The Quick ROI of Automated Storage and Retrieval Systems
Any significant investment in warehouse technology or equipment should demonstrate a valid return on investment (ROI) by effectively boosting overall productivity and reducing operational costs over time.
Investments that deliver a clear and fast ROI justify the initial expenditure and reinforce strategic decision-making, aligning with long-term business goals and growth.
In this article, we’ll explore factors driving the surprisingly quick ROI of Modula automated storage and retrieval systems (ASRS), focusing on how these systems can help optimize warehouse operations, reduce labor costs and maximize storage efficiency in warehouses.
What Is the ROI of Modula Automated Storage and Retrieval Systems (ASRS)?
Prospective customers typically ask about the typical payback period for an ROI with a Modula vertical lift module (VLM) or horizontal carousel (HC).
Most individuals are surprised to learn the ROI ranges from six to 18 months.
Despite hefty upfront costs, a detailed analysis shows that Modula VLMs or HCs offer different ways to cut expenses and capital costs, which accounts for the rapid ROI.
How Do Modula Automated Storage and Retrieval Systems Deliver a Quick ROI?
Save Space
Logistics real estate consulting firm, Prologis, predicts a 5% increase in warehouse rents in the United States and a 4% global increase in 2021, likely due to a surge in inventory and limited storage space, according to a DC Velocity report.
Our automated storage systems, especially our vertical lift modules, occupy 90% less floor space than traditional shelving.
This significant space savings means many of our customers avoid relocating to larger facilities. Besides avoiding capital costs of expanding facilities, this can also yield additional benefits.
For example, warehouse managers can repurpose areas previously used for storage to generate profit, such as setting up additional production lines or expanding assembly areas.
Many automotive dealers using our VLMs have also capitalized on this space efficiency, minimizing building and maintenance costs for storage facilities.
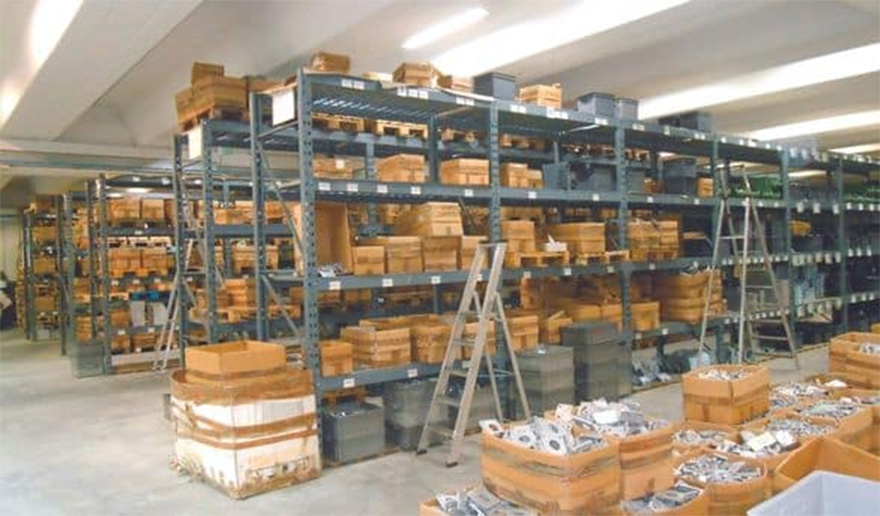

Increase Efficiency
Vertical lift modules and horizontal carousels significantly outperform manual methods, often boosting productivity by 300% or more.
These systems also enhance efficiency by delivering items directly to the operator, as they follow the goods-to-person principle.
In many manufacturing and warehouse settings, layouts are often ineffective, which can lead to wasted space. Integrating automated storage and retrieval systems transforms these facilities by optimizing their layout and maximizing every corner possible.
Support Accurate Pick Rates
In traditional warehouses, human errors are nearly inevitable, as employees rely on printed pick lists to retrieve dozens of units from shelves daily.
Delivering the wrong item is costly, leading to additional delivery expenses and customer dissatisfaction.
Industry estimates place the cost of each mispick at up to $100. This means that just a few errors weekly can cost an organization up to $10,000 annually.
Modula automated storage and retrieval systems, which are equipped with laser pointers, alphanumeric LED bars and put-to-light systems, can help guide operators precisely to the right SKUs and quantities needed, virtually eliminating mispicks.
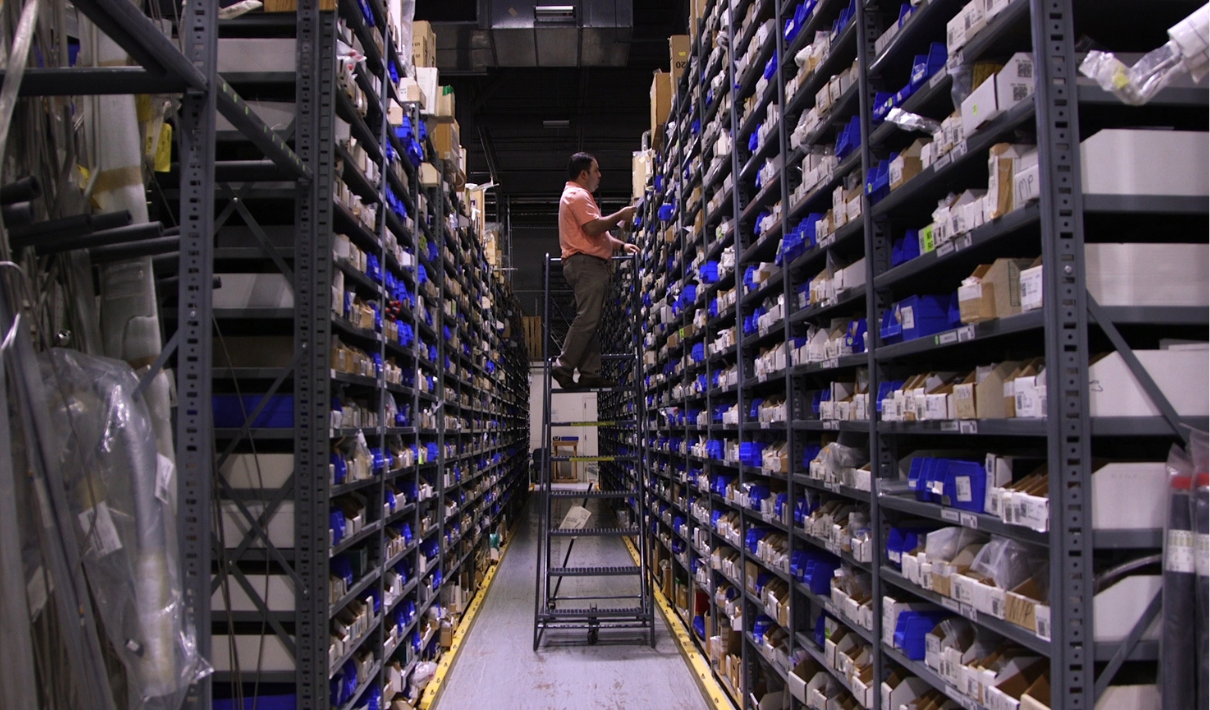
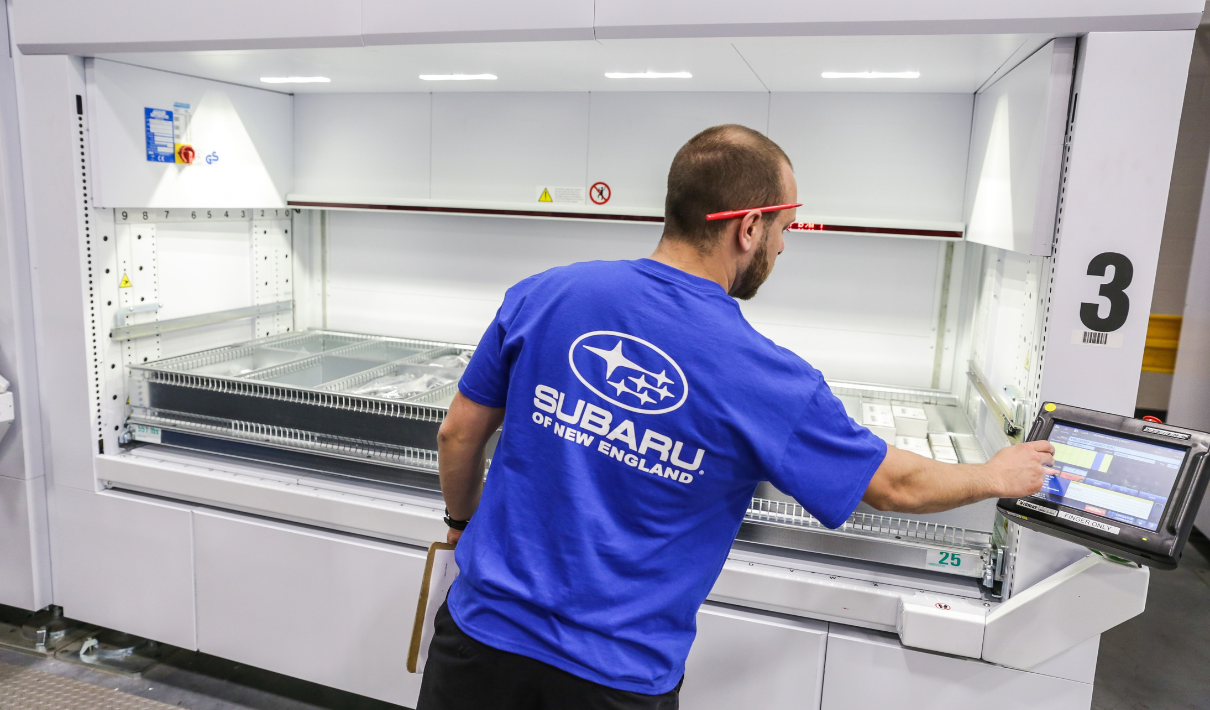
Improve Productivity
According to Zebra’s 2024 Warehousing Vision Study, 60% of warehouse operators identify labor recruitment and productivity as their top challenges.
Industry studies show storage solutions can boost workforce productivity by up to 85%, allowing one warehouse operator to handle the workload previously managed by several individuals.
VLMs and HCs also eliminate physical strain by removing the need to walk, stoop, or climb ladders to retrieve items, typically resulting in lower turnover. These systems require less skill to operate, broadening the pool of potential candidates.
The best part? Automated storage systems reduce costs related to workplace injuries, as goods are delivered at an ergonomically correct height.
Better Manage Inventory Tracking
Warehouse management systems (WMS) track the movement of items in real time, virtually eliminating the need for manual inventory monitoring.
Additionally, your company can gain better supply chain insights, especially when integrating Modula’s warehouse management systems with the company’s ERP or DMS.
Warehouse managers no longer have to worry about understocking or overstocking issues. Furthermore, inventory tracking can help secure your inventory against theft, as valuable items are kept in a controlled environment with restricted and monitored access.
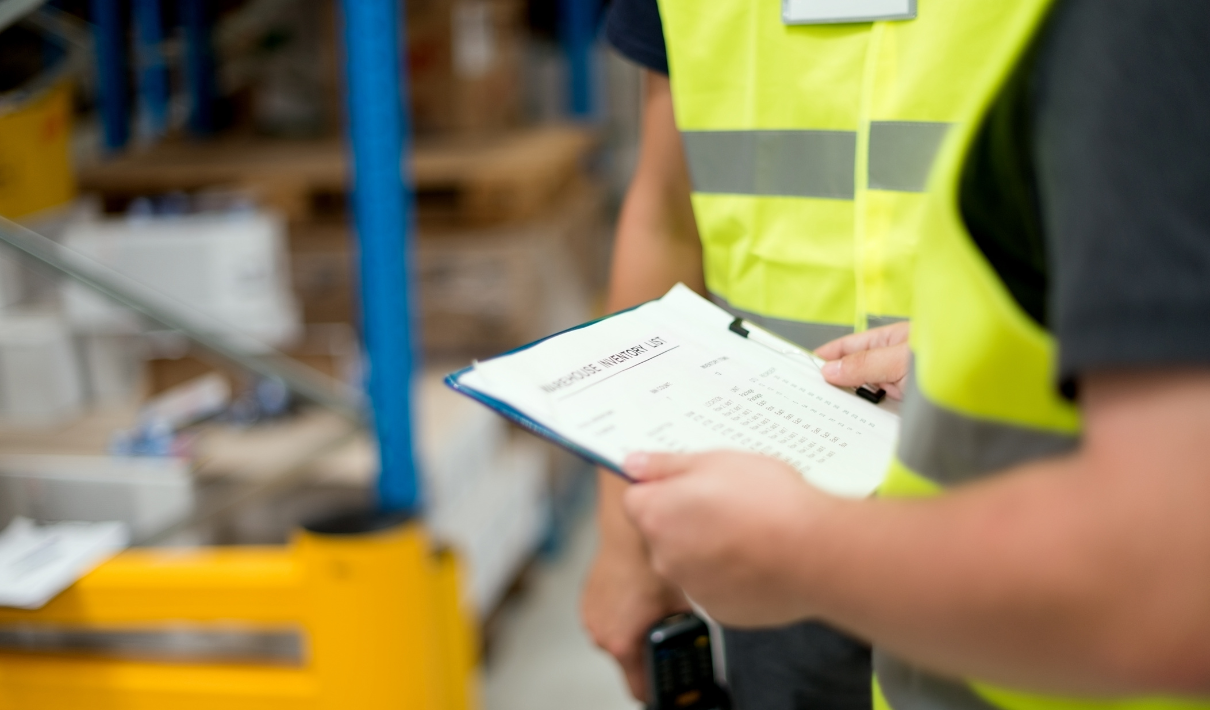
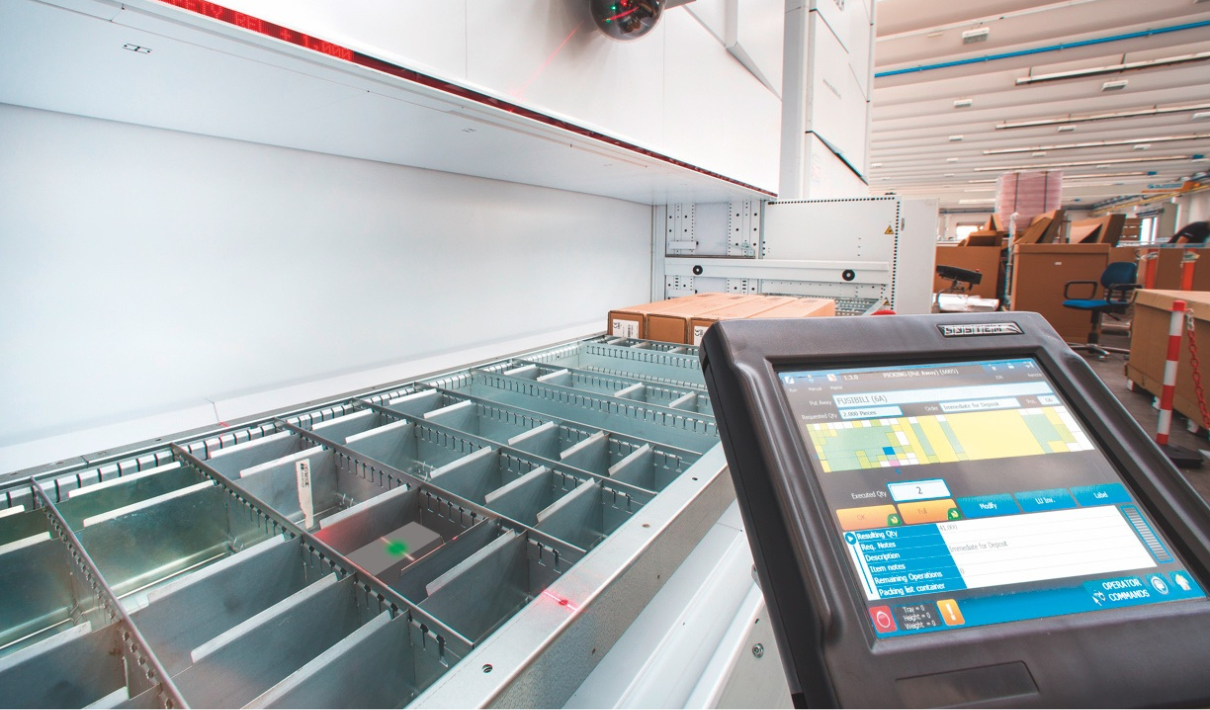
How To Calculate the ROI of Your Automated Storage and Retrieval System
Calculating the ROI of your ASRS is essential for understanding its financial impact and justifying the investment.
We’ll detail the steps to help you calculate your return on investment, so you can make well-informed decisions about your warehouse automation strategy.
Identify Costs
Start by calculating all costs associated with the ASRS, including purchase price, installation, software integration and any training for staff.
For example:
- Purchase price: $500,000
- Installation costs: $50,000
- Software integration: $25,000
- Staff training: $10,000
Quantify Savings and Gains
Measure the direct benefits the system provides, such as labor savings from reduced workforce requirements, increased productivity, lower error rates, reduced inventory damage and savings from better space utilization.
Here are a few formulas to help you measure some of the benefits of automation
1. LABOR COST SAVING
- Fewer workers needed for picking, packing, and replenishment.
- Faster retrieval times reduce labor hours.
- Annual Labor Savings Formula = No. of workers reduced x times Hourly wage x Hours per year
2. SPACE OPTIMIZATION SAVING
- ASRS allows higher-density storage, reducing warehouse space costs.
- Potential to avoid warehouse expansion or rental costs.
- Space savings Formula = Warehouse cost per sq. Ft. x sq. ft. saved
3. INCREASED ORDER ACCURACY SAVING
- Fewer mispicks reduce errors, refunds, and customer complaints.
- Savings from reduced returns and rework
- Accuracy Savings Formula = Average cost per mispick x Mispicks reduced per year
4. INCREASED THROUGHPUT SAVING
- Faster picking speeds increase the number of orders fulfilled per hour.
- More orders processed per shift = Higher revenue.
- Throughput savings Formula = New orders per hour\Old orders per hour x Revenue per order
5. INVENTORY CARRYING COST SAVINGS
- ASRS improves inventory tracking, reducing overstocking and stockouts.
- Less capital tied up in excess inventory.
- Inventory Carrying Cost Savings Formula = Reduction in excess stock x Carrying cost percentage
Estimate the Intangible Benefits
Consider the value of less tangible benefits, such as improved employee morale, enhanced customer satisfaction from more accurate order fulfillment, and increased security measures.
Additionally, factor in workplace safety improvements, as AS/RS reduces manual lifting, bending, and climbing, lowering workplace injuries, absenteeism, and compensation claims. Employee satisfaction and retention also improve, as automation reduces repetitive tasks and burnout, allowing workers to focus on higher-value responsibilities.
Better data accuracy from real-time inventory tracking minimizes stock discrepancies, enhances demand forecasting, and streamlines decision-making. AS/RS also contributes to sustainability by maximizing warehouse space, reducing energy consumption, and minimizing packaging waste.
While these benefits may not have immediate monetary values, they significantly impact long-term efficiency, risk reduction, and overall business growth—strengthening the ROI of AS/RS investment.
Calculate Net Benefits
To determine the net benefits of your ASRS, subtract both the initial investment and ongoing operational costs from the total benefits accrued during a specific period, typically over one year.
Apply the ROI Formula
Use this formula:
This formula calculates the ROI percentage, indicating the return generated for each dollar spent.
Leverage our ROI calculator to accurately assess the financial benefits and payback period of your investment.
- ROI Formula = Net Benefits : Total Cost x 100
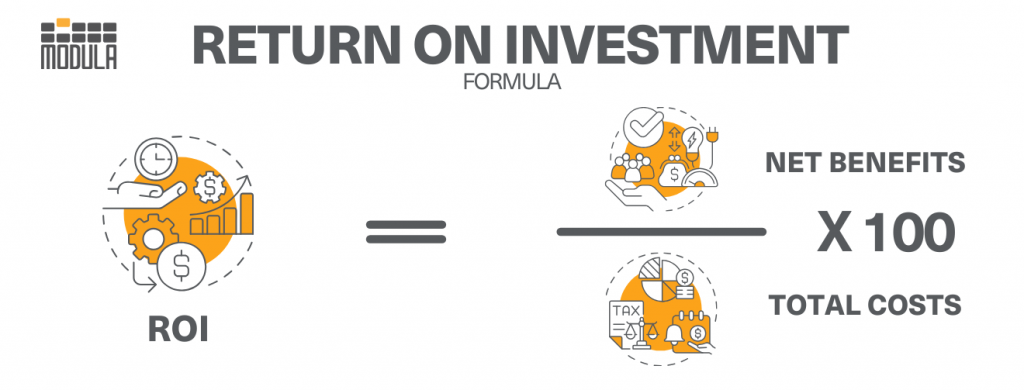
Assess the ROI Period
Determine how long it takes for the savings and gains to cover all initial costs. This timeline is crucial for understanding the cash flow impact and investment recovery period.
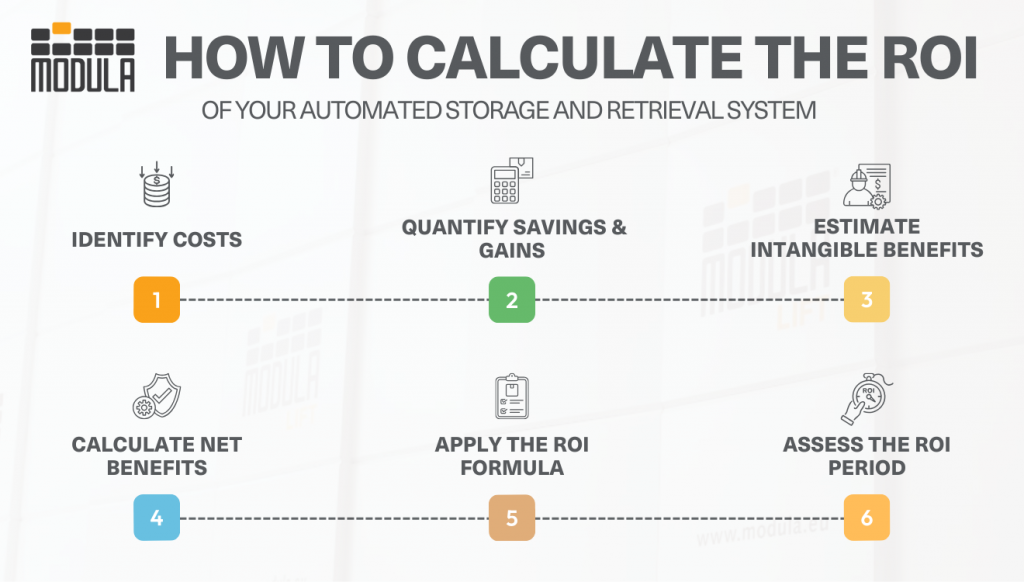
Maximize Your Investment With Modula Automated Storage and Retrieval Systems
At Modula, we revolutionize warehouse operations by optimizing space, enhancing accuracy and efficiency, and improving safety, among other benefits.
Our automated storage and retrieval systems include:
Modula Vertical Lift Modules (VLMs)
For warehouses with high ceilings, consider our Modula Vertical Lift Modules.
These smart storage solutions securely store large inventories and instantly retrieve items with a single click on the Copilot controller.
Choose from three options:
- Modula Lift: Designed for heavy loads and fast picking, Modula Lift is the ideal solution for storing industrial products, components, and spare parts across various industries and environments.
- Modula Slim: With twice the load capacity of standard vertical carousels and a compact footprint of just 32.29 square feet (3 square meters), Modula Slim optimizes space while improving storage and retrieval efficiency.
- Modula Next: Modula Next is an advanced solution that combines the space-saving efficiency of VLMs with the precision and control of industrial vending machines. Unlike conventional VLMs, its shuttering door system opens only the compartment containing the requested item, ensuring unmatched accuracy in picking and replenishment.
- Modula Pallet: The Modula Pallet is a cutting-edge warehouse solution that keeps pallet movements at ground level, maximizing vertical space while lowering the risks associated with lifting and high-level storage.
Modula Horizontal Carousel
If your warehouse or storage area has low ceilings, the Modula Horizontal Carousel is the ideal solution.
With a picking accuracy of up to 99% and speed of up to 550 lines per hour per employee, this system maximizes every inch of available space while boosting productivity and minimizing safety risks.
With flexibility in mind, Modula Horizontal Carousels seamlessly adapt to spaces with complex layouts or architectural constraints, such as irregularly shaped storage areas, mezzanines, or facilities with height limitations.
Many businesses achieve a quick return on their investment in automated storage and retrieval solutions, as the right material is delivered exactly where, when, and how it’s needed.
Each operation may see different variables influencing ROI, based on its starting point. Just reach out and we’ll be happy to provide an estimate of what you can expect.