The True Cost of Warehouse Storage Racks + The Benefits of Automation
Static warehouse storage racks are simple and cost-effective at first glance — but a closer look reveals hidden costs and compromised efficiency.
The truth is, traditional warehouse storage racks and shelves are inherently inefficient, wasting space and time, in addition to posing safety hazards and organizational issues.
The alternative? Automated warehouse racking systems, which can reduce space requirements by up to 90% and dramatically boost warehouse efficiency.
If you’re still utilizing static storage solutions throughout your warehouse, it’s time to make the switch — and we’re here to explain why. We’ll share the top challenges associated with traditional storage, and explain why the answer is automated.
What are Warehouse Storage Racks?
Warehouse storage racks are storage solutions designed to house and organize inventory in horizontal rows across multiple levels.
These warehouse shelving systems are typically made of durable materials like steel or aluminum, and they come in various configurations and load capacities to accommodate a wide range of inventory.
Industrial Shelving vs. Racking Systems
Industrial shelving is ideal for storing small parts that can be picked by hand, while racking systems are designed to handle larger and heavier loads that require the assistance of forklifts.
While industrial shelving can be used to pick and place goods manually, racking systems are equipped with wider and deeper trays, and are often stacked higher to maximize vertical space.
Accessing larger loads, such as entire pallets or large boxes, from a racking system typically requires the use of heavy equipment.
5 Types of Manual Warehouse Storage Solutions [+ Challenges of Each]
From conventional shelving to mobile pallet racking, here are five types of traditional warehouse storage solutions, along with the challenges that come with each.
1. Conventional Shelving
Conventional shelving, also known as static shelving, is one of the most common types of warehouse storage. It is composed of static, free-standing units with horizontal shelves supported by vertical posts.
These storage systems are typically used for storing small parts that can be easily picked by hand, making it a good option for manual order picking operations.
When it comes to challenges, conventional shelving:
- Reduces productivity, as warehouse operators are required to manually navigate their way around the warehouse to store and pick inventory
- Accommodates the tallest item, leaving more room than necessary for smaller items
- Takes up most of your warehouse space
- Requires aisles to allow manual picking and placing of items.
- Poses a risk hazard for warehouse operators who need to reach low and climb high to retrieve items
2. Pallet Racking
Pallet racking systems are used in warehouses to store and organize pallets or large containers.
This type of warehouse storage is composed of upright frames and horizontal beams that create a stable structure for storing pallets. The pallets are then stored in horizontal rows, on multiple vertical levels.
When it comes to challenges, pallet racking:
- Requires forklift trucks to load and unload materials from racks
- Poses safety risks if not properly installed and maintained, such as falling objects and structure collapse
- Requires wide aisles to allow forklifts to access heavy loads
- Lacks the ability to accommodate changes in inventory size or storage requirements
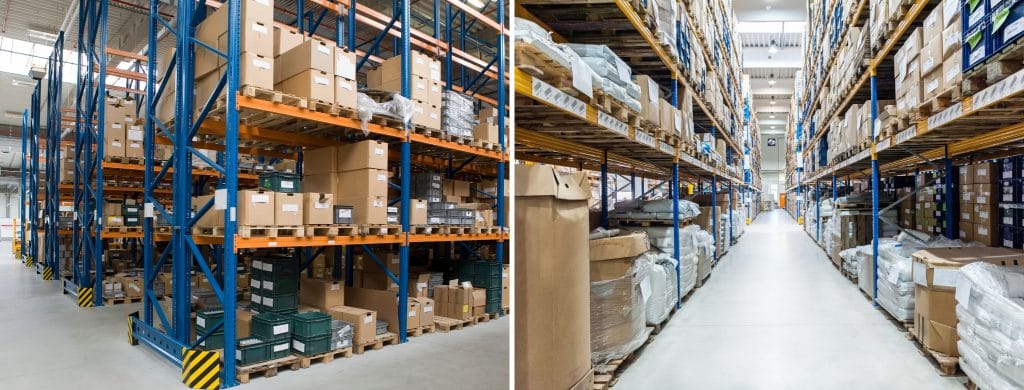
3. Compact or Narrow Aisle Shelving or Racks
Narrow aisle shelving systems are warehouse storage solutions that have narrow aisles between the shelving units. They are ideal for small warehouses that need to take advantage of every inch and corner of the facility.
Narrow aisle shelving systems are designed to maximize storage density while minimizing aisle space. These storage solutions require forklifts specifically designed to maneuver in tight spaces.
In addition, the smaller space between the shelves translates to less room for workers or forklifts, which requires additional safety measures and specialized handling equipment that can safely load and unload items within the limited aisle width.
Narrow aisle shelving units are ideal for homogeneous products, primarily with low or medium rotation, in smaller warehouses where space is at a premium
When it comes to challenges, narrow aisle shelving:
- Requires specialized handling equipment
- Requires additional safety measures due to the narrow aisles
Reduces picking rates due to narrow aisles and limited accessibility to individual items - Increases the risk of damage to stored goods and equipment passing through
- risk of damage to stored goods and equipment passing through
4. Mobile Pallet Racking
Mobile pallet racking, also known as mobile racking, is a warehouse storage system that works by mounting traditional pallet racks onto motorized carriages or bases that run on rails installed in the floor.
The entire racking system can be moved along the rails, allowing for multiple racks to be positioned closely together when not being used.
When it comes to challenges, mobile pallet racking:
- Requires regular maintenance to ensure optimal efficiency — any malfunction or breakdown in the system can also disrupt warehouse operations, leading to costly downtime
- Reduces productivity compared to conventional shelving systems, as the sliding of the racking system takes time
- Requires additional training for warehouse staff to ensure proper use and safety, as it is more complex than conventional shelving
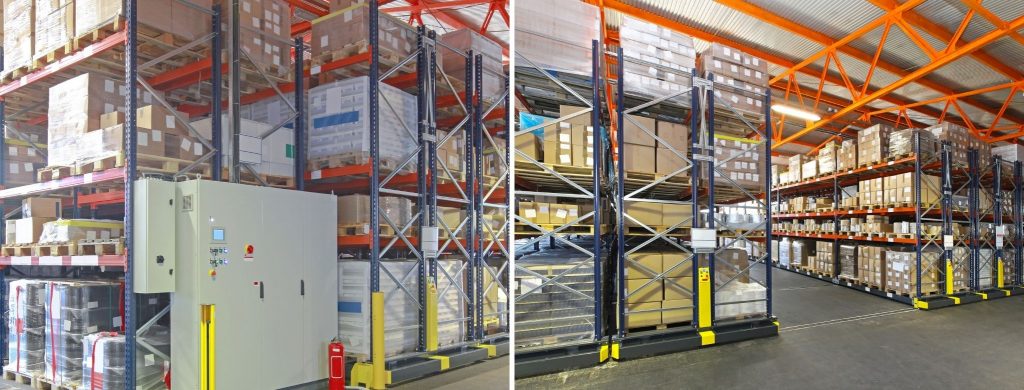
5. Drive-in and Drive-Through Racking
Drive-in and drive-through racking systems are variants of compact shelving. They are designed to maximize the available space and height of a warehouse by reducing the forklift operating aisles.
Drive-in racks have only one access aisle and are based on the last in, first out (LIFO) method, meaning that the last pallets loaded will be the first to be unloaded.
On the other hand, drive-through racking has an entrance and exit that follows the first in, first out (FIFO) method. However, they offer a less compact storage space as they require an additional aisle.
When it comes to challenges, drive-in and drive-through racking:
- Limit the measurements of the loading units and the number of references that can be stored
- Reduce flexibility in warehouse operations due to limited selectivity and loading/unloading sequence requirements
- Increase the risk of product damage, as forklifts need to enter the racks to load and unload inventory
- Slow down the picking process due to the need to navigate the deep storage lanes in drive-in and drive-through racking systems
- Pose higher installation costs due to specialized design and the need for forklifts and handling equipment
Benefits of Automated Warehouse Racking Systems [Like Automated Storage and Retrieval Systems]
Automated warehouse racking systems can improve productivity and efficiency in your warehouse operations, while ensuring that your operators are safe in their day-to-day activities.
Key benefits of automated racking include:
- Increases storage capacity: Instead of moving into a bigger warehouse that can cost you up to $8 per square foot, automated warehouse racking systems take advantage of the existing vertical and horizontal space in your warehouse, resulting in a significant increase in overall storage capacity compared to traditional manual systems.
- Improves productivity: Automated warehouse racking systems significantly reduce the time needed for picking, as the inventory is automatically delivered to warehouse operators. In addition, these systems can work around the clock, eliminating downtime.
- Enhances accuracy: Automated warehouse racking systems are less prone to human error, resulting in greater picking accuracy.
- Optimizes space: Automated warehouse racking systems optimize warehouse space, resulting in a more efficient and organized warehouse layout.
- Boosts workplace safety: Automated warehouse racking systems can reduce the risk of accidents (like overexertion) by eliminating the need for human intervention, such as reaching inventory in high and low areas.
- Improves inventory control and tracking: Automated systems include advanced software for inventory management, providing real-time insights so you can gain complete visibility into your stock levels and item movement. Ultimately, this leads to accurate demand forecasting and better stock control.
- Allows for scalability: Automated warehouse racking systems can be modified to your inventory type, size and shape, helping you meet changing business needs or storage requirements.
Modula’s Automated Warehouse Racking Systems
As an industry leader in the manufacturing industry, our automated warehouse racking systems are designed to help you maximize your existing warehouse space, boost productivity, improve picking accuracy and gain inventory visibility across your warehouse facility.
1. Modula Vertical Lift Modules
The Modula vertical lift module (VLM) is a tall, towering storage solution that resembles a vending machine, with internal shelves that safely store goods.
The shelves are adjustable, and the machine helps optimize the arrangement of the stored goods to maximize the VLM’s capacity.
As a result, Modula VLMs can help you reduce your warehouse space requirements by up to 90%.
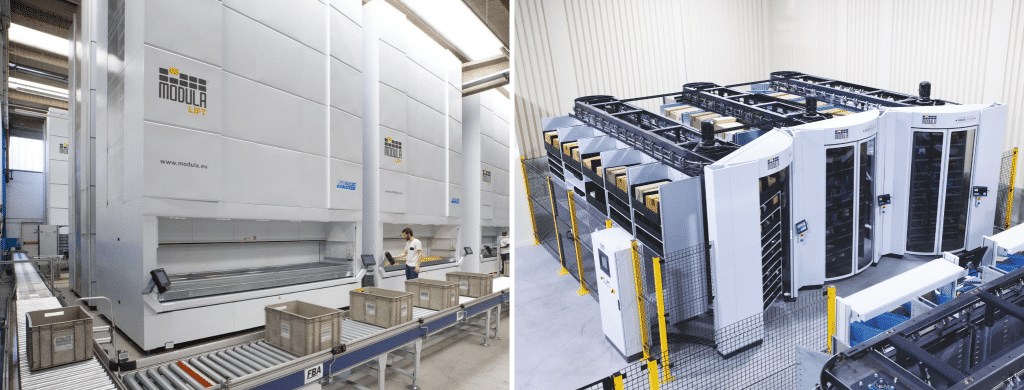
By tapping on the intuitive screen, your warehouse operator automatically receives items at an ergonomic height from the VLM.
Since there’s no need for multiple expansive aisles and scattered shelving, a VLM drastically reduces space requirements.
Our VLMs come in two models — Modula Lift and Modula Slim. Each model utilizes minimal floor space by taking advantage of high ceilings instead.
In addition, Modula VLMs allow you to:
- Process more orders in less time with a throughput of up to 140 trays per hour
- Manage inventory security with a reliable locking and validation feature
2. Modula Horizontal Carousels
The Modula horizontal carousel (HC) offers the same advantages as the VLM. The only difference? The Modula HC takes advantage of the horizontal space, where ceiling height is limited.
The Modula HC allows you to:
- Modify shelf spacing to store a wide variety of inventory
- Experience high-speed picking in a low-ceiling environment
- Achieve better productivity with picking rates of up to 550 lines per hour
- Obtain full traceability of stock levels and orders
Key Takeaways on Warehouse Storage Racks
Manual warehouse storage racks are key components in an efficient warehouse, however, they can have limitations in terms of space utilization and adaptability, compared to automated warehouse storage racks.
By investing in automated warehouse storage racks, you can improve productivity, reduce mispicks, and ensure that both your employees and inventory are safe.
From eliminating the need to lift heavy inventory and reach items from high and low areas to reducing the need for manual picking, both the VLM and HC address safety, organization, and productivity concerns that stem from traditional shelving.
At Modula, we offer leading automated storage solutions to help you optimize space, boost productivity, and meet changing consumer demands.
Contact our Modula team of material handling experts for a free evaluation of your warehouse. We’ll help you find the right solutions to boost efficiency across your organization.