What Is Warehouse Logistics? Components, Challenges & Tips
Warehouse logistics is the backbone of every supply chain operation, as it ensures the efficient storage, handling and distribution of goods.
With the ideal warehouse logistics in place, your organization can cut costs, speed up deliveries and meet changing consumer demands.
In this article, we’ll cover everything you need to know about warehouse logistics, including its key components and best practices.
We’ll also share automated solutions at Modula to help optimize your operations, increase efficiency and improve overall performance in your warehouse.
What Is Warehouse Logistics?
Warehouse logistics is the process of organizing, coordinating, managing and implementing the storage and movement of goods in a warehouse.
The process includes handling the physical flow of items, such as shipping and receiving, and efficiently managing information and time.
Warehouse logistics also utilizes advanced technologies and smart strategies to improve efficiency, increase customer satisfaction and cut costs.
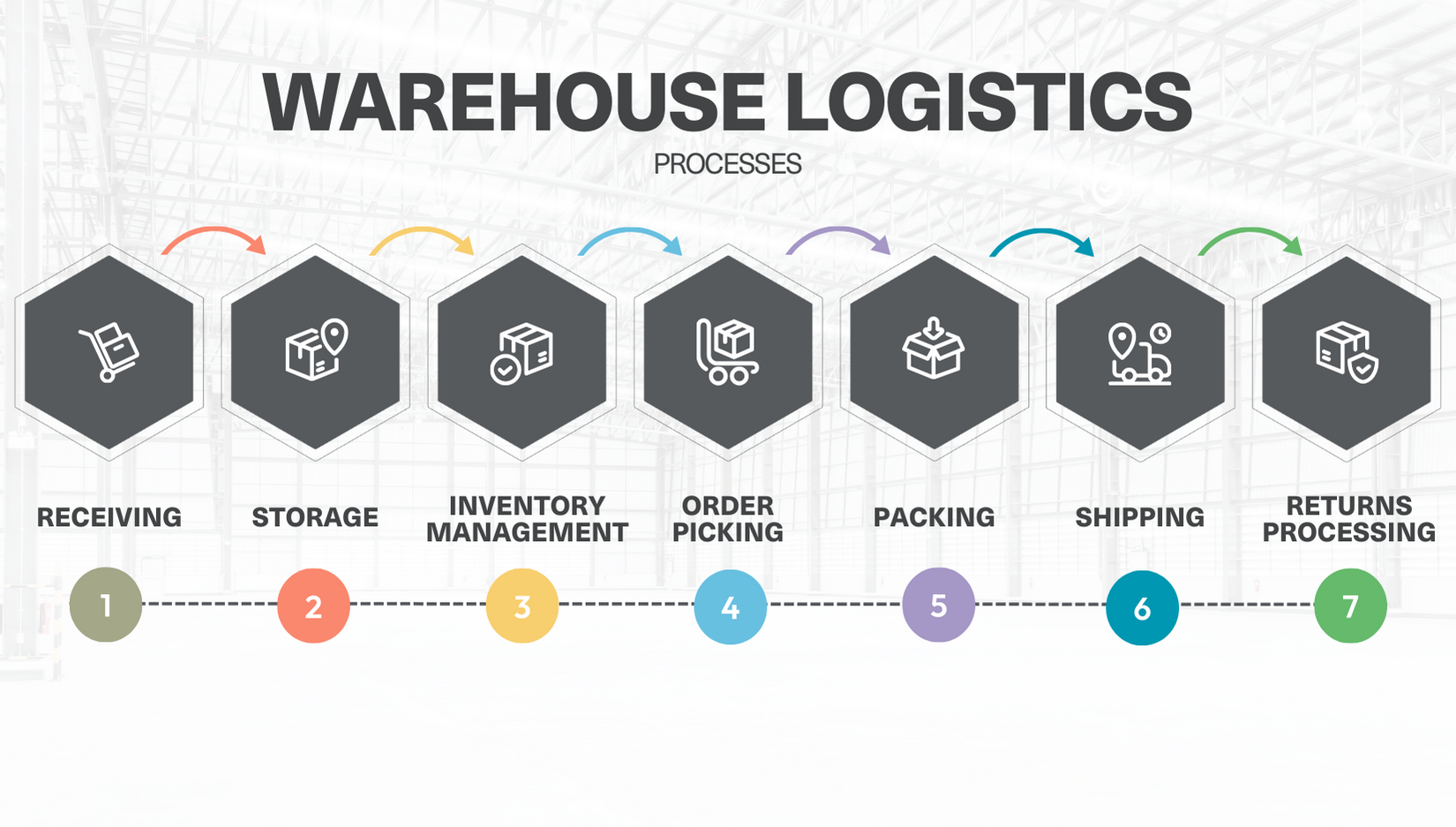
Supply Chain vs. Warehouse Logistics
While supply chains and logistics are related, they serve different roles in business operations.
Managing your supply chain involves overseeing the flow of goods and services from point A (the facility) to point B (the consumers), and collaborating closely with suppliers, distributors and customers.
On the other hand, warehouse logistics focuses on handling goods within your warehouse or distribution center, aiming to improve inventory management, reduce storage costs and optimize order fulfillment.
Key Components of Warehouse Logistics
Each component of warehouse logistics plays a key role in ensuring inventory moves swiftly and accurately from your facility to consumers.
Let’s dive into the three main components of warehousing logistics:
Warehouse Management
A key aspect of logistics is continuously improving your warehouse’s daily operations. This includes refining warehouse tasks to boost efficiency and meet market needs.
Warehouse management is essential for organizing, cross-docking and distributing inventory. It also includes overseeing staff, maintaining safety standards and building connections with shipping companies.
Warehouse Operations
Effective warehouse management can help improve the movement of goods inside and out of your warehouse.
Optimizing your operations offers a plethora of benefits, including:
- Reduced inventory and shipping costs
- Improved warehouse organization
- Boosted employee productivity
- Accurate picking
Warehouse Management System (WMS)
A warehouse management system (WMS) is a software solution that can help you organize and manage warehouse tasks.
You can also integrate a WMS with a wide range of technologies, such as RFID technology, barcode scanning and historical data and reporting.
It provides your warehouse operators with a comprehensive view of your inventory and oversees processes from receiving to distribution, including data collection.
Key Benefits of an Optimized Warehouse Logistics Plan
A strategic warehouse logistics plan is essential for any business aiming to enhance efficiency. This strategic approach provides key benefits that significantly improve the bottom line and boost profitability, including:
- Improved customer satisfaction: There’s nothing quite like the feeling of delivering an order on time and in mint condition. Doing this consistently can ensure your customers are satisfied while building your reputation as a reliable, go-to brand in the market.
- Better inventory control: A well-organized logistics strategy guarantees that inventory records are precise and updated. This accuracy is paramount for decreasing (or even eliminating) order fulfillment errors and reducing possible inventory shrinkage.
- Boosted efficiency: Envision your inventory transitioning smoothly from the moment your staff receives it until shipment. Streamlined logistics facilitate a seamless flow, significantly reducing errors and enhancing workflows. Automated sorting systems quickly categorize and organize shipments, further decreasing processing times.
- Reliable delivery schedules: Knowing exactly when your SKUs will arrive is paramount for strengthening supply chain reliability — a cornerstone of effective warehouse logistics. This means you can consistently meet customer demands and deliver products on time, in the correct quantities.
- Reduced operational expenses: Streamlined logistics can help lower labor costs and minimize waste, such as unnecessary warehouse traveling. When you improve your facility’s layout and incorporate automation into your processes, you can cut down on your employees’ time spent on each task.
Challenges of Warehouse Logistics
Properly managing inventory is paramount to streamlining warehouse operations. However, inventory management often poses unique challenges that can affect the productivity and efficiency of operations.
According to Manufacturing.net, around 20 to 30% of inventory is obsolete, even in well-run companies. This can cost them up to 11% of revenue loss, highlighting the importance of gaining full visibility into your goods.
Key challenges of warehouse logistics include:
- Space constraints: Limited warehouse space significantly challenges warehousing logistics, leading to inefficient storage, difficulty finding items and longer material handling times.
- Inefficient picking strategy: Picking, packing and shipping errors can lead to incorrect or incomplete orders, which may result in customer complaints, costly returns and loss of revenue. For example, if your employee picks the wrong SKU, it must be verified and returned to the packing area for correction.
- Ineffective labor management: Warehouses often experience labor shortages during peak seasons, which typically occurs when consumers prepare for the holidays. Ineffective labor management can cause excessive workloads and significantly reduce productivity levels.
- Inaccurate inventory management: Effectively managing inventory means keeping accurate stock levels to avoid both overstocks and stockouts. Businesses must also handle different SKUs, a variety of product features and changing demand.
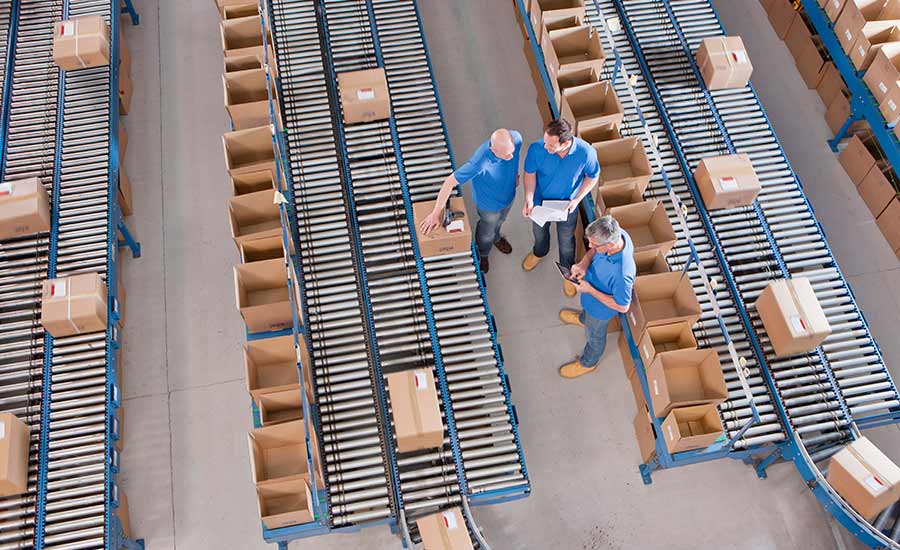
Tips to Improve Your Warehouse Logistics
Warehouse logistics best practices include methods that focus on optimizing space utilization, enhancing inventory accuracy, leveraging technology for efficiency and more.
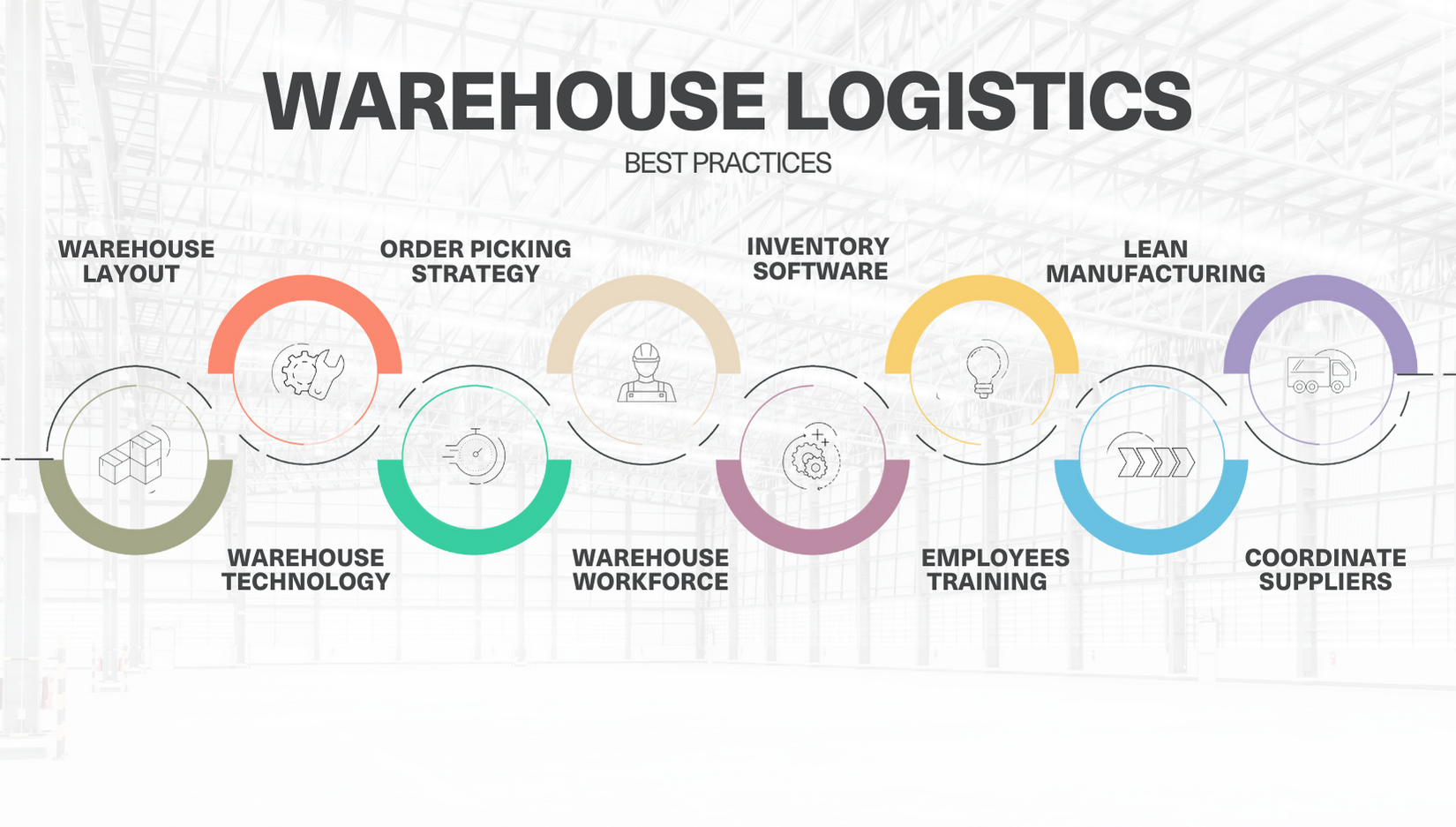
Here’s how you can improve your warehouse logistics:
Select a Strategic Warehouse Layout
An effective warehouse layout improves inventory flow. If your warehouse is disorganized or cluttered, modifying its layout can streamline processes by eliminating confusing setups.
You can choose from a wide range of layouts, such as the U-, I- and L-shaped design layouts.
- In the U-shaped layout, the flow of goods moves in a U shape. It begins and finishes at the open ends of the U, which are typically designated for shipping and receiving. This setup allows for efficient movement between these critical areas.
- In the I-shaped layout, operations flow in a straight line, facilitating a direct path from receiving to shipping. The I-shaped design allows for a linear flow from receiving to shipment.
- In the L-shaped layout, operations flow in a configuration that resembles the letter “L”. This layout maximizes the use of a warehouse’s corners, which is particularly beneficial for facilities that need to separate different functions within the same building. For example, one leg of the “L” can be allocated for receiving and processing, while the other is for storage and shipping.
Invest in Warehouse Technology
As warehouses expand, using smart systems like autonomous mobile robots (AMRs), automated guided vehicles (AGVs), and warehouse robots can help cut down on manual work and boost picking speed and accuracy.
Moreover, adopting warehouse storage solutions like automated storage and retrieval systems (ASRS) can help reduce manual errors like mispicks, inaccurate inventory counts and misplaced items.
These systems also save space, improve picking accuracy and enhance overall productivity.
At Modula, our state-of-the-art ASRS, including Modula Vertical Lift Modules (VLMs), can help optimize your warehouse logistics.
Modula’s VLMs are the ideal automated vertical storage solutions that can store various parts and components in your facility, regardless of their size and dimensions. By utilizing high ceilings, you can also significantly reduce the space needed for storage.
If ceiling height is a concern, Modula Horizontal Carousels (HC) offer a safe and efficient way to store inventory in one place.
Utilize the Ideal Order Picking Strategy and Systems
The best picking strategy can help minimize, or even eliminate, mispicks. This further reduces costly returns and product exchanges.
To choose the best order picking strategy for your business, consider factors like the size of your inventory, the variety of items, order volume and the layout of your warehouse.
For example, if you have a high volume of similar small items, a zone picking strategy, where pickers are responsible for specific areas and pass items down a line, might be most efficient.
You can also try automated picking solutions to increase picking speed and accuracy by replacing pick tickets with light devices and minimizing the inventory search time.
At Modula, we provide reliable picking systems that seamlessly integrate with our storage solutions, ensuring order accuracy and efficiency.
Optimize Your Warehouse Workforce
To maintain peak productivity in your warehouse, make sure you have the right number of skilled workers.
To balance your staff, it’s crucial to understand how management needs fluctuate alongside demand.
For example, you’ll likely need more staff before and after a busy holiday season, to manage both increased orders and post-holiday returns.
Implement a Warehouse Management System
An advanced WMS can help improve your warehouse logistics, as it streamlines a wide range of processes, from inventory tracking to setting access levels. This ensures accurate, real-time data is always available.
Modula’s Warehouse Management System (WMS) is designed to integrate seamlessly with our advanced ASRS. It’s customized to enhance operations, offering an easy-to-use interface for simple management and real-time inventory tracking.
Prioritize Employee Training
While warehouse management systems can perform different tasks, such as monitoring the location and movement of goods within your facility, your employees will still need training on how to use these innovations.
Consider implementing regular training sessions, like simulation training and coaching, to ensure all your warehouse operators can safely use the equipment.
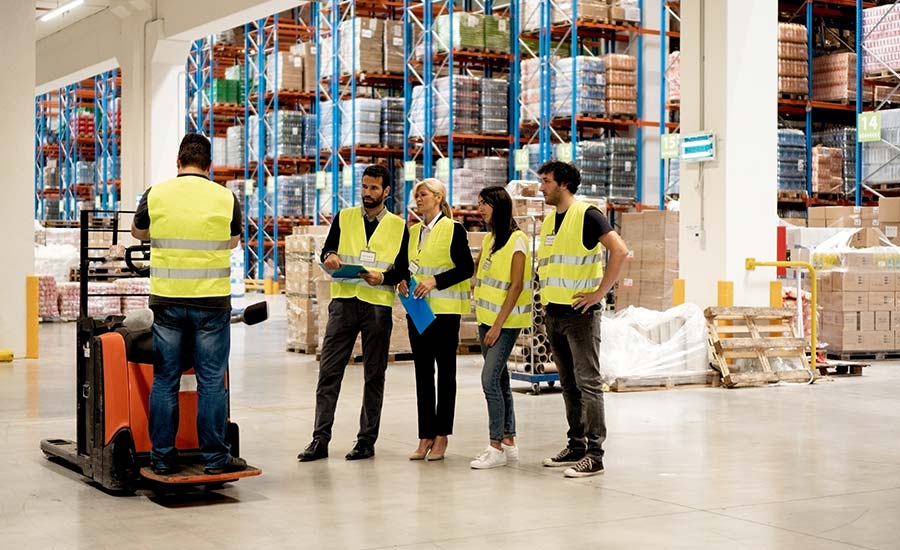
Adopt Lean Manufacturing
Lean manufacturing is an approach to warehouse management that strives to boost efficiency, improve productivity and cut waste, such as excess stock and unnecessary labor hours, without affecting overall productivity.
To achieve lean manufacturing in your operations:
- Identify and eliminate unnecessary steps in your workflows to make your operations more efficient
- Train and involve employees in identifying areas for improvement, ensuring they have the skills and authority to make changes
- Regularly review processes and implement improvements, aiming for ongoing enhancement of efficiency and productivity
Coordinate With Suppliers and Contractors
Contractors and suppliers are crucial to your company’s operations. Work closely with them by coordinating warehouse logistics, such as sharing delivery times or scheduling deliveries, to better manage your inventory.
At Modula, we provide advanced automated solutions to improve your warehouse logistics. Reach out to learn how we can customize our technology for your operations.
Our experts are available to provide tailored advice and solutions for your business.
Monitor Your Warehouse Logistics
Optimal warehouse logistics must remain flexible, adapting to changing consumer behavior and fluctuations in the flow of goods. As you introduce new equipment to your team, each process may need a unique approach.
For example, when you install automated storage and retrieval systems (ASRS) in your facility, you may want to reconfigure your warehouse layout to optimize the flow of goods.
Similarly, training programs will most likely be updated or developed to ensure new employees can operate machinery efficiently and safely.