What Is WMS Integration? [Types + Key Benefits]
A warehouse management system (WMS) is an innovation that primarily acts as the brain of your warehouse operations.
It can manage complex warehouse tasks, such as picking movements, location tracking, and inventory control, enhancing overall efficiency.
However, a WMS alone can’t reach its full potential.
One of the biggest benefits of cloud-based WMS is its ability to seamlessly integrate with other technologies and software, streamlining warehouse processes, such as
A recent industry report highlights technology transformation as a key trend this year, with the market for cloud-based WMS continuing to grow. However, without proper integrations, this technology remains underutilized.
In this article, we’ll explain all you need to know about WMS integration, from its definition to the different types, and share how Modula’s WMS can help your business.
What Is WMS Integration?
A Warehouse Management System (WMS) is a software that streamlines and centralizes all operations within a warehouse, from receiving goods to final shipment. Acting as a central hub for your supply chain, a WMS offers real-time visibility into inventory levels across your warehouses and even those in transit. This comprehensive view goes beyond just inventory management. WMS software equips you with tools to optimize picking and packing processes, maximize resource utilization, and generate valuable data analytics.
Warehouse management system integration, or WMS integration, is the process of connecting the system to other business solutions.
Business software systems include Enterprise Resource Planning (ERP), Distribution Management System (DMS), Customer Relationship Management (CRM), accounting software and eCommerce platforms.
These integrations facilitate seamless communication and data flow between the warehouse and other business functions, optimizing inventory management, order processing, shipping, and customer service.
For example, WMS integration allows you to automatically update inventory data across your systems, ensuring that inventory information remains accurate and consistent.
5 Types of WMS Integration
WMS integration involves connecting your warehouse management system with various other business systems to streamline operations, enhance data flow, and optimize overall efficiency. Here are the key types of WMS integrations:
Accounting and ERP Integrations
Accounting and ERP integrations connect your WMS with accounting software (e.g., accounts payable/receivable systems) and Enterprise Resource Planning (ERP) systems.
These integrations ensure that financial reporting is accurate and reflects the latest business activities, such as sales orders and inventory changes.
Additionally, A WMS also automatically captures all billable events, such as receiving, storage, picking, packing and shipping fees, and generates invoices for each customer at the end of the billing period.
Integrating with accounting systems also allows you to quickly consolidate invoices into a single monthly statement, which can then be sent to customers for payment.
Electronic Data Interchange (EDI) Integrations
Electronic Data Interchange (EDI) integrations facilitate the electronic exchange of business documents, such as purchase orders, invoices, and shipping notices, between the WMS and trade partners.
This type of integration standardizes data communication to improve transaction speed, accuracy, and business efficiency. This eliminates the need for manual data entry and the potential errors associated with it.
Marketplace or Shopping Carts Integrations
Integrating WMS with online shopping carts and marketplaces streamlines the order fulfillment process directly from the sales platform.
This setup automatically updates inventory levels and the order status on both the WMS and the online marketplace, enhancing customer satisfaction with accurate, real-time information.
For example, if you have an e-store, you can connect your WMS via API to automatically send orders directly to the WMS as soon as they come in, complete with all the order details.
This eliminates the need to take orders over the phone and manually enter shipping information.
Mobile Barcode Scanning
Integrating your WMS with mobile barcode scanning allows your system to recognize scanned barcodes as inputs across different platform fields, such as inventory tracking and quality checks.
For example, during picking, you simply scan the item’s barcode, and the system immediately marks it as picked.
There’s no need to manually record long SKUs, UPCs, or serial numbers, as the system can capture all this information with a single scan.
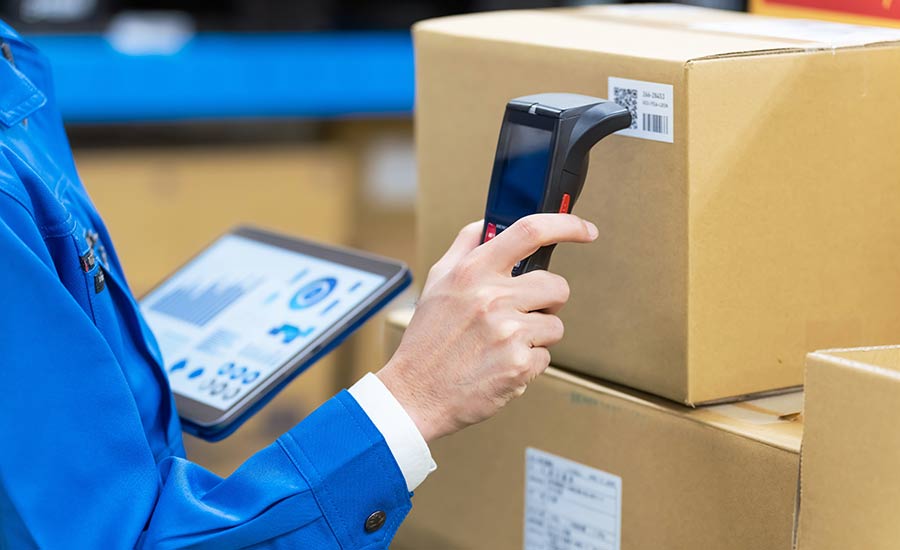
Shipping Carrier Integrations
Shipping carrier integrations connect your WMS with various shipping carriers, including FedEx, UPS, DHL, and USPS.
This type of integration automates the creation of shipping labels, tracks shipments, and updates order statuses, reducing manual errors and improving delivery times.
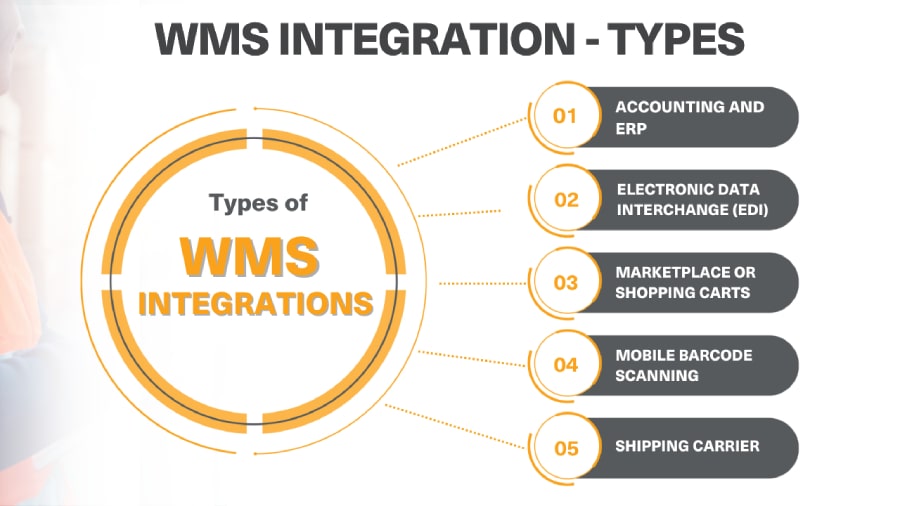
Key Benefits of WMS Integration
WMS integration provides numerous benefits, streamlining operations, enhancing accuracy, and improving customer service.
Here are some of its key advantages:
- Enhanced inventory management: Integrating your WMS with ERP systems allows for real-time inventory tracking. For example, when you sell a product in a digital storefront, the inventory levels are automatically updated across all platforms. This can help prevent over-selling or stockouts.
- Efficient order processing: Connecting your WMS with an order management system allows businesses to automate the order fulfillment process. For example, when a customer places an order, the WMS immediately generates a pick list — a document that warehouse pickers use to fulfill customer orders — then allocates the nearest available stock, speeding up delivery times.
- Increased visibility: With all data consolidated in one place, warehouse managers can gain a comprehensive view of their warehouse operations. This can help them identify potential issues before they escalate, optimize the layout and flow of goods, adjust staffing levels to meet demand, and refine inventory levels to reduce holding costs.
- Improved accuracy in shipping: WMS integration with shipping software automatically generates shipping labels and documentation based on the latest order information. This process minimizes errors in manual entry and improves the accuracy of shipment tracking. For example, the WMS automatically selects the most cost-effective shipping method based on the destination and weight, updates the system, and then notifies the customer.
- Improved customer satisfaction: Seamless integration between WMS and CRM systems can significantly enhance customer service. For example, customer service representatives can access real-time information about order status and stock levels, enabling them to provide customers with timely and accurate updates on their orders.
- Cost control and financial insight: Integrating your WMS with financial software can help in accurately tracking costs associated with warehouse operations, such as labor, storage and shipping. For example, by analyzing data from both WMS and financial systems, you can identify areas in which waste is occurring, such as excessive packaging materials or inefficient use of warehouse space.
More on WMS and ERP Integration?
WMS (Warehouse Management System) and ERP (Enterprise Resource Planning) integration is a critical aspect of modern supply chain management. This integration allows for seamless communication and data exchange between warehouse operations and other business processes managed by the ERP system.
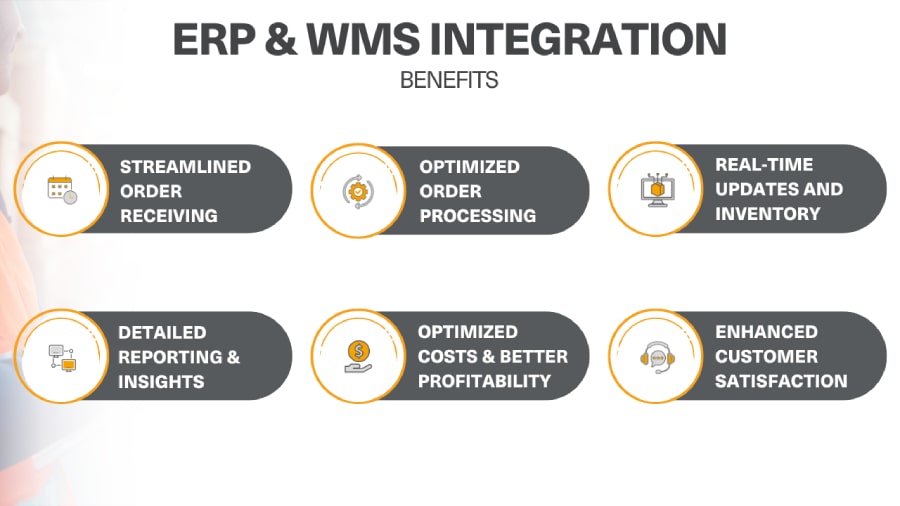
How Your ERP and WMS Can Work Together
The collaboration between systems enhances the efficiency of business processes, from the moment an order is created in the ERP to when it’s fulfilled in the WMS.
Here are some examples that illustrate how WMS and ERP integration can help optimize your warehouse operations:
- Receive customer orders: The ERP system creates sales orders and forwards them to the connected WMS to allocate inventory and fulfill orders.
- Process orders: Upon receiving customer orders, the ERP system ranks them based on the type of order, customer priority, and delivery deadlines. It then communicates this information to the WMS. The WMS uses these details to organize and schedule picking and packing tasks and assigns workers to specific orders.
- Obtain real-time updates: The WMS gathers updates on inventory levels, stock movements, and order statuses and relays this information to the ERP system. The ERP uses these updates to manage inventory and process orders efficiently.
- Generate warehouse reports: By working together, the ERP and WMS systems produce reports that offer crucial insights into warehouse operations, financial performance, and other key metrics.
- Manage operation costs: The ERP system supplies cost data, pricing, and financial details to the WMS, which uses this information to calculate costs and margins.
Optimize Your Warehouse Operations and Beyond with Modula’s WMS
The Modula Warehouse Management System (WMS) is designed to manage Modula’s automated storage and retrieval systems (ASRS) or other smart warehouse solutions.
It can also function as a stand-alone software in traditional, manual warehouses.
As one of the market’s most intuitive and advanced software solutions, Modula WMS easily integrates with nearly all ERP and DMS systems.
This integration speeds up and improves the accuracy of processes like receiving, picking, and storing products.
Here’s how it works:
- You need one PC as the warehouse server and additional PCs for staff access.
- As your operations grow, you can easily add more PCs.
- Once installed, the WMS is ready to use and can seamlessly connect with any corporate ERP system.
Key benefits of our WMS include:
- Maintain item records, assign unique identifiers, monitor item movement, and keep tabs on stock levels.
- Optimize and prioritize orders. Monitor the entire order process, including processing, shipping, and delivery.
- Manage the placement and movement of products within your warehouse. Establish and maintain location codes and labels.
- Assign tasks, set access levels and permissions, and monitor user activity to manage staff effectively.
- Keep an eye on system performance. Identify and fix errors, generate reports and alerts, and analyze key statistics.
- Seamlessly connect and exchange data with other systems and software, either through direct data entry or by importing and exporting files.
At Modula, we offer cutting-edge automated solutions to streamline your warehouse operations.
Reach out to us to discover how our technology can work for you and your team. Our specialists are ready to provide tailored advice and solutions to meet your specific warehouse needs.