MotoMart Optimizes Agricultural Spare Parts Management with Modula
MotoMart Case Study Summary
MotoMart, a leading agricultural equipment distributor in Colombia, has been serving the agricultural sector for over four decades.
With the acquisition of Amarillo Machinery and the need for more storage, the company turned to Modula for an efficient, space-saving solution. By installing two Modula ML50D Lifts, MotoMart achieved an 80% reduction in storage area and streamlined their spare parts management process. With integration into their ERP system and advanced features like laser pointer and LED bar technology, the Modula systems have enhanced inventory control, reduced search times, and enabled MotoMart to offer faster, more reliable service to their customers.
The Challenge
MotoMart’s expansion into a new building, prompted by the acquisition of Amarillo Machinery, required a solution that could store a larger inventory while minimizing the storage space needed. Previously, the company relied on traditional shelving and manual searches for parts, which was time-consuming and inefficient. With customer service being a priority in the agricultural sector, MotoMart needed a solution that could provide quick access to spare parts and improve warehouse efficiency.
The Solution
MotoMart integrated two Modula ML50D Lifts into their new warehouse, taking advantage of the full height of their facility. This allowed the company to reduce its storage footprint by 80% and expand their service and repair areas. Modula’s WMS integration with MotoMart’s ERP system. This allowed them to streamline their spare parts management, making it easier for employees to locate parts and quickly fulfill customer orders.
The Modula systems are equipped with advanced features. These include the Co-Pilot touchscreen console, laser pointer, and alphanumeric LED bar, which guide operators to the exact location of each spare part, improving accuracy and reducing search times. The ability to search for parts on a PC and have them delivered to the appropriate bay instantly further enhanced the efficiency of the picking process.
Key Benefits of the MotoMart Case Study:
- Space Optimization: By utilizing the vertical space, MotoMart reduced their storage area by 80%. As a result, they expanded the service and repair areas.
- Improved Efficiency: Features like the Co-Pilot console, laser pointer, and LED bar reduce search times. Moreover, they help operators locate parts with precision.
- Enhanced Inventory Control: Integration with the ERP system and real-time access to spare parts data improves inventory accuracy and order fulfillment speed.
- Better Customer Service: Faster access to spare parts and more organized inventory. These advantages have helped MotoMart provide timely and efficient service to their customers, an essential factor in the agricultural sector.

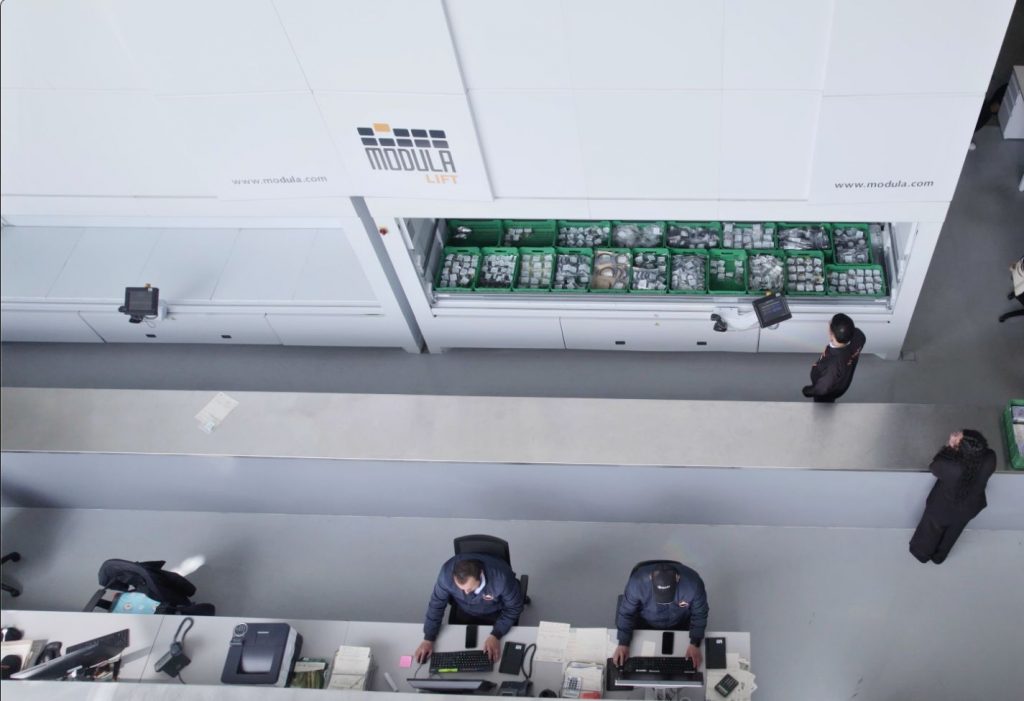
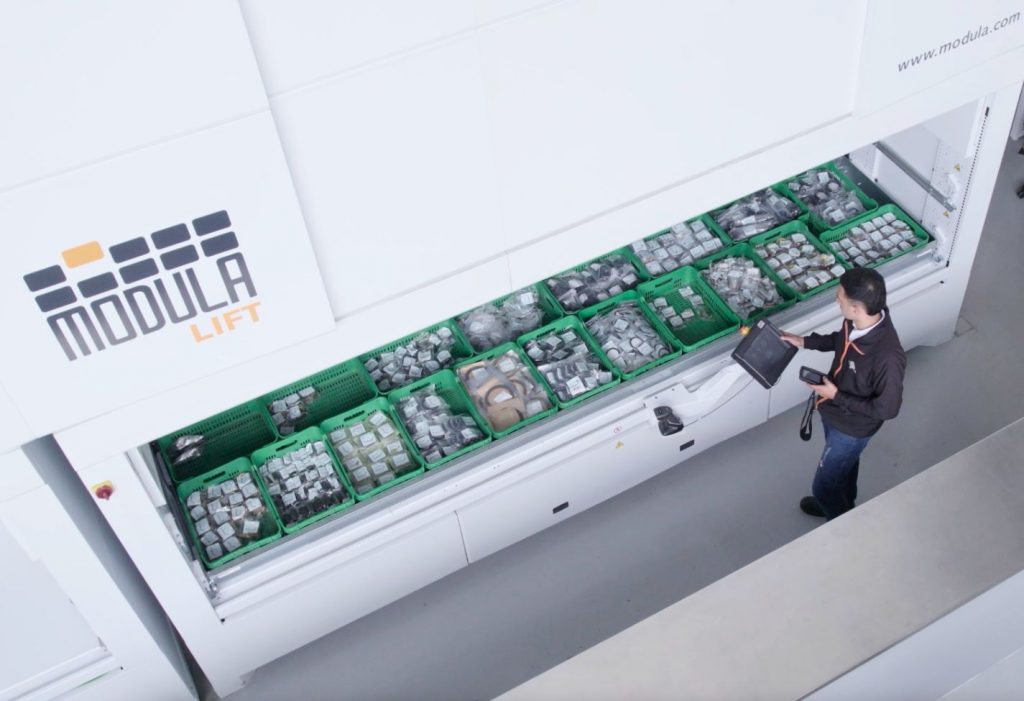
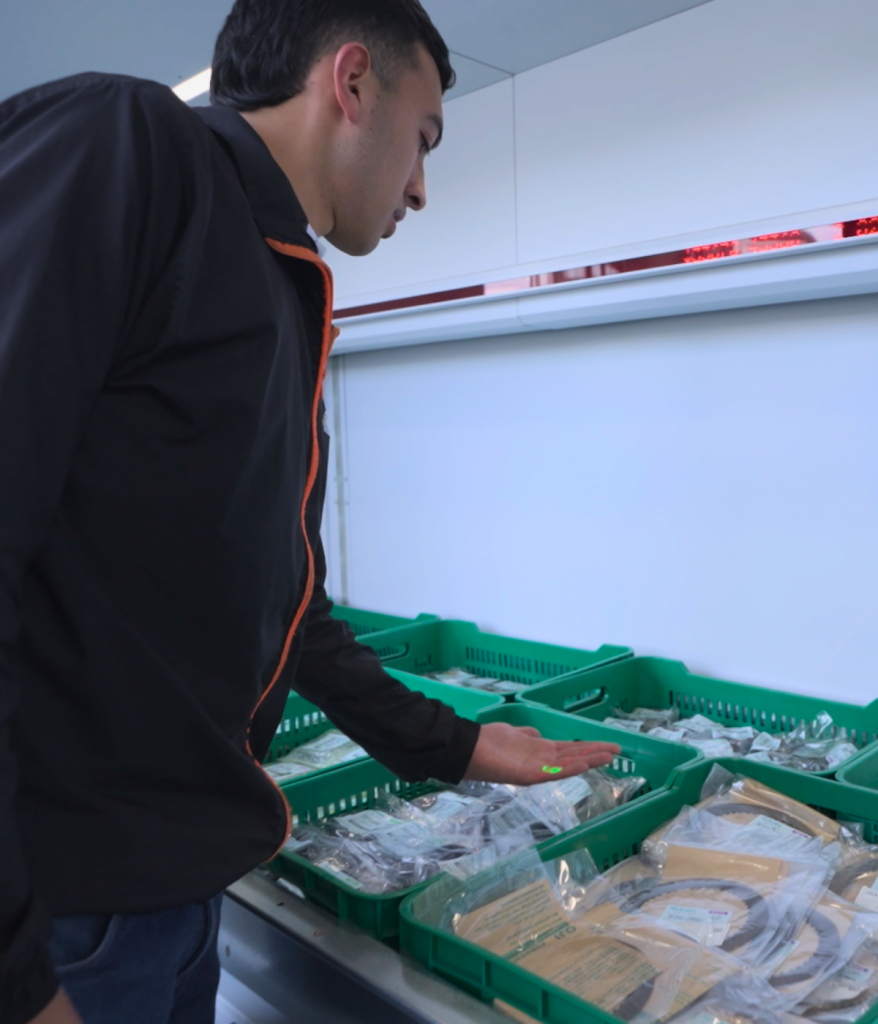
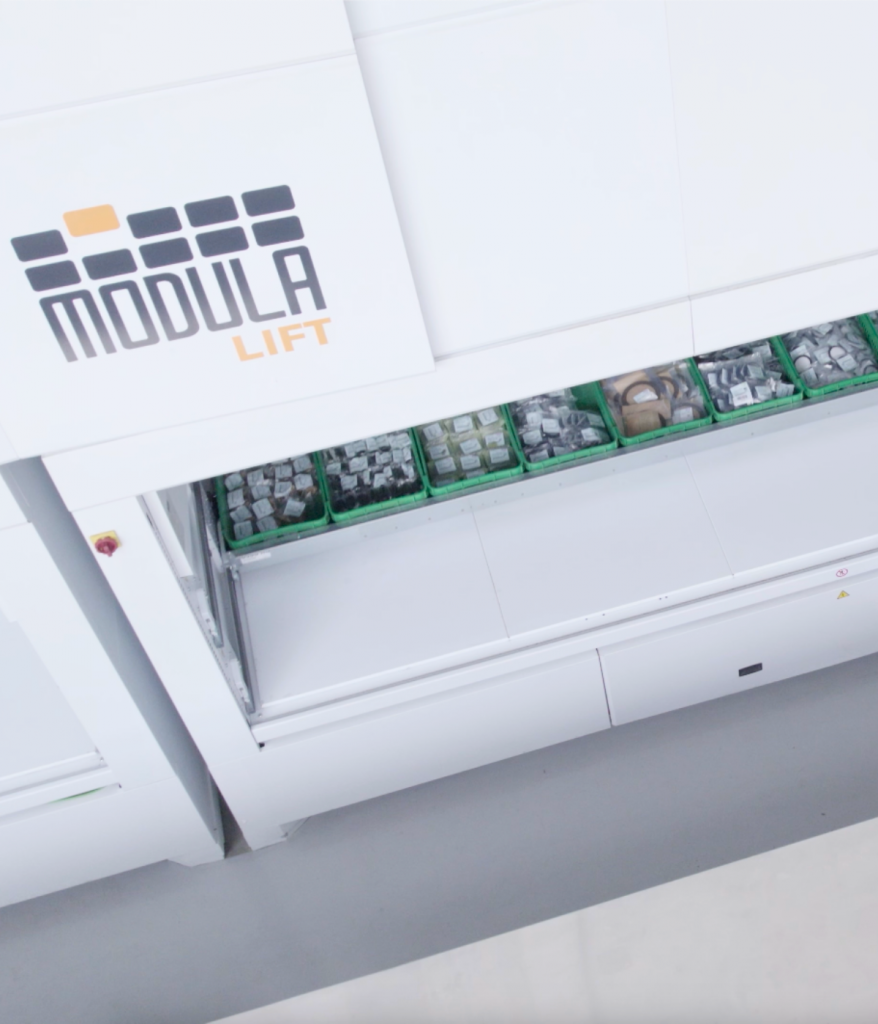