Automated Storage Solutions for Pharmaceutical Companies
Medical and pharmaceutical companies operate in one of the most complex and regulated sectors, which poses significant challenges, especially when it comes to material handling and inventory management.
These include adhering to strict regulatory guidelines, ensuring the traceability of products from manufacture to delivery, preserving the integrity of temperature-sensitive medications while
accurately forecasting demand to prevent surplus or shortages.
Given these challenges, pharmaceutical manufacturers are analyzing every aspect of cost optimization — including logistics, supply chain management and production costs.
Switching to digital solutions and advanced warehouse technology can provide substantial benefits, such as saving valuable floor space, enhancing productivity, ensuring accuracy in a controlled and secure inventory environment, and ultimately reducing costs.
In this article, we’ll outline the common challenges faced by pharmaceutical facilities, explore the reasons behind the shift towards automated warehouse solutions and introduce storage solutions designed to optimize operations.
Challenges of Pharmaceutical Parts Management
Efficiently managing and storing inventory is key to optimizing the operations for pharmaceutical facilities. However, managing inventory often presents unique challenges that can impact the productivity and efficiency of the operations.
According to the Healthcare Distribution Alliance (HDA), pharmaceutical companies can face a 1-3% loss in sales annually due to inventory mismanagement issues such as stockouts or overstocking, emphasizing the high stakes involved in effective inventory control
Key challenges of pharmaceutical parts management include:
- Temperature and humidity control: Medicines and vaccines require specific temperature and humidity conditions to ensure their potency and efficiency. For example, vaccines should be stored in a refrigerated environment — typically between 2°C and 8°C. Any deviation from this temperature range can lead to the vaccine losing its active components. The Global Cold Chain Alliance (GCCA) also highlights that the global market for temperature-controlled pharmaceutical logistics is growing at an annual rate of approximately 8-10%.
- Security: Pharmaceutical facilities store high-value items, such as medical equipment, which makes them a theft target. Facilities must implement security measures, including access controls and surveillance systems, to make sure these valuable assets are protected around the clock.
- Contamination: Cross-contamination between different medicines can cause degradation of drug efficacy and alteration of drug properties. In addition, allergens or microbial contamination can lead to adverse reactions in patients.
- Inventory tracking: From vaccines to medical equipment, pharmaceutical facilities store a wide range of inventory, encompassing goods with different weights and sizes. Because of this, tracking inventory is key to preventing stockouts, dead stock and mispicks. A 2021 study by McKinsey & Company on the pharmaceutical industry indicated that companies embracing digital transformation, including digital inventory management systems, can achieve up to a 50% reduction in inventory holding costs. These systems improve visibility, forecasting accuracy, and operational efficiency, directly impacting the bottom line.
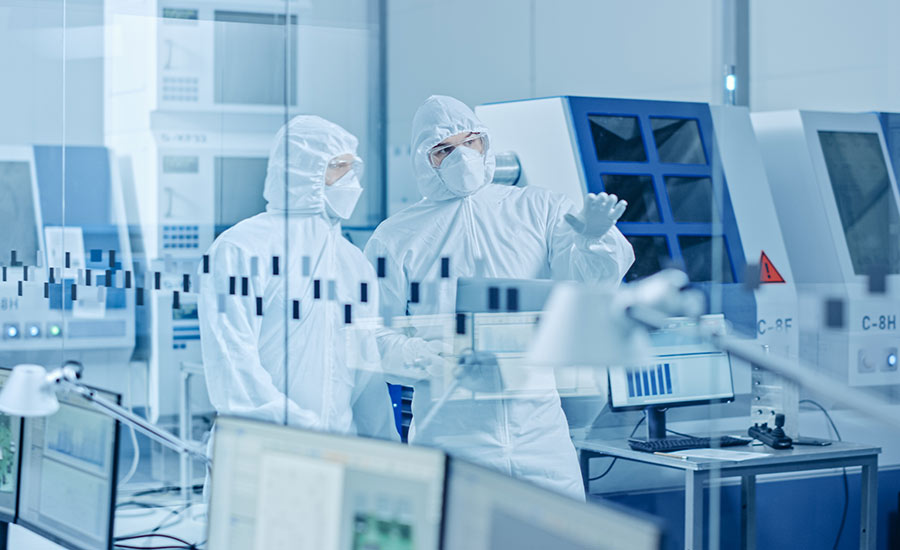
Benefits of Automated Storage Solutions as Pharmacy Storage Systems
One way to tackle these challenges? Investing in automated storage solutions. Many medical and pharmaceutical facilities across the United States are equipped with Modula vertical lift modules (VLMs) and special applications.
Control Temperature and Prevent Cross-Contamination
Thanks to our automated storage solutions for controlled environments, medications and their ingredients remain effective and safe for use.
Modula Climate Control is a vertical lift module (VLM) designed to regulate humidity and temperature, preventing issues caused by temperature fluctuations, such as loss of potency or spoilage.
This temperature controlled VLM effectively manages air circulation within confined spaces and ensures that medications are kept within a temperature range of 36°F to 77°F, with a variation of only 2°F (2°C to 25°C, with a 1°C variation).
In addition, it maintains relative humidity levels at no more than 5%.
But what about the risk of contamination? Modula Clean Room storage system enables pharmaceutical and medical facilities to store materials, such as medications and sterile instruments without a risk for contamination.
The module limits dust and particle generation during operations and prevents existing dust in the cleanroom from entering the storage unit. This system also meets ISO 14644 regulations and complies with class 7 and 8 requirements.
Provide Security Against Unauthorized Access
The risk of unauthorized individuals accessing medications is a serious issue, as it can lead to financial losses and health dangers if these medications are used improperly.
All our automated storage solutions, such as our Vertical Lift Modules, are equipped with a secure locking and validation feature which is vital for different industries.
Each module is password-protected and can only be accessed by authorized personnel using a personal badge or access code. All picking operations are monitored and log-ins are tracked, including specific tray access, based on the selected security level.
For facilities with limited ceiling height, the Modula Horizontal Carousel can provide the utmost safety and security.
Each model features safety doors and is enclosed with 8-foot-high fencing. This design prevents accidents and secures inventory from unauthorized access.
Here are other benefits of VLMs:
- Reduce storage footprint: Save up to 90% of valuable floor space compared to using traditional storage methods
- Increase productivity and accuracy: Quickly identify the items that need to be picked or replenished using simple visual picking aids
- Retrieve inventory at an ergonomic height: Deliver items at the optimal ergonomic retrieval height
- Full traceability and real-time inventory: Monitor and document picking operations to offer full traceability of the parts and products, while tracking stock levels in real-time
- Integrate software: Integrate Modula’s warehouse management system (WMS) with any existing ERP or host systems is a simple process, with no customization required
Gain Complete Inventory Visibility With Modula’s Warehouse Management System
Our VLMs and automated storage solutions for controlled environments can be easily integrated into any existing local IT system, thanks to Modula’s warehouse management system (WMS).
This software provides an accurate and continuous exchange of information with minimal impact on the pre-existing procedures.
As a result, the risk of human error, such as mispicks, is minimized or even eliminated. By harnessing all available inventory data, Modula’s software system facilitates complete control and worker accountability.
Users can monitor stock levels in real-time, speed up order execution times for both picking and replenishment operations and avoid the accidental release of obsolete, expired or on-hold products.
Therefore, medical and pharmaceutical companies can gain the necessary insights to make crucial inventory decisions and reduce unnecessary costs.
Modula’s traceability and validation features, such as the controlled restricted access and barcode verification, are also key features for the medical and pharmaceutical industry where precision, safety and accuracy are paramount.
All VLMs are password-protected, allowing only authorized operators with a personal badge and/or access code entry to operate the machine.
All picking operations are monitored and log-ins are tracked, even down to specific trays, depending on the chosen level of security. Tracking access to specific trays is also beneficial for inventory control, as this minimizes the risk of product theft.
By installing these automated storage and retrieval systems, our medical device and pharmaceutical manufacturing customers have streamlined their operations and reduced unnecessary operating costs.
Automated Pharmacy Storage Solutions Case Study #1: Innomed (USA)
Modula streamlines operations and efficiency at Innomed, a lead manufacturer of surgical instruments for orthopedic surgery based in Savannah, GA.
Thanks to two Modula Lift VLMs, Innomed currently stores over 90% of its inventory within automated storage units.
This allowed them to reclaim the previously used floor space and boost user productivity and ergonomics. Goods are now safely delivered to the operators at the optimal ergonomic work height, avoiding unnecessary bending, walking and reaching for parts.
Watch our video case study of Innomed (USA):
Automated Pharmacy Storage Solutions Case Study #2: Santé Service (France)
The Santé Service healthcare facility is located in France and has over 1,300 patients. The facility chose Modula to increase productivity and accuracy in their picking and storage operations.
With more than 800 packages a day and 1,000 requests per hour to be shipped, Modula’s VLMs were the ideal solution. The two ML25 Lift stored up to 90% of their medical stock, and items were automatically delivered to the operator in a safe and efficient way.
Automated Pharmacy Storage Solutions Case Study #3: Orfit Industries (Belgium)
Orfit Industries is a world leader in the development and production of thermoplastic semi-finished medical devices.
With the introduction of four Modula ML50D Lifts, Orfit significantly increased accuracy and speed in their picking operations — think 40 order lines per hour to over 220 order lines per hour.
Watch our video case study at Orfit Industries (Belgium):
At Modula, we can optimize the operations of your pharmaceutical facility with our state-of-the-art automated storage and retrieval systems and advanced WMS.
Reach out to our expert team for a comprehensive warehouse audit. During this process, we will meticulously assess your current operations and pinpoint areas where our innovative solutions can be seamlessly integrated to enhance productivity, efficiency and accuracy.