Worker safety and productivity in the face of COVID-19
How to solve warehouse worker safety and productivity problems posed by the pandemic
As the pandemic has swept across the world in the past few months, the necessity – and the dangers – of fully operational warehouses have come into public view as never before. Consumers have come to appreciate the critical role that a well-functioning supply chain plays in getting the items they need. And they’ve learned that items they want, but deemed “non-essential,” may not be available for months.
At the same time, news accounts of problems at warehouses, such as those at Amazon and Safeway, are getting attention due to worker concerns about their own safety. Unions are calling for strikes in response to employees being infected by the virus while on the job.
Is there a way that warehouses can protect workers and, if necessary, stay just as productive even as some employees are unable to work? Absolutely.
The advantages of a Vertical Lift Module for warehouse worker safety
In a traditional warehouse, workers are sent to retrieve items stacked on shelves across a massive facility, passing each other many times a day.
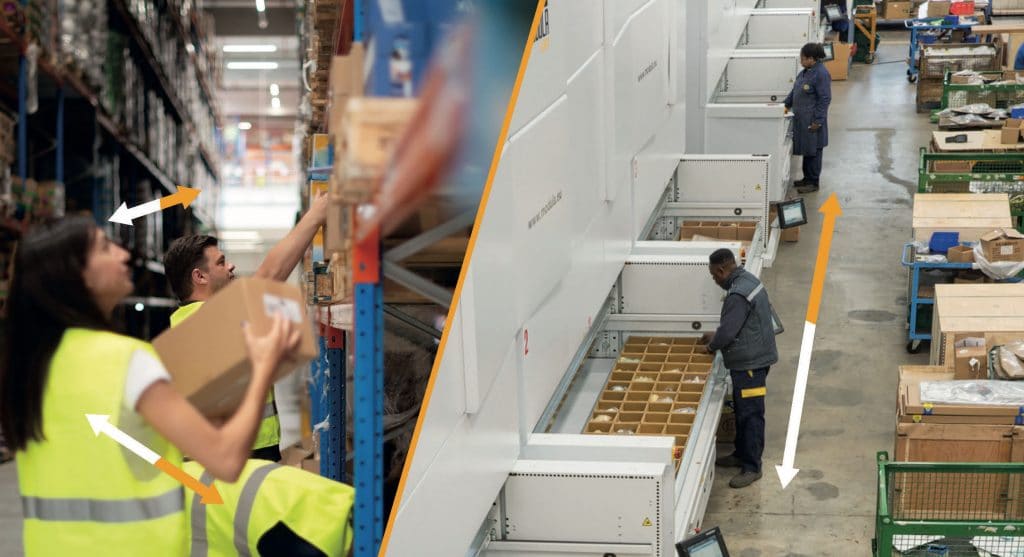
With the pressures added to ship more items to keep up with demand and meet production quotas, warehouse managers are likely to hire even more workers if they can.
This makes a bad situation worse in terms of COVID-19. Having more and more people scrambling up and down aisles makes it all but impossible to maintain six feet of distance between them without drastically reducing productivity.
What if instead of the workers going to the goods, the goods came to the workers?
This is the basic idea of a vertical lift module or VLM. Items are stored in a tall, efficiently packed machine, and a worker touches a screen to withdraw the required items. Now a worker can stand at the machine and retrieve all the parts needed without walking around the floor and passing by other workers — making it easy to adhere to the six-foot minimum distance.
Besides the advantage of social distancing, workers are safer using a VLM than they are in a traditional warehouse. The goods are delivered to them at chest height – there are none of the ergonomic problems caused by reaching high or low to pull a heavy item from a shelf. This enables workers to avoid injuries that would force them to leave the workforce temporarily or even permanently. The experience is far more pleasant for workers overall, making job turnover less of a factor than it tends to be in warehouses.
(Reported turnover averages are typically 30% or more annually even without the effects of a pandemic!)
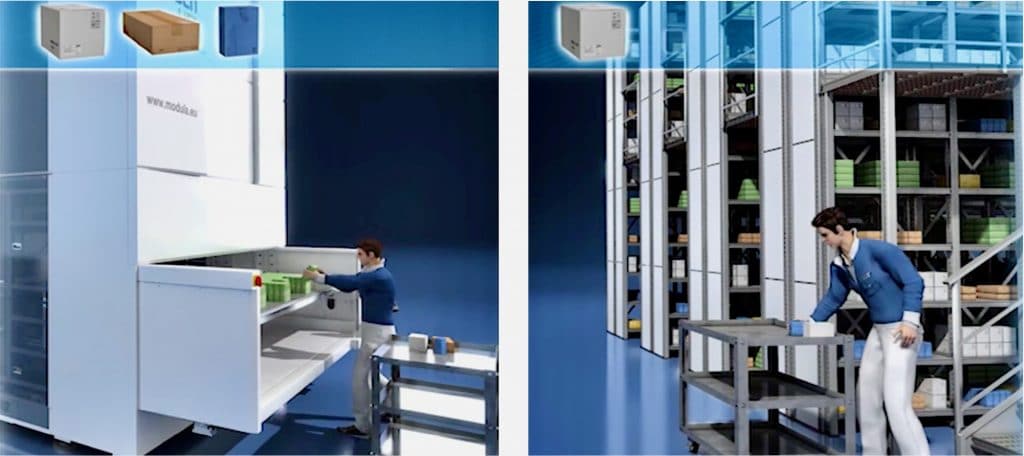
Reduce Picking errors
With the high pressures to boost productivity that many warehouses are now feeling, another weakness of traditional warehouses is exposed: mispicks.
Sending customers, the wrong item, too many items, a damaged item, or failing to send one at all is expensive. Estimates are that each mispick costs a company between $25 and $100. Add it up and it can represent the loss of tens or hundreds of thousands of dollars a year.
A VLM eliminates that issue. Pick-to-light systems and laser pointers quickly guide workers to select the right item, cutting out common errors that arise when humans have to make repeated judgment calls all day.
As long as information about an item has been entered accurately when it’s placed in the VLM, a worker will get the right item each time the order is fulfilled.
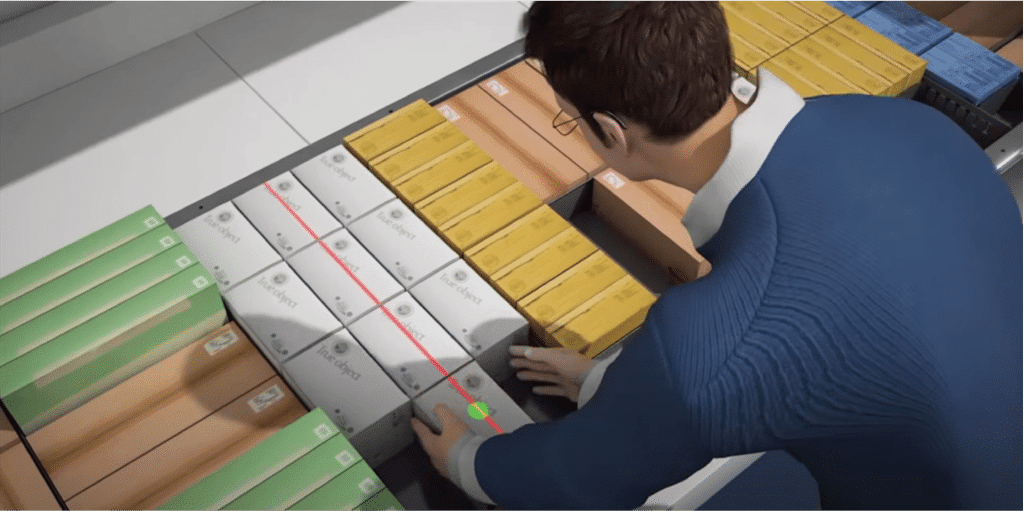
Cut warehouse size while maintaining productivity
Additionally, employing VLMs instead of traditional shelving in a warehouse can reduce the total footprint by 90 percent. So a much smaller warehouse is just as productive as its larger counterpart. Companies that have the option of downsizing to a smaller space can save on fixed as well as variable costs. Conversely, existing warehouse space can be far more productive by replacing a shelf system with VLMs.
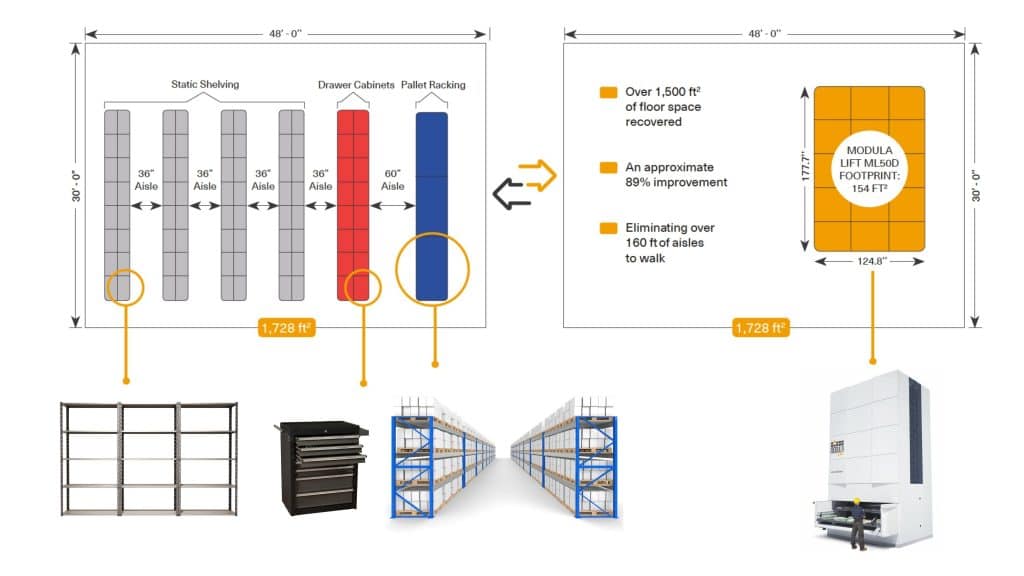
Floor Space Utilization: Automated Storage Systems vs. Traditional Static Storage Methods
Overcome Staffing Shortfalls
And finally, the pandemic is creating disruptive forces that are hard to control now and may continue to be challenging in the future. In recent years, it’s been tough enough to hire and retain warehouse workers, and that isn’t likely to abate. So automated systems such as VLMs and accessories that connect them digitally with the rest of a supply chain can make a warehouse more efficient, even with staffing shortfalls. The health and safety of workers will continue to be a concern for warehouse managers, and the need for greater productivity is never going to end.
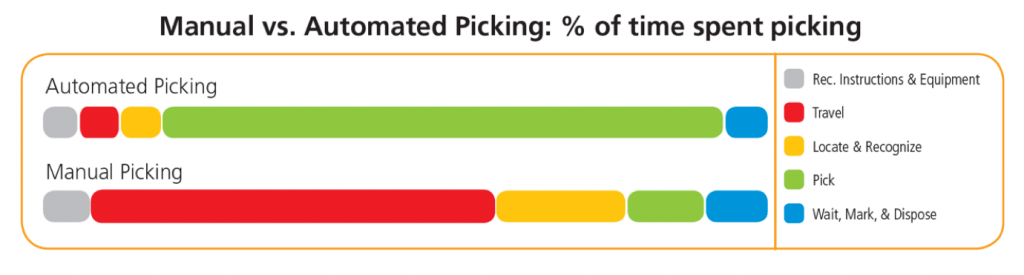
Contact us to find out more