Horizontal Carousel FAQs Part I: Comparison to Vertical Lift Modules
Horizontal Carousel Storage Systems: Answers to the Most Common Questions
The Modula HC New Generation is the most up-to-date and reliable horizontal carousel available on the market today. While horizontal carousels have been around for many years, deciding whether to buy one, a vertical lift module or another automated storage system can require a careful analysis. Both technologies offer similar efficiency gains: better storage density, higher productivity, fewer picking errors and a far better inventory control compared to shelving and racks.
There’s a lot to know about the topic, so we’ve divided these FAQs into two parts.
In the first part, we’ll compare horizontal carousels with vertical lift modules. In the second part, we’ll take a look at how the Modula HC can be employed to address varying applications where an automated storage and retrieval solution may be useful.
While we provide an extensive amount of detail in these two parts, we advise talking to a Modula sales representative to get a more definitive answer for your specific application.
Comparing horizontal carousels to vertical lift modules
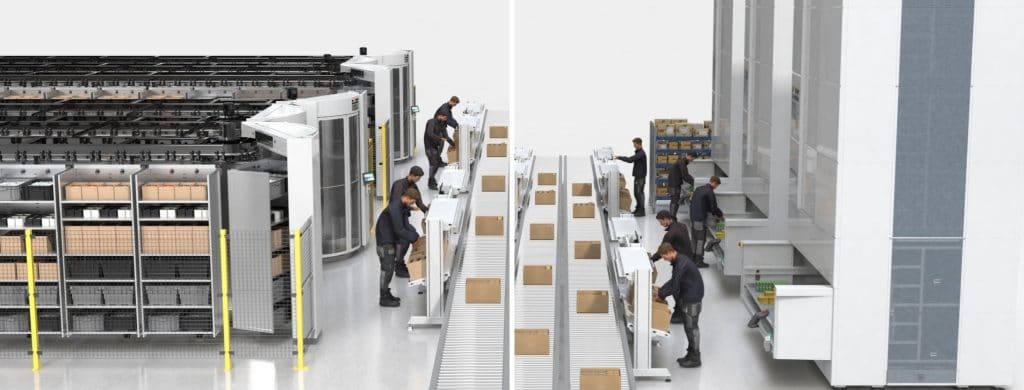
For which applications is the horizontal carousel a better choice than a vertical lift module?
The biggest factor is the ceiling height in your facility. Choose a horizontal carousel if your ceiling is below 10 feet. For higher ceilings, a vertical lift module is a better choice. But there are other key factors to keep into consideration such as the size and weight of the parts being handled as well as the business cycle and fulfillment requirements
How does a horizontal carousel compare to a VLM in pick speeds?
Pick speeds vary highly, depending on the distribution of material within the storage system, the line item per order density, and any self-imposed process times, like bagging, tagging, or weigh counting items. Both systems can pick 130-550 items picks per hour if configured to do so. Again, ceiling height should be the main consideration, together with other logistical and operational aspects.
Does a horizontal carousel have imbalance issues similar to those on a vertical carousel?
No. Each bin/carrier is independently supported on the Modula Horizontal Carousel and the operation is not affected whether a bin is at its maximum weight or empty. It is recommended to avoid loading the unit to its 1,200 pound (544 kg) maximum capacity regularly because this will cause premature wear.
Which technology is best in terms of storage density – a vertical storage solution or a horizontal carousel?
Horizontal carousels do not utilize the vertical cube as well as vertical storage solutions, therefore they require more floor space to operate. Vertical lift modules utilize the vertical air space so their footprint is relatively small. Both offer much better storage density compared to traditional racks or shelves.
Is it true that horizontal carousels are great for picking, but they require a great deal of time to replenish?
Not if the operator slots products and sizes properly, which would result in only replenishing 5-10% of the operation’s SKUs daily and require an hour to complete.
What is the ROI on a horizontal carousel or VLM?
Implementing a horizontal carousel warehouse or a vertical lift module into your operation is an investment that can create an effective ROI in as little as six months. This is due to the improved floor space utilization, reduced labor costs, increased picking accuracy, and better inventory control.
Which type of products/parts cannot be stored in a horizontal carousel?
Single items that would be strenuous to move by a single operator, weighing around 25kg (55 lbs), are better stored in a system that allows work aids to be involved such as a vertical lift module. The Modula HC is designed for human retrieval, not machines.
VLMs are also a better fit for special products that require a secure and clean environment. In an HC, products are stored in open bins/shelves subject to airborne contaminants. By contrast, a vertical lift module is fully enclosed with an automatic door. This prevents goods from being damaged and minimizes exposure to the warehouse environment.
Is there an ideal item size for storage?
A horizontal carousel is best used when picking slow- to medium-moving split case items as well as slow-moving small boxes and with high retrieval rates in which the product mix doesn’t change much. This is because the shelves in a horizontal carousel bin are vertically adjustable on 2” centers. The location is set during the installation. If the product height changes, you would need to readjust the location within the bin.
Besides the physical size limits, an ideal SKU should have a replenishment cycle of 3-6 weeks and a cubic movement over that time that does not take up more than one bin of space.
Is it possible to store liquids?
It depends on local jurisdiction. Typically, if you can ship it over the road without requiring the use of special accommodations you can store it in a horizontal carousel.
Can horizontal carousels be used in cold room applications?
The answer depends on certification requirements, but the minimum permissible temperature inside a building with an operator is 41° F (5° C). Ask your representative about installations in colder environments.
If you have any other questions or would like to learn more about this technology, contact our Modula HC team of specialists.