Batch Picking 101: All You Need to Know About the Process
From single order picking to multi-order picking, there are several different types of order picking that will help streamline your order fulfillment process.
With 131 billion packages shipped worldwide in 2020, the need for efficient warehouse picking has never been greater. It’s crucial to choose a method that will boost labor productivity, fulfill customer satisfaction and cut costs.
If you’re curious about batch picking, you’ve come to the right place. In this article, we’ll cover all you need to know about this method, from how it works and the difference between batch picking vs. order picking, plus the technologies and sectors where it works best and when you should use it.
What Is Batch Picking?
Batch picking, also known as multi-order picking, is a method that allows your pickers to work on multiple orders or batches at the same time. Compared to other order picking methods, it is the most efficient, since your employees move around your warehouse less, which cuts time on travel between orders.
Your pickers can go through orders faster, further speeding up the order fulfillment process.
How Does Batch Picking Work?
In this method, the operator picks multiple items of the same type at the same time (batches) and then sorts them into the different orders. Once finished, the batch of orders moves to another storage area where additional items will be picked, until the orders are complete.
The goal of this method is to reduce the number of trips employees have to make to the picking areas, to increase operational efficiency.
Here’s how it works:
1. Create a Picking List
First, you create picking lists.
A picking list can be manually generated, or you can use a warehouse management system (WMS) or order management system (OMS). A picking list is a document that reports the items to be shipped, the quantities for each item, and their storage location in the warehouse.
2. Group Orders with the Same Picking Requirements
Next, your pickers will receive their picking list and will use equipment such as mobile scanners, carts, or totes to fulfill each order. Additional technology such as voice-picking headsets can also be used in this stage to assist your picker with an item’s location.
In this stage, an inventory management system or WMS also helps to automatically group orders with the same items into a batch.
3. Assign the Picking List to Pickers
If you’re working with automation, your inventory management system or WMS calculates the best route to minimize your employees’ travel time and generate the picking lists for each picker.
4. Pick Items
Next, it’s time to pick the items. Picking ranges from pushing a cart that includes totes for each order to combining all SKUs into a single bin that will then be packed, sorted, and delivered.
The warehouse operator, following the picking list, picks the items according to the route. Once the assigned batch orders are completed, they move to the personnel in charge of packing.
5. Pack and Ship Orders
Last but not the least, it’s time to pack and ship your customers’ orders. Once finished, the batch of orders moves to another storage area where additional items will be picked, until the orders are complete.
Batch Picking vs. Order Picking: What’s The Difference?
Batch picking and order picking are the most common warehouse picking methods.
Order picking, also known as single order picking, is the most common method that a picker uses to retrieve a product individually from its designated location. It’s designed to pick one order at a time.
While single order picking is simple and easy to understand, it is the least efficient method, as it requires more travel time for picking. With the average picker retrieving 60-80 orders per hour, single order picking can slow your picking process, since pickers retrieve items one by one.
On the other hand, batch picking allows multi-order picking. In this method, pickers arrange order batches by SKU.
Unlike order picking, which requires many visits to a location depending on the order, picking by batches allows an employee to only visit the picking location once, saving more time.

What Technologies Are Used for Batch Picking?
To efficiently implement this order picking method, ad hoc software can be used to reduce the distances that need to be covered and the repetition of movements.
Warehouse management systems (WMS) are solutions designed to support logistics operations while helping you manage your storage systems.
At Modula, our Warehouse Management System controls, coordinates, and optimizes all handling operations quickly, accurately, and automatically.
Modula picking aids for order preparation are:
- Put to Light – This system provides a display that guides the operator to the positions in which to put the items of each order. For each item, the display visually indicates the container and quantity of each SKU to be inserted. Thanks to the WMS, the Put to Light system can also be implemented for the multi-order picking method.
- Picking Station – These are steel structures with shelves for containers, which can be integrated in traditional warehouses with manual transport or in modern warehouses with automated transport. These are the structures on which the Put to Light device works best.
- Picking Carts – Unlike fixed Picking Stations, Picking Carts are maneuverable carts with pivoting wheels. They are equipped with shelves for containers and Put to Light displays for the easy identification of the container in which the picked item must be placed. Picking Carts for multiple orders may be used in warehouses with traditional shelving as well as in automatic storage systems.
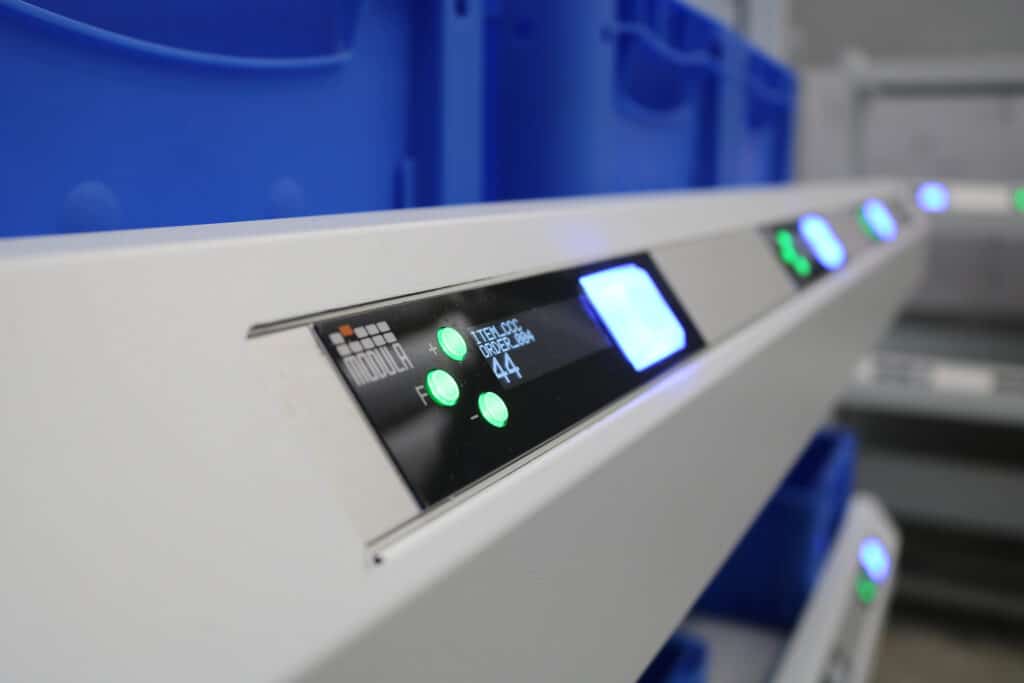
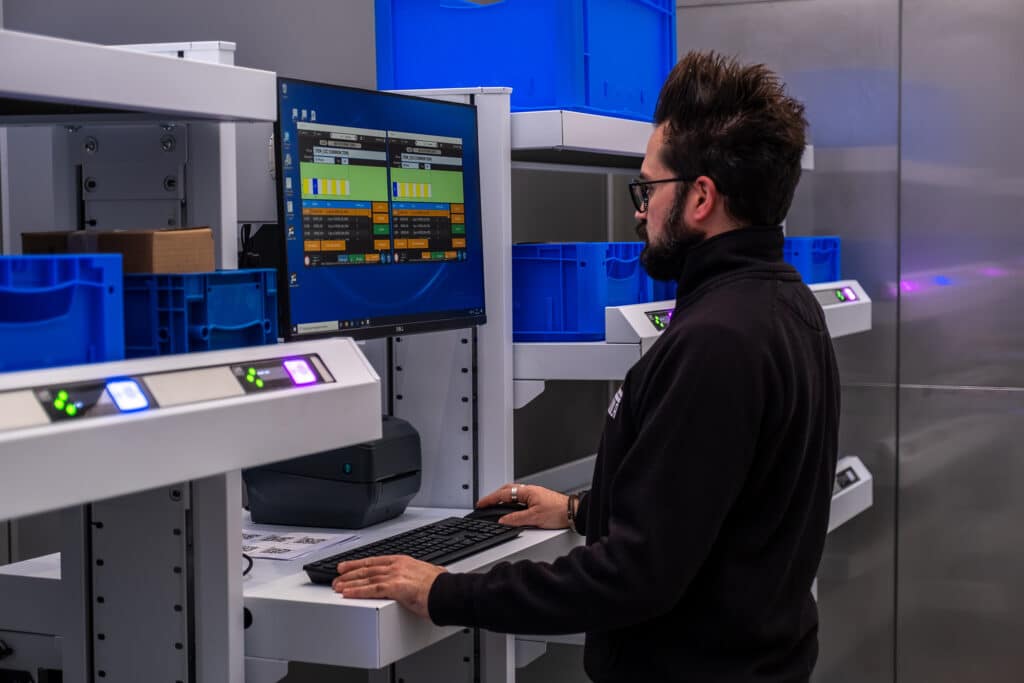
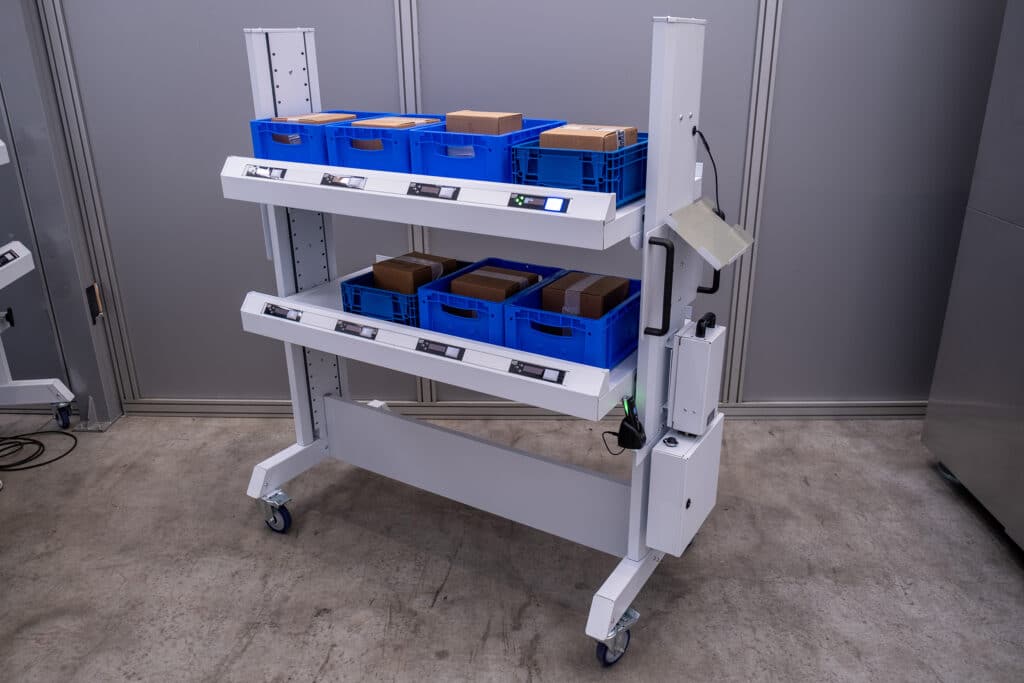
Benefits Of Batch Picking
This order picking method is particularly effective and optimized when:
- Your picked items are homogeneous and small in size. In this way, your operator can easily prepare batches of orders by placing them in the picking cart.
- Your company has many orders to process. Order preparation and retrieval times for the items involved are reduced, which results in less warehouse congestion.
- Orders have just a few and homogeneous SKUs. The picking and sorting processes can be carried out simultaneously, with a further reduction of picking errors.
The advantages include:
- Decrease of the number of trips
- Reduction of labor and related costs
- Reduction of employee fatigue
- Increased productivity
In addition, with the Mobile Picking APP, compatible with Android systems, it is possible to communicate directly with the Modula WMS which guides the picker, thus increasing efficiency.
Which Sectors Use Batch Picking the Most?
Batch picking offers multiple advantages for warehouses, including reducing travel time in your warehouse, decreasing employee fatigue and increasing productivity.
This makes it the preferred picking strategy for e-commerce – regardless of the sector – where order preparation speed and accuracy must be at the highest levels.
To learn more about our Vertical Lift Modules and Horizontal Carousels and how automation can help you efficiently manage E-Commerce Fulfillment: