101 Guide to MRO Inventory Management
Maintaining an adequate stock of maintenance, repair and operations (MRO) inventory in your facility can help you quickly repair warehouse equipment, reduce costly downtime and make sure your production lines are continuously operating.
We’ll explain all you need to know about MRO inventory management, from its challenges to best practices, and share our advanced storage solutions and sophisticated warehouse management system at Modula.
What Is MRO Inventory Management?
Maintenance, repair and operations (MRO) inventory management is the process of purchasing, storing and replenishing this inventory in the most cost-efficient way.
MRO inventory typically includes a wide range of products and materials across various industries. Each industry has its specific needs, but generally, MRO products are used to maintain equipment and ensure operational efficiency.
Effective MRO inventory management can help ensure you have adequate stock on hand for asset maintenance while minimizing costs.
How Does MRO Inventory Management Work?
Here’s an overview of the ins and outs of effectively managing your MRO inventory:
- Planning and forecasting: Forecast your MRO inventory based on historical data and current trends to help you understand which supplies are required and their quantity.
- Procurement: Begin selecting suppliers, negotiating prices and placing orders to help you get the best quality items at the most affordable prices. For example, you can choose a supplier who offers discounts when you purchase bulk, allowing you to save money on large orders.
- Receiving and inspecting: Check the inventory’s quality and quantity to ensure they meet your standards and order requirements.
- Storing and managing: Organize and manage your MRO inventory to ensure easy access, efficient tracking and optimal use of storage space. In addition, this stage includes categorizing items and arranging them for easy access.
- Auditing and replenishing: Audit your MRO inventory every month or quarter to check your stock against your inventory records and actual needs. This will help you maintain accurate inventory records and replenish your inventory to align with the current usage trends and projected demands.
- Reviewing and optimizing: Analyze the efficiency of your MRO inventory management to identify areas for improvement and better cost saving opportunities. Assess factors such as procurement costs, supplier costs, performance and inventory turnover or the rate at which your stock is sold.
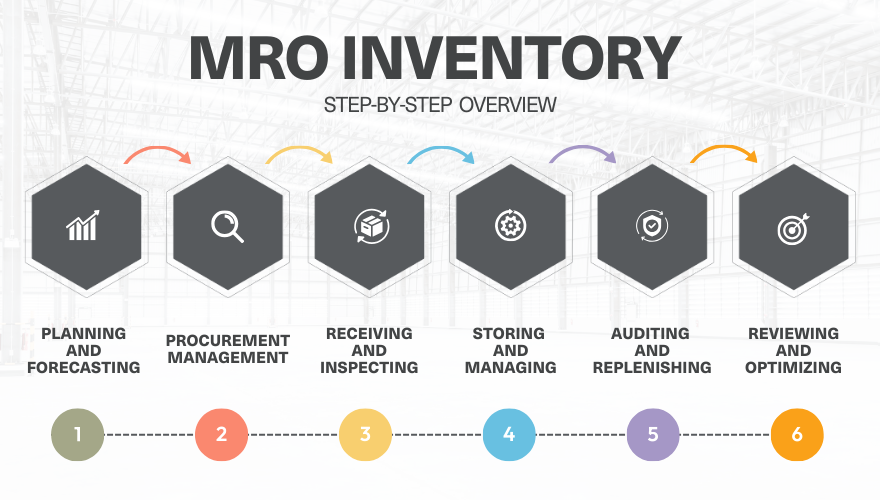
Challenges of MRO Inventory Management
Managing MRO inventory often comes with challenges, which can significantly impact the efficiency and reliability of your maintenance operations and productivity.
Some common challenges of MRO inventory management include:
High Acquisition Costs
High acquisition costs are due to shipping fees, taxes and storage costs. These can impact your budget by significantly increasing the cost of owning MRO inventory.
A report from Mordor Intelligence predicted an upsurge in MRO expenditures through 2028, as it reviewed what’s in store for handling the spare parts, equipment and consumables a company uses to manufacture a product.
In addition, the report found that manufacturers started to realize they needed to better equip themselves to control MRO expenditures to reduce the total cost and stay competitive in maturing markets.
Buyers demanded higher quality, while chief executive officers wanted larger profit margins. The result? MRO needed to perform optimally and run efficiently.
To reduce acquisition costs:
- Buy in bulk to take advantage of discounts
- Shop from local suppliers to reduce shipping fees
- Optimize the use of vertical or horizontal space in your warehouse to eliminate the need for additional storage
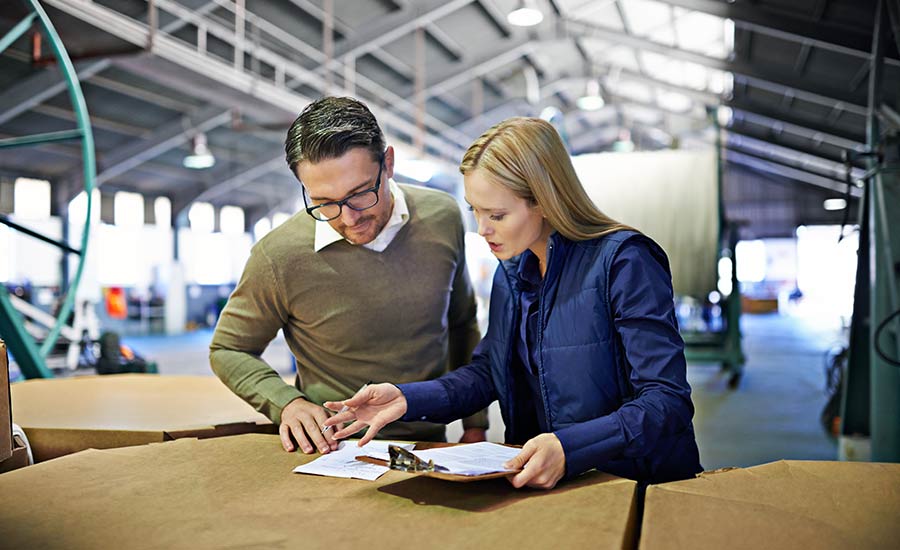
Tracking Inventory
Without a comprehensive inventory management system, you can’t be sure of the accurate stock levels of your MRO inventory.
For example, if an airline doesn’t carry spare parts for engine maintenance and something malfunctions, the airline will lose money every hour that a flight is delayed.
It’s the same concept in a warehouse. If you don’t have a stock of spare parts for a forklift, and the forklift fails, you’ll be looking at costly downtime and potentially bigger maintenance issues.
To track your MRO stock levels in real-time:
- Use a warehouse management system to gain real-time updates on inventory levels, locations and movement
- Equip your inventory with barcode or RFID tags and use scanners to track item movement
- Verify your physical stock against your system records every month or quarter to ensure inventory accuracy
- Configure your system to notify your warehouse manager when MRO inventory is running low, helping you prevent stockouts
Inaccurate Forecasting
MRO items are often required for unplanned repairs and maintenance, making demand prediction more challenging compared to regular inventory items.
Inaccurate forecasting can lead to stockouts, causing delays in maintenance and operational downtimes, or excess inventory, leading to increased holding costs.
To prevent inaccurate forecasting:
- Regularly analyze historical usage data and stay informed about upcoming maintenance schedules
- Implement advanced forecasting tools and techniques, such as predictive maintenance, to make more accurate predictions based on trends and patterns
- Adopt a flexible inventory strategy, such as safety stock or just-in-time inventory that can adapt to changes in demand
Parts Obsolescence
Technological advancements and equipment upgrades can lead to a significant challenge in MRO inventory management: parts obsolescence.
Parts obsolescence refers to the event in which components or parts used in manufacturing or repair of equipment become outdated or no longer available from the original manufacturers.
Take for example a manufacturing facility that has stocked various spare parts. Over time, they upgrade their machinery, and suddenly, they find that these spare parts are no longer compatible with the new equipment, which, in turn, makes the parts useless.
To reduce the risk of parts obsolescence:
- Regularly review and update your MRO inventory in line with equipment upgrades and technological changes
- Establish strong relationships with suppliers for updates on product lifecycles and potential discontinuations
- Consider adopting a just-in-time inventory approach to minimize the stock of items that are at a higher risk of becoming obsolete
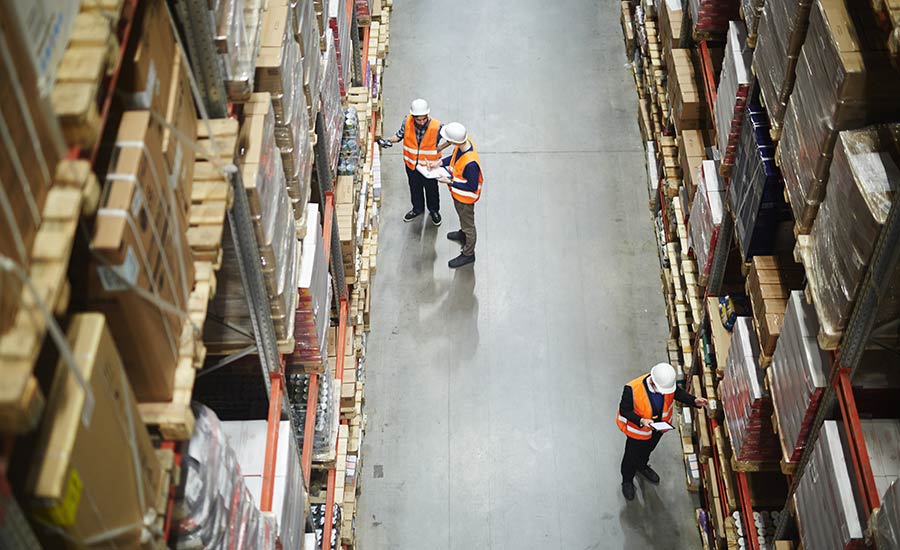
Personnel
Effective MRO inventory management heavily relies on the expertise of your personnel, as they provide knowledge and insights regarding your equipment and warehouse processes.
The challenge lies in ensuring that the staff managing MRO inventory is well-trained and knowledgeable about the technical aspects of the inventory and inventory management best practices.
For example, in a manufacturing setting, skilled personnel must understand the specifics of various machinery parts and their purpose in production. Inadequate expertise can lead to mismanagement, resulting in stockouts or excessive inventory, which are both costly scenarios.
To address personnel needs:
- Provide regular training on new technologies and the best practices in inventory management
- Implement systems to capture and share internal knowledge, mitigating the impact of staff turnover
- Promote cross-training to create a versatile and informed workforce, covering gaps and reducing knowledge loss risks
- Consider hiring specialists for industries with specialized equipment needs
MRO Inventory Management Best Practices
After investing in automated solutions, the next step is implementing these technologies into your warehouse daily operations.
Let’s take a look at the best practices for MRO inventory management.
Optimize Your Existing Warehouse Space
Eliminate the need to move into a bigger facility by making the most of your existing warehouse. Opt for vertical lift modules to maximize your vertical space and horizontal carousels to take advantage of your floor space.
Consider Vendor-Managed Inventory (VMI)
Consider vendor-managed inventory (VMI) or an arrangement in which your supplier manages and replenishes your inventory to help you:
- Reduce holding costs or fees that refer to storing items in a warehouse
- Prevent stockouts
- Free up space for other warehouse operations, such as expanding your production area or adding new product lines
Conduct Regular Audits
Conduct regular inventory audits to make sure your physical stock levels align with the records in your inventory management system.
This can help identify discrepancies early on so you can address issues, such as misplaced items, unrecorded usage or errors in data entry.
Educate Your Employees
Make sure that your staff is well-trained in inventory management practices by conducting regular training sessions and providing access to educational resources and workshops.
This can help keep them updated on the best practices and new technologies, ensuring they are equipped with the necessary skills and knowledge to manage your MRO inventory.
Use an Inventory Management Software
Implement a comprehensive inventory management software system to gain a bird’s eye view of your MRO inventory levels, monitor their location within your facility and give permission to make sure authorized employees have access to these parts.
Implement Automated Warehouse Solutions
Integrate automated solutions across your warehouse operations to enhance overall efficiency and streamline processes, such as sorting goods, counting inventory and picking and placing items.
This integration can lead to faster throughput and improved accuracy in tracking and managing stock levels.
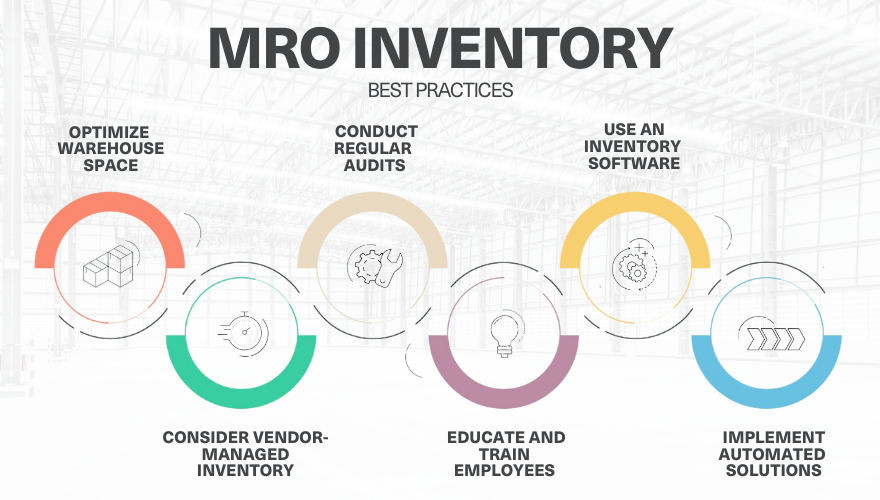
Benefits of Utilizing Modula Automated Solutions for MRO Inventory Management
For MRO departments, maintaining an efficient inventory is key to minimizing downtime and making sure operations are smooth.
Modula’s suite of automated storage solutions and Warehouse Management System (WMS) are specifically designed to address the unique MRO facilities challenges, delivering benefits across key areas.
Optimize Space Use
Modula automated storage and retrieval systems (ASRS) are designed to maximize storage space. They can store items in a compact and high-density approach, which is particularly beneficial for MRO departments that often have a wide variety of parts and tools of different sizes.
Modula vertical lift modules (VLMs) make the most out of your available ceiling height to minimize floor space usage while ensuring items are delivered to employees at a comfortable, ergonomic height.
Modula’s VLMs are available in three models:
- Modula Lift: Ideal for facilities with limited floor space, Modula lift utilizes vertical space effectively, compressing up to 9,050 sq ft of conventional storage into a mere 150 sq ft footprint. This allows MRO departments to store significantly more parts in a smaller space, freeing up valuable floor area for other critical operations.
- Modula Slim: Ideal for facilities with limited space, requiring only 32.29 sq ft of floor area, perfect for places where parts and components are needed.
If your MRO facility has limited ceiling height, the Modula Horizontal Carousel (HC) can be a perfect solution. It offers up to 99% accuracy in picking and picking speeds of up to 550 lines per hour, essential for the fast and precise management of MRO parts.
Modula’s horizontal carousel allows you to:
- Attain up to 99% accuracy in picking, drastically reducing errors and increasing efficiency
- Manage picking speeds of up to 550 lines per hour, streamlining your operations and saving time
- Secure your inventory from unauthorized access, thanks to the 8’ high perimeter fencing
- Minimize the risks associated with moving machinery, ensuring a safer work environment
Enhance Inventory Accuracy and Control
Automated systems provide secure storage for MRO tools and parts, which can be fragile or expensive.
Controlled access to inventory can help in tracking usage and minimizing instances of lost or misplaced items. In addition, these systems are equipped with advanced inventory management software. They can keep precise track of every item in storage, including its location, quantity and usage history.
This level of detail helps ensure that the right parts are always in stock, preventing delays in maintenance tasks due to missing or hard-to-find components.
Modula’s real-time inventory tracking and monitoring allows your MRO personnel to:
- Eliminate manual counting and discrepancies with automated tracing, ensuring accurate data for informed decision-making
- Analyze historical data and usage patterns to predict future needs, preventing stockouts and costly overstocking
- Make informed decisions based on real-time data, reducing unnecessary inventory and associated costs
Modula’s Warehouse Management System (WMS) is our comprehensive and intelligent inventory management software designed to seamlessly integrate with Modula’s automated storage and retrieval systems.
Maximize Picking Efficiency and Productivity
Automated storage and retrieval systems can help optimize the process of retrieving and storing items, which can significantly speed up the process compared to manual methods.
For MRO departments, this translates into quicker access to necessary tools and parts, leading to faster completion of maintenance and repair tasks.
Modula’s automated storage and retrieval systems allow you to:
- Eliminate time-consuming manual tasks associated with picking and storing. VLMs and HCs deliver items directly to the operator at an ergonomic height, significantly reducing travel time and increasing picking speeds.
- Minimize bending, reaching and lifting, reducing the risk of injury and creating a safer work environment for MRO personnel
Reduce Inventory Costs and Downtime
By optimizing storage space, improving inventory accuracy, and increasing worker productivity, automated storage and retrieval systems can lead to significant cost savings.
This is beneficial for MRO departments, in which efficient operation is key to minimizing downtime in production.
Modula’s automated storage and retrieval systems allow you to:
- Reduce carrying costs by accurately predicting future demand and optimizing inventory levels, ultimately reducing the risk of overstocking and minimize carrying costs for unused parts.
- Minimize the need for manual labor, leading to significant cost savings on personnel expenses. This can help you optimize your workforce and allocate your resources towards higher-value activities, such as quality assurance.
- Improve inventory accuracy and faster picking speeds to minimize downtime associated with searching for parts or waiting for deliveries. This ensures MRO teams can respond to maintenance requests quickly and efficiently, minimizing disruptions and optimizing operational uptime.
Scale Your Changing Needs
As the needs of the MRO department change, automated storage and retrieval systems can be adapted and scaled.
This flexibility ensures your investment remains valuable over time, accommodating new types of inventories or changing volumes of orders.
Modula’s automated storage and retrieval systems allow you to:
- Accommodate your MRO department’s evolving needs and changing inventory requirements without making significant infrastructure changes.
- Seamlessly integrate with existing MRO software and systems, minimizing disruption to your current workflows and ensuring a smooth transition.
- Customize your MRO facility layout and storage requirements to ensure optimal space utilization and efficient operations.
Improve Safety and Ergonomics
Automated storage and retrieval systems can eliminate the need for your employees to perform physically demanding tasks, such as climbing, lifting heavy items or retrieving items from high shelves.
This improves safety by minimizing the risk of accidents and injuries and contributes to better ergonomics in the workplace.
Modula’s vertical storage solutions and HC systems provide maximum safety for personnel, even in demanding working conditions.
Our automated storage and retrieval systems work by delivering inventory directly to your employees, reducing their need to use heavy machinery.
Additional safety features, such as security light curtains, can help prevent other injuries, such as getting pinched by moving parts.
Use Preventive and Reactive Maintenance
Using preventive maintenance and reactive maintenance is an important aspect of managing an MRO department effectively, as it creates strategic decisions about when to invest in preventive maintenance and how to respond efficiently to unforeseen repairs.
Modula Cloud is a is a remote management tool for Modula’s storage systems, providing detailed, real-time insights into warehouse operations, equipment performance, and maintenance needs.
This level of oversight and data-driven decision-making capability allows for more effective maintenance scheduling, minimizing downtime and operational disruptions.
Always on and user-friendly, Modula Cloud consolidates all data into an intuitive online portal. This allows for secure and efficient tracking and management of your warehouse operations, so you can access it from any device, anywhere.
Modula Cloud allows you to:
- Stay informed with real-time alerts, keeping you updated on important warehouse events and changes
- Experience the freedom and flexibility of remotely managing operations
- Quickly address issues with remote troubleshooting and support, reducing costly downtime
- Anticipate maintenance needs with predictive analytics
Ultimately, Modula Cloud can help your MRO manager make informed decisions about maintenance, balancing preventive actions with reactive needs, and ensuring smooth operations.
At Modula, we offer advanced storage solutions and a complete WMS to help ensure your maintenance inventory is always secure and on hand when needed.