A Guide to Inventory Carrying Costs + How To Calculate It
Companies may underestimate their total expenses, including advertising and customer acquisition.
Similarly, while businesses record shipping and handling expenses like postage, they may overlook the comprehensive inventory costs associated with packaging, packing materials and labor required for loading products onto trucks and other necessary actions to fulfill orders.
This oversight highlights the importance of accurately accounting for inventory carrying costs.
In this article, we’ll guide you on how to accurately calculate inventory carrying costs to minimize overall business expenditures.
We’ll also provide practical strategies and advanced solutions that can help streamline operations, enhance efficiency and ultimately save you money.
What Is Inventory Carrying Cost?
Inventory carrying cost, or inventory holding cost, is a KPI that measures the overall expense associated with storing and handling goods over a specific period. They are typically expressed as a percentage of a company’s inventory.
This includes product costs, warehousing, transportation and labor.
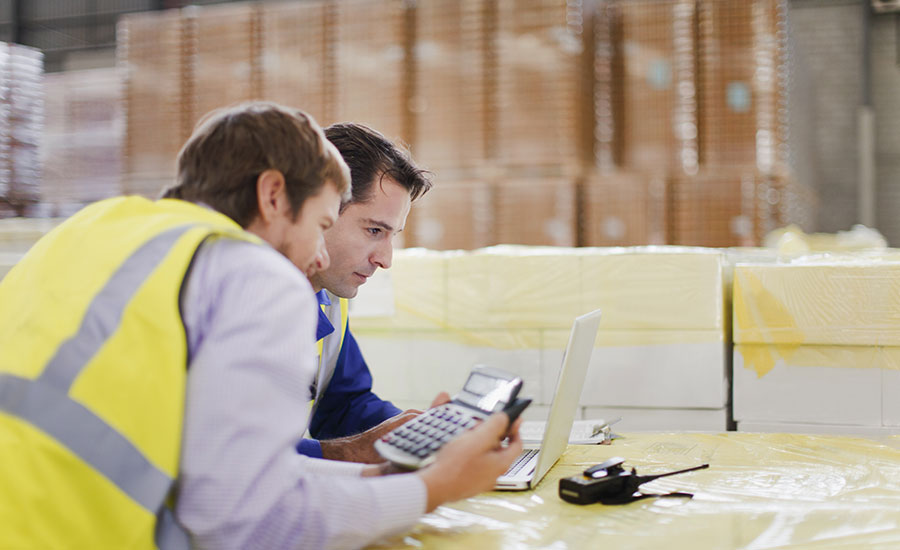
Components of Inventory Carrying Cost
Different expenses play a role in calculating inventory carrying costs, and they often lead to significant financial waste for businesses.
- Cost of Capital: Includes expenses for acquiring inventory funds, such as interest on loans or the opportunity costs of using company resources elsewhere
- Inventory Storage Costs: Include all costs tied to physically storing goods, such as warehouse rent or property costs, utilities and maintenance
- Employee Cost: Covers wages, benefits, and other staff expenses
- Opportunity Cost: Represents the potential revenue waived by allocating resources to inventory rather than other profitable activities
- Obsolescence: Refers to costs that arise when inventory loses value due to natural deterioration or technological advances that change customer preferences
- Insurance and Taxes: Covers costs for insuring inventory against risks and any applicable taxes on stored goods or properties
- Administrative Costs: Refers to expenses related to managing inventory operations, including management salaries, tracking systems and office supplies
- Inventory Shrinkage: Reflects losses from record-keeping mistakes, theft and damage or errors, reducing the available stock for sale
- Material Handling: Includes costs for physically managing inventory, such as moving equipment and labor expenses for handling goods
- Delayed Innovation: Represents costs from postponing investments in new products or enhancements, as resources are allotted to existing inventory
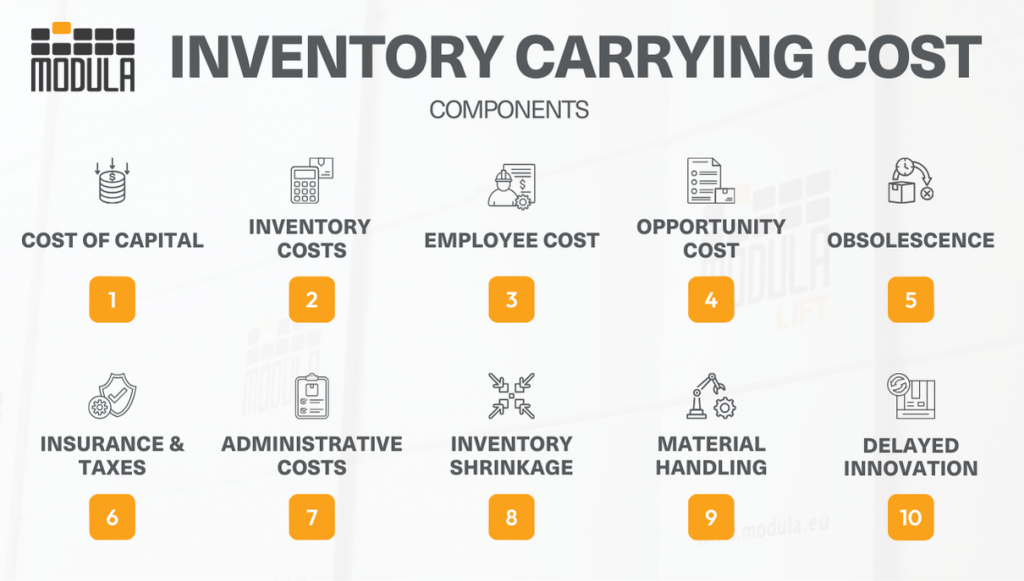
How To Calculate Inventory Carrying Cost
To calculate inventory carrying costs, add the annual expenses for capital, storage, labor, transportation, insurance, taxes, administrative costs, depreciation, obsolescence and shrinkage.
Divide the total by the total inventory value and multiply by 100 to get a percentage.
Inventory Carrying Costs = (Total Carrying Costs / Total Annual Inventory Value) x 100
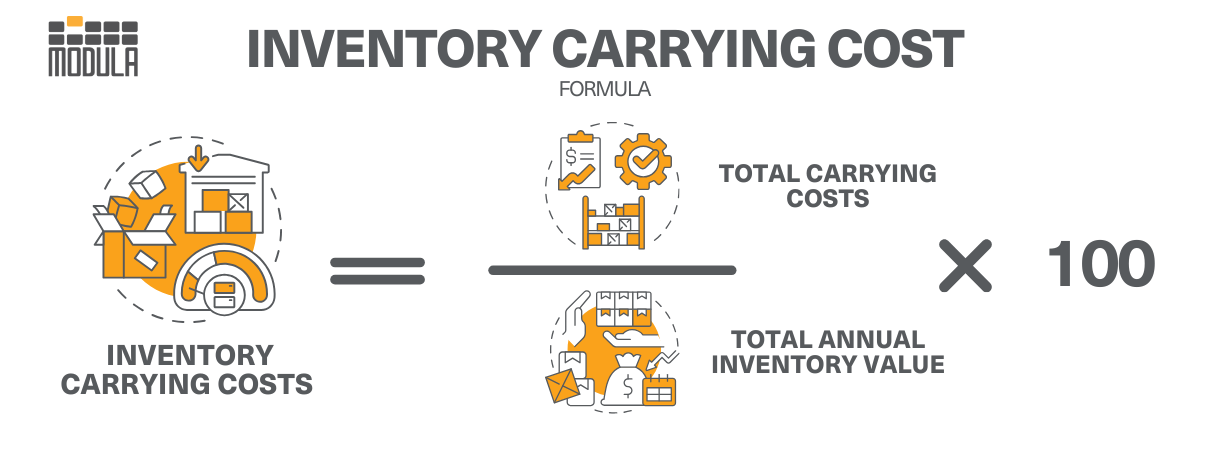
Carrying Cost Example
As summer approaches, an electronics retailer finds itself overstocked with last year’s smartphone and laptop models.
To make room for new arrivals, the retailer calculates its inventory carrying costs: $5,000 in storage, $4,000 in labor, $3,500 for transportation, $1,500 for insurance, and $2,000 for shrinkage and obsolescence, bringing the total to $16,000.
The cost of goods for this inventory is $90,000.
Key Benefits of Calculating the Cost of Carrying Inventory
Holding costs can constitute one quarter of all inventory expenses, and they may impact your business’ overall financial health.
If your organization fails to calculate the cost of maintaining your inventory, you may face cash flow problems.
Other reasons holding costs are important include:
- Production planning: Calculating carrying costs can help businesses make informed decisions on production schedules and resource allocation. For example, a manufacturer may leverage detailed carrying cost data to balance the production of high-demand items with the reduction of overproduction for slower-moving products. This strategy ensures efficient resource use, optimizes storage and reduces costs from excess inventory.
- Profitability analysis: Analyzing carrying costs allows your business to evaluate inventory profitability. This analysis can also help with setting optimal pricing strategies, identifying discountable items and planning promotions that maximize sales without sacrificing profit margins.
- Inventory accounting: Accurately calculating carrying costs is essential for reliable inventory accounting and ensures financial statements reflect true inventory costs. For instance, your company may use precise carrying cost data to adjust its end-of-year financial reports, ensuring that reported inventory values match actual on-hand costs.
How To Minimize Inventory Carrying Costs
Here are seven strategies to help you decrease inventory costs and boost your inventory performance.
Change Your Warehouse Layout
Revamping a facility or warehouse can help boost inventory visibility and diminish the likelihood of overlooked stock and cut costs related to capital, depreciation, obsolescence, insurance and taxes.
For example, rearranging shelves to place high-demand items closer to packing stations can minimize picking time and lower labor costs.
You can also use bins for compact storage or install shelves to maximize vertical space.
Reduce Inventory on Hand
Keeping lower inventory levels reduces storage cost and handling, as it decreases the space required and minimizes the resources needed for managing excess stock.
For instance, a retailer might use sales data to predict demand more accurately, further avoiding overstocking and the associated carrying costs.
Accelerate Inventory Turnover
When you increase the rate at which inventory sells, also known as sell-through rate, you reduce the time products sit in storage.
Compute your sell-through rate with this formula:
Sell-through rate = (Number of units sold during the period / Number of units available at the beginning of the period) x 100
For example, implementing flash sales or discounts on slow-moving items can help clear out inventory faster, improving overall turnover rates.
Negotiate With Your Suppliers
Another strategy to minimize carrying costs is to renegotiate contracts with your suppliers.
Make sure you’re not absorbing the majority of inevitable risks and costs before customers purchase the items.
To give you an idea, structure agreements so that suppliers are responsible for any damage, theft or administrative costs while goods are in their custody.
Implement Just-In-Time (JIT) Inventory System
Adopting a just-in-time (JIT) inventory system can significantly decrease the amount of inventory that you need to store, further lowering carrying costs.
This system requires coordinating with suppliers to deliver goods only as needed in the production process, minimizing the time inventory remains unused.
Improve Demand Forecasting
Utilizing advanced analytics and historical sales data helps your company better predict customer demand and adjust inventory levels accordingly.
Let’s say your company is in the fashion industry. You can analyze past sales trends of seasonal products to accurately predict future demand.
This analysis could lead to stocking fewer winter coats during a mild winter forecast, further minimizing the inventory carrying costs associated with unsold stock and making room for more in-demand spring attire.
Implement a Warehouse Management System (WMS)
A warehouse management system (WMS) that updates in real time offers a bird’s eye view of inventory levels, rather than outdated figures from the previous night or a few hours ago.
A WMS enables smart inventory tracking by enabling a realistic approach to achieving optimal stock levels. It helps employees time new orders accurately and track metrics such as inventory turnover and sales volume.
Additionally, a WMS streamlines fulfillment and shipping processes, making them faster and more cost-effective.
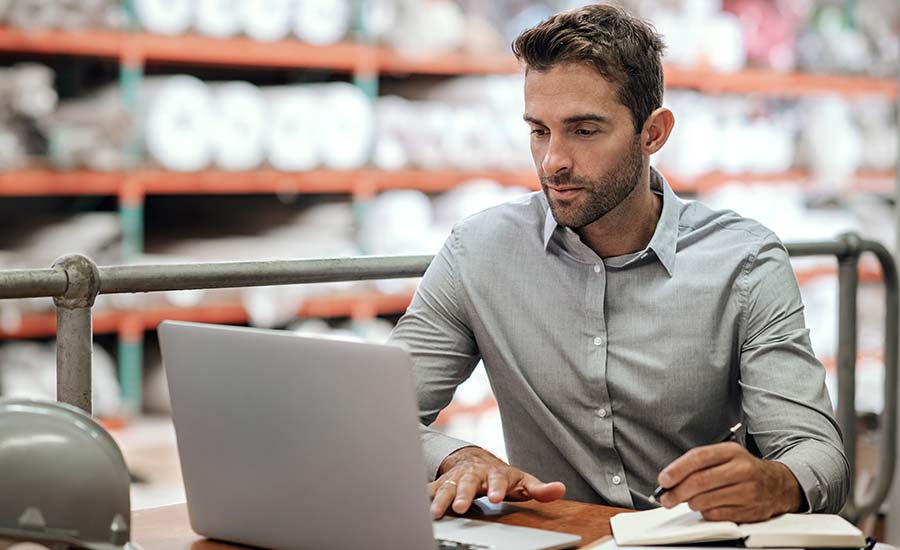
Scale Down Inventory Carrying Costs With Modula’s Warehouse Management System
One of the most effective strategies your business can use to cut back on inventory carrying costs is to implement a warehouse management system. This technology reduces related costs by offering various ways to optimize inventory levels.
The transparency an inventory management system provides is invaluable for any product-based company.
It enables purchasing, operations and supply chain professionals to make more informed decisions by tracking current stock levels and all pending purchase and customer orders.
Modula’s warehouse management system (WMS) can help your operations streamline processes, enhance accuracy and improve efficiency by automating inventory tracking and optimizing storage layout.
This leads to quicker retrieval times and reduced labor costs, effectively lowering overall inventory carrying costs.