Warehouse Operations 101: Processes & Best Practices
A recent survey found that in 2023, issues with orders or deliveries were one of the top reasons people worldwide contacted customer service.
Winning customers and meeting their expectations starts with having seamless warehouse operations.
In this article, we’ll explain everything about warehouse operations, including its processes, best practices and more. We’ll also show you how Modula’s automated solutions can optimize your processes and boost overall customer satisfaction.
What Are Warehouse Operations?
Warehouse operations encompass different processes that streamline the flow of goods in and out of a facility.
The goal of warehouse operations is to efficiently meet customer needs using space, equipment and labor. In addition, ensuring goods are safe and accessible requires ongoing planning and changes.
Warehouse operations include activities such as receiving inventory, organizing and storing goods, picking and packing orders and managing inventory and shipping.
7 Key Warehouse Processes
To improve your warehouse operations, you need to understand the tasks, activities and processes you’re overseeing.
Here are the key warehouse processes and procedures:
Receiving
Your warehouse employee receives the goods from suppliers. They check the items for damage, quantity and accuracy against the delivery documentation, using a warehouse management system.
Storing
After receiving the inventory, your warehouse employee moves them to their designated storage location with the help of a conveyor or forklift.
Your team can use storage strategies that consider the size, weight and frequency of access for each item to optimize space and efficiency.
For example, they can place category A products, or frequently picked inventory, in easily accessible areas near the warehouse’s front to speed up the picking process.
On the other hand, they can store bulky or heavier items on lower shelves to improve safety and reduce handling time.
Order Processing
After placing an order, your employee checks it for accuracy and confirms whether the item is in stock. They also update inventory levels, process payments and create shipping labels or packing slips.
To optimize this step, consider using a warehouse management system for real-time inventory visibility.
Picking
After receiving orders, your team can start picking items. While picking seems like a straightforward task of taking goods from their storage areas, it’s a key step to prevent costly returns, unhappy customers and lost revenue.
Automated picking solutions can significantly enhance accuracy, improving warehouse efficiency.
Innovations can range from simple barcode readers to advanced aids like pick displays, LED bars and laser pointers, boosting picking accuracy to up to 99%.
Packing
Your warehouse employee then securely places the items in a box or poly mailer, adds any necessary packing materials and attaches the shipping label.
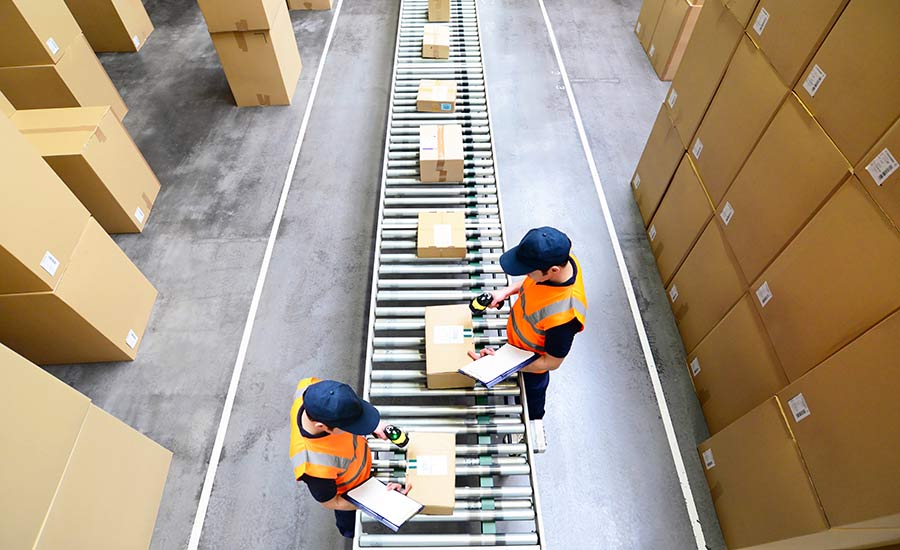
Shipping
Using a trolley, forklift or a warehouse robot, your warehouse operator transports packages to the shipping area for consolidation.
Next, they sort packages by carrier type and destination, assigning each shipment to a courier service, USPS or a freight forwarder.
Sending tracking updates after shipping an order is essential for keeping customers informed about the status of their shipment and expected delivery dates.
Finally, your warehouse operator prepares the shipment for delivery. This includes labeling, loading onto delivery trucks and updating the inventory system to reflect the outbound goods.
Returns Processing
The returns process in warehouse operations involves handling goods customers or suppliers return due to defects or incorrect orders. This process includes:
- Receiving: Your warehouse employee receives and checks the returned goods for damage, completeness and accuracy, documenting any discrepancies or issues and reporting them to the relevant department or team.
- Inspecting: Your warehouse employee inspects the returned goods to assess their condition and decide if they can be resold, repaired or discarded, possibly testing the goods or inspecting their packaging.
- Classifying: Your warehouse employee categorizes the returned goods based on their condition and intended disposition into groups like “resalable,” “repairable” and “scrap”.
- Processing: According to their classification, the returned goods undergo processing, which can include restocking for resale, repairing, refurbishing or environmentally responsible disposal.
- Record keeping: Your warehouse employee maintains detailed records of the returns process, taking note of information about the returned goods, reasons for product returns and the item’s overall condition and quality.
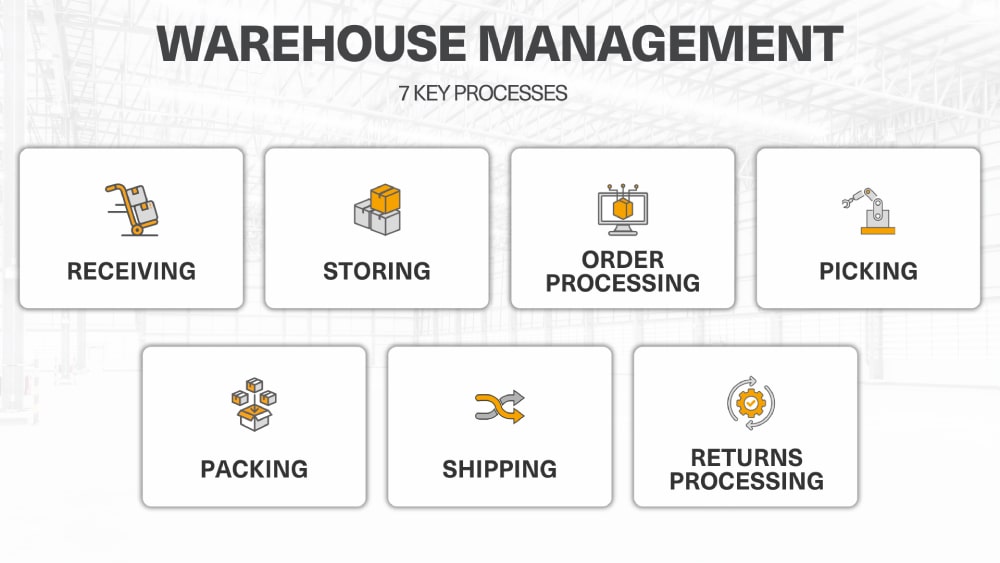
Warehouse Operations Best Practices
Implementing best practices in warehouse operations can significantly enhance efficiency, safety and customer satisfaction.
Here are some key strategies:
Strategically Design Your Warehouse
An efficient warehouse layout can make the most of your available space while boosting productivity.
Consider factors like inventory flow, SKUs being stored, material handling paths and the accessibility of high-demand items to minimize movement and processing time.
To optimize your warehouse layout:
- Use adjustable shelving and modular storage units that you can reconfigure as inventory needs change
- Design your warehouse layout to support a logical flow of inventory, from receiving to shipping, reducing unnecessary handling and movement. For example, position high-demand items closer to packing and shipping areas to speed up retrieval and reduce processing time
- Organize inventory based on seasonal shifts, keeping similar items together and prioritizing placement based on demand and turnover rates. For example, store winter gear at the front of the warehouse during colder months and switch to summer must-haves as temperatures rise, ensuring that seasonal products are always accessible.
Zone Your Inventory
Storing items in dedicated zones significantly boosts warehouse efficiency by cutting down travel time and movement. Your employees can store or retrieve inventory in just one trip per zone, instead of moving across multiple locations inside the warehouse.
To zone your inventory:
- Group your inventory into categories based on type, size or demand
- Utilize signs and labels to mark each zone, making it easy for employees to find and store items
- Periodically evaluate the effectiveness of your zoning layout and make adjustments based on changing inventory needs or sales patterns
Optimize Your Existing Space
Maximize storage capacity and efficiency by utilizing your facility’s current vertical and horizontal space.
Installing taller storage units and investing in equipment that can reach high shelves can dramatically increase your warehouse’s storage potential without expanding its footprint.
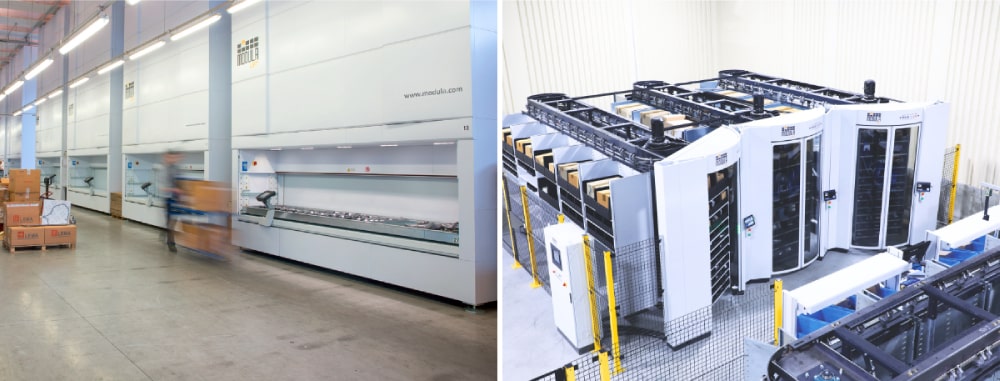
At Modula, our Vertical Lift Modules (VLMs) can help further streamline your warehouse operations by
utilizing the vertical height of your warehouse and automating the storage and retrieval process.
Save up to 90% of floor space over traditional warehouse storage racks, freeing up space for future expansion.
If you have limited ceiling height, our Horizontal Carousels (HCs) are the ideal storage solutions for high-speed picking in warehouses with low ceilings.
The best part? You can get a return on your investment in just six to 18 months.
Streamline Your Returns Process
Optimizing your returns process plays a key role in enhancing customer satisfaction and encouraging repeat business.
To streamline your returns process:
- Make your return policies clear and easy to understand for customers. For example, outline the steps they need to follow to initiate a return, specify the timeframe within which returns are accepted and list the types of products that they can or can’t return.
- Offer clear information on return receipt and refund processing to enhance transparency and increase customer satisfaction.
- Review return policies at least once a year to identify product issues or customer trends, and use this information to improve product quality and customer satisfaction
Utilize the Right Warehouse Equipment
Invest in the right tools and equipment for your operational needs. Whether it’s forklifts or advanced picking systems, the proper equipment can achieve accuracy and boost productivity and safety in your warehouse.
To choose the right warehouse equipment:
- Clearly identify what tasks need automation or improvement in your warehouse operations. Consider factors like inventory size, item weight and storage requirements.
- Choose equipment that integrates with your warehouse management system (WMS) for streamlined operations, real-time tracking and inventory management.
- Calculate the return on investment (ROI) of each equipment option by comparing its cost against the efficiency and productivity gains it offers.
- Consider scalability and flexibility in your equipment choices to accommodate future business growth and changes in operations.
- Arrange for a demo or trial period to test the equipment’s functionality and compatibility with your warehouse operations before making a final decision.
Gain Complete Visibility into Your Inventory
Make sure your inventory records match what’s in stock to avoid expensive mistakes like having too much or too little inventory.
To get a bird’s-eye view of your inventory:
- Schedule and perform physical counts of your inventory — at least once every two months — to verify its accuracy against your records.
- Analyze historical sales data, market trends and seasonal fluctuations to anticipate future demand patterns to proactively adjust inventory levels, minimize stockouts and avoid excess inventory costs.
- Use a warehouse management system to update your inventory levels in real-time as items are received, sold or returned.
Modula’s Warehouse Management System (WMS) is a comprehensive inventory management software. It’s designed to work with Modula’s automated storage solutions or by itself in traditional, manual warehouses.
Thanks to it, you can track and manage each item by its records, unique IDs and stock levels. You can also monitor the location and movement of products in your warehouse by setting up location codes and labels.
The Modula WMS is one of the most user-friendly and sophisticated software solutions on the market. It can be connected with almost all DMS and ERP systems to enhance processes like receiving, storing, and picking.
Prioritize Warehouse Safety
Implementing safety protocols and OSHA standards in your warehouse is essential, as it can help protect your employees from injuries, reduces the risk of accidents and ensures a smooth flow of operations.
To ensure your warehouse is safe:
- Provide hands-on training for all employees on safety practices, equipment handling and emergency procedures.
- Require your warehouse operators to use appropriate personal protective equipment (PPE) when working.
- Make sure your warehouse equipment is in optimal working condition by conducting maintenance routines, as faulty equipment can compromise safety.
Perform Warehouse Inspections
Keeping tabs on how your warehouse operations are running can help your business maintain efficiency, optimize inventory management and meet customer demands promptly.
To efficiently conduct a warehouse inspection:
- Set a routine schedule for inspections to ensure consistent operational standards
- Prepare a warehouse safety checklist that covers all areas, including equipment, aisles, emergency exits and storage practices
- Check in with your employees and seek their feedback on potential safety issues and operational improvements
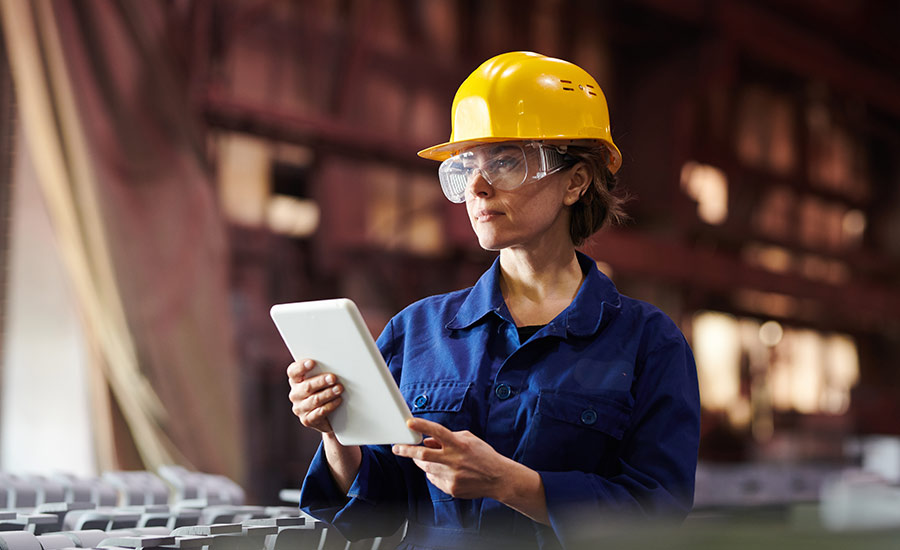
Track Your Warehouse KPIs
Monitoring your warehouse’s key performance indicators (KPIs) can help you identify areas for improvement, make informed decisions to boost productivity, reduce costs and optimize overall warehouse operations.
To track your warehouse KPIs:
- Determine which KPIs are most relevant to your warehouse operations, such as order accuracy, inventory turnover and shipping times.
- Establish performance benchmarks for each KPI to gauge your warehouse’s efficiency and identify areas for improvement.
- Schedule weekly or monthly reviews of your KPI data to monitor performance trends and make necessary adjustments.
Hire a Knowledgeable Warehouse Manager
Employing an expert to manage your warehouse operations allows you to enhance efficiency, reduce operational costs, oversee safety standards and improve team productivity, ultimately boosting overall performance.
Streamline Your Warehouse Operations with Modula Solutions
At Modula, we provide smart, cutting-edge automation to make your warehouse operations better. Reach out to us to see how our tech can be customized for you.
Our team is here to offer tailored advice and solutions for your warehouse needs.
A Quick Recap on Warehouse Operations
Understanding warehouse operations can help your business operate at peak efficiency and reduce disruptive issues, such as inventory inaccuracies, order processing delays, space utilization problems and higher operational costs.
By implementing warehouse technology and following best practices, your business can excel in managing warehouse operations and improving your bottom line.