Vertical Carousels vs. Vertical Lift Modules: Which Is Better?
If you’re looking to upgrade your storage with a vertical carousel or lift module, you may be wondering which automated warehouse storage solution is better.
Vertical carousels (VCs) and vertical lift modules (VLMs) are both computer-controlled, automated storage and retrieval systems (ASRS) that occupy as little floor space as possible by taking advantage of a warehouse’s available ceiling height.
However, they differ in terms of their structural design, operational mechanism and storing inventory method.
We’ll compare vertical carousels vs. vertical lift modules to help you make an informed decision on which storage system reigns supreme.
Moreover, we’ll introduce you to our space-saving vertical lift modules to help reimagine your warehouse operations.
What Is a Vertical Carousel?
A vertical carousel (VC) or vertical storage carousel is an automated storage and retrieval system that is designed to store inventory while reducing the floor area needed for storage, thanks to its upright and compact structure.
A vertical carousel is composed of a series of carriers mounted on a vertical closed-loop track, inside a metal enclosure. It transports inventory in a vertical loop, resembling the movement of a Ferris wheel.
Introduced in the 1950s, a vertical carousel is primarily designed to carry items of similar size and weight. It is also described as a storage carousel or vertical rotating shelf system — to differentiate it from a horizontal carousel.
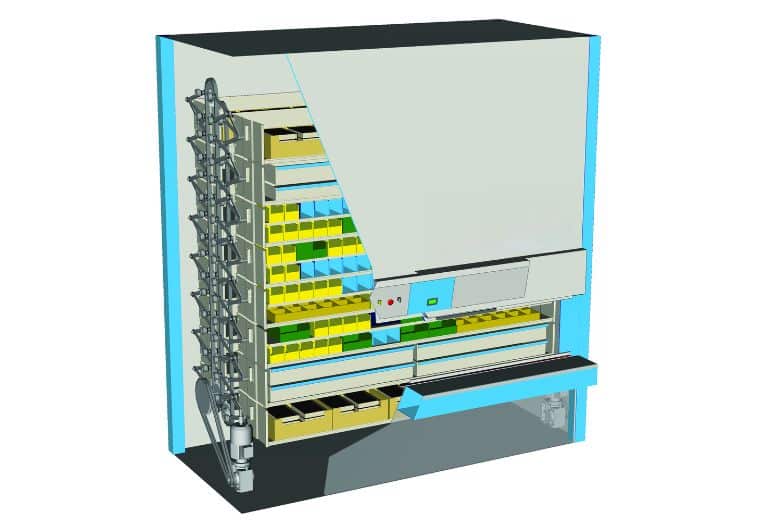
What Is a Vertical Lift Module?
A vertical lift module (VLM) is an automated storage and retrieval system that operates based on the goods-to-person principle, where inventory is automatically delivered to the warehouse operator.
Like a vertical carousel, a VLM can help store inventory while saving floor space by utilizing the height of the warehouse.
Like a vertical carousel, a vertical lift module is equipped with a more advanced design and operates like a vending machine, where items can be retrieved without rotating everything stored inside.
When an item is requested, an extractor collects individual trays from where they sit in the machine, then delivers the item to a picking bay.
The warehouse operator then receives the item at an ergonomically comfortable height, eliminating the need to reach high or low areas to receive the item, leading to less strain in the workplace.
Vertical Carousels vs. Vertical Lift Modules
While both VCs and VLMs can store inventory in as little space as possible, they function in different ways. We’ll break down the differences between these systems below.
Depth and Width
Vertical carousels (VCs) and vertical lift modules (VLMs) differ significantly from vertical lift modules in width and depth.
To be more specific, VCs typically range from 6 to 13 feet wide and just over 4 to 5 feet deep.
They generally store smaller goods, with carriers that hold inventory measuring from 4 to 12 feet wide and offer a depth of 5 feet at most.
On the other hand, a vertical lift module provides twice the depth, offering more inventory space. In terms of width, a standard VLM measures between 5 to 15 feet.
At Modula, we offer the most compact vertical lift module in the industry — The Slim. It occupies only 32.29 square feet of floor space and measures less than 66 inches deep.
Unit Height and Balance
While a vertical carousel rotates every time the user needs to pick or replenish an item, vertical lift modules only present the tray with the required item.
VCs are prone to many unbalancing issues. Unbalancing issues can occur for different reasons, including:
- A difference in size or weight of the products stored
- The presence of a few carriers in a row being empty
- An odd number of carriers
Any of these conditions can create stress on critical components in the unit. The motor could overload, and the carousel can shut down completely until the condition is corrected. If this happens, the motor will struggle to move the carriers through the curve of the unit.
On the other hand, vertical lift modules are composed of two tray towers — one in the front and one in the back — along with a central elevator.
Once the user requests the item, the elevator extracts it. Vertical lift modules can reach up to 53 inches or more and contain trays of different heights. For example, small items can be stored in one tray, while larger items can be stored in another tray.
The modular design of the VLM ensures almost unlimited flexibility. The height can be modified and adjusted to optimize the unit for the ceiling height by adding or removing modules.
If you change locations or move to a different site, the VLM can be quickly adapted to the new height requirements.
Height and Type of Inventory Storage
While vertical carousels have height restrictions in regard to their trays, vertical lift module trays can be modified to fit your inventory.
Due to the movement of every bin during warehouse operations, the VC is not the ideal choice when storing fragile products or items that are sensitive to continuous movement, such as glass.
Another important difference to take into account is the height of the products you need to store.
As a VC is a closed-loop system with all the carriers being tied together, the height of the unit cannot be changed.
For example, a carousel with a 12 pitch has a clear height of 10.75 inches. You can add additional shelf levels to divide the 10.75 inches up into smaller levels, but you can never go taller. This would require a new unit.
On the other hand, VLMs offer dynamic storage locations and flexible configurations — the height of trays can range anywhere between 3 inches and 660 inches.
Thanks to partitions and dividers, warehouse operators can create the exact number of storage locations required, and tray configurations can be adjusted at any time to accommodate changes in the size or quantity of stored items or seasonal demands.
In addition, a built-in height-detection system on a VLM can determine the vertical dimensions of an item as the tray is put away, calculating adjustments in real-time to maximize the unit’s storage density.
Payload Storage Capacity
A vertical carousel is prone to load imbalances, while a vertical lift module offers stability for heavy inventory.
In a vertical carousel, the carriers are connected in a fixed order, allowing the entire carousel system to rotate every time the warehouse operator needs to pick or replenish an item, which can cause imbalances.
To avoid load imbalances, inventory items need to be the same size and weight, as you can’t change the tray positions.
Alternatively, vertical lift modules are composed of two tray towers — one in the front and one in the back — along with a central elevator.
At Modula, each unit’s trays accommodate heavy loads of up to 2,200 pounds per tray, without strain or imbalance issues.
Take the Modula Slim, for example. It has twice the load capacity compared to typical vertical carousels with no balancing issues.
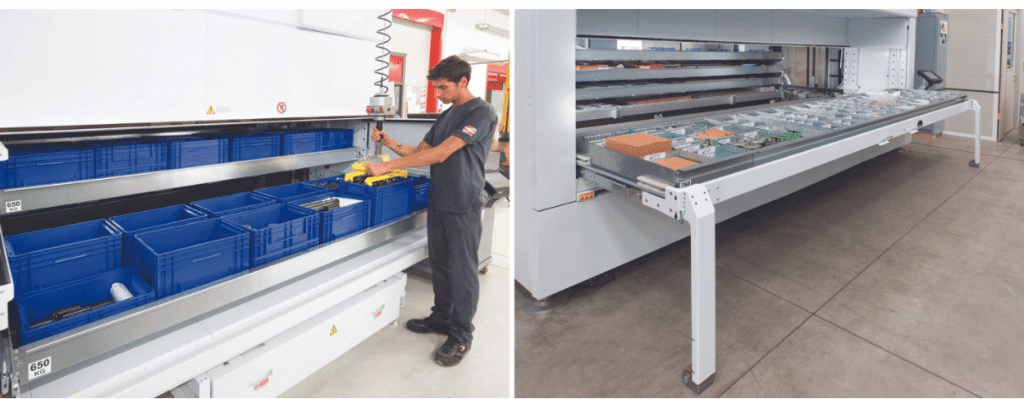
Front Picking
While a vertical carousel restricts the visibility of products and the number of items users have access to at any given time, the VLM always provides top picking, allowing visibility and access for products.
With a VLM, there are no additional movements added to the pick cycle. The selected tray is brought into the picking bay, where it is 100% visible and accessible to the operators.
Because the vertical carousel storage system is a closed loop system and there is always another carrier directly above it, the product must be picked from the front and not the top — allowing warehouse operators to reach into the face of the carrier to pick parts.
Top picking in a carousel is only possible using totes or boxes that can be pulled out of the carrier, exposing the entire product, adding unnecessary steps to the picking process.
Dual Access
While a vertical carousel cannot work from both access openings simultaneously, a vertical lift module can.
Because the VC system of carriers is tied together in one array, it is not possible to work at two access openings, simultaneously. Each access opening needs to be given or taken priority over the other.
Again, this is because if one carrier moves, they all move. In addition, it is not possible to get various combinations of carriers to appear at each corresponding access opening at any given time.
Some systems even require that the door of the opposite opening be closed in order for the other opening to work.
On the other hand, after the VLM has delivered a tray to one access, it can continue on to deliver (or remove) one item from the other opening.
Warehouse operators are free to work on their respective trays at any time while they are in the access opening. This creates a more productive environment for both picking and replenishment, as all replenishment can occur during the picking cycle.
The vertical lift module can also extend over different floors, with access openings on the front and rear, allowing operations on multiple levels simultaneously. The units can also be installed outside of the building to further expand storage space.
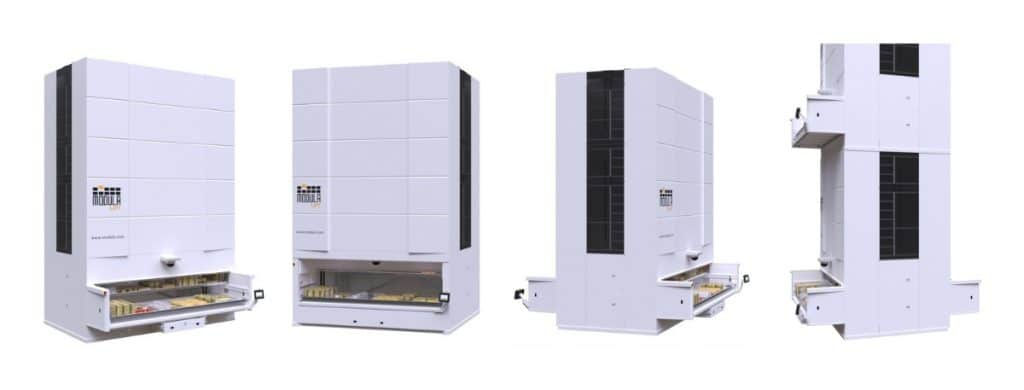
Picking Accuracy
A vertical lift module offers a greater boost in picking accuracy compared to a vertical carousel.
The VC rotates all trays past the access window in order to get to the required storage location. Any carrier can be stopped at the access window along the way, increasing the likelihood that a warehouse operator could pick the wrong SKU, which can lead costly product returns.
On the other hand, a VLM only delivers one tray at a time, while other items are kept safe in their own unit. Only the tray with the required SKU is brought to the picking bay.
Thanks to advanced picking aids (such as the laser pointer or LED bars) operators can quickly and easily identify the items that need to be picked or replenished.
Picking Speed
While a vertical carousel is slow and less efficient, a vertical lift module can save warehouse operators time, as they don’t need to wait for the entire set of trays to move — just the tray holding the required item.
When warehouse operators need to retrieve an item from a VC, they need to wait for the entire set of trays to move before accessing the specific tray that carries the item.
Once you place inventory into a tray, the carousel needs to rotate 180 degrees to ensure that the loads are evenly distributed.
On the other hand, while the operator is working on one tray in a VLM, the elevator is retrieving the second tray in the queue, reducing the waiting time.
In addition, the VLM can be equipped with laser pointers — to improve picking accuracy, specifically for small parts — and a dual delivery bay to further enhance the picking speed.
At Modula, our VLMs offer picking speeds of up to 300 lines per hour or more.
Security
Vertical lift modules offer more security features compared to the vertical carousel.
The VC rotates all carriers past the access window to get to the required storage location, making each item accessible, regardless of access restrictions.
On the other hand, the VLM delivers one tray at a time, while other items remain secured in their own tray. Only the tray with the desired product is brought to the access window, making it possible to restrict access to other products when and if necessary.
In addition, VLMs are equipped with different safety options for an added layer of security, such as electronic key system (EKS) radio frequency identification and badge readers. Thanks to the automatic closing door, inventory is safe when the machine is turned off or unattended.
Find out how you can personalize your Modula VLM by watching the video below:
Installation
A vertical lift module is easier to install than a vertical carousel.
A VLM comes in separate pieces that you can easily transport, making it possible to install in only two days. You can also adjust their trays when needed.
The vertical carousel setup process, on the other hand, is more complex due to its intricate loop system that includes chain drives and motors.
They also require more time for installation, typically around four to five days.
What Is the ROI for Vertical Carousels Storage Systems and Vertical Lift Modules?
Vertical carousels offer a quick return on investment (ROI) due to their lower upfront costs.
However, when you take a more long-term approach, vertical lift modules deliver a faster and more sustainable ROI.
In fact, at Modula, our vertical lift modules and horizontal carousels provide a return on investment ranging from 6 to 18 months.
The Ideal Alternative to Vertical Storage Carousels: Vertical Lift Modules at Modula
Vertical carousels have been around longer than vertical lift modules, but the advantages you can reap from VLMs are clear.
If you are considering an automated storage and retrieval system, it is important to evaluate which system is right for your handling and picking needs.
Modula is the industry leader in advanced storage solutions and warehouse management systems. Our solutions optimize your warehouse operations to improve productivity and efficiency, while keeping your inventory safe.
Our automated vertical lift modules take up a minimum footprint in your warehouse by utilizing the ceiling height available.
Our advanced models allow your warehouse operators to easily access your inventory while it is stored in a secure and safe environment.
With a simple touch on the user-friendly Copilot controller or with the scan of the barcode, SKUs are automatically delivered to your warehouse operator, quickly and effortlessly.
At Modula, we offer two vertical lift modules:
- Modula Lift: The most popular vertical lift module, Modula Lift is available in a wide range of capacities and sizes.
- Modula Slim: This vertical lift module is designed to fit small spaces with the same functionalities as the Modula Lift.
Our vertical lift modules allow you to:
- Increase productivity and efficiency
- Drastically reduce picking errors
- Ensure accurate delivery of the right item to the right person
- Ensure optimal ergonomic item retrieval
- Quickly locate items in your warehouse
If you need all the benefits of a VLM with the footprint of a vertical carousel, look no further than the Modula Slim:
In the video below, see the Modula Slim in action:
The Modula Slim allows you to:
- Optimize floor space by only using 32.29 square feet of your facility
- Boost picking accuracy through automated pointing lasers and alphanumeric LED bars
- Accommodate loads without imbalance issues
- Store inventory of different sizes and weight, thanks to modifiable trays
- Adjust trays to maximize storage density — the Modula Slim measures SKUs as the tray is put away
- Use less than 1.2kW/h in your warehouse, thanks to a choice of a single-phase (220V) power supply or three-phase (480V)
Wrapping Up on Vertical Storage Carousels vs. Vertical Lift Modules
If you are considering an automated storage and retrieval system, it is important to evaluate which of these two systems is right for your handling and picking needs.
To recap, a vertical lift module outranks a vertical carousel in regard to picking accuracy, security and speed. Without limitation in terms of depth, height and product range, VLMs offer more flexibility and capability while providing ergonomics.
Why choose outdated technology when the market offers a much more sophisticated and efficient solution?
At Modula, we can help you reimagine your storage solutions with our advanced vertical lift modules to increase your warehouse productivity and ensure accurate picking, while keeping your warehouse employees safe and your warehouse running efficiently.