Warehouse Automation for Beginners: Types & 2024 Technology Trends
Whether it’s automating labor-intensive tasks, improving productivity, or reducing human error, warehouse automation addresses a wide range of warehousing needs and challenges.
We’ll share everything you need to know about warehouse automation, from how it works to the top trends to leverage in 2024.
Plus, we’ll introduce you to our advanced automated solutions at Modula that will help you reimagine your warehouse space and streamline operations.
What Is Warehouse Automation?
Warehouse automation is the process of using technology to improve workplace productivity and safety, help warehouse operators manage labor-intensive tasks and ultimately, streamline warehouse operations.
Warehouse automation encompasses a range of technologies, including robots, computer systems, and automated material handling equipment, to automate and optimize various warehouse processes and tasks.
Check out the difference between a traditional and an automated warehouse in the video below:
Traditional vs Automated Warehouse Picking System
Types of Warehouse Automation Technology
From automated storage and retrieval systems to autonomous mobile robots, here are eight solutions that expedite your order fulfillment process and reduce manual tasks.
- Goods-to-Person (G2P): With G2P, goods are delivered directly to warehouse operators through the use of carousels, vertical lift modules, or conveyors. This type of warehouse automation increases efficiency, throughput, and productivity while reducing warehouse congestion.
- Automated storage and retrieval systems (AS/RS): Automated storage and retrieval systems (AS/RS) are part of the goods-to-person technology. These high-tech solutions are used in warehouses to store items in a specific area and retrieve them when needed. AS/RS are supported by computers. They are integrated with a warehouse management system (WMS) or warehouse execution system (WES), to determine which order should be retrieved from the inventory. This solution includes automated systems such as tote shuttles, mini-loaders, unit-loaders, horizontal carousels, vertical lift modules, and more.
- Mobile robots (autonomous mobile robots and automatic guided vehicles): Autonomous mobile robots (AMRs) are sophisticated robots that use artificial intelligence and sensors to navigate their way throughout the warehouse independently and transport goods. On the other hand, automatic guided vehicles (AGVs) are the predecessors of AMRs. While AGVs can transport goods over long distances, they require guidance from warehouse operators and rely on wires and reflective markers to function.
- Pick to light systems: Pick to light systems are a type of order-fulfillment technology that uses colored LED lights to guide operators in the picking and sorting processes.
- Put to light systems: Put to light systems are “pick to light in reverse”. They guide warehouse operators during the replenishment phase. The lights direct operators to the correct location to sort, or “put,” items.
- Voice picking and tasking: Pick by voice or voice picking uses mobile headsets and speech recognition to direct warehouse pickers to the accurate picking location.
- Automated sortation systems: These systems identify goods on a conveyor system and redirect them to their designated warehouse locations using barcode scanners, radio frequency identification (RFID) and sensors. This type of warehouse automation is used for receiving, picking and packing.
What Warehouse Processes Can You Automate?
A vast majority of warehouse processes can be automated with smart technology to increase productivity, streamline operations and reduce human error.
Warehouse processes that can be automated include:
- Receiving
- Sorting
- Returns
- Inventory management
- Picking
- Replenishment
- Put away
- Packing
- Shipping
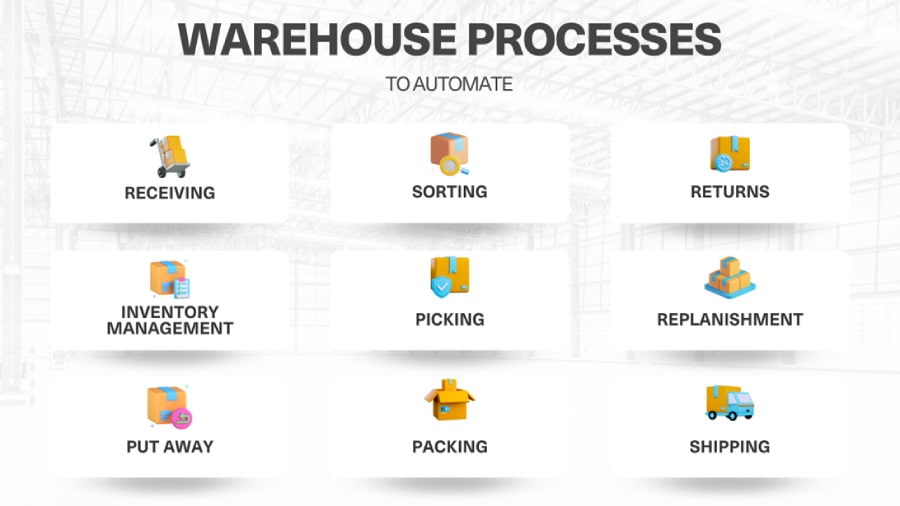
When To Automate Your Warehouse
Whether you’re in the early stages of optimizing your warehouse, or you’re experiencing some difficulties and looking to streamline operations, warehouse automation can be the answer you’re looking for.
A few examples of when you should consider automating your warehouse include:
- Your manual processes are causing inefficiencies and errors such as mispicks
- Your inventory counts are inaccurate
- You are running out of storage space for your inventory
- You want to increase workplace safety
- You want to reduce labor costs
- You need to handle higher volumes of inventory and shipments
- You want to increase productivity
12 Warehouse Automation Technology Trends for 2024
From LED lights that indicate pick locations to intelligent robots that reduce your warehouse operator’s travel time, here are 12 warehouse automation technology trends to leverage in 2024.
AI and ML Integration
Artificial intelligence (AI) is the ability of a computer or robot to perform tasks that are typically done by a human. AI boosts productivity and accuracy within the warehouse (by preventing mispicks, for example).
Machine learning (ML) is a branch of AI technology in which machines can forecast stock needs, plan inventory purchases and perform other tasks — for example, a robot that handles fragile products to prevent damages.
Collaborative Robots
Collaborative robots, or cobots, are robots that are equipped with sensors and safety features that allow them to work with human workers, improving productivity and efficiency.
Typically, cobots are used to perform tasks such as order picking, packing and palletizing (storing products in a pallet).
IoT-Powered Smart Warehouses
Internet of Things (IoT) technologies boost efficiency, cut costs and increase productivity within the warehouse.
IoT devices include sensors, RFID tags and wearable devices that track and manage inventory, monitor equipment and streamline supply chain operations.
AR and VR for Warehouse Training
Virtual reality (VR) is a computer-generated environment that utilizes neural networks, machine learning technologies and a pose tracking system to immerse you in a virtual environment.
On the other hand, augmented reality (AR) combines the real world and a computer-generated environment to create an interactive experience.
You can integrate AR and VR technologies into your warehouse training program to introduce processes and improve employee productivity and safety.
For example, you can use a 360 VR headset to introduce your employees to the order fulfillment process before they enter your warehouse.
Warehouse Management Systems
Warehouse management systems (WMS) are scalable software applications that manage inventory and day-to-day warehouse operations, such as tracking orders, shipping and delivery.
Advances in warehouse management systems provide real-time data for better decision-making and improved efficiency.
Automated Storage and Retrieval Systems (AS/RS)
Automated storage and retrieval systems (AS/RS) are powered by computer systems to automatically store and retrieve goods in a warehouse with optimal accuracy and speed.
These solutions are integrated with a warehouse management system (WMS) or warehouse execution system (WES), to determine which orders should be retrieved from the inventory.
There are seven types of AS/RS:
- Unit-Load AS/RS
- Mini-Load AS/RS
- Vertical Carousel-based AS/RS
- Horizontal Carousel-based AS/RS
- Vertical Lift Module AS/RS
- Shuttle- and Bot-based AS/RS
- Micro-Load (Stocker)
Voice Picking
Voice picking is a type of warehouse automation technology that utilizes voice recognition and commands to boost picking accuracy and efficiency by freeing employees’ hands at work.
In voice picking, a warehouse operator wears a headset to hear voice commands and prompts that lead them to the picking location.
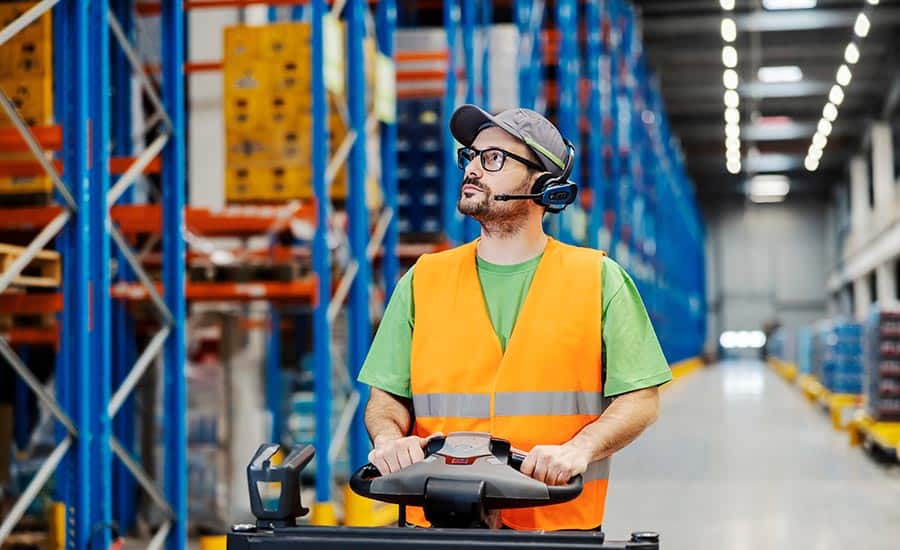
Wearables
Wearables are devices worn by warehouse operators to improve warehouse productivity and efficiency.
Wearables include devices such as GPS-tracking bracelets, smart watches and finger-trigger gloves.
These solutions are equipped with sensors and cameras that allow employees to access picking data in real time and track inventory.
Automated Guided Vehicles & Autonomous Mobile Robots
Automated guided vehicles (AGVs) are vehicles that can travel throughout your warehouse with the help of pre-defined routes and a warehouse operator.
On the other hand, autonomous mobile robots (AMRs) are more sophisticated robots that can travel throughout your warehouse without human intervention thanks to sensors, artificial intelligence and machine learning.
Both AGVs and AMRs transport goods within your warehouse to improve efficiency and increase workplace safety.
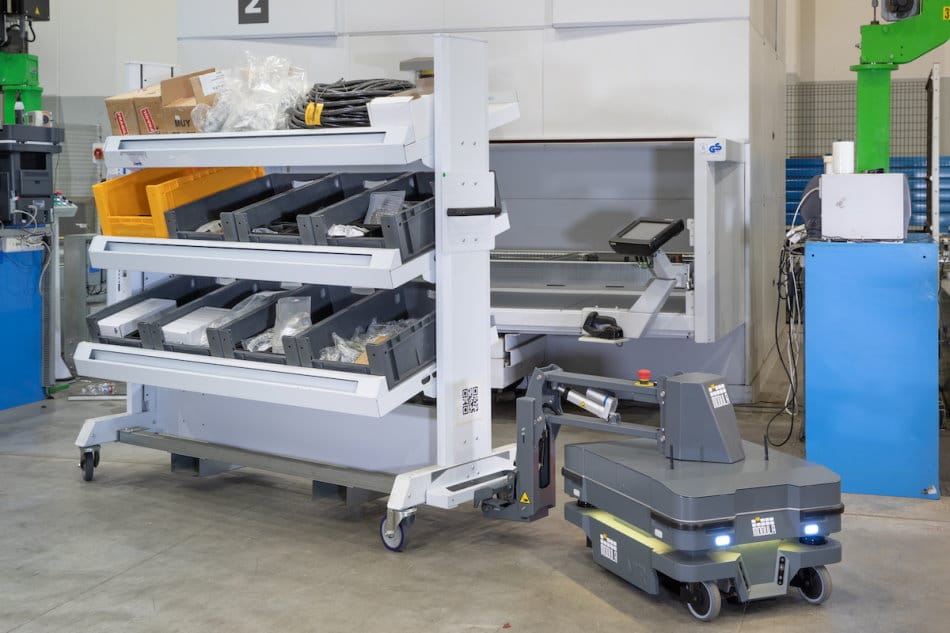
Warehouse Drones
Warehouse drones, or unmanned aerial vehicles (UAVs), are aerial robots that capture images of your inventory and retrieve products, to help with inventory management and stock replenishment.
Warehouse drones are equipped with cameras and sensors to help gather data. They can be controlled by warehouse operators or programmed to fly autonomously.
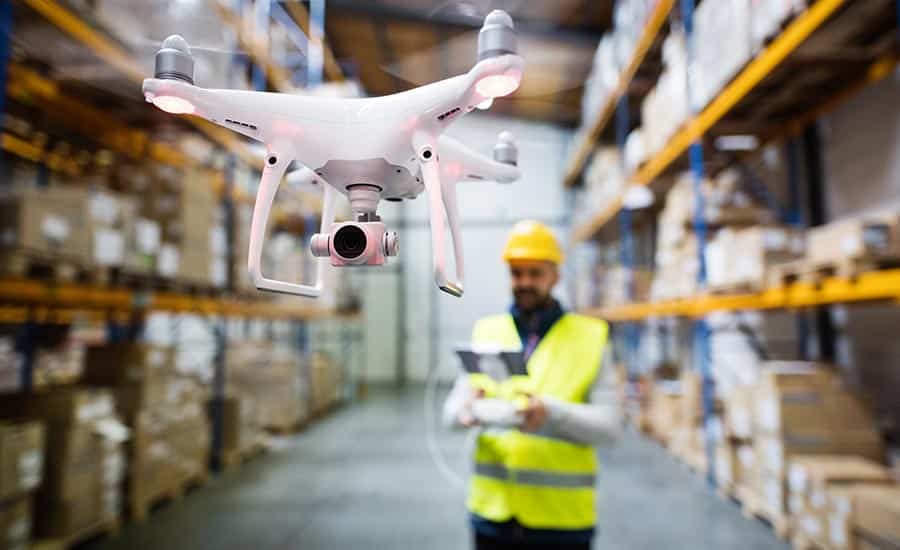
Predictive Maintenance
Predictive maintenance is a warehouse maintenance strategy that utilizes data collected by a software system.
In predictive maintenance, data from sensors and other sources is collected and analyzed to detect patterns and anomalies that indicate potential equipment failure.
This data is used to create a predictive model that can identify when maintenance is likely to be required. This allows you to schedule maintenance at a time that is most convenient, reducing costly downtime and increasing equipment lifespan.
Predictive maintenance can be applied to a wide range of equipment, including machinery, vehicles, and production lines.
Sustainability
Warehouses consume a lot of energy to run equipment and HVAC systems. In fact, a non-refrigerated warehouse in the United States consumes around 6.1 kilowatt-hours (kWh) per square foot each year.
Sustainability is expected to become even more critical in 2023 as companies face increasing pressure from consumers, regulators, and stakeholders to reduce their environmental impact.
This trend is likely to drive the adoption of new technologies and practices, such as the use of renewable energy resources and automated material handling systems to optimize their use of resources and minimize waste.
How To Automate Your Warehouse Step-by-Step
So, how exactly do you automate your warehouse? Here are six steps to warehouse automation:
- Assess your current processes: Evaluate your current warehouse processes, including receiving, storing, picking, packing, and shipping. Identify areas where automation can bring improvements.
- Define goals and requirements: Next, identify the specific goals and requirements you want to achieve through automation, such as improving accuracy and efficiency and gaining complete visibility over your inventory.
- Research: Research and compare different types of technologies and solutions. For example, autonomous mobile robots and robot arms in the picking process, and warehouse management systems for inventory management.
- Develop a plan and budget: Then, develop a comprehensive implementation plan and budget for the automation solutions, including resources required, timeline and estimated costs.
- Determine and implement the type of warehouse automation you need: Do you need to streamline manual data entry and minimize human errors? Or, do you need to improve picking accuracy? Identify the type of warehouse automation that aligns with your goals and implement the solutions.
- Train employees: Once your automated solutions are in place, train your employees on the new technology and processes to reduce the risk of workplace accidents, and maximize the automated solution’s performance.
How Can Warehouse Automation Impact Your Operations?
Warehouse automation is used to optimize different warehouse processes, such as receiving, returning, picking, sorting and shipping.
Here are seven key benefits you can look forward to when implementing automation.
Optimizes Warehouse Space
Global retail eCommerce sales are expected to reach $7.4 trillion by 2025.
While moving into a bigger warehouse to store a larger inventory may be an option for some companies, investing in smart systems (think vertical lift modules) can free up as much as 90% of your current warehouse space, allowing you to optimize what you’re working with instead of moving.
Boosts Employee Safety
A recent study found that overexertion, falls and getting struck by an object were the top disabling workplace accidents in 2022, respectively.
Automated solutions help prevent workplace injuries in several ways: they handle heavy lifting, bring items directly to employees, and perform tasks that may be hazardous for employees.
Improves Inventory Control and Visibility
Manual inventory management is time consuming and prone to human error.
The solution to simplified and accurate reporting? Warehouse automation.
Automated systems continuously update your POS software, resulting in accurate inventory data. A warehouse management system also provides inventory visibility down to a specific tray or item.
Enhances Accuracy and Reduced Errors
Human errors in inventory management and order fulfillment can lead to costly mistakes, such as incorrect inventory records leading to stockouts or excess stock, and sending the wrong items to customers, respectively.
In addition, a recent industry report found that 25% of customers return items they purchased online because they received the wrong item.
Mispicks are costly errors that occur when an employee picks the wrong item or quantity of items, fails to pack an item or mislabels an order.
Automated systems, which are guided by precise algorithms and continuous data flow, minimize these errors.
For example, robotic picking systems and advanced sorting systems can help make sure that the correct items are picked, packed and shipped to the correct customer.
Increases Warehouse Throughput
A recent survey found that more than 40% of consumers in the United States expects their online packages to be delivered within two to three days of ordering, while 27% said that they hope to receive their deliveries within the same day of ordering.
Boosting warehouse throughput can help you improve productivity and increase customer retention, by delivering accurate purchase items within the expected delivery time.
Facilitates Scalability
Optimize the Picking Process
Automated systems can seamlessly scale up or down with relatively less effort compared to expanding your workforce.
This flexibility enables businesses to easily respond to market changes, growth opportunities or peak seasons (think holidays or end-of-year clearance sales).
Foster Sustainability
Automation promotes sustainability in your warehouse operations. For example, innovations such as Modula Vertical Lift Modules and Horizontal Carousels only utilize energy when they are in use.
When these modules are not in use, they remain in a standby mode that consumes minimal energy, further reducing the operational carbon footprint, lowering energy costs and improving overall resource efficiency.
Automated Warehouse Solutions at Modula
Modula is the leading provider of modern storage solutions and inventory management systems. We reimagine your warehouse operations through our automated solutions, which allow you to:
- Optimize your warehouse space
- Perform high-speed and accurate order fulfillment
- Increase picking accuracy to up to 99%
Modula Vertical Lift Modules
With our vertical lift modules (VLMs), you can optimize your warehouse space using your available ceiling height and ease operational efforts by delivering items to your employees at an ergonomic retrieval height.
Choose from Modula’s two vertical lift modules:
- Modula Lift: Utilizes 9,050 square feet of traditional storage in only 150 square feet
- Modula Slim: Requires only 32.29 square feet of floor space
Modula Horizontal Carousels
We’ve walked you through vertical solutions, but what if your warehouse has low ceilings?
Our Modula Horizontal Carousel (HC) is ideal for warehouses where ceiling height is limited.
In addition to taking advantage of your warehouse width, our horizontal solution enables fast and accurate order fulfillment, thanks to:
- Picking accuracy of up to 99%
- Picking rates of up to 550 lines per hour for each worker
- Single or dual three-horsepower drives to move more goods quickly
Modula Order Picking Solutions
Say goodbye to tedious manual picking processes. Our Modula order picking solutions are intuitive and easy to implement for quick and efficient order fulfillment.
Our order picking solutions allow you to:
- Improve picking accuracy thanks to visual picking aids such as LED bars
- Increase picking speed by reducing the need to search for items in the warehouse
- Improve inventory management by providing an in-depth view of your existing and forecasted inventory
Modula Warehouse Management Systems
Modula Warehouse management system (WMS) is the leading intuitive software solution that provides visibility into your entire inventory. It is built to operate Modula’s automated storage and retrieval solutions. If you own a traditional warehouse, our WMS can act as a stand-alone software.
As one of the most intuitive and next-level software solutions on the market, Modula WMS seamlessly integrates with almost all DMS and ERP systems, to enable seamless inventory and order management.
Our Modula WMS allows you to:
- Manage and track individual goods
- Monitor orders, including order processing, shipping and delivery
- Manage and track the movement and location of inventory within your warehouse
- Assign tasks to warehouse operators, monitor user activity, and set access levels and permissions
- Monitor system performance
- Generate reports and alerts
- Analyze analytics
- Integrate and share data with other systems through file import/export or data entry
Modula Web Analytics
Redefine remote warehouse management and support with Explore Modula Web Analytics.
The easy-to-use online portal allows you to securely manage and monitor your warehouse operations from any device, no matter where you are in the world.
Modula Web Analytics is a support, remote management, and analytics platform that gathers analytical data from your automated storage and retrieval systems, regardless of their location.
Explore Modula Web Analytics offers:
- Remote support, management and monitoring of your Modula storage systems
- Predictive maintenance, which allows you to monitor storage unit status in real time
- Real-time notifications and updates
- 24/7 supervision
Warehouse automation provides a streamlined solution for warehouses to fulfill orders and meet increasing consumer demands.
At Modula, our solutions range from horizontal and vertical carousels to order picking solutions and more. We help you upgrade your warehouse operations thanks to automated solutions. Fulfill more orders and meet rising consumer demands in 2023 with Modula’s automated solutions.