What is Lean Manufacturing? 8 Types of Waste Automation Can Eliminate
From keeping your warehouse operators safe to eliminating waste in the warehouse caused by inefficiencies, lean manufacturing is an approach that can significantly reduce costs and improve operational efficiency.
We’ll share all you need to know about this approach, including the five principles of lean manufacturing and the benefits it offers for your warehouse.
Plus, we’ll introduce you to our advanced automated storage solutions at Modula to help you implement lean principles in your warehouse.
What Is Lean Manufacturing?
Lean manufacturing is an approach to warehouse management that aims to improve efficiency, reduce waste and increase productivity by applying a set of five principles.
The lean approach originated from the Toyota Production System, a framework for efficient manufacturing that was developed in Japan.
Waste types (in their Japanese counterparts) can be grouped into three general categories:
- Mura: A Japanese term that refers to unevenness. This waste is created by irregularities in a process, like an imbalanced workload. For example, if some warehouse operators work full time while other employees are idle, the uneven distribution of work is considered a waste.
- Muri: A Japanese term that refers to overburden. This waste is created when resources such as machines, employees or systems are pushed beyond their limits. For example, if warehouse employees need to skip breaks or rush their tasks to meet seasonal demands, it creates waste due to stress and overwork.
- Muda: A Japanese term that refers to any form of waste that doesn’t add value to work or warehouse processes. This waste is created by unnecessary processes that consume time, resources or space. For example, if a warehouse picker travels throughout the warehouse to manually pick items when a machine could perform this task instead, it is considered waste.
The 5 Principles of Lean Manufacturing
The five principles of lean manufacturing aim to optimize workflow, reduce waste and improve efficiency.
Lean manufacturing principles include:
Identify the Value
The “identify the value” principle is the first step in the lean manufacturing process. It states that companies should determine what provides value to their customer and how their products or services can meet those values.
To implement this principle, conduct customer surveys and focus groups, analyze market trends and review customer feedback to get a better understanding of what your customers find valuable.
Map the Value Stream
The “map the value stream” principle states that companies should identify and analyze every step in the production process, from raw materials to the shipment reaching the customer.
A value stream is the complete life cycle of a product, which includes the product’s design, how the customer uses the product and how it is discarded, to pinpoint where value is added and where waste occurs.
To implement this principle, create a visual map or diagram that outlines each stage of the manufacturing process by gathering data, resources and costs associated with each step. Then, review the visual map to identify areas of waste or bottlenecks to eliminate steps that don’t add value.
Create a Flow
The “create a flow” principle states that items should seamlessly flow from production to shipment without interruption, by way of a strategically organized floor space.
To implement this principle:
- Evaluate your current layout to identify bottlenecks and areas with safety concerns, such as narrow aisles that could cause accidents and cluttered workspaces.
- Create zones based on the frequency of item retrieval. For example, store fast-moving inventory near the shipping area to improve efficiency.
- Take advantage of your available ceiling height and use minimal floor space by installing vertical modules.
Establish a Pull System
The “establish a pull system” principle states that production should be driven by realistic demand rather than forecasts, to reduce inventory costs. In a pull system, goods are produced only when an order is placed.
To implement this principle, analyze consumer behavior and purchasing patterns to understand the demand, then adjust production as needed.
Seek Perfection
The “seek perfection” principle states that organizations should build a culture of continuous improvement to increase overall quality.
To implement this principle:
- Identify problem areas and make sure standards are followed and maintained.
- Remind your team about the importance of lean manufacturing principles and make sure they know how to implement each principle.
- Express your thanks publicly or reward your employees with gift cards or monetary bonuses to help increase morale and encourage others to follow their example.

Benefits of Lean Production
Lean manufacturing offers significant benefits, such as reduced operational costs and shorter production times. By focusing on eliminating waste and improving efficiency, this approach also leads to higher product quality and greater customer satisfaction.
The key benefits of lean production include:
- Increase productivity: Lean manufacturing cuts wasteful processes in the warehouse, such as storing excessive inventory and overproducing goods. By getting rid of these unnecessary steps, the warehouse can run more efficiently.
- Improve workplace safety: Lean manufacturing focuses on workplace safety by utilizing automated warehouse solutions — a variety of advanced equipment and systems used in a facility — to eliminate unsafe work practices, such as overexertion when reaching high or low places.
- Save space and money: Utilizing lean methods in your current warehouse can help you manage inventory better and cut down on excess stock. This, in turn, prevents you from moving to a larger warehouse or renting more space.
- Boost employee morale: Lean manufacturing principles promote employee involvement and empowerment. When you involve your warehouse operators in improvement initiatives and reward them with good work, you can improve retention rates.
Types of Waste Eliminated by Lean Manufacturing & Automation
While processes differ between factories and warehouses, the typical types of waste found are quite similar and always involve inefficient use of time and money. In lean manufacturing, waste is any expense or effort that doesn’t generate a product or a service that a potential client is willing to pay for.
One area where such inefficiencies are often observed is in warehousing. Conventional racking, shelving, drawer cabinets still used in many facilities often contribute to this waste as they occupy significant valuable space within the facility. These also lead to slower process flows where time is mainly spent locating and retrieving parts.
Lean manufacturing is based on identifying and eliminating waste, significantly optimizing manufacturing processes and dramatically improving the efficiency and productivity of overall operations.
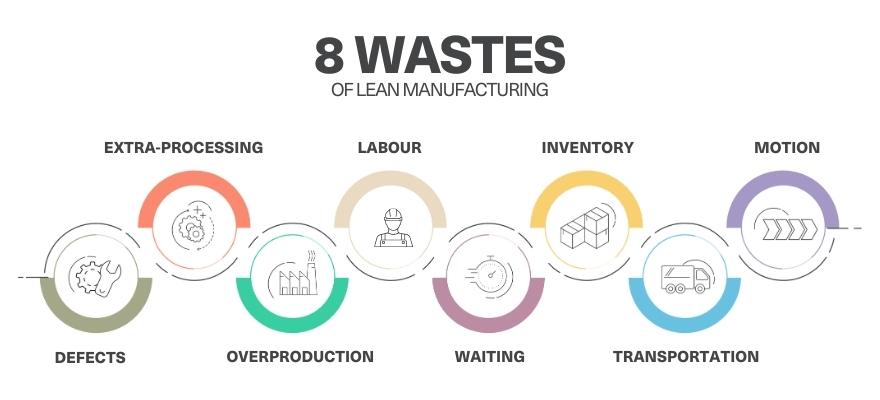
1. Defects Caused by Human Intervention
One of the most easily recognizable wastes in lean manufacturing is defects due to mistakes such as poor quality controls, uncontrolled inventory management, or missing processes and documentation.
Industry studies have shown that each picking error results in an 11-13% drain on profitability. This has a considerable financial impact at the end of the year not counting the risk it poses for the company.
Lean manufacturing and automated warehouse solutions can help prevent errors caused by manual tasks. The lean approach can effectively identify and eliminate defects by performing a root cause analysis and implementing continuous improvement processes.
On the other hand, automated warehouse solutions align with the principles of lean manufacturing by reducing waste and automating manual tasks to prevent errors.
Automation technologies like vertical lift modules (VLMs) and horizontal carousels (HCs) can enhance inventory control and reduce human error.
For example, Modula’s VLMs are fully automated vertical storage systems that allow for large inventory of goods to be quickly accessed while being stored in a safe and secure environment.
Items are delivered to the operators with a simple touch on the user-friendly copilot controller or the scan of a barcode. Modula’s laser pointer also accurately pinpoints the SKU by mapping it on an X, Y axis, preventing mispicks.
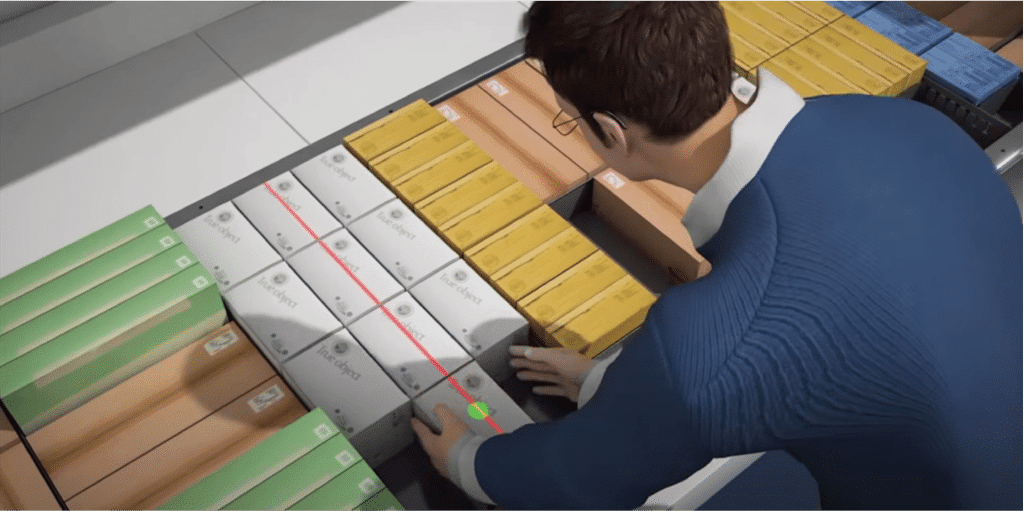
The item’s position is first highlighted with a red line indicating the correct column. The exact location is then highlighted with a green light. This feature eliminates the need to search for items and ensures that the right part is delivered to the right person, significantly reducing the risk of human error.
In addition, the user can monitor stock levels in real-time, speed up order execution times for both picking and replenishment operations and avoid the accidental release of wrong, obsolete, expired or on-hold products.

2. Excess Processing/ Inappropriate Processing
Repairing, remanufacturing, over-processing, excessive reports, re-entering data or duplicating existing data are examples of inappropriate processing waste.
Lean manufacturing manages these issues by implementing standardized processes, taking advantage of vertical storage solutions and utilizing efficient data management systems.
Modula vertical lift modules can help eliminate these wastes as they optimize operating procedures, increase flexibility and lower the costs in almost any type of warehouse.
A large inventory of items can be stored in a minimal footprint, bringing items closer to where they are needed. This reduces the length of the production line, optimizes the operation flow and prevents errors or product damages during transportation which would require costly repairs or re-manufacturing.
Lean order processing is also easy to implement thanks to the Modula warehouse management system (WMS) software that can be directly connected to the local ERP offering full traceability and real time inventory, preventing duplicate data and eliminating excessive reporting.

Likewise, all picking operations are monitored and log-ins are tracked, even down to specific trays preventing operators from picking the same items or for high valuable products to be stolen, which would result in more reports and documents needed to correct the problem.
Many manufacturing facilities need adaptable equipment, as they constantly change and readjust their product mix to keep up with the market demands.
The modular design of the VLM allows for flexibility. The height can be modified and adjusted to optimize the ceiling height, by adding or removing modules and these can be easily adapted to the new height requirements of different location within the production or warehouse facility.
Trays can be organized for every type or size of the item. Thanks to partitions and dividers, users can create the exact number of storage locations required and the configuration can be adjusted at any time to accommodate changes in the size or quantity of the stored items.
This guarantees the same outputs even with changes in products or tools.

3. Overproduction
Overproduction occurs when more parts or products are produced than orders are placed.
Some organizations still work on the principle of “Just-in-Case” instead of “Just-in-Time,” in which production is based on unclear or inaccurate forecasts and without an exact overview of the number of products still available in stock at the end of the month.
This can lead to waste, such as excessive inventory, storage, resources, movement costs and significant capital tied up in unused inventory.
Lean manufacturing addresses overproduction by implementing the “pull” system, which means products are only made as they are needed.
In addition, warehousing and manufacturing facilities can have full control over the flow of goods, using vertical storage solutions.
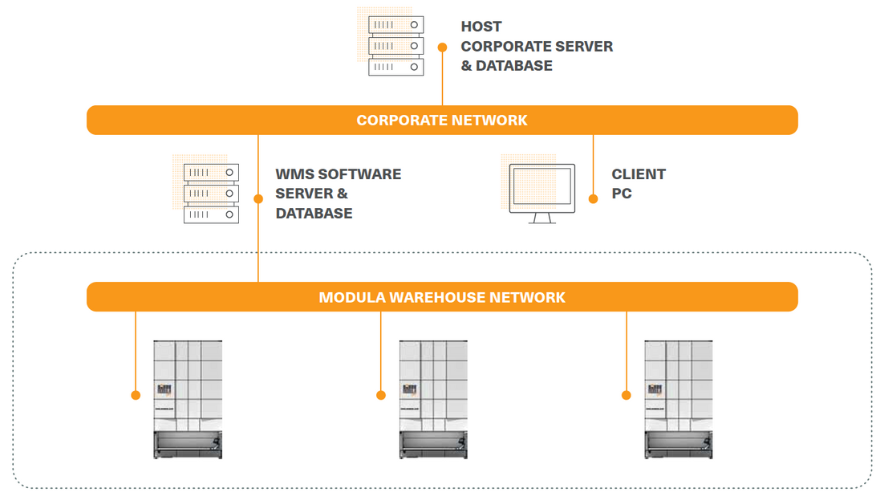
Modula’s VLMs can be integrated into any existing local IT system thanks to Modula WMS. This inventory management software provides an accurate and continuous exchange of information with minimal impact on pre-existing procedures.
By using the available data to its full potential, Modula’s WLMs guarantee improved inventory control and accountability. All picking and replenishment operations are monitored and documented to offer full traceability of the orders and monitor stock levels in real time.
4. Labor cost
Lean manufacturing principles can help optimize labor-intensive activities and labor costs by standardizing procedures and implementing automation where possible.
Automated warehouse solutions, such as VLMs, can eliminate labor waste by automating cumbersome tasks, allowing human operators to be more productive and focus on more value-added activities.
In fact, industry studies have shown that vertical storage solutions can increase workforce productivity by up to 85%, as one worker is able to handle the same volume of work previously performed by multiple operators.
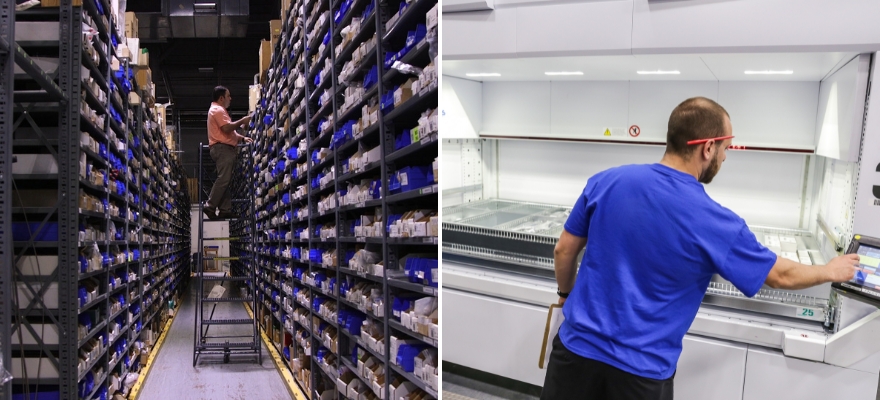
Modula’s VLMs retrieve trays with the stored items and deliver them to the user at the optimum ergonomic retrieval height. Thanks to features like the laser pointer, the item and quantity to be picked are immediately identified.
Compared to traditional shelving systems, items are directly delivered to employees, eliminating the need to walk up and down aisles or climb up and down stairs or ladders just to pick items.
The good news? Labor costs can also be decreased without laying off the workforce. Managers can create new revenue activities by reclaiming otherwise wasted space and labor, such as additional manufacturing or warehouse areas, or by processing more orders within the same operations.
Thanks to vertical storage solutions, they can also look ahead at the upcoming production to ensure efficient staffing and eliminate unnecessary overtime.
The learning process to operate the machines is also quick. Operators just need to simply learn how to operate the very user-friendly operator interface. In the case of the Modula VLM, a color touchscreen controller makes picking from the unit very simple and fast.
5. Waiting
Waiting is often the outcome of unbalanced processes causing a delay in flow. This leaves operators standing idle, waiting for the previous process to be cleared out or for the products to be delivered.
When production stalls, no value is being produced, but the cost of overhead operations continues to grow. This type of waste is also a result of a lack of information in the process, which may cause production staff to wait for instructions from other departments.
Lean manufacturing aims to ensure a steady flow in production, preventing any interruptions or bottlenecks by using techniques, such as value stream mapping and continuous improvement.
Just as lean manufacturing focuses on eliminating waste and optimizing flow, vertical storage solutions significantly help reduce the time spent on order processing.
Operators can process even complex orders (such as large volumes of orders) in the shortest possible time and with a high-quality level, even during peak workload times, as they don’t have to wait between jobs or when retrieving parts.
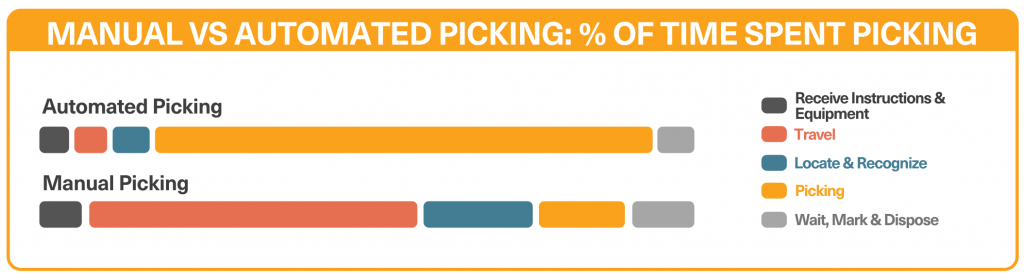
Vertical lift modules automatically deliver items to the operator with a simple touch on the copilot console or a scan of a barcode. This feature drastically reduces handling times both in picking and replenishing as there is no walking back and forth through the warehouse to find and retrieve ordered goods. Moreover, thanks to the simple inventory management software and the visual picking aids, operators can quickly and easily identify the items needed, reducing picking errors that could cause interruptions in the operations flow.
6. Inventory
Excessive inventory is a manufacturing waste, as it results in additional costs, such as costs for storage space, capital, inventory service, inventory risk and stockout.
For example, Storage space costs generate building and facility maintenance expenses. Inventory services costs are tied to insurance fees. Inventory risk costs involve the possibility that items might fall in value, or be damaged or lost over the period they are stored.
Lean manufacturing addresses excessive inventory in a warehouse through its “Just-In-Time” inventory system, which aims to align material orders from suppliers directly with production schedules.
By reducing inventory to only what is needed for near-term production, lean manufacturing minimizes storage costs, reduces the risk of obsolescence and frees up capital for other value-added activities.
VLMs can also significantly reduce the costs of inventory storage space, as they only take up a minimal footprint in a facility. It can also reduce the necessary size of inventory storage space by up to 90%, reducing building and maintenance costs.
Thanks to a height detection system, the height of each tray is measured as the tray is put away, allowing for the densest storage location to be determined in real-time, maximizing the storage density within the unit.
VLMs can reduce the costs of physical labor and the associated human resource expenses and decrease the costs associated with inventory risks by increasing inventory security.
The units can be configured to admit only authorized operators, and WMS can keep track of SKUs stored in the unit to reduce misplaced parts.
7. Transportation
Moving a product in a warehouse costs money, as it requires resources such as labor and equipment.
Lean manufacturing can help solve this problem by identifying the movement of products within the warehouse, creating a functional layout, and maximizing space to help your operations while eliminating the high cost of transporting products.
Thanks to the enclosed system of vertically arranged trays, Modula’s VLMs utilize the available room height from floor to ceiling, allowing for items to be stored up to 46 ft. high in a safe and secure unit.
Manufacturers can save valuable floor space and concentrate operations in a smaller footprint, eliminating motion and transportation waste.

Following the parts to pickers principle, these automated storage systems automatically deliver the items to the operator’s location. This reduces the movement of goods and the cost of potential damages during transportation.
8. Motion
Motion waste is typically generated by employees moving around without adding value to the process. This is typically caused by an inefficient warehouse layout.
This type of waste can also result in physical injury to employees, which may incur even greater costs to the business.
Lean manufacturing can solve this waste by applying lean warehousing principles and value stream mapping to optimize the warehouse layout for more efficient workflow.
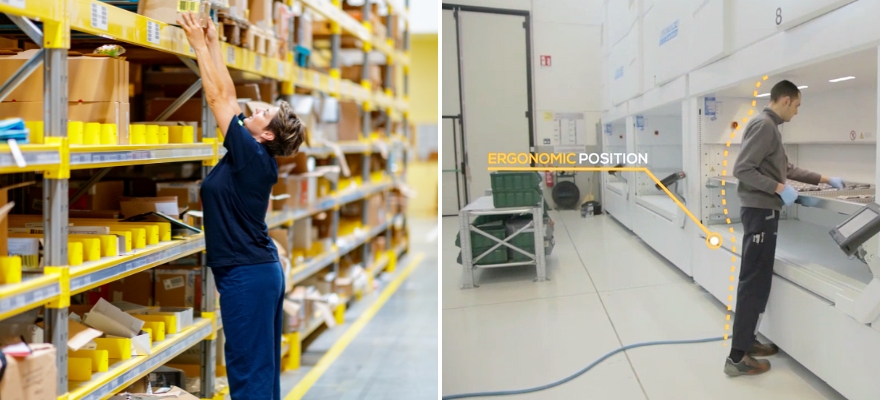
Vertical lift modules automatically deliver parts to the picker at an ergonomic height
By designing the layout to minimize travel distances between workstations and storage areas, lean manufacturing aims can reduce the amount of unnecessary movement.
Vertical storage solutions can also easily solve this problem, as they automatically deliver parts to the picker, rather than having the picker go and locate the parts within long aisles of shelving and cabinets.
Walking time for parts retrieval is reduced up to 70% when compared to static shelving. Consequently, non-productive indirect labor is replaced by more productive direct labor and productivity can be increased by approximately 2.5 times.
Vertical storage solutions significantly reduce the risk of injury from motion and offer maximum safety for personnel in even the most demanding working conditions.
Inventory is delivered directly to employees without exposing them to moving parts or requiring them to use heavy machinery.
Products and tools are removed from the floor, eliminating tripping hazards and many safety features including security light curtains to prevent injuries for operators.
Lean Manufacturing Best Practices
Ready to eliminate waste in your facility? Here’s how to fully integrate the lean manufacturing approach in your warehouse:
1. Train Your Warehouse Operators
When employees are well-trained, they feel more competent and empowered to do their jobs. This can lead to increased job satisfaction and lower turnover rates.
To train your warehouse operators:
- Provide new employees with a clear introduction to your warehouse processes, including lean management principles.
- Conduct regular training sessions on lean principles and techniques. Offer hands-on training for your employees, including shadowing, role-playing exercises and mock simulations.
- Provide specific training on lean manufacturing methods, such as value stream mapping, visual management and waste reduction techniques.
2. Implement Warehouse Automation
Automation complements lean practices by making operations more efficient and removing waste.
Automated warehouse solutions, like automated storage and retrieval systems and automated warehouse pickers, can eliminate manual tasks, such as transporting heavy inventory and manual picking.
On the other hand, vertical lift modules can maximize your available warehouse space by taking advantage of your ceiling height.
3. Encourage Continuous Improvement
Lean is all about continuous improvement, as it focuses on constantly identifying and eliminating waste and inefficiencies in warehouse processes. This ongoing effort reduces costs, speeds up production and improves overall quality.
To encourage continuous improvement in your warehouse operations:
- Hold regular team meetings to identify opportunities for improvement and discuss ideas on how to resolve bottlenecks in warehouse operations.
- Host formal kaizen events— an approach to creating continuous improvement — in which your team works together to solve a problem, such as how to improve your warehouse’s layout.
- Review and update standard operating procedures and policies to implement best practices.
At Modula, we offer leading automated storage solutions to help you make the most of your existing warehouse space, boost productivity and improve picking accuracy, all while adapting to changing customer demands.
If you’re not sure about the best storage options for your needs, reach out to our material handling experts. We’ll perform a thorough warehouse audit to help you find the right solution for your facility.