Vertical carousel vs vertical lift module: Know the differences to make the right choice
Quick, off the top of your head: What’s the difference between a vertical carousel and a vertical lift module? If you said they’re the same thing, you’re not alone. Even those who own vertical lift modules sometimes mistakenly refer to them as vertical carousels. But there are important differences worth understanding if you’re in the market for an automated, vertical storage system. In this article, we’ll explore the mechanical, operational, and cost differences to help you make an informed decision.
A quick comparison of a vertical carousel and a vertical lift module
Introduced in the 1950s, a vertical carousel is like a Ferris wheel that stores small items and rotates to deliver them. It consists of trays attached to a chain that rotates.
It is primarily designed to carry items of similar size and weight. You might have heard it described as a storage carousel or vertical rotating shelf system – to differentiate it from a horizontal carousel.
A vertical lift module has a more advanced design and operates like a vending machine in which items can be retrieved without rotating everything stored inside. An inserter/extractor grabs individual trays from where they sit in the machine, delivers them to a bay, and then returns the tray to its initial position.
Because the vertical carousel came first, that term seems to have stuck for the entire category. For our purposes, we’ll just abbreviate the two: VC for vertical carousel, VLM for vertical lift module.
In the majority of applications, VLMs have clear advantages. They are more space-efficient, can carry heavier objects and more overall weight can typically operate more efficiently, and are readily modified if there are changes in the types of items being stored.
VCs can be used effectively primarily when an organization needs daily access to records, such as a healthcare organization accessing patient files. If the organization doesn’t need daily access to such files but instead requires long-term storage, a VLM is far better. Thanks to a height-detection system, the height of the products in the tray is measured as the tray is put away, allowing the densest storage location to be determined in real-time.
Vertical Carousel vs. Vertical Lift Module: Key Differences
- Unlike vertical carousels which have to be balanced so all of the weight doesn’t end up on one tray, vertical lift modules don’t have to balance weight and can retrieve items faster.
- The shelves on a vertical carousel cannot be adjusted, so when tall items are stored on the same shelf as small items, space can end up being wasted. Vertical lift modules can have trays of different heights, so waste storage isn’t an issue. For example, small items can be stored in one tray, while larger items can be stored in another tray.
- Vertical carousels are limited to heights of about only 25 feet due to balance issues while vertical lift modules can reach up to 50 feet or more.
- Vertical carousels require the entire set of shelves to move, which can affect productivity and efficiency, unlike vertical lift modules.
- Vertical carousels are less flexible to install because their end frames are one solid piece and are not always easy to move into a location, while vertical lift modules come in separate pieces that can be easily transported. A VC will usually take up to four days of installation while a VLM can be installed in only two days.
6 Advantages of a Vertical Lift Module
Like vertical carousels, the main function of a vertical lift module is to safely deliver and retrieve items in your warehouse, but with additional and more advanced features.
Here are six advantages of a vertical lift module:
1. Maximizes Your Storage Potential
Vertical lift modules can easily accommodate items of different sizes and automatically adjust trays to maximize vertical carousel storage density.
At Modula, the trays in our modules are built to accommodate heavy loads without strain.
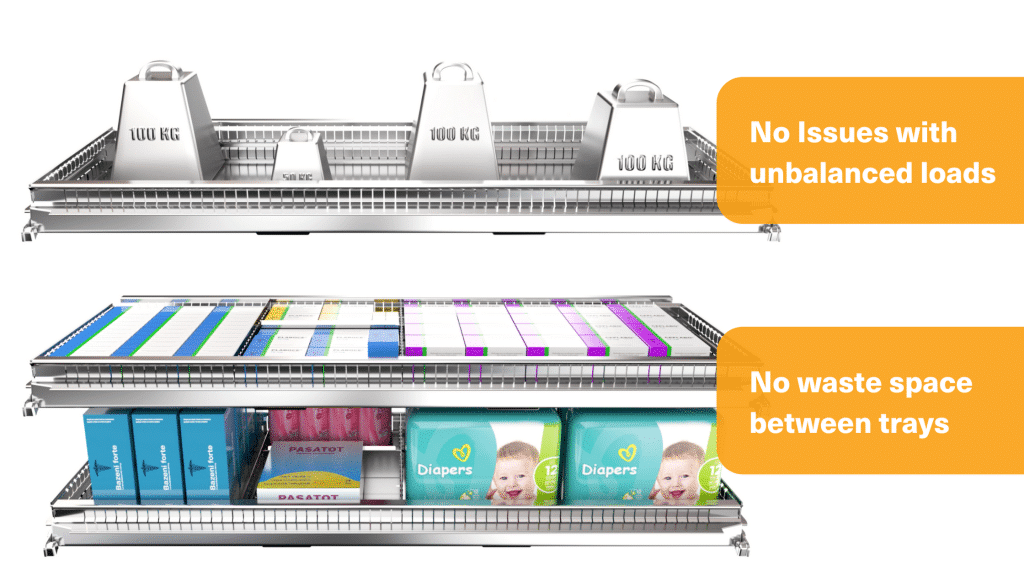
2. Saves Space in Your Warehouse
According to a 2021 recent survey, 36% of respondents said that insufficient space for inventory is one of the biggest challenges warehouse operators face.
Vertical lift modules help you save space in your warehouse by taking advantage of high ceilings.
The result?
An organized warehouse with increased free space that can be dedicated to more storage.
At Modula, our Vertical Lift Module uses only 150 square feet of your warehouse footprint, in contrast to 9,050 square feet of traditional storage.
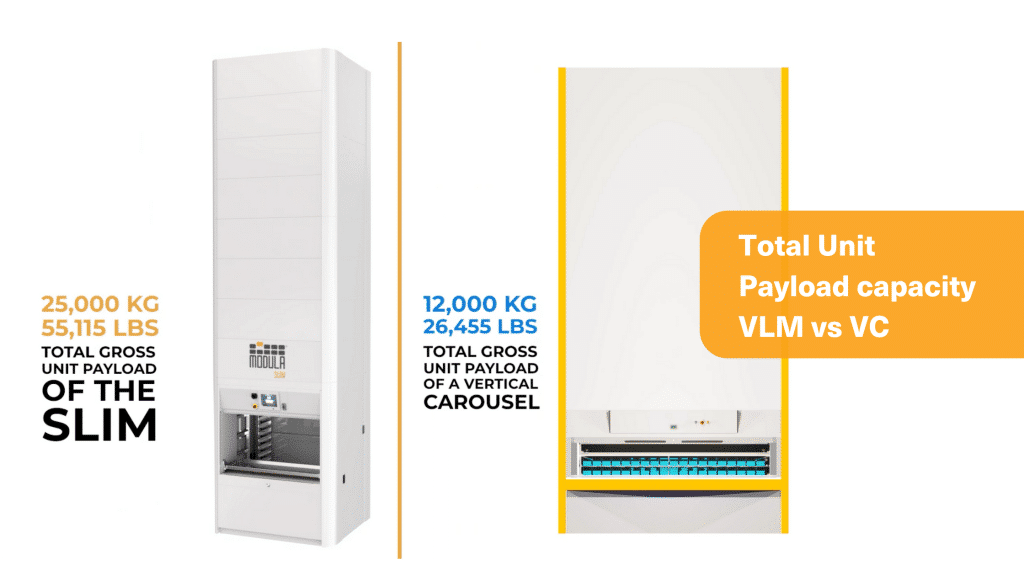
3. Increases Picking Efficiency and Speed
According to a 2017 survey, lack of speed ranks second as the most common cause of customer service frustration.
Vertical lift modules can save you time in picking items, since you don’t need to wait for the entire set of trays to move – just the tray holding the item or goods.
With the greater range of visual aids that they can provide (for example, laser pointers to indicate where the needed item is located), vertical lift modules provide faster and more accurate retrieval for your operators.
At Modula, our Modula Lift modules offer picking speeds of 300 lines per hour or more.
4. Provides a Safe and Efficient Working Environment
A 2017 study found that there’s a direct relationship between injuries and fatigue at the workplace.
With warehouse operators frequently reaching high and low to store and retrieve items, the risk of injuries in a warehouse is prevalent.
So how can a vertical lift module reduce the risk of injuries in your warehouse?
By eliminating the stress of reaching high and low, our Modula Lifts provide an ergonomic working environment for your employees.
Instead of traveling to items, your items will come to you.
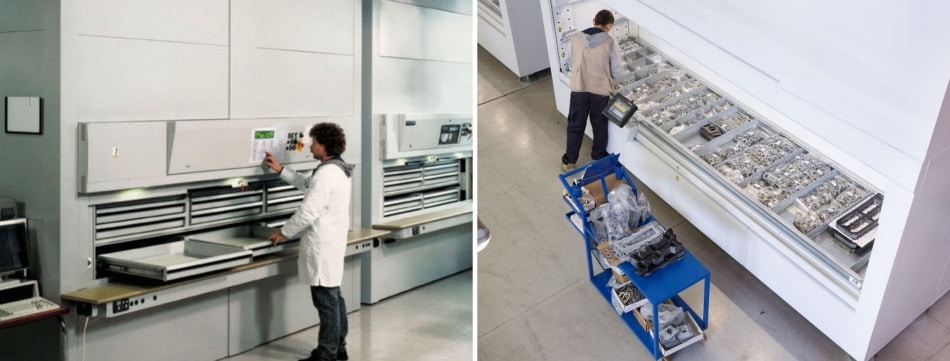
Vertical lift modules provide a safe and efficient working environment for your warehouse operators
5. Increases Security While Providing Clean Storage for Your Products
Concerned about product safety?
Our vertical lift modules offer a safe and clean space for your items.
Your items will be stored in a fully enclosed system which prevents them from being damaged or exposed to dust.
Plus, only designated employees will have access to them.
Disadvantages of Vertical Carousels, Old and New
Since vertical storage carousels have been around longer than vertical lift modules, they are relatively abundant and often sell at relatively low prices on the used market.
However, disadvantages include the installation obstacles of merely getting the vertical storage carousel into your facility, as they are installed as one unit and can’t be installed in sections.
Plus, you’ll need to have the machine certified for safety. And while the external surfaces might look fine, the inner workings might not be up to par on a used model.
Worn parts, bad circuit boards and problematic wire harnesses can lead to hidden costs that make a used vertical carousel much less of a bargain than it might appear.
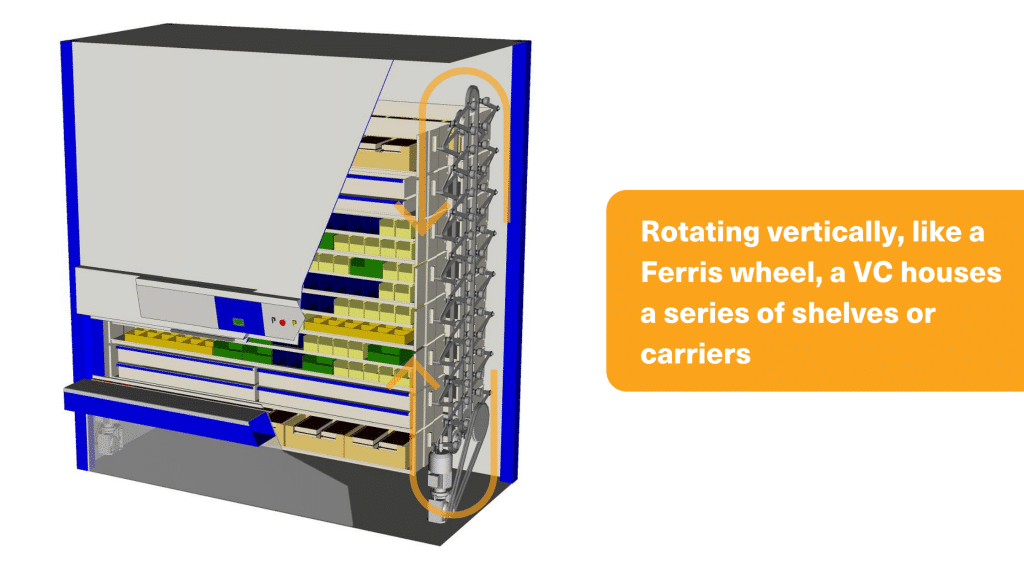
What about brand-new vertical carousels?
Think about how you get on and off a Ferris wheel. Passengers are seated in one capsule to ensure the load is evenly distributed along the wheel, then the wheel is rotated 180 degrees to load the next set of passengers.
If all the passengers were loaded in adjacent capsules consecutively, the wheel would quickly become unbalanced and the Ferris wheel would tip over.
The same goes for loading a vertical carousel.
Items need to have identical weights to avoid load imbalances and should have similar sizes to optimize the storage space, since the tray positions can’t be changed.
A vertical carousel can also only reach a maximum of about 25 feet.
Why choose outdated technology when the market offers a much more sophisticated and efficient solution?
Our verdict: Vertical carousels aren’t worth the purchase, considering these pitfalls.
See also: 10 Disadvantages of Vertical Carousels
What Is the ROI for Vertical Carousels and Vertical Lift Modules?
The price of a new vertical carousel and a vertical lift module is roughly the same.
But considering the previously mentioned benefits that come with a vertical lift module, you’ll see a quicker ROI for vertical lift modules than a vertical carousel.
It’s the clear winner in overall efficiency.
That, in turn, means a quicker ROI and a machine that will serve your needs not just now but in the years to come.
Vertical Lift Modules: Automated Storage Solutions at Modula
At Modula, we offer automated vertical lift modules that take up a minimum footprint in your warehouse by utilizing the ceiling height available.
Our systems allow your warehouse operators easy access to your large inventory of goods while being stored in a secure and safe environment.
Items will be automatically delivered to you operators with a simple touch on the user-friendly Copilot controller or with the scan of the barcode.
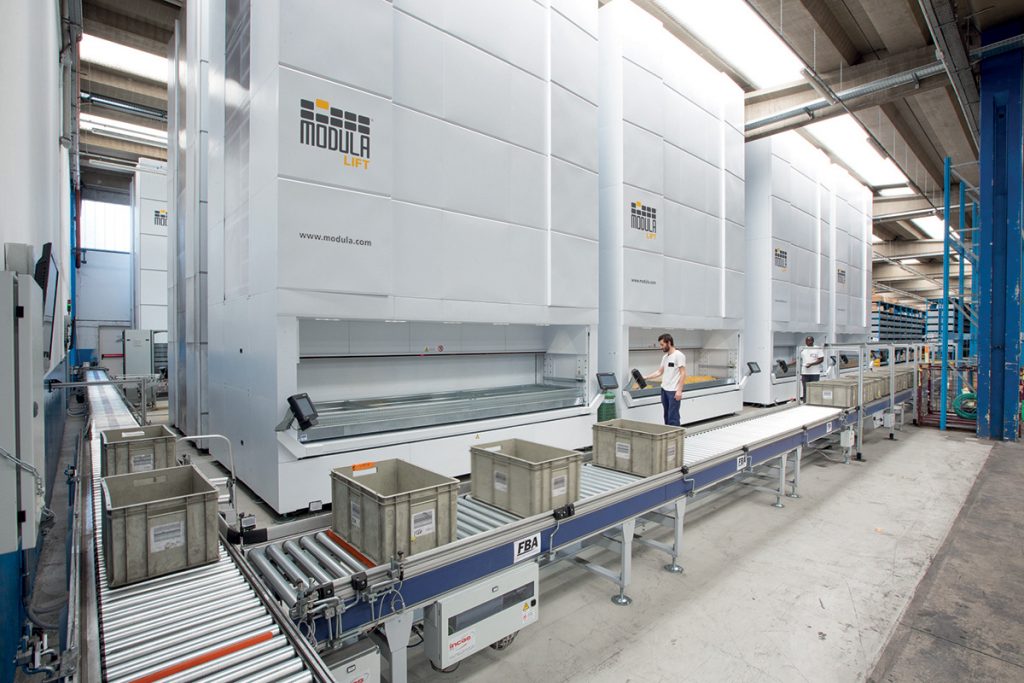
At Modula, we offer two vertical lift modules:
- Modula Lift: Considered our most popular vertical lift module, Modula Lift is available in a wide array of capacities and sizes, used by businesses to modernize their operations.
- Modula Slim: This vertical lift module is designed to fit small spaces with similar functionalities as Modula Lift.
When you purchase one of our vertical lift modules, you benefit from:
- Increased productivity and efficiency
- Drastically reduced picking errors
- Accurate delivery of the right item to the right person
- Optimal ergonomic retrieval height of items
- Real-time location of items in your warehouse inventory
Wrapping Up On Vertical Carousels & Vertical Lift Modules
Vertical carousels may have been around longer than vertical lift modules, but the advantages you can reap from VLMs are clear.
The advantages of a vertical lift module include:
- Maximizes your storage potential
- Saves space in your warehouse
- Increases picking efficiency and speed
- Provides a safe and efficient working environment
- Increases security while providing clean storage for your products
At Modula, we help you reimagine your storage solutions with our advanced vertical lift modules to increase your warehouse productivity and ensure accurate picking while keeping your warehouse employees safe and your warehouse running efficiently.