What Is Order Picking? Definition, Methods & Systems to Use
The recent boom in eCommerce has prompted a series of challenges, including a greater need for onshore inventories, increased customer expectations and costly product returns.
With these challenges, the need to optimize processes such as order picking has never been more crucial.
We’ll explain the process of order picking, along with the best warehouse order picking strategies and systems you can use to optimize your picking process.
Plus, we’ll share the best technologies (including order picking robots) you can leverage to complement your strategy and further improve picking accuracy, speed and efficiency.
What Is Order Picking?
Order picking, or warehouse order picking, is the process of collecting goods from a warehouse, which are then packed and shipped to the customer.
Order picking allows warehouse operators to efficiently fulfill customer orders by choosing the correct SKUs from your inventory, thanks to picking systems such as picker robots and voice-picking systems.
Effective warehouse picking reduces — or even eliminates — mispicks and improves overall customer satisfaction.
Types of Order Picking Methods
To optimize picking processes and, in turn, the entire order fulfillment process, it’s important to find the picking methods and strategies that work best for your organization.
Common picking methods in the warehouse include:
Single Order Picking
Single order picking, or discrete order picking, is a picking strategy in which a warehouse employee manually picks a single order.
In this method, a picker receives printed pick lists and travels through the warehouse to manually collect each item on the list for a specific order.
Zone Picking
Zone picking, or pick and pass, is a picking strategy in which the facility is divided into several zones and pickers are assigned to specific areas.
Each warehouse employee is responsible for gathering goods within their designated zone and passing the order to the next zone until all items in the order are picked.
Batch/Multi-Order Picking
Batch picking is a picking strategy in which a warehouse employee collects multiple orders simultaneously during a single pass through the facility.
In this method, orders with similar items or destinations are grouped together — for example, all orders containing a specific type of electric component or all orders destined for the same city.
The picker then retrieves all items for these grouped orders in one journey around the facility.
Wave Picking
Wave picking is a picking strategy in which orders are grouped and picked in waves throughout the day based on specific criteria, such as delivery schedules or shipping destinations.
In this method, a warehouse management system (WMS) schedules and organizes the waves.
Warehouse employees collect items for a batch of orders during each wave, which allows for a more organized and efficient use of labor and warehouse resources.
Parallel Picking
Parallel picking is a picking strategy in which multiple warehouse employees work simultaneously on picking partial parts of the same order.
In this method, an order is divided into smaller parts or sections, and each picker is responsible for collecting items from their assigned section of the warehouse.
For example, if a phone accessory kit consists of different items stored in different parts of the facility, one warehouse employee will be responsible for collecting earphones from one section, while another employee collects a phone case from a different area.
After picking all parts of the order, warehouse employees consolidate them at a central location before packing and shipping.
Cluster Picking
Cluster picking is a picking strategy in which a warehouse employee picks items for multiple orders simultaneously using a multi-compartment cart or trolley.
In this method, the picker travels throughout the warehouse once, picking items for several orders and placing them into different compartments or bins on their cart.
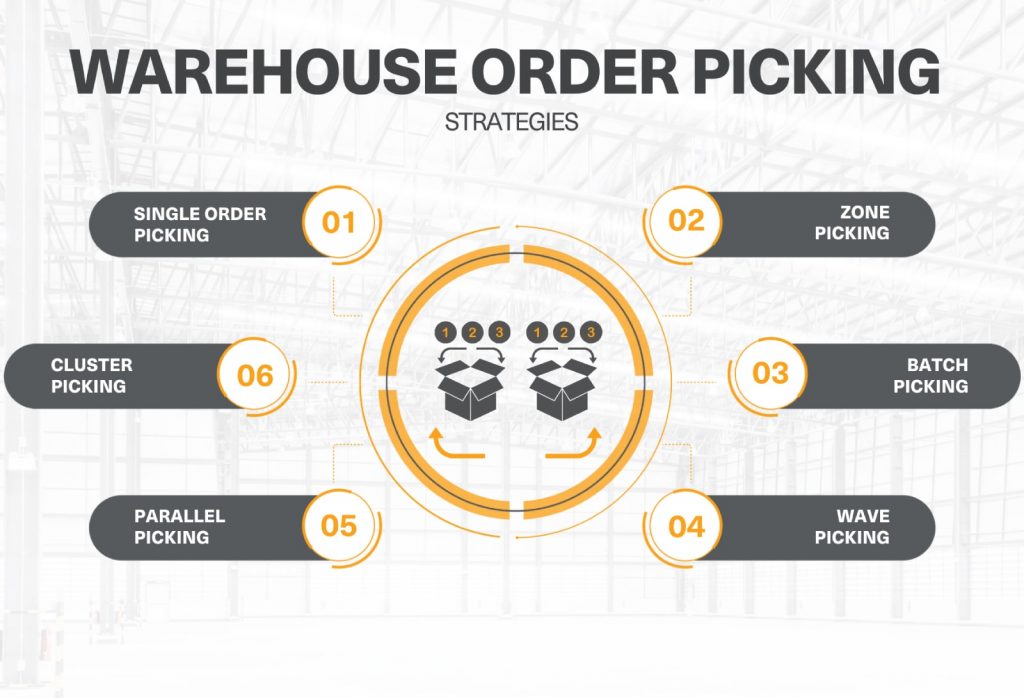
Top Order Picking Systems
Warehouse picking systems come in different types to enhance picking efficiency and accuracy.
Types of picking systems include:
Collaborative Robots
Collaborative robots, or cobots, are advanced warehouse robotics designed to work alongside warehouse employees to enhance efficiency and productivity.
They are equipped with sensors and built-in safety features for seamless collaboration. In warehouses, cobots are used for tasks like palletizing (organizing products on pallets), as well as picking and packing orders.
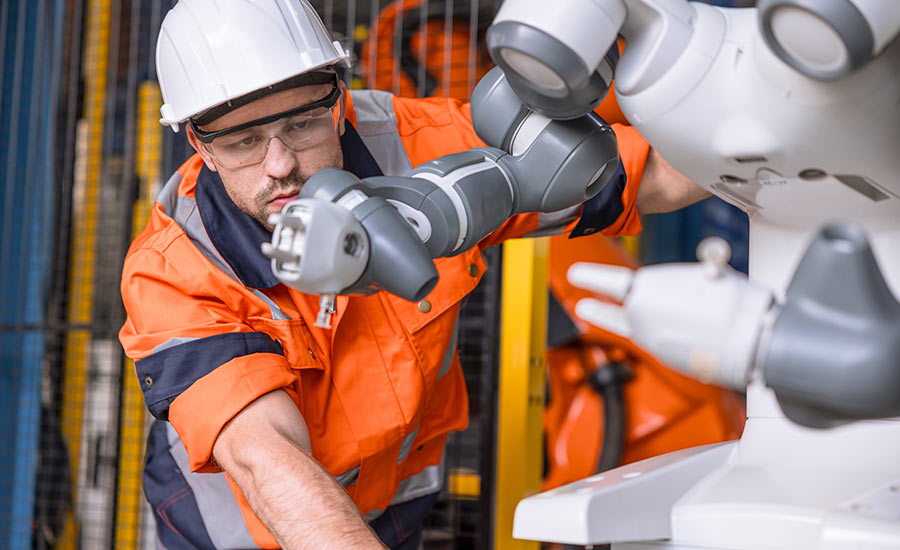
Pick to Light Systems
Pick to light systems are assisted picking technologies that guide warehouse operators with visual picking instructions. They can help reduce errors and improve picking accuracy.
This type of picking system leverages alphanumerical LED displays and buttons at various storage locations within the warehouse to help employees with light-assisted manual putting, sorting, picking and assembly tasks.
Voice-Picking Systems
Voice-picking systems are picking systems that utilize voice prompts and advanced speech recognition software to communicate picking instructions to warehouse employees through headsets.
Warehouse employees receive verbal commands on which items to pick and where to find them, allowing them to keep their hands and eyes free for the task.
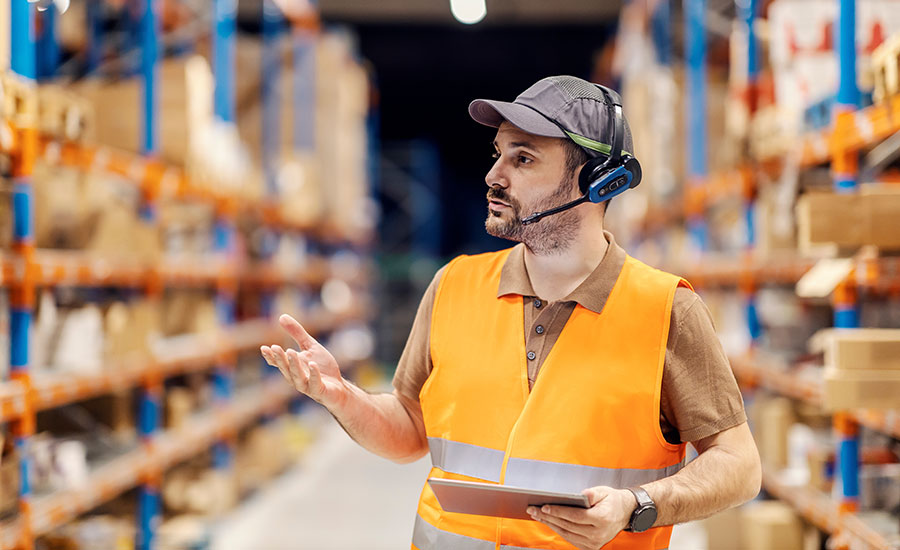
Heavy-Duty Picking Equipment
Heavy-duty picking equipment are warehouse machines designed to handle large and heavy inventory, such as boxes of orders.
This type of equipment enhances warehouse operations by boosting efficiency, picking accuracy, safety and productivity.
Heavy-duty warehouse equipment include:
- Forklifts: Lifts and transports heavy loads, especially palletized products
- Reach trucks: Retrieves items from high shelves in narrow aisles
- Order pickers: Lifts warehouse pickers to the level of high racks for picking individual goods
- Stackers: Used for stacking and retrieving pallets in stacking areas
Autonomous Mobile Robots (AMRs)
Autonomous mobile robots (AMRs) are sophisticated robots that can independently travel in a warehouse, reducing the need for human intervention.
They use technologies such as machine learning, artificial intelligence and sensors to plan and adapt to their paths in real-time.
Automated Storage and Retrieval Systems (ASRS)
Automated storage and retrieval systems (ASRS) are computer-controlled systems that automatically store and retrieve items in a warehouse.
Automated storage and retrieval system are integrated with a WMS to identify which items to retrieve.
This warehouse storage solution includes tote shuttles, mini-loaders, vertical lift modules, horizontal carousels and unit loaders.
ASRS are ideal picking and storage solutions to optimize storage and retrieval processes for efficiency and accuracy.
At Modula, we reimagine warehouse operations with our leading automated solutions, designed to improve picking efficiency and accuracy.
Our order picking solutions include:
- Put to Light: Save time on warehouse picking and increase accuracy when processing large batches of orders. Our Put to Light system features an OLED configurative display and uses a scanner and LED lights to direct the operator to the location where the items must be placed.
- Modula Picking Station: This solution uses the Put to Light system for batch picking and order consolidation and allows for scanning or touch light validation to boost accuracy.
- Modula Picking App: This innovative solution is for improving picking and replenishment operations. The app allows picking operators to manage picking on their mobile devices and monitor processes on the go.
- Modula Picking Cart: This system is equipped with shelves, four wheels, Put to Light controllers, battery backup and Wi-Fi controllers. It also features five configurable displays and scan or touch validation for improved speed and accuracy.
3 Key Benefits of Choosing the Right Order Picking Method and System
A streamlined picking process gives you the best opportunity to quickly fulfill customer orders without sacrificing quality.
Certain picking methods, such as zone picking, can help make better use of warehouse space.
This division allows for more organized storage and reduces the distance that workers need to travel to collect items, speeding up the picking process.
Achieve Scalability or Adaptability
As order volumes change or business expands, having an effective picking method enables a warehouse to adapt more easily.
This scalability is essential for handling peak periods, such as holidays or sales seasons, without a drop in service quality.
Meet Customer Expectations
The right picking strategy can notably improve the timeliness of shipments.
Since delivery is a crucial part of the shopping experience for many, logistics companies need to ensure orders are picked, packed, and ready for shipment quickly.
5 Essential Warehouse Order Picking Best Practices
Once you’ve invested in the right picking systems, the next step is to implement these solutions into your warehouse picking processes.
Warehouse order picking best practices you should implement include:
Optimize Your Warehouse Layout
Arrange your warehouse to streamline the flow of goods, reduce travel time for pickers and ensure easy access to frequently picked items.
For example, you can arrange your warehouse for optimal picking by placing the most frequently picked items near the shipping area.
This minimizes the distance pickers need to travel to collect these items, speeding up the entire picking process.
Use the Correct Equipment
Equip your team with appropriate tools to improve safety and achieve efficiency in the picking process.
This includes using automated storage and retrieval systems to reduce physical strain and utilizing AMRs for picking efficiency.
Implement a Warehouse Management System
Utilize a WMS to optimize picking routes and reduce mispicks. When you use a WMS, it analyzes the order and determines the most efficient route based on the items’ locations.
For example, if a customer orders a pair of shoes, a jacket and backpack, the WMS first identifies where each item is stored.
It can direct the picker to start at the footwear section, move to outerwear and finish at the accessories area, if this is the shortest possible path.
Modula’s warehouse management system is designed to seamlessly integrate with our advanced automated storage and retrieval systems, creating a unified and efficient warehouse management experience and improving overall productivity.
It stands out as one of the market’s most intuitive and advanced software solutions and effortlessly interfaces with nearly all DMS and ERP systems, optimizing processes such as receiving, storing and picking.
Track Your Warehouse Productivity
Regularly monitor and analyze warehouse key performance indicators (KPIs) related to picking, such as picking productivity and picking accuracy, to identify areas for improvement and implement changes when needed.
For example, if your data shows a decrease in picking accuracy, consider adjusting your picking method to reduce errors.
In addition, if productivity metrics are lagging, you can explore introducing automated order picking systems to your employees or reorganizing the layout of your warehouse to streamline the picking process and improve efficiency.
Outsource Fulfillment to a Third-Party Logistics (3PL)
If you don’t have the resources or lack the space, consider partnering with a 3PL to expertly handle your warehousing and fulfillment needs — especially if you are scaling operations.
When it comes to order picking, a 3PL can help implement advanced technologies and proven strategies, such as automated picking systems or optimized warehouse layouts, which can significantly reduce the time and cost associated with fulfilling orders.
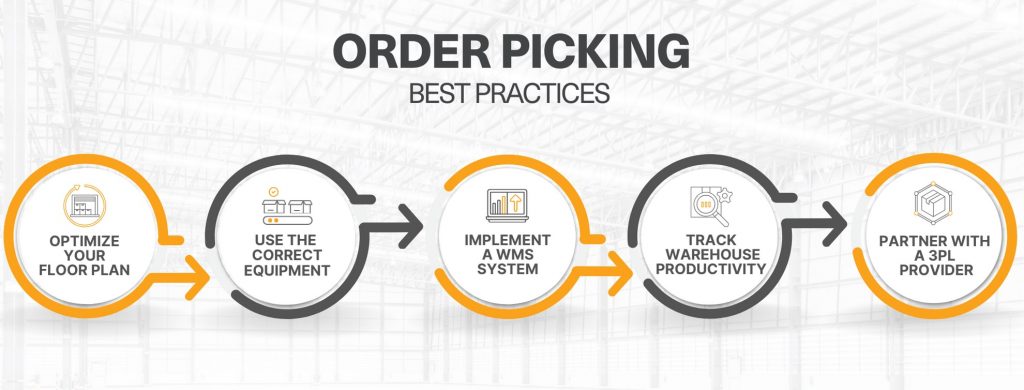
At Modula, we help you streamline the picking process with automation, reducing mispicks, increasing speed, and improving accuracy.
From Put to Light systems to automated storage and retrieval systems, our solutions are designed to improve efficiency throughout your warehouse operations.
Reach out to our team to discover how our picking solutions can help meet your needs.