Inventory Replenishment: How It Works & Best Practices
Inventory Replenishment: Key Points
- Inventory replenishment works by forecasting demand, setting reorder points and automatically generating purchase orders when inventory reaches predefined thresholds
- Automatic replenishment improves inventory efficiency by leveraging solutions like warehouse management systems to maintain optimal stock levels
- Best practices include tracking and adjusting lead times to prevent stockouts and ensure timely replenishment
Whether shopping online or in-store, consumers often face the frustration of out-of-stock items.
To avoid this, businesses are turning to advanced inventory replenishment systems which can reduce stockouts by up to 60%.
Inventory replenishment involves continuously monitoring stock levels, forecasting demand based on historical data and market trends, and automatically reordering products when inventory drops below a predefined threshold.
By leveraging technologies like warehouse management systems (WMS), companies can maintain optimal stock levels and streamline replenishment processes.
In this article, we will:
- Break down how automatic replenishment works
- Explain why inventory replenishment is essential in supply chain management
- Share best practices for keeping inventory under control
- Introduce Modula’s warehouse solutions designed to seamlessly integrate with your inventory replenishment system
How Auto-Replenishment Works
Auto replenishment, or automatic replenishment, is an inventory management process that monitors stock levels and automatically reorders items to maintain predetermined inventory thresholds.
Automatic replenishment leverages advanced algorithms and data analytics to optimize inventory management, which is essential in both fully automated and manual labor-intensive warehouses.
Auto-Replenishment in Manual or Traditional Warehouses:
In manual facilities, automatic replenishment acts as a smart support system that diminishes human error and improves stock visibility.
Here’s how it typically works:
- Data integration: The replenishment system integrates with the warehouse management system (WMS) to access real-time inventory levels and historical usage data.
- Threshold setting: Warehouse managers set minimum and maximum stock levels based on demand forecasts, seasonality, and lead times.
- Alerts and notifications: When inventory falls below the minimum threshold, the system automatically sends alerts to the warehouse or procurement team.
- Order generation: The system generates draft purchase orders for review and approval, ensuring accuracy before submission to suppliers.
- Restocking and verification: Upon delivery, warehouse staff manually restock shelves and confirm receipt in the system. The replenishment software then updates inventory levels and recalibrates reorder points as needed.
Auto-Replenishment in Automated Warehouses:
In contrast to manual environments, automated warehouses rely heavily on robotics, artificial intelligence (AI) and the Internet of Things (IoT).
This allows automatic replenishment systems to function with greater speed, accuracy, and minimal human intervention.
Here’s how the process works in a fully automated setting:
- Seamless integration: These systems are fully integrated with advanced warehouse management systems (WMS), enabling real-time communication between software and robotic hardware.
- Automated monitoring: Sensors and IoT devices continuously track inventory levels, eliminating the need for manual inventory inspections.
- Direct replenishment orders: When stock falls below preset thresholds, the system autonomously generates and sends replenishment orders to suppliers, eliminating the need for manual review or approval.
- Robotics and restocking: Automated guided vehicles (AGVs) or warehouse robots transport replenished items from receiving docks to their assigned storage locations, reducing downtime and maximizing throughput.
- Continuous optimization: AI-powered algorithms analyze replenishment data to fine-tune reorder points, quantities and delivery schedules, further improving supply chain responsiveness and decreasing waste.
Understanding Inventory Replenishment
Inventory replenishment is the process of restocking products to maintain optimal stock levels and ensure consistent availability.
It prevents stockouts, avoids overstocking, and keeps operations running smoothly by replacing items sold or used in production in a timely, efficient manner.
Replenishments can be manual, based on periodic reviews, or automated through systems that track inventory in real time and trigger reorders when thresholds are met.
SYSTEM TYPE | INVENTORY REPLENISHMENT | PROCUREMENT |
Focus | Maintaining stock levels in internal storage | Acquiring goods/services from external suppliers |
Objective | Keep the right quantity of items available for ongoing operations | Source the right products, at the right time and cost |
Scope | Ongoing restocking of existing SKUs | Selection, negotiation, and purchase of goods or services |
Trigger | Based on inventory thresholds, demand, or sales patterns | Based on production needs, contracts, or new product launches |
Tools Involved | WMS, ASRS, Replenishment rules | ERP, Supplier portals, RFQs, POs |
Example | Auto-ordering items when stock reaches minimum level | Sourcing a new supplier for custom packaging materials |
Why Inventory Replenishment Is Essential in Supply Chain Management
Inventory replenishment, also known as stock replenishment, ensures that the company orders items from suppliers in time to meet customer demand without collecting excess inventory.
It plays a crucial role in supply chain management by helping businesses maintain a balanced stock of goods to meet customer demand without overstocking.
When properly managed, replenishment delivers a range of operational and financial benefits:
Optimizes Inventory Levels
Effective replenishment helps maintain optimal inventory levels, minimizing the risks of both stockouts and overstocking. When you avoid excess inventory, your business can free up capital and improve cash flow.
Improves Customer Satisfaction
Ensuring availability of the right products when customers need them boosts satisfaction and fosters repeat business, while a consistent replenishment process builds trust and brand loyalty.
Increases Sales Opportunities
Stockouts can lead to missed sales, driving customers to competitors or causing them to delay purchases, harming both revenue and loyalty.
Keeping popular products in stock allows businesses to meet demand promptly and maximize revenue.
Reduces Holding Costs
Proper inventory control lowers carrying costs related to warehousing, insurance and potential spoilage — especially for perishable or seasonal goods.
Enhances Supply Chain Efficiency
Modern replenishment systems use automation and predictive analytics to forecast demand and manage restocking schedules. This diminishes manual labor, errors and delays across the supply chain.
Strengthens Supplier Relationships
Predictable and consistent replenishment orders improve supplier trust and can open opportunities for negotiating better pricing, payment terms or priority fulfillment.
Boosts Agility and Responsiveness
A responsive replenishment process allows businesses to adapt quickly to market shifts and emerging consumer trends.
Eliminates Emergency Purchases
Proactive replenishment planning helps avoid last-minute or emergency purchases, which often come with higher costs and can disrupt budget allocations.
Types of Inventory Replenishment Strategies
There’s no one-size-fits-all approach to inventory replenishment. The right strategy depends on your business model, product type, demand patterns, and warehouse operations. Below are the most common inventory replenishment methods and when to use them.
1. Fixed Order Quantity (FOQ)
This strategy triggers a replenishment order for a fixed quantity whenever inventory drops below a specific threshold (reorder point).
- Best for: Products with consistent demand and predictable usage rates.
- Example: A manufacturer reorders 500 units of a component every time stock drops to 1,000 units.
2. Fixed Order Interval (FOI)
Replenishment orders are placed at regular time intervals (e.g., weekly or monthly), regardless of stock levels.
- Best for: Low-value items or when coordinating regular supplier shipments is more efficient.
- Example: A retailer places a restocking order for office supplies every Friday, based on what was sold during the week.
Demand-Driven Replenishment
This method adjusts reorder quantities and timing based on real-time sales or production data.
- Best for: High-volume or fast-moving products with fluctuating demand.
- Example: An e-commerce company restocks trending products daily based on live order data.
3. Top-Off Replenishment
Instead of waiting for inventory to drop below a threshold, this strategy replenishes storage locations to their full capacity during downtime or between shifts.
- Best for: Fast-paced picking environments like distribution centers, to ensure high availability at picking stations.
- Example: During a slow period, the WMS schedules top-off replenishment to refill bins at picking zones to 100%.
4. Vendor-Managed Inventory (VMI)
The supplier monitors stock levels and initiates replenishment as needed, based on data shared by the customer.
- Best for: Long-term supplier partnerships with high trust and integration.
- Example: A food distributor shares real-time inventory data with its beverage supplier, who handles restocking without customer input.
5. Just-in-Time (JIT) Replenishment
Minimizes on-hand inventory by scheduling deliveries to arrive exactly when needed for production or fulfillment.
- Best for: Lean operations where inventory holding costs are high.
- Example: A manufacturer receives parts hours before they’re needed on the assembly line.
Choosing the right replenishment strategy, or a combination of them, can significantly improve efficiency, reduce carrying costs, and support service level goals.
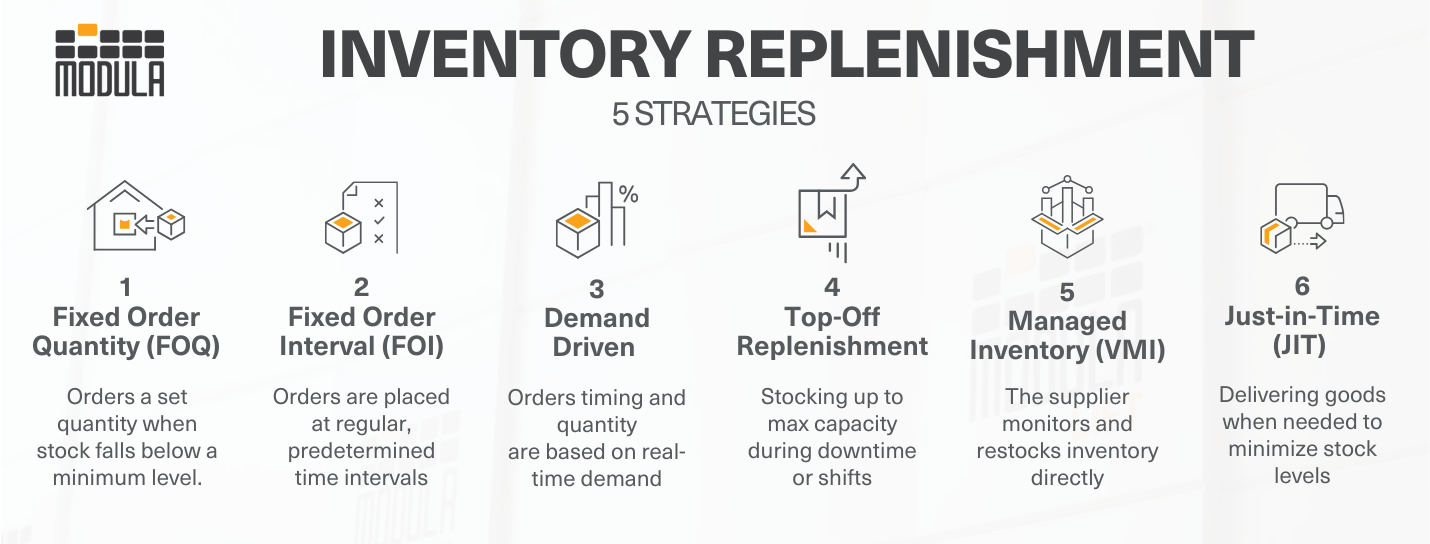
6 Common Challenges in Stock Replenishment
Warehouse management frequently involves numerous obstacles, especially when it comes to stock replenishment.
Even with a well-defined strategy in place, issues such as overstocking, markdowns and stockouts can still occur.
These setbacks not only damage a company’s reputation but can also result in significant financial losses due to emergency restocking, lost sales or excess holding costs.
Overstocking and Markdowns
Excessive stock often leads to unexpected price reductions, as surplus inventory binds capital and increases the likelihood of items becoming obsolete.
To clear space and recover investments, businesses might be forced to discount unsold items, potentially damaging their brand reputation and incurring significant financial losses.
Out-of-Stock Scenarios
Even with a solid replenishment strategy, stock shortages can still occur. Such interruptions could erode customer confidence and harm a company’s standing.
Fluctuating Forecasts
Demand forecasts are usually uncertain and often influenced by shifting customer preferences because different factors can influence consumer behavior, including economic conditions, seasonal trends, marketing campaigns and emerging social influences.
These fluctuations can lead to inaccurate inventory orders and misaligned management strategies.
Supplier Delays
Delays from suppliers can interrupt delivery timelines, affecting production schedules and downstream operations.
Warehouse Space Limitations
Poorly optimized warehouse layouts or limited storage capacity can complicate inventory management and increase storage costs significantly, as they restrict the efficient movement and placement of goods.
Lack of End-to-End Visibility
When suppliers or internal teams don’t have access to real-time inventory data, replenishment actions may be delayed or misaligned. This lack of visibility can weaken coordination and lower customer service levels.
Inventory Replenishment Best Practices
Optimizing replenishment is essential for meeting customer demand, minimizing costs, and avoiding inventory pitfalls. While the process can be complex, the following best practices provide a strong foundation for improvement:
Identifying Accurate Lead Time
Accurately determining lead times is crucial to avoiding stockouts.
Lead time, or the duration between placing an order and receiving inventory from a supplier, must be consistently monitored and updated to ensure timely replenishment and decrease inventory gaps.
Inter-store Replenishment
Transferring inventory between retail locations can help balance stock levels and reduce costs. This involves relocating products from stores with surplus stock to those experiencing higher demand.
Inter-store transfers free up space and improve product availability, provided there’s a centralized inventory management system in place.
Performing ABC Analysis
Using ABC analysis allows businesses to categorize SKUs based on their sales impact, usually dividing items into “A” (high value), “B” (moderate value), and “C” (low value) groups.
This prioritization streamlines replenishment decisions and supports more strategic inventory allocation.
While effective, it can be resource-intensive for businesses managing large product catalogs since analyzing and categorizing several products requires significant time and effort.
Monitoring Vendor Performance
Timely deliveries are critical to maintaining effective replenishment cycles. Regularly evaluating vendor performance helps ensure reliability and continuity in supply.
Setting critical performance metrics is vital for evaluating supplier effectiveness. Key metrics to track include lead times, frequency of late deliveries and instances of incomplete or missing inventory.
Utilizing an Inventory Management System
Using a unified inventory management platform improves replenishment strategy execution.
While small retailers can rely on spreadsheets for manual tracking, this approach becomes inefficient, as operations scale across multiple locations, sales channels or SKUs.
For omnichannel retailers and large-scale warehouses, advanced inventory software is essential.
These platforms provide real-time visibility, identify bottlenecks and enable rapid adjustments to replenishment plans, helping businesses remain agile and aligned with operational goals.
Integrate Your Inventory Replenishment Software With Other Warehouse Solutions
Automated supply replenishment systems are not standalone solutions. They are also integral components of a broader warehouse and inventory management ecosystem.
Their effectiveness increases substantially when they are integrated with complementary warehouse solutions, tailored to meet specific business needs and designed to scale alongside organizational growth.
Additionally, it’s essential to consider their financial impact to ensure a positive return on investment.
For best results, automated replenishment systems should be seamlessly incorporated with existing warehouse and business management tools, such as:
- Warehouse management systems (WMS): These provide real-time inventory levels and insights, enabling precise replenishment triggers based on actual stock requirements.
- Enterprise resource planning (ERP) systems: Integration with ERP systems ensures that financial data, order management, and supply chain operations are synchronized, facilitating a holistic approach to inventory management.
- Customer relationship management (CRM) systems: Analyzing customer purchasing patterns and preferences from CRM data informs replenishment strategies and timing, enhancing customer satisfaction.
By creating a connected environment, businesses can align replenishment processes with broader operational goals—improving both responsiveness and return on investment.
How WMS and ASRS Enhance Warehouse Efficiency and Inventory Control
Warehouse management systems (WMS) and automated storage and retrieval systems (ASRS) are essential tools for optimizing inventory control and improving overall warehouse performance.
When integrated, they create a streamlined, data-driven environment that supports accurate replenishment and responsive operations.
WMS: Real-Time Visibility and Smarter Inventory Control
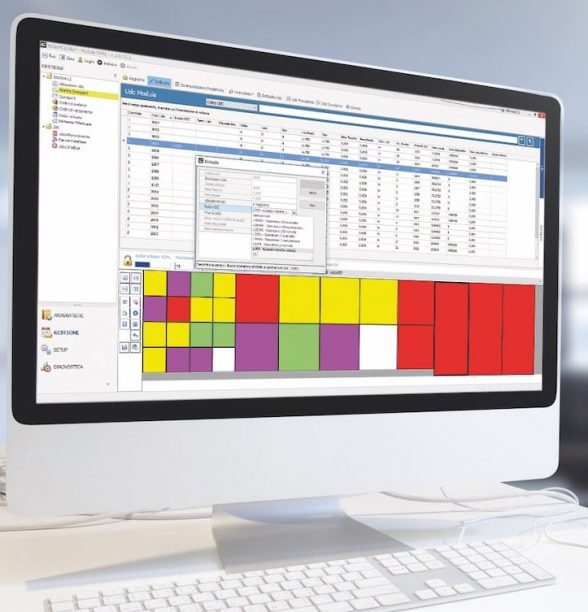
A WMS acts as the central intelligence of warehouse operations.
- It continuously monitors inventory in real time, tracking stock levels, locations, and movements through barcode scanners or RFID systems.
- This level of visibility enables businesses to forecast demand more accurately, define precise reorder points, and maintain optimal stock levels.
- Modula’s Warehouse Management System (WMS) supports advanced replenishment logic, including minimum/maximum levels and dynamic prioritization based on SKU performance.
- It identifies slow-moving or obsolete items that might otherwise take up valuable space or tie up capital.
ASRS: Maximizing Space and Accelerating Throughput
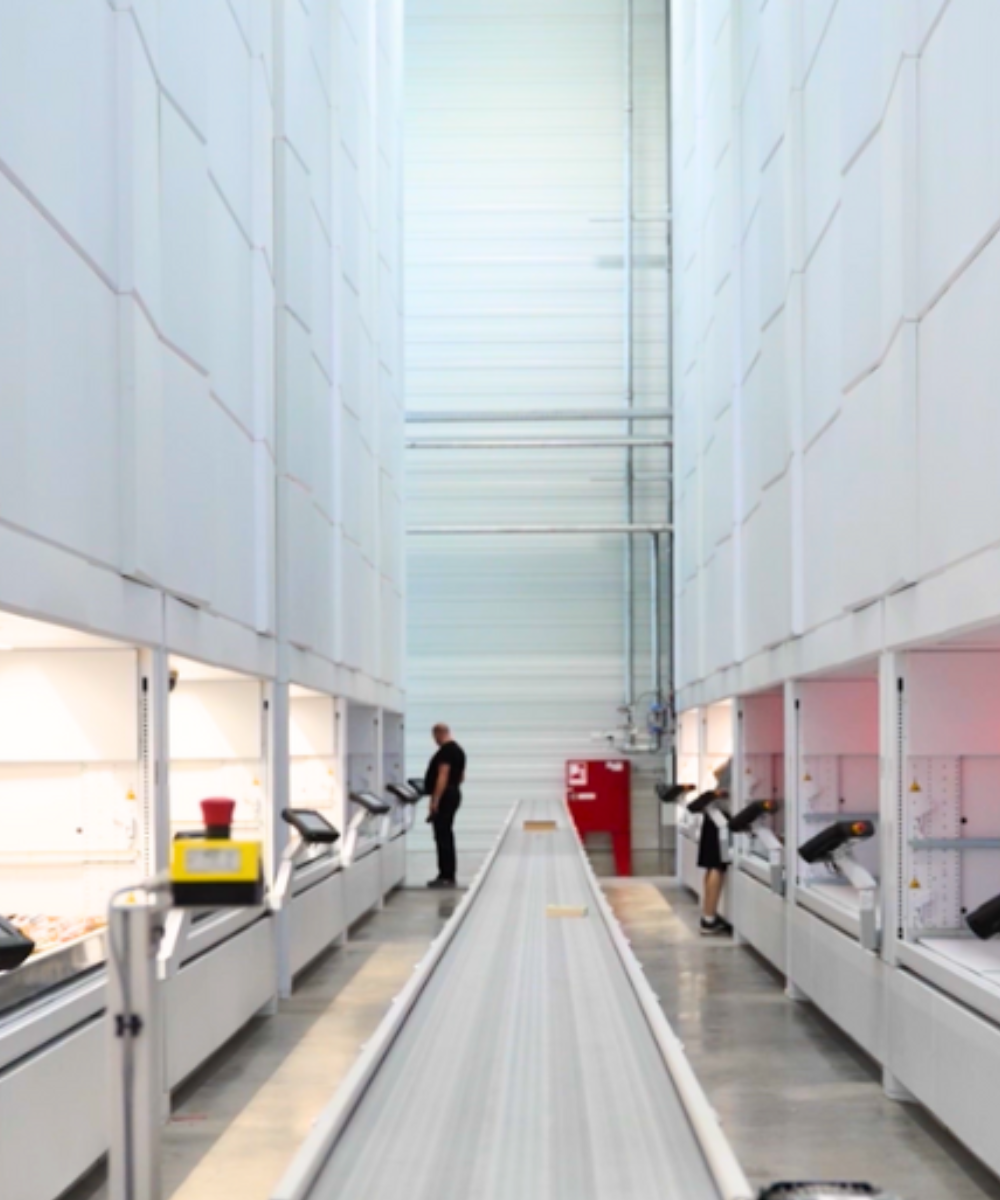
ASRS, such as Modula’s vertical lift modules or horizontal carousels, store goods in high-density, space-saving configurations.
- They reduce the need for wide aisles and manual access, allowing warehouses to recover up to 90% of floor space.
- Items are automatically retrieved and delivered directly to the operator, eliminating the time spent walking, searching, or climbing to reach products.
- ASRS supports faster replenishment by streamlining the restocking process and minimizing manual handling.
WMS and ASRS: A Seamless Replenishment Workflow
When integrated, WMS and ASRS technologies work in unison to automate and synchronize warehouse activities.
The WMS analyzes product usage and demand history to assign ideal storage locations, while the ASRS physically handles placement and retrieval.
As stock is consumed, the WMS updates inventory counts in real time and automatically triggers replenishment.
The ASRS then prepares and delivers the required trays or pallets directly to the operator, streamlining the process and minimizing downtime.
The Modula Advantage
Modula’s full portfolio of ASRS solutions, combined with its proprietary WMS software, offers a complete, scalable ecosystem for warehouse automation.
Whether you’re managing small parts, large goods, pallets, or high-speed e-commerce operations, Modula’s integrated solutions improve storage density, reduce picking times, and enhance replenishment control.
From real-time visibility to intelligent automation, Modula enables businesses to take full control of their inventory and operate with greater agility.
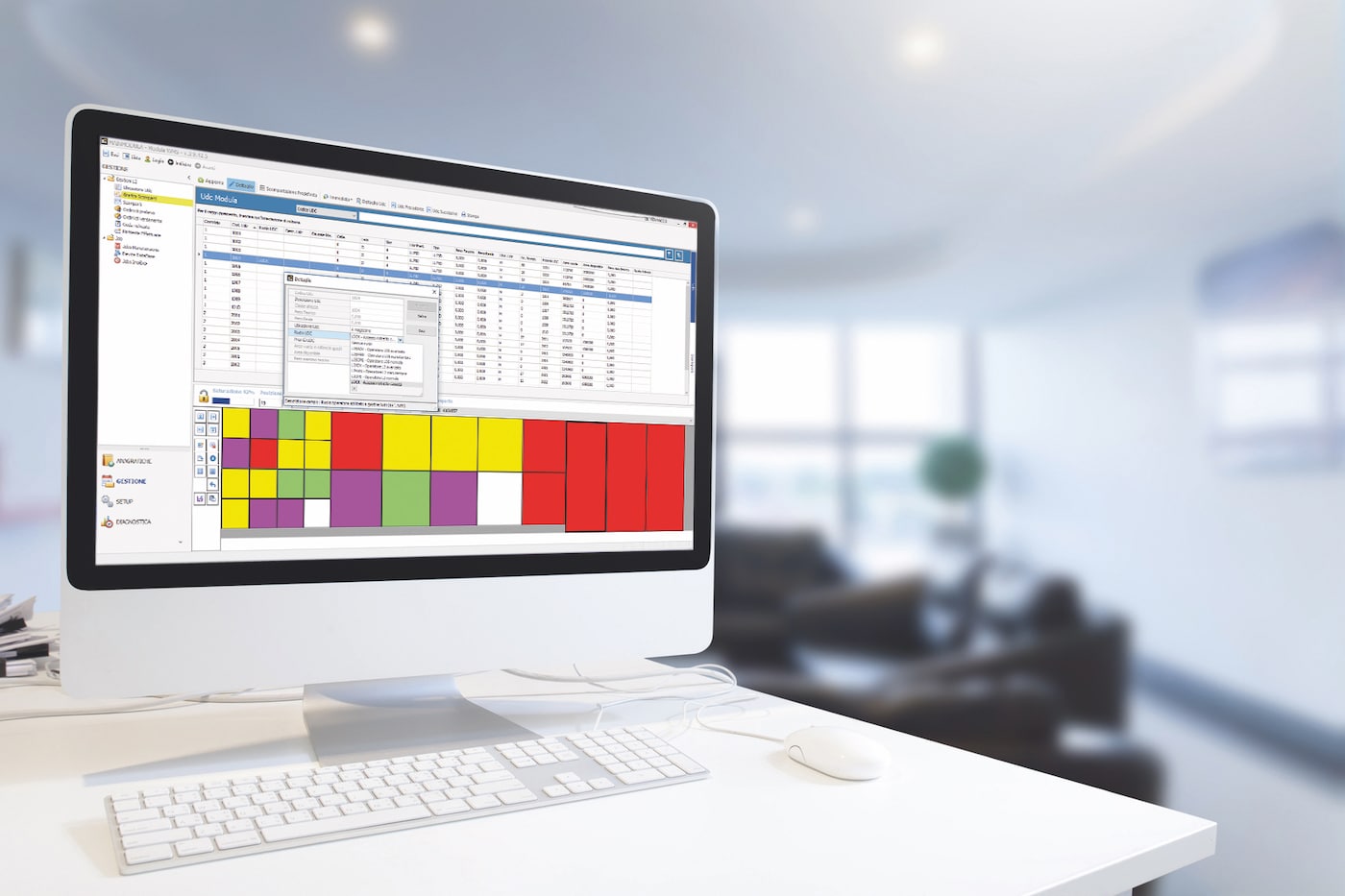
Discover More About Modula’s WMS & ASRS Solutions
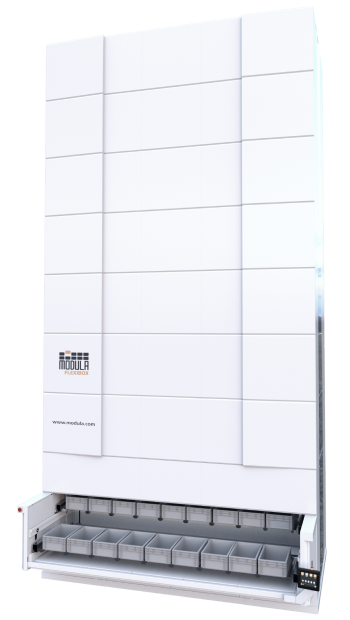