Automated Storage Systems for Agricultural Equipment Dealerships
In 2020, the COVID-19 pandemic significantly impacted the agriculture sector across the globe, creating unprecedented challenges in food production and supply chains.
These challenges have emphasized the need for resilience and efficiency in agricultural practices, especially in managing the intricate parts and inventory essential for day-to-day operations.
With the global population steadily growing and arable land becoming increasingly scarce, the demand for food continues to rise. Consequently, there’s a pressing need for agricultural operations to enhance productivity and efficiency to meet this increasing demand.
A key issue that has emerged is the frequent mishandling and mispicking of agricultural parts, leading to operational delays and inefficiencies.
This is where automated agricultural storage solutions come in as an invaluable tool for agricultural manufacturers, suppliers and dealers. These systems streamline inventory management processes, improving efficiency and accuracy while mitigating operational hurdles.
In this blog, we’ll share the top challenges that agricultural companies face and why they are switching to automated warehouse solutions. We’ll also introduce you to the automated solutions that can help — including our Vertical Lift Modules and Warehouse Management System at Modula.
Why are Agricultural Equipment Dealerships Adopting Automated Vertical Storage Solutions in their Parts and Service Department?
Progressive American agricultural manufacturers, suppliers and dealers can meet consumer demands by expanding storage capacities, reducing inefficiencies and improving materials handling speed and responsiveness.
By doing so, they can enhance productivity and protect profits. If not, they will risk losing their competitive advantages and in turn, their customers.
One of the key areas in which these inefficiencies are evident is in outdated agricultural parts storage operations.
A sizable number of organizations dealing with agricultural equipment use the traditional method of storing parts on warehouse storage racks, such as static shelves in warehouses.
Traditional methods of storage rely on manual processes. For example, the parts must be gathered for shipment by workers who travel around the warehouse, grab the needed parts and then ship them.
These manual processes are inherently inefficient and potentially harmful, as workers waste time navigating aisles in a warehouse. In addition, workers can strain their bodies when they reach high areas or stoop down to retrieve parts.
Challenges of Agricultural Parts Management
Managing agricultural parts often comes with challenges, which can significantly impact the efficiency and reliability of your operations.
Common challenges of agricultural parts management include:
Seasonal Demands and Operational Strain
The seasonal nature of agricultural operations intensifies the urgency of efficient parts management. During peak periods like planting and harvesting seasons, the demand for equipment repairs and maintenance surges, straining dealership resources.
According to a 2023 report by the Association of Equipment Manufacturers (AEM), agricultural equipment sales typically peak in the spring and fall, leading to increased service and parts demands during these times.
To meet seasonal demands and prevent operational strain:
- Utilize historical data to predict peak demand periods and plan inventory accordingly
- Implement just-in-time inventory management and use software for better tracking
- Streamline workflows, adopt lean principles and invest in technology for better service
Tracking Inventory
From blades to nuts and bolts, agricultural parts are often diverse, encompassing a broad spectrum of items with various weights and sizes.
For example, according to a 2022 survey conducted by Farm Equipment Magazine, over 60% of agricultural equipment dealerships report difficulties in accurately tracking and managing their parts inventory due to the sheer volume and variety of items.
Due to the different parts, keeping an accurate and updated inventory is key, which requires a reliable system for tracking each item.
To track your agricultural parts in real-time:
- Conduct regular physical stock checks — either monthly or quarterly — and compare these counts with your system records
- Use a warehouse management system (WMS) to obtain real-time updates on inventory levels, movement and location
- Equip your inventory items with barcode or RFID tags and use scanners to accurately track the movement of each item
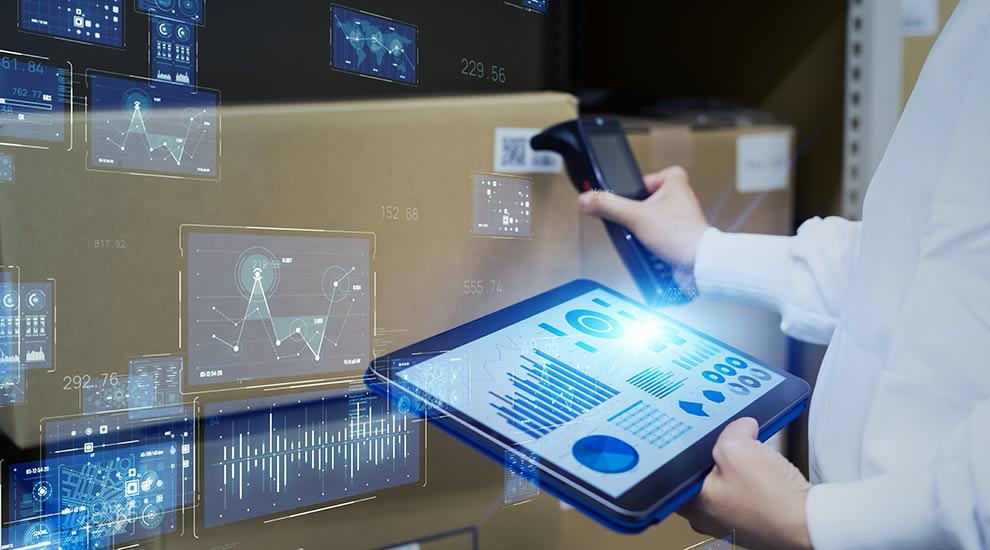
Manual Processes and Inefficiencies
Farmers depend on being out in their fields — especially during planting and harvesting periods in which every hour is critical. Any issue that disrupts their plans such as a broken vehicle or blade, can be costly.
Picking an incorrect part can delay repairs, as the wrong part is returned and a new one is sent out.
Mispicks can also damage the reputation of the agricultural dealer on which the farmer depends to stay productive when it matters most.
Traditional warehouses increase this risk due to their inefficiencies and manual processes in which tracking inventory is cumbersome. Even with diligent manual tracking, counts are completed periodically instead of continuously.
Take for example a warehouse manager who doesn’t have real-time insights into stock levels. If the inventory has been taken at 9 a.m., the warehouse manager might not know at 3 p.m. if a part is still in stock or not.
In addition, relying on humans to both retrieve items and report on the status of a given item is prone to errors at best.
In peak seasons when parts orders for repairs are coming in with urgency, the organization that can respond quickly and efficiently wins. The one that stumbles along and causes delays eventually pays the price.
To prevent mispicks:
- Regularly train warehouse staff on proper picking procedures and the use of any related technology
- Consider adopting voice picking technology, in which employees receive verbal instructions through a headset, allowing them to keep their eyes and hands free on accurate picking
- Implement a WMS to gain a comprehensive view of your inventory
Skilled Labor Shortage
Attracting and retaining skilled technicians for equipment maintenance and repair is becoming increasingly challenging for agricultural dealerships. This shortage can significantly impact equipment uptime and customer satisfaction.
Equipment maintenance and repair often require specialized skills and knowledge due to the complexity of modern farming machinery and technology.
In addition, the perception of the agricultural industry as outdated or less glamorous compared to other sectors may deter skilled workers from pursuing careers in agriculture.
To attract skilled labor:
- Invest in automated storage and retrieval systems (AS/RS) and robotics to automate repetitive tasks and optimize warehouse operations, reducing the reliance on manual labor
- Implement inventory management software integrated with AS/RS technology to streamline inventory tracking, replenishment and order fulfillment processes
- Provide training programs to educate employees on operating and maintaining automated warehouse solutions, empowering them to leverage technology effectively and enhance productivity
Compliance and Environment Sustainability
Agricultural companies face the dual challenge of ensuring product traceability and compliance with food safety regulations, while also addressing environmental sustainability concerns.
Consumers and regulators demand transparency in the journey of agricultural products from farm to table, requiring robust systems for tracking and reporting.
This traceability must be managed alongside efforts to reduce the environmental impact of material handling and storage operations, such as minimizing waste, conserving resources and implementing sustainable practices.
To comply with regulations and become more sustainable:
- Implement vertical storage solutions to maximize warehouse space, reduce energy consumption and enhance product traceability
- Use software to automate inventory tracking, ensuring accuracy in product location, quantity and movement for better compliance and traceability
- Adopt automated picking solutions to improve handling efficiency and reduce product damage
- Choose storage systems that are designed to minimize electricity usage, supporting environmental sustainability initiatives
- Utilize warehouse automation to further support sustainability. For example, Modula’s VLMs and HCs only use energy when the warehouse operator activates the modules. When the VLMs and HCs aren’t being used, they remain dormant, consuming minimal electricity.
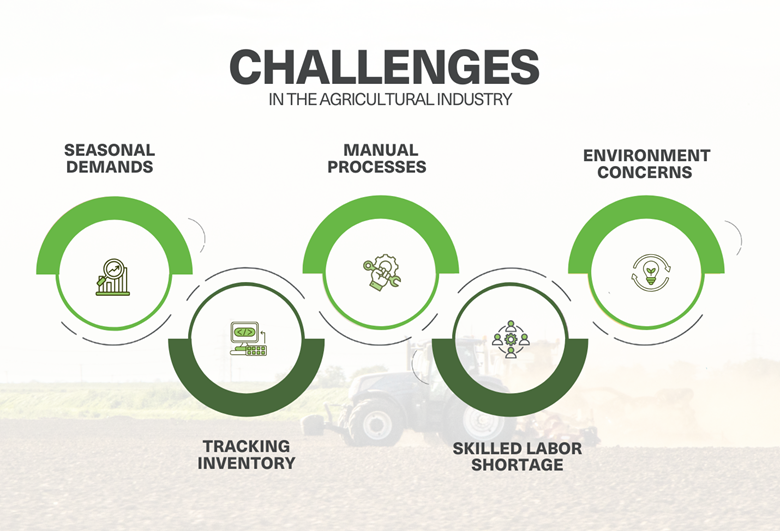
Benefits of Modula Vertical Lift Modules as Agricultural Storage Systems
One solution to address these challenges? Automated storage and retrieval systems or computer-controlled systems that can efficiently store and retrieve goods.
At Modula, we provide automated storage solutions and retrieval systems to help further optimize your agricultural parts storage with advanced storage systems like Modula Vertical Lift Modules (VLMs).
With the reduced footprint of a VLM compared to traditional warehouse shelving systems, agricultural parts and servicing dealerships can cut down on needed floor space by up to 90%.
Easy-to-use touchscreens allow your operators to enter the item that needs to be retrieved. Like a giant vending machine, the VLM delivers it at an ergonomic height that protects your workers from injury.
It takes less than 30 seconds to bring the part to the worker. And with picking aids such as pick-to-light and laser-guided pointers, pickers can retrieve the proper agricultural part with accuracy and faster throughput.
When combined with a WMS that automatically tracks inventory and optimizes logistics, a VLM greatly enhances productivity and accuracy, improves performance and helps agricultural parts departments prevent overbuying or underbuying parts.
By using a VLM, you take a major step towards improving efficiency and properly tracking the flow of parts. A VLM can store all the items that are typically found in an agricultural dealership used to maintain tractors, harvesters and the like.
It doesn’t matter where the parts are stored —the machine retrieves the proper internal tray and delivers it to the operator quickly and accurately.
Parts that are commonly ordered together can be placed near each other in the same tray in the VLM, further increasing productivity.
When a warehouse worker enters the names or numbers of the SKU, the VLM retrieves the internal tray storing the items, delivers it to the worker and then guides the worker to retrieve them from the appropriate compartment using laser pointers and LED indicator systems.
This ensures accurate picks, not the mispicks that are common with manual systems.
The critical task of inventory tracking is managed by connecting the VLM to the WMS. This combination means that your warehouse manager can track the status of all parts in your facility.
Any time a part is removed from the VLM or replenished — the system records that activity. As a result, you don’t need to worry about replenishing stock with too many parts, failing to order those that are too low or replacing depleted inventory.
Modula Vertical Lift Modules as Safe and Productive Agricultural Storage Systems
VLMs can help your workers avoid the stress and strains associated with day-to-day work. Parts are often stacked high above shelves or near the floor, and pulling from their places all day can wear down workers.
With a vertical lift module, your warehouse operator automatically receives the part.
This simplified workflow of not having to perform regular inventory inspections and remembering to indicate when a part has been removed or restocked, significantly reduces the mental strain on workers while increasing productivity.
With these benefits, agricultural dealerships can avoid the high turnover rates that are common in the industry.
Find out how Modula helped the agricultural industry, with over 170 installations of warehouse automation across different businesses.
A Quick Recap on Vertical Lift Modules for Agricultural Storage Systems
If you have an agricultural equipment dealership, you know the important role you play in providing a continuous food supply to the world. Your business must operate at peak efficiency to stay competitive, while making sure your employees feel safe and secure in their workplace.
At Modula, we can help the operations of your agricultural equipment dealerships with our advanced automated storage and retrieval systems and warehouse management system.
Contact our team for a warehouse audit and explore how our innovative solutions can be tailored to meet your specific needs.