Choosing the Right Solution: Vertical Lift Modules vs. Horizontal Carousels
Vertical lift Modules vs Horizontal Carousels. Both are based on the part to picker principle and offer similar benefits. But which is the right automated storage system for your operations?
As all industries cope with the impact of the coronavirus (COVID-19) pandemic, many warehousing and distribution operations are reshaping themselves to meet unprecedented demands. More companies are now looking to automated storage and retrieval systems (AS/RS) to automate processes once performed manually to stay just as productive even if some employees are unable to work.
But which one is the right fit for your operations?
The first step to identify the most suitable automated storage systems for your business is to analyze your current operations and determine which areas can benefit from the integration.
What heights are available for storage in your facility? Are you running out of space? Do you need to increase your throughput? Do you need a better inventory control? Are you having trouble keeping pace with growing demand or seasonal picks? What type of parts do you handle? What are your current picking rates?
Let’s take a look at the 2 types of automatic storage systems that are often compared: Vertical Lift Modules vs Horizontal Carousels
Both technologies are based on the part to picker principle and offer similar benefits: space optimization, high productivity, efficiency, safety, quality control and inventory management. But which is best? That depends on:
- Space available & ceiling height
- Size and weight of parts handled
- Business cycle and fulfillment requirements.
Vertical lift modules (VLM)
A Vertical Lift Module (VLM) is an enclosed system of vertically arranged trays, at its front and back. A centered inserter/extractor automatically locates and retrieves the stored trays and delivers them to the operator at an ergonomically positioned pick window, with a simple touch on the user-friendly copilot controller. This feature eliminates the need to search for items and ensures that the right part is delivered to the right person.
By utilizing the available room height from floor to ceiling, this automated storage and retrieval system maximizes any area’s storage potential, making it possible to recover up to 90% of space compared to standard shelving. Moreover, a height detection system measures the height of the products in the tray as the tray is put away and stored where it requires the least amount of space for maximum storage density.
Trays can be organized for items of every type and size. By using partitions and dividers, it is possible to create the exact number of storage locations required in each tray and configuration settings can be adjusted at any time to accommodate changes in the size or quantity of the stored items.
The vertical storage solutions can also dramatically increase the productivity and picking accuracy as they are equipped with simple visual picking aids that guide operators to quickly and easily identify the items needed to be picked or replenished.
Vertical lifts are most efficient when:
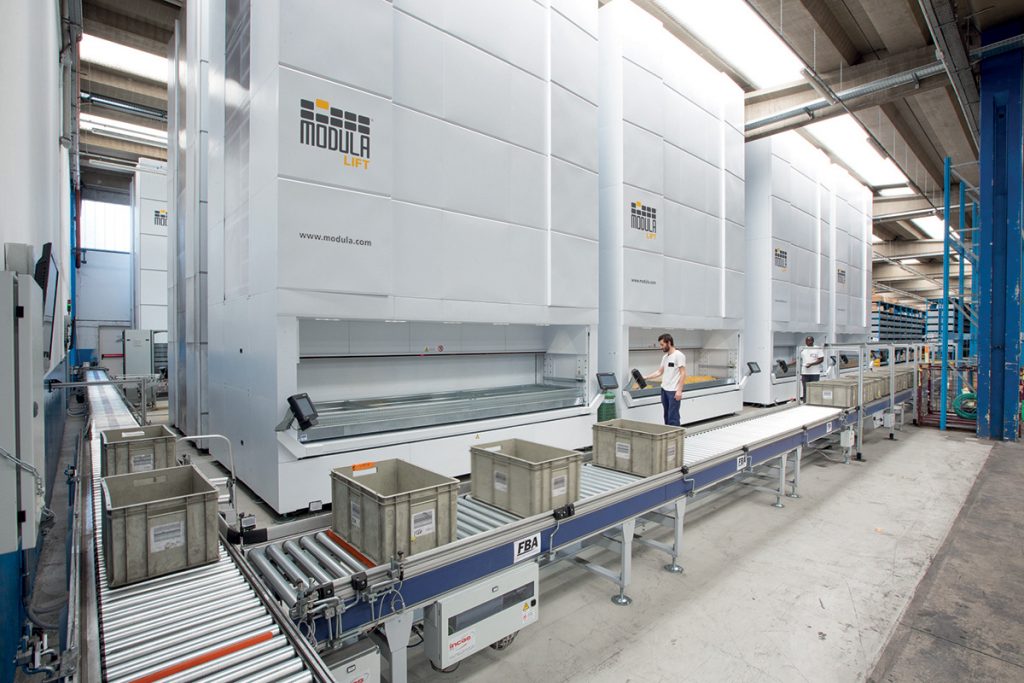
- Ceiling heights are over 12’ as the often-wasted air space can be used for parts or product storage
- The product mix constantly fluctuates in numbers, sizes and weights
- The size of the parts stored varies from very large to very small, heavy to light
- The weight and the size of the products present ergonomic and space claim challenges and integrated lifting assistance is needed
Horizontal Carousels
The horizontal carousel consists of carriers (bins) mounted on an oval track that rotates horizontally and delivers stored goods to the picker.
Following the parts-to-pickers principle, when the operator requests a particular item, the horizontal carousel warehouse automatically rotates so that the appropriate bin is accessible, and the item can be picked. There’s no walking back and forth to find and retrieve goods. Thanks to the visual picking aids, the user can quickly identify which item should be picked and the quantity requested.
To speed picking times, horizontal carousels are often used in pods. As the worker picks from one horizontal carousel in the pod, the other is pre-positioning the next pick. This minimizes worker downtime and increases throughput.
To achieve even higher picking rates, the horizontal carousel can be used in combination with batch picking. Using warehouse management software, an operator can create a batch of orders and fill them all at one time. When the horizontal carousel presents an SKU for picking, the operator picks the total SKU quantity for all orders. The Batch Picking Lights, located at each order position, will then direct the picker to the correct location and indicate the quantity that needs to be placed in each order.
This increases accuracy, reduces picking errors and retrieval time, all while increasing productivity. With this configuration, picking rates can go up to 550 lines per operator each hour.
Horizontal carousels are the ideal solution when:
- Ceiling heights are less than 10’ and floor space is not a main concern
- Budget may be a concern – Horizontal carousels warehouse tends to be more economical
- Applications require high throughput. Arranged in a pod of 2 to 4 units, horizontal carousels have a pick rate up to 550 lines per hour.
- The product mix doesn`t change often and parts are medium or slow movers
- Applications which always need to have emergency access to the inventory
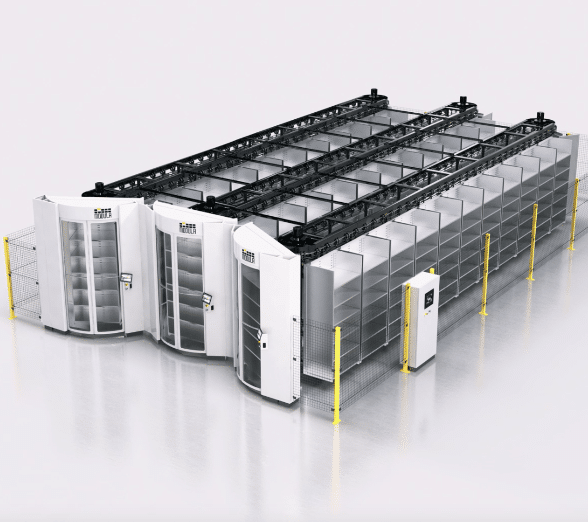
In conclusion
If you are considering an automated storage and retrieval system, it is important to evaluate first which system is right for your handling and picking needs. Sometime the solution involves more than one of these automated storage solutions working together.
With the right system analysis and design, the implementation of a horizontal carousel warehouse or a vertical lift module into your operation is an investment that takes as little as 6 months for an effective ROI. This is due to the Improved Floor Space Utilization, Reduced Labor Costs, Increased Picking Accuracy, and better Inventory Control.
As the future increasingly speeds towards automation and advancing technology, companies will soon not be able to afford a warehouse that cannot keep up with consumer expectations. Investing in an automated warehouse today means your company will be one step ahead going forward, and you will be able to continue operations where traditional labor physically cannot.