Overcoming the labor shortage problem with automation
An automated storage solution may be just what your company needs to address the labor shortage problem.
As the most severe effects of the pandemic lessen and warehouses and factories ramp up their activities, there’s an obstacle that managers are facing across the U.S.: a severe labor shortage.
Finding warehouse workers in particular has been an issue for years. But companies have been surprised to find that despite many new job openings, applications have been slow in coming.
As Barron’s reported, there were twice as many manufacturing job openings in April 2021 as there were in the year before the pandemic and more openings in American manufacturing companies than at any point since the 1990s. Open positions were up by 30% from the pre-pandemic average in transportation, warehousing, and utilities as well, Barron’s said.
Part of the reason may be that workers don’t want to return to the jobs they had before that they didn’t like. A Pew Research Center survey showed that 66 percent of the unemployed had seriously reconsidered their field of work – a far higher percentage than during the Great Recession. “They may just want more pleasant work that they had before, including safer work,” the Washington Post noted in a story titled, “It’s not a labor shortage. It’s a great reassessment of work in America.”
Fortunately, there are automated storage systems that can help address the labor shortage issue such as Modula’s vertical lift modules (VLMs) and horizontal carousels (HCs). Let’s look at how they do so.
Creating a more efficient and safer environment with automated storage solution
The traditional shelving systems that many warehouses and factories use to store goods are not an ideal work environment. Workers need to spend their days walking back and forth through the aisles and stooping low or reaching high to retrieve items. Sometimes they need to climb ladders or other mechanical means to retrieve high items. At best, this causes stress and strain. At worst, it can lead to serious injuries.
A Modula automated storage solution eliminates that problem. Rather than having workers go to items, items are delivered to the workers. Parts are presented at an ergonomically proper height to allow workers to retrieve them or restock them. And with inventory automatically tracked by the machine, the work is mentally easier as well as the machine makes certain the right part is picked, not the worker.
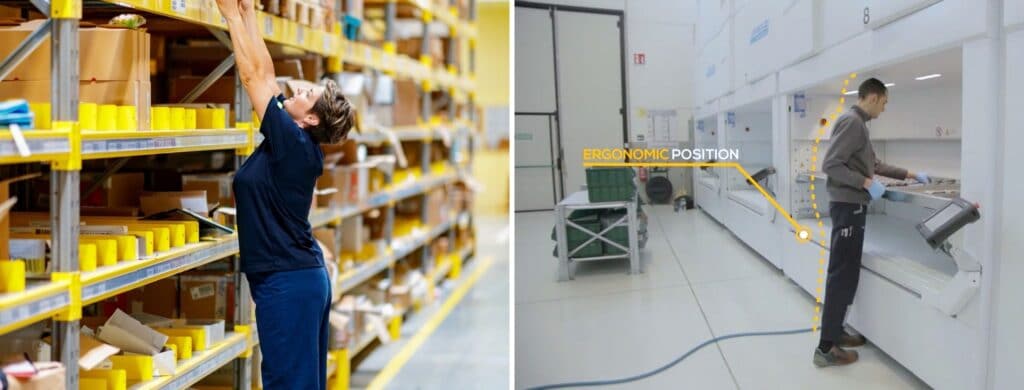
Industry studies have shown that vertical storage solutions can increase workforce productivity by up to 85% as one worker is able to handle the same volume of work previously performed by multiple operators. Compared to traditional static shelving systems, employees are primarily busy in the value-added picking operations, as they are not forced to walk up and down aisles or climb up and down stairs or ladders.
Watch our case studies videos to learn how companies that have installed Modula storage systems are seeing dramatically improved results in operational efficiency and worker satisfaction.
Higher throughput and greater picking accuracy with AS/RS
As e-commerce becomes increasingly popular, the pressure on warehouses to fulfill orders grows. This means faster and faster turnarounds – and a more exhausted workforce. It also leads to more mispicks and the higher costs of handling returns and dissatisfied customers associated with shipping the wrong item.
Modula’s VLMs and HCs can dramatically speed up productivity – five times as fast or more. Picking rates of 300 lines an hour or higher are par for the course. And because inventory is controlled automatically, with visual aids such as lasers indicating to operators what items to pick, mispicks are reduced to virtually nothing.
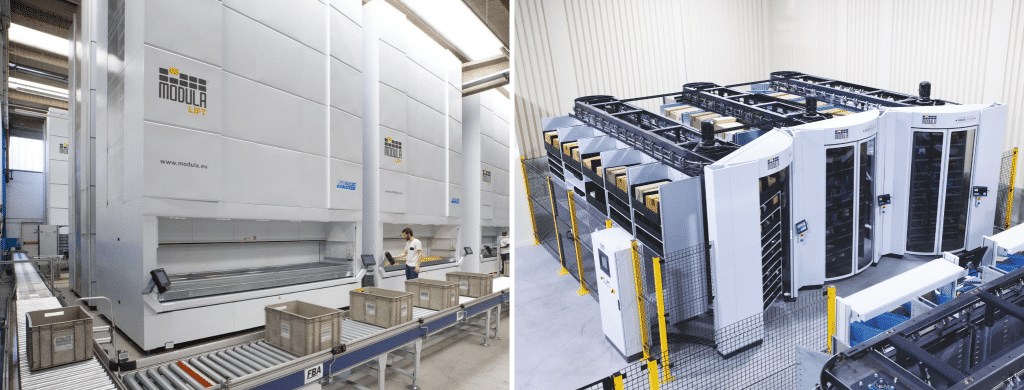
Same efficiency and productivity even with staffing shortfalls and reorganized shifts
Modula vertical storage systems are the best solution to guarantee operational continuity and productivity in any situation. Especially during these challenging times. Thanks to the high efficiency of Modula’s dual-bay delivery system and the pick-to-light systems, fewer resources are needed to process the same number of orders. Within 30 minutes of training, anyone can productively and safely operate a Modula storage system. Efficiency is not affected, even with staffing shortfalls and reorganized shifts.
Greater storage efficiency with full control over your inventory
Moving from a traditional system to an automated storage solution from Modula can reduce the floor space needed in your warehouse or factory by up to 90%. That means you may be able to consolidate space for other revenue-earning activities, reduce your monthly lease costs or avoid moving to a larger facility.
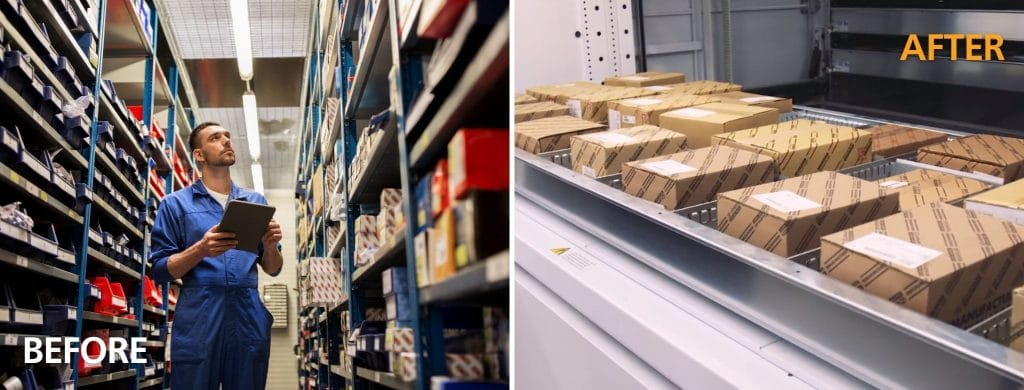
Moreover, with automated storage solutions, warehousing and manufacturing facilities have full control over the processes as all operations are tracked and monitored. They can look ahead at the upcoming production or orders to ensure efficient staffing and eliminate unnecessary overtime.
An ROI in 6 to 18 months
Many customers are surprised by how quickly one of our units pays for itself. But given the advantages it provides in terms of throughput, accuracy and storage efficiency – to say nothing of overcoming labor shortage issues – it’s not surprising that the ROI is so fast. We say it typically takes about a year for one of our units to pay for itself, but it can be slightly longer or slightly shorter as well.
The best way to know how a Modula automated storage system can benefit your business is to contact us. Complete our form and one of our trained sales advisors can describe what solutions would be best for your business.