How Much Does a Vertical Carousel Storage System Cost in 2023?
If you’re looking to optimize your warehouse processes, a vertical carousel storage system can offer a wide range of benefits in terms of productivity, efficiency and cost-saving initiatives. In addition, it provides a secure place to store and track your inventory, while maintaining a safe and ergonomic environment for your employees.
What does the investment entail?
We’ll break down the total cost of a vertical carousel storage system, from purchasing to maintenance costs, and everything in between.
Plus, we’ll introduce you to a cost-efficient alternative you may not have considered.
What Is a Vertical Carousel Storage System?
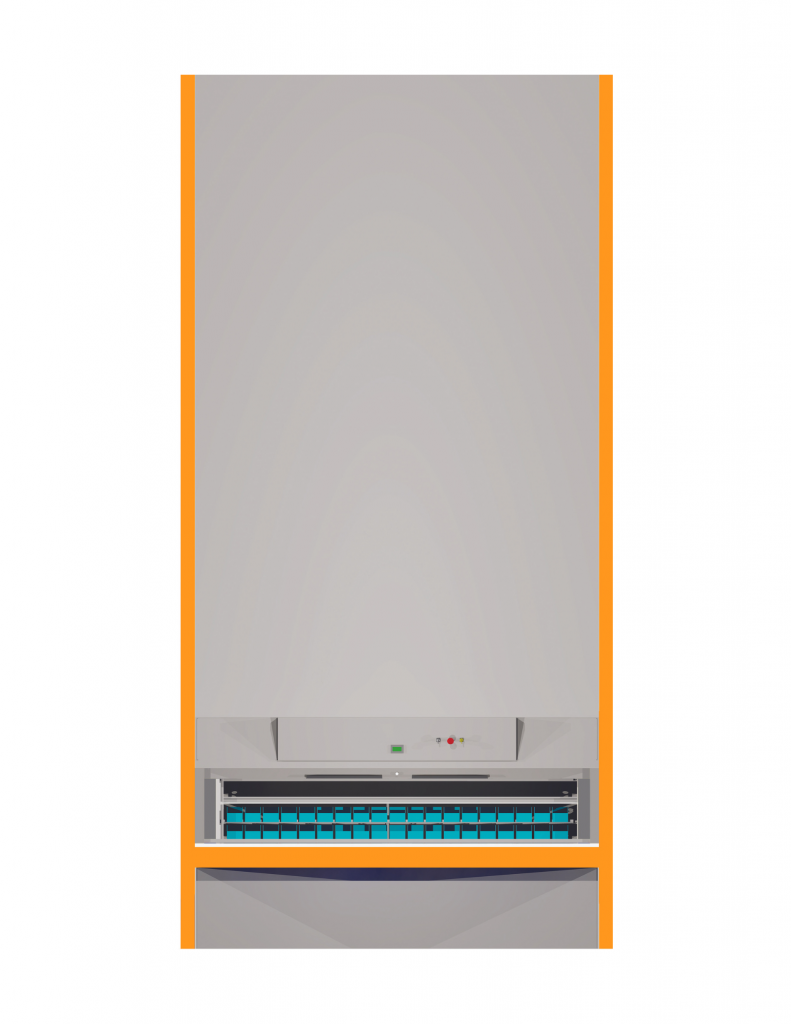
A vertical carousel (VC) is an automated storage and retrieval system that is designed to store inventory while reducing the floor area needed for storage, thanks to its upright and compact structure.
A typical vertical carousel comprises a series of carriers that are securely mounted on a closed-loop vertical track, all enclosed within a metal casing. This system efficiently transports inventory in a vertical circular motion, resembling the movement of a Ferris wheel.
Originally introduced in the 1950s, the primary purpose of a vertical carousel is to handle items of consistent size and weight. You may also encounter terms like “storage carousel” or “vertical rotating shelf system” used interchangeably to describe this storage solution, to differentiate it from a horizontal carousel.
How Much Does a Vertical Carousel Storage System Cost?
Initial Purchase Costs:
The cost of a vertical carousel storage system can vary based on several factors, such as size, features, delivery, installation, and maintenance. For a new system, the typical price range is between $60,000 and $80,000. Used models are also an option, with prices generally ranging from $30,000 to $40,000. However, outdated models can come with outdated technology and potential maintenance issues.
Installation Expenses:
Beyond the purchase price, you’ll need to budget for installation. In addition to the physical placement within your facility, there is an additional electrical setup and software integration. The total installation cost may range around $10,000.
Ongoing Maintenance:
Yearly maintenance for a vertical carousel can cost between $2,000 and $5,000. This includes routine checks, software updates, and replacement of worn-out parts.
Is a Vertical Carousel Cost-Efficient?
At first glance, a vertical carousel storage system might seem like a cost-efficient choice for your warehouse needs. However, the initial cost savings can be misleading.
While the upfront costs are lower, vertical carousels often come with a set of limitations and hidden costs that can affect their long-term value, including:
- Limited Flexibility: Vertical carousels have a fixed set of shelves or bins that rotate, making them less adaptable to varying inventory sizes and weights. This rigidity can become a significant drawback as your storage needs evolve, requiring additional investment in new storage solutions.
- Maintenance: The mechanical components in vertical carousels are prone to wear and tear, especially the chains and motors. This can lead to frequent maintenance needs, adding to the long-term costs.
- Energy Consumption: The design of vertical carousels requires the entire carousel to rotate to retrieve an item. This can be energy-intensive, especially if the desired item is on the opposite side of the access point, leading to higher energy costs over time.
- Operational Inefficiencies: The carousel’s design inherently limits picking speed and accuracy. Because all trays rotate past the access window, there’s an increased chance of picking the wrong item, leading to costly errors and returns.
A Cost-Efficient Alternative to Vertical Carousels: Vertical Lift Modules
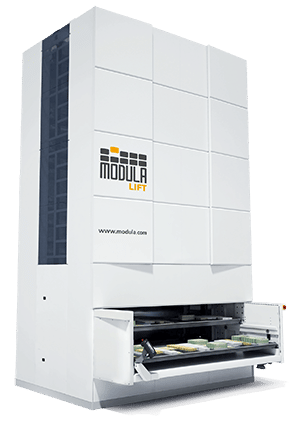
Vertical lift modules are automated storage and retrieval systems that automatically deliver goods to the warehouse operator, following the goods to person principle.
Unlike a vertical carousel, a vertical lift module is equipped with a more advanced design and operates like a vending machine, where items can be retrieved without rotating everything stored inside.
When an item is requested, an extractor collects individual trays from where they sit in the machine, then delivers the item to the operator at an ergonomically comfortable height.
This storage solution is more cost-efficient than vertical carousels, thanks to advanced automation features that boost productivity, improve picking speed and reduce the time and labor required for inventory management.
These advantages translate to long-term savings, offsetting the initial investment.
How Much Does a Vertical Lift Module Cost?
Initial Purchase Costs:
The starting price for a VLM is usually around $75,000, which is about the average cost of a Modula Slim. The final cost can vary based on different factors—like the model, the accessories you choose, the height and dimensions of the unit, and any special software requirements you might have. While the upfront costs may seem like those of a vertical carousel, the long-term value is where VLMs truly shine.
Installation Expenses:
Installation for a VLM tends to be less complicated than for a vertical carousel. Expenses usually start at $12,000 and cover unit installation, software setup and integration, as well as basic training for your warehouse staff.
Maintenance Costs:
Thanks to their advanced technology, VLMs are generally easy to maintain. Annual maintenance costs are typically between $2,000 and $5,000.
Why Vertical Lift Modules Are a Cost-Efficient Warehouse Solution
While both Vertical Carousels and Vertical Lift Modules (VLMs) offer their own sets of advantages in automated storage solutions, VLMs stand out as the more cost-efficient option for several key reasons.
Boost Picking Accuracy
A vertical lift module increases picking accuracy more effectively than a vertical carousel.
In the Vertical Carousel (VC), all trays rotate past the access window to reach the required storage location. When warehouse operators need to retrieve an item from a VC, they must wait for the entire set of trays to move before accessing the specific tray with the desired item. Additionally, once the picking is done, the carousel needs to rotate 180 degrees to ensure even load distribution.
On the other hand, a Vertical Lift Module (VLM) operates more efficiently, saving time for warehouse operators. In a VLM, only one tray with the required SKU is delivered at a time, while the other remains securely stored in the unit. This eliminates the need to wait for the entire set of trays to move. Furthermore, the VLM can be equipped with a dual delivery bay to further enhance picking speed.
Advanced picking aids such as laser pointers or LED bars in VLMs allow operators to quickly and easily identify the items that need to be picked or replenished.
In a vertical carousel, any carrier can be stopped at the access window along the way, increasing the likelihood of operators picking the wrong SKU, which can lead to expensive product returns. This is due to the vertical carousel’s closed-loop system, which always has another carrier directly above it. This requires products to be picked from the front rather than the top — restricting the visibility of products and the number of items users have access to at any given time. Top picking in a carousel is only possible using totes or boxes that can be pulled out of the carrier, adding unnecessary steps to the picking process.
On the other hand, a vertical lift module consistently provides top picking, ensuring visibility and access for products. With a VLM, there are no additional movements added to the pick cycle. The selected tray is brought directly into the picking bay, where it is 100% visible and accessible to the operators.
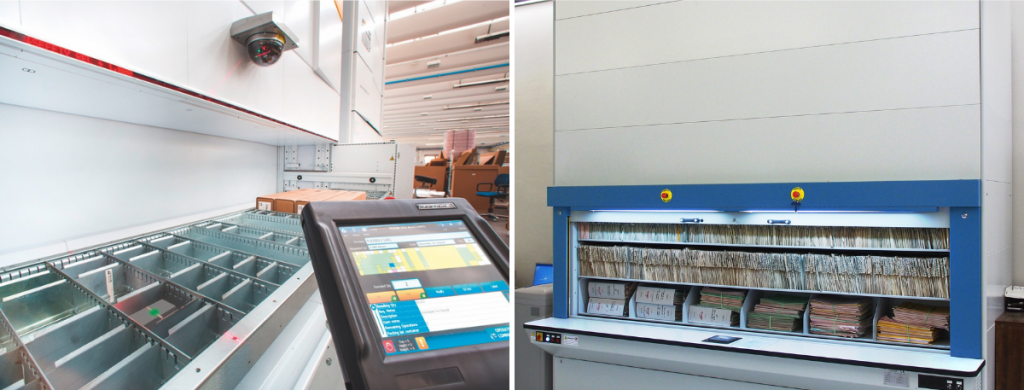
Offer Better Payload Storage Capacity
A vertical lift module provides stability for heavy items — for example, Modula’s VLM trays can accommodate around 2,200 pounds per tray, while a vertical carousel can experience load imbalances when storing heavy inventory.
In a vertical carousel, the carriers are connected in a fixed order, causing the storage system to rotate every time an item is replenished or picked, creating imbalance issues.
On the other hand, as a vertical lift module is composed of two tray towers (one tray tower in the front and one in the back), the VLM configuration can manage heavier loads.
Improve Security
A vertical lift module offers more security features compared to a vertical carousel.
In a vertical carousel, all carriers rotate past the access window, making each inventory item accessible, regardless of access restrictions.
On the other hand, a vertical lift module delivers one tray at a time, while other goods are secured in their own tray. VLMs also have controlled access features to ensure that only authorized warehouse operators can access the stored items, adding an extra layer of security.
In addition, VLMs are equipped with different safety options, such as electronic key system (EKS), radio frequency identification (RFID) and badge readers. Thanks to the automatic closing door, inventory is safe when the machine is turned off or unattended.
Flexibility in Handling Different Types of Products
When it comes to product storage, vertical lift modules (VLMs) offer greater adaptability for accommodating various product heights and types compared to vertical carousels.
While vertical carousels have height restrictions in regard to their trays, vertical lift module trays can be modified to fit your inventory.
Due to the movement of every bin during warehouse operations, the vertical carousel is not the ideal choice when storing fragile products or items that are sensitive to continuous movement, such as glass.
Another important difference to take into account is the height of the products you need to store.
As a VC is a closed-loop system with all the carriers being tied together, the height of the unit cannot be changed. For example, a carousel with a 12 pitch has a clear height of 10.75 inches. You can add additional shelf levels to divide the 10.75 inches up into smaller levels, but you can never go taller. This would require a new unit.
On the other hand, VLMs offer dynamic storage locations and flexible configurations — the height of trays can range anywhere between 3 inches and 660 inches. Thanks to partitions and dividers, warehouse operators can create the exact number of storage locations required, and tray configurations can be adjusted at any time to accommodate changes in the size or quantity of stored items or seasonal demands. In addition, a built-in height-detection system on a VLM can determine the vertical dimensions of an item as the tray is put away, calculating adjustments in real-time to maximize the unit’s storage density.
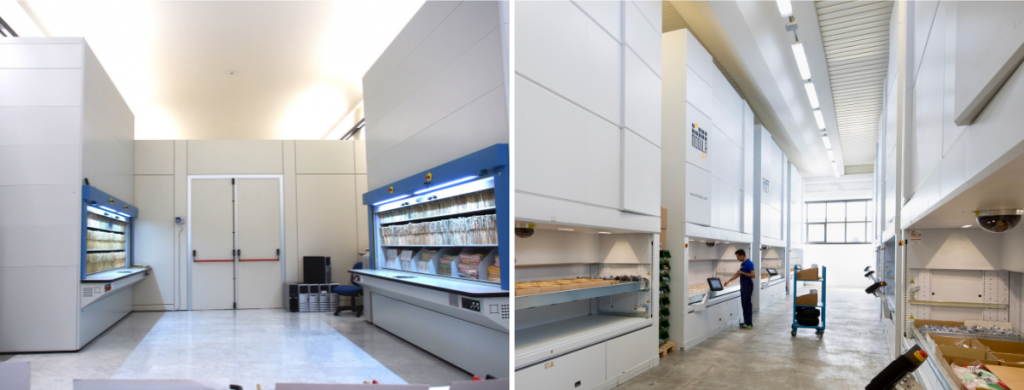
Cut Costs on Electricity Bills
You can save more money on a vertical lift module compared to a vertical carousel.
In a vertical carousel, the entire storage system needs to rotate to retrieve or replenish goods, often consuming more energy — especially if the desired item is on the opposite side of the access point.
On the other hand, most vertical lift modules incorporate advanced energy-saving technologies, such as LED lights, climate control efficiency, and standby mode, reducing energy consumption and contributing to sustainability goals and long-term cost savings.
A Summary of Cost Differences: Vertical Carousel vs. Vertical Lift Module
While vertical carousels and vertical lift modules are both used in material handling and storage, as highlighted in this article, they significantly differ in their operational mechanisms and associated costs.
Let’s summarize our analysis and compare the cost differences:
- Vertical Carousel System: $60,000+
- Vertical Lift Modules: $75,000+
The number of parts in your storage system has a direct correlation with the cost of purchase, as more parts translate to higher manufacturing costs.
Vertical carousels have simpler mechanical components and structure, compared to VLMs. They consist of a series of shelves or bins attached to a chain drive, allowing inventory to rotate around a track in a fixed loop, similar to the movement of a Ferris wheel.
On the other hand, vertical lift modules are composed of a more complex design that operates like a vending machine, where inventory can be delivered without rotating each item that is stored inside.
While a vertical carousel is usually less expensive compared to a vertical lift module in terms of purchasing costs, a VLM can help you save on warehouse costs in the long run, as it offers increased throughput and can adapt to a wide range of inventory sizes and shapes.
- Vertical Carousel System: Starts at $10,000+
- Vertical Lift Modules: Starts at $12,000+
The overall cost of your storage system also depends on installation. Installation costs can include removing and disposing of the current storage system, reinforcing floors and moving overhead ducts or sprinklers for the new storage technology.
Vertical carousels usually have lower installation costs due to their simpler structure and fewer mechanical components, requiring less extensive modifications to the existing infrastructure. The installation process is also less time-consuming, which also translates to lower labor costs.
On the other hand, vertical lift modules can require more extensive preparation and modifications, such as reinforcing existing structures and relocating utilities, resulting in higher installation costs.
However, despite these initial costs and complexities, investing in vertical lift modules is still more cost-efficient in the long run. The enhanced operational efficiency, superior space utilization and adaptability they provide, can lead to substantial long-term savings and operational benefits.
- Vertical Carousel System: Around $2,000 to $5,000 for annual upkeep
- Vertical Lift Modules: About $2,000 to $5,000 for yearly maintenance
One of the key factors in the total cost of ownership for any automated storage system is its running and maintenance costs.
Vertical lift modules generally have low maintenance costs due to their advanced technologies, such as energy recovery systems, energy-efficient motors, and intelligent control systems.
These technologies not only reduce energy consumption, but also minimize wear and tear on mechanical components, leading to less frequent and less costly maintenance.
In contrast, vertical carousels—especially older models—may require more frequent maintenance. The system’s design, which necessitates the entire carousel to rotate for item retrieval, can lead to higher energy consumption and increased wear and tear on mechanical parts.
This results in more frequent maintenance needs, adding to the long-term operational costs—especially if the desired item is far from the access point, requiring the carousel to rotate more than necessary.
- Vertical Carousel System: 15-18 months
- Vertical Lift Modules: 6-18 months
Return on investment (ROI) refers to the financial benefit you can achieve relative to the amount of money invested in your storage system.
Both vertical carousels and vertical lift modules gain a fast ROI.
While vertical carousels gain a fast ROI due to their lower costs, vertical lift modules — despite having higher upfront costs — provide a quick and more sustainable ROI over the long term. In fact, Modula VLMs provide an ROI in 6-18 months.
Thanks to the VLM’s adaptability and advanced features, it can optimize storage space and improve overall operational efficiency, leading to quicker profitability.
Vertical Lift Modules at Modula
As the leader in automated storage solutions and warehouse management systems, Modula offers state-of-the-art, advanced solutions that are designed to reimagine productivity and efficiency across your organization.
Our VLMs are engineered to optimize your current warehouse space by leveraging the available ceiling height, boosting storage capacity and efficiency.
We offer two VLM modules:
- Modula Lift: Ideal for storing industrial components and spare parts, the Modula Lift is available in a wide range of capacities and dimensions to accommodate different types of inventory.
- Modula Slim: Specifically designed for environments with restricted floor space, the Modula Slim only takes up a small footprint of only 32.29 square feet, making it the ideal choice for maximizing storage in constrained areas.
Modula VLMs allow you to:
- Achieve faster picking with over 200 lines per hour
- Maximize your available ceiling height and save up to 90% of floor space
- Boost order processing with capabilities of handling 140 trays per hour
- Receive goods automatically, thanks to the user-friendly Copilot controller
- Protect your inventory with a secure, enclosed system
- Improve employee safety by eliminating the need to reach high and low areas
Choosing Space-Efficiency: Modula Slim Over Vertical Carousel for Limited Depth Applications

In the world of warehouse optimization, space has always been a precious commodity. For many situations in the past, the Vertical Carousel was the go-to solution because of its relatively shallow depth compared to traditional Vertical Lift Modules (VLMs).
However, recognizing the need for a smarter and more compact storage solution, Modula designed the Slim.
The Most Compact VLM in the Market
In simple terms, Modula Slim is a Vertical Lift Module (VLM) that combines all the power and efficiency of a traditional VLM into an incredibly compact space. This advanced technology is based on the same principles as our LIFT model but with a much smaller footprint.
With Modula Slim, you have the flexibility to store a wide range of materials and products, including loose materials, containers (boxes, drawers, cartons), small items, spare parts, coils, bottles, and much more.
It offers a range of advantages over vertical carousels, making inventory management more efficient and cost-effective.
Choose Modula Slim for greater flexibility, higher load capacity, and better storage density. With quick installation and low energy consumption, it’s the obvious choice for those seeking a smart and compact storage system.
Why Choose Modula Slim?
- Space Recovery: Modula Slim frees up floor space by optimizing storage density. It’s the perfect solution for warehouses with limited depth.
- Reduced Picking Times: Picking times are reduced thanks to its ability to make materials easily accessible to all operators quickly and ergonomically.
- Complete Inventory Control: Modula Slim helps you keep stock levels and your entire warehouse inventory under control.
- Integration with ERP: This system easily integrates into business processes by communicating with any ERP system.
- Tracking and Control: It records picking and restocking operations, controlling who has access and logging their activity. It eliminates picking and restocking errors by guiding the operator through the entire process.
- Easy Installation and Training: Modula Slim is built on a pre-assembled base module that is easy to ship and quick to install. This means it can be up and running in your facility in just 48 hours. Additionally, staff can be trained in a few days to operate the Modula Slim, realizing a quick return on investment thanks to the significantly increased picking speed this storage solution offers.
- Low Energy Consumption: Modula Slim is designed for low energy consumption, contributing to sustainability goals and long-term savings.
- Customization: You can customize Modula Slim with various options, including visual aids, Put to Light, access control systems, partitions, and our customizable divider system to keep items separated and organized in trays.
At Modula, we provide premier automated storage and retrieval systems to maximize warehouse space, enhance efficiency and adapt to evolving consumer needs.
Speak to our material handling experts to find the optimal storage solution for your warehouse. We’ll conduct a thorough warehouse assessment to help guide you to the model that’s right for your needs.