What is Buffer Storage? A Complete Guide. Benefits + How to Automate Your Buffer Storage
Automated buffer storage management can help your warehouse or production site keep up with increasing consumer demand, help you manage supply chain disruptions, and more.
But how does it work exactly? We’re here to explain.
In this article, we’ll share everything you need to know about buffer storage, including the benefits it offers, how to set up a storage buffer and how automation plays a key role in streamlining the process.
What is Buffer Storage?
As the name implies, buffer storage, also known as safety stock, is used in manufacturing to temporarily store materials before they move into another production process. It is also used to store safety stock needed in the manufacturing process, in case supply chain shortages, transportation delays or unexpected surges in demand occur.
Ultimately, buffering ensures production doesn’t reach a standstill.
Buffer storage is also quite common in warehouses and fulfillment centers, where inventory is the biggest asset.
For example, a stockout, or out-of-stock (OOS) occurs when inventory becomes unavailable, preventing an item from being purchased or shipped, resulting in a loss in sales. This can happen anywhere in the supply chain, and can result in a loss of sales and affect brand reputation and customer loyalty.
Recent data from Adobe shows that stockouts were up 250% in 2021, compared to pre-pandemic levels.
One survey found 69% of consumers will choose a substitute item when a product is out of stock, and after three of them, 70% will opt for a different brand entirely.
For warehouses and fulfillment centers, having a buffer in the inventory of finished goods is a worthwhile investment when the demand is greater than anticipated. In addition, it prevents stockouts caused by unexpected delays from suppliers and streamlines the order fulfillment process.
How to Implement an Efficient Buffer Storage Area
Today’s manufacturers, suppliers, and retailers often rely on safety stock inventory, or buffer stock, to mitigate this risk, keep up with manufacturing demand and meet customers’ expectations. In addition to buffer stock, they can also rely on warehouse consolidation or the act of storing shipments in one warehouse.
An organized and efficient buffer storage area positioned in the right location within the warehouse is a key factor.
Generally, goods in the buffer area are stored for a short time, waiting to be moved on to the next process, such as production, consolidation area or shipping for final products.
This inventory should be quick to locate and easily accessible.
A such, Buffer storage should be positioned near receiving and shipping areas, and along manufacturing lines in a warehouse to ensure a seamless workflow of goods.
1. Benefits of Buffer Storage
- Guarantees production lines continue to run smoothly even during supply chain disruptions and shortages
- Helps stabilize any fluctuations in supply and demand chains and lead times
- Prevents delays in order fulfillment and lost revenue from being out of inventory
- Assures stability and flexibility during unforeseen circumstances
2. Disadvantages of Buffer Storage
- Space utilization: Buffer storage areas can take up a large amount of space
- Additional Labor: Dedicated resources are needed to manage and maintain this storage area
- Additional costs: Such as inventory services costs and inventory risk costs, due to the possibility that items might fall in value, be damaged or lost over the period they are stored
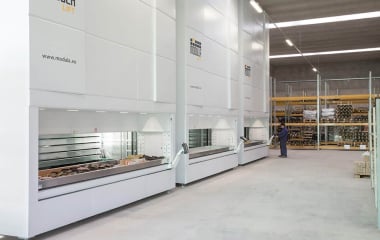
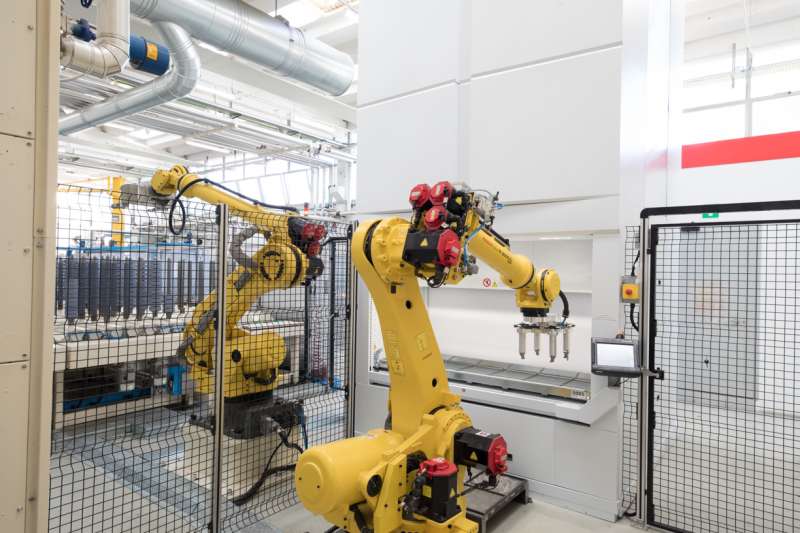
How Does Buffer Storage Work with AS/RS?
Automated storage and retrieval systems (AS/RS) drastically help streamline buffer stock management.
AS/RS are fully automated storage and picking systems that take up a minimum footprint allowing for a large inventory of raw materials or final products to be stored in small footprints near receiving and shipping areas, and along manufacturing lines in a warehouse.
Both raw materials and final products can be stored in a high-density storage location, reducing the storage footprint by up to 90%.
Following the parts-to-pickers principle, automated warehouse storage solutions transport items directly to the operator.
AS/RS reduce handling times both in picking and replenishing since there’s no walking back and forth in the buffer storage area to find and retrieve goods.
Thanks to visual picking aids, the user quickly identifies the quantity requested and which item should be picked, optimizing how goods flow from and to the buffering area.
To further improve efficiency, you can integrate warehouse management software, which will:
- Provide inventory quantity reports in real-time
- Notify you when products are running low to prevent shortages or when your inventory has reached a maximum quantity to deliver goods in the first in, first out (FIFO) method
- Alert warehouse operators when the buffer stock is ready for delivery
In addition, you can integrate a conveyor system or mobile automated robots with your AS/RS to deliver buffer stock to your operators.
Benefits of Automated Buffer Storage Management
An automated buffer storage management system provides a secure, organized and enclosed space for your buffer stock to safeguard both your products and employees.
From saving warehouse space to preventing picking errors, here are five key reasons to invest in automated solutions for your buffer stock.
1. Saves Space
Instead of allotting a section of your floor area to store temporary goods, an automated storage buffer helps you save space by providing a dedicated and organized container to accommodate your products.
At Modula, we maximize your available warehouse space by thinking vertically and horizontally. Our vertical solutions utilize warehouse height, while our horizontal solutions utilize warehouse width.
2. Prevents Workplace Injuries
Cluttered floors caused by scattered boxes and goods waiting to be delivered pose a safety risk for employees. In fact, falls on the same level or trips ranked as the second most disabling United States workplace injury in 2021.
Instead of depositing goods on the floor, an automated storage buffer allows employees to walk safely in dedicated pathways, by providing an organized space for housing temporary goods.
3. Streamlines Availability of Goods
From toilet paper to sriracha hot sauce, it’s no secret that the supply chain shortage poses a challenge to the warehousing industry.
Whether you’re facing a supply chain disruption or an unexpected uptick in demand, implementing an automated storage buffer can help you address the challenges of the warehousing industry.
In addition, an automated storage buffer streamlines the order fulfillment process by preventing delays and interruptions.
4. Ensures Security
Whether you own a small business or large enterprise, warehouse theft can occur with a lack of stringent security measures.
Even retail giant Amazon has experienced warehouse theft — in 2022; a warehouse manager stole $273,000 worth of computer parts from an Amazon warehouse in North Carolina.
While there are different ways to prevent warehouse theft such as monitoring staff and limiting access to products, implementing an automated storage buffer secures goods in an enclosed system until they are dispatched to your customers, increasing security.
5. Prevents Mispicks
In your automated storage buffer, products are organized following the order in which they will be dispatched, to minimize errors and streamline supply.
At Modula, we prevent mispicks from occurring with our Put to Light Systems.
Instead of manually reviewing pick tickets or paper lists, our Put to Light Systems guide operators to the correct location to accurately pick multiple orders.
Modula Solutions for Buffer Storage Management
At Modula, we elevate the management of buffer stock with the most advanced automated storage and retrieval systems. Our automated solutions save space, improve employee safety, prevent mispicks and boost workforce productivity and accuracy.
1. Modula Vertical Lift Modules
Streamline your warehouse storage by thinking vertical. At Modula, we offer two vertical lift modules:
- Modula Lift, our most popular vertical lift module, is the perfect storage solution for industrial goods, components and spare parts for every workplace environment and industry.
- Modula Slim is the optimal storage solution for warehouses with limited floor space.
Our Vertical Lift Modules allow you to:
- Save 90% of floor space by using a minimal footprint, taking advantage of the available ceiling height
- Increase picking speeds of 300 lines per hour or more
- Keep your goods safe by securing them in an enclosed system with restricted access
- Receive goods automatically thanks to the user-friendly Copilot controller
- Boost inventory management with monitored and documented picking operations
- Improve safety for warehouse operators by eliminating the need to reach for products
- Accommodate heavy loads without strain
- Reduce employee and operational costs
2. Modula Horizontal Carousels
If your warehouse ceiling height is limited, our Modula Horizontal Carousels offer the perfect storage solution.
Our Horizontal Carousels allow you to:
- Store more goods with compact and high-density storage areas
- Retrieve items quickly and easily with Modula’s digital Copilot feature
- Integrate with Modula Warehouse Management Systems (WMS) to boost accuracy and productivity
- Promote 99% picking accuracy with our Put to Light Systems and barcode readers
- Utilize picking rates of up to 550 lines per hour for each warehouse employee
- Offer the most ideal working environment by protecting employees against hazards, minimizing physical strain, enabling fast machine stoppage and removing unessential travel around the warehouse
- Monitor picking operations in real-time thanks to automation
3. Warehouse Management Solutions
Take your automated storage systems to the next level with our warehouse management solutions to increase accuracy, productivity and efficiency.
Our Warehouse Management Solutions allow you to:
- Access extensive inventory control and visibility
- Boost accuracy when integrated with our automated storage solutions, as well as retrieval methods including picking and shelving
- Gain better control over managing inventory, materials handling and preventive maintenance guidance
- Operate in batch and multi-order modes without compromising productivity and quality for larger than usual orders

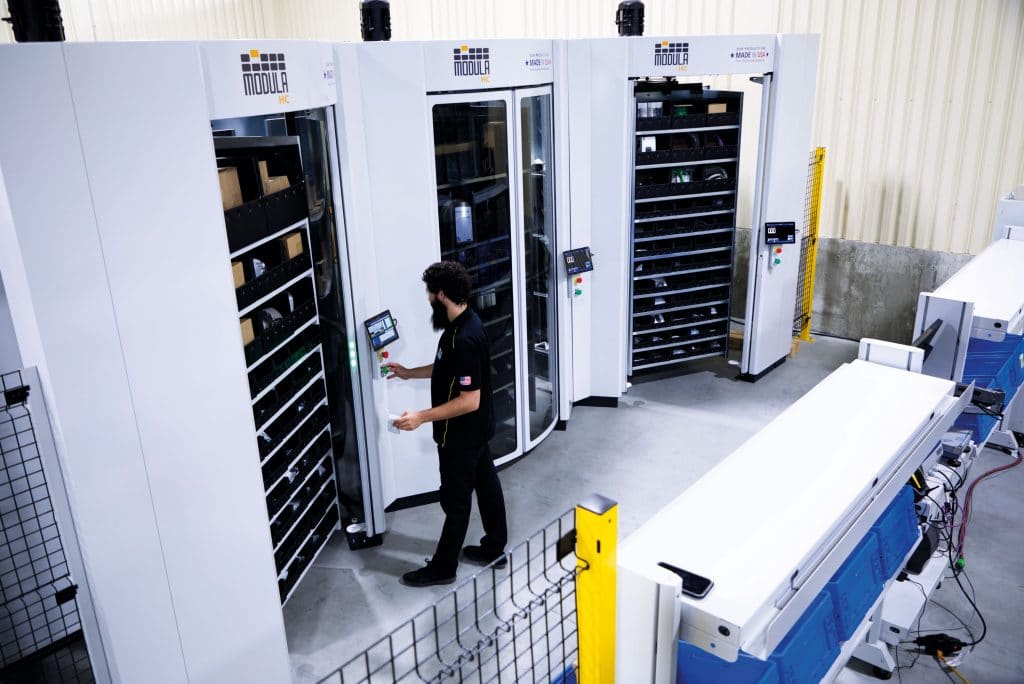

4. Modula Warehouse Order Picking Solutions
Easy to install and navigate, our order picking solutions are ideal for boosting your buffer storage management when dealing with multi- and batch orders.
Our Modula Warehouse Order Picking Solutions include:
- Modula Put to Light to guide your warehouse operators to the accurate location on a station or cart in which to “put” the items
- Mobile Picking Station to process large quantity orders in less time
- Modula Picking Cart to move retrievals to different locations within your warehouse
- Modula Mobile Picking App to manage your manual picking operations from the touch of your smartphone or tablet
Wrapping Up on Buffer Storage
Even more than just storing additional goods to meet unexpected scenarios, buffer storage is a vital process in your warehouse operation, as it secures your products and optimizes your warehouse space.
At Modula, our automated storage and retrieval systems are built to streamline your warehouse operations and how you manage your buffer stock.
Redefine how you store your buffer stock with our most advanced storage and retrieval systems at Modula.