management.
Demand correlation describes items that are usually ordered together. Analyzing previous order histories can help identify these products.
For example, if you notice that customers often buy shampoo and conditioner at the same time, placing these items next to each other in the warehouse can optimize the picking process and speed up order fulfillment.
Once you identify them, rearrange your warehouse to place commonly purchased items closer together, significantly reducing picking time.
Gain Feedback from Your Warehouse Pickers
Pickers know your warehouse layout best, as they’re always on the move in your facility.
They are most likely to have ideas on how to rearrange things for better efficiency, such as grouping frequently ordered items closer to packing stations.
Collaborate with your warehouse pickers to find ways to organize inventory more effectively, making the order picking process smoother and less confusing.
Collaborate with a 3PL
Slotting can be challenging without the right team and technology.
Opt for a tech-driven third-party logistics (3PL) company to help alleviate the stress of managing warehouse operations, organizing inventory and fulfilling orders quickly at an affordable rate.
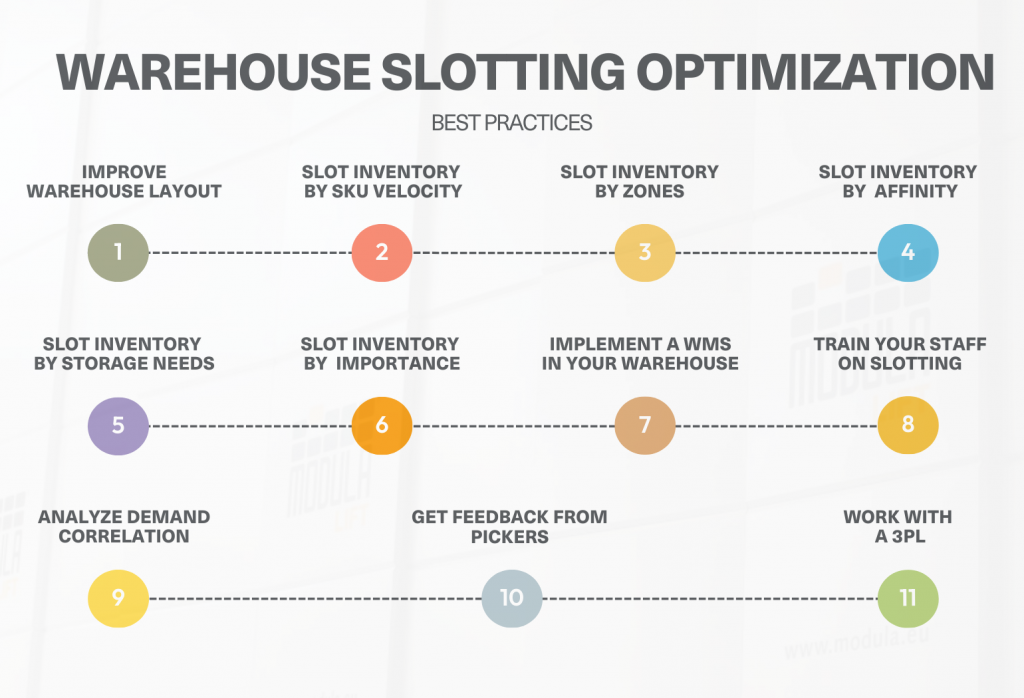
A Quick Recap on Warehouse Slotting
To recap, warehouse slotting or inventory slotting is the process of creating an efficient organization strategy in a warehouse.
This process is typically dependent on SKU number, SKU velocity, product type, product groupings and other factors, to determine the ideal warehouse setup.
At Modula, we offer intuitive and state-of-the-art automated solutions to optimize the slotting process. Contact our team to learn how our technology can be tailored to your needs.
Our experts are ready to provide personalized advice and solutions for your warehouse.