Horizontal Carousel Storage Systems: Answers to the Most Common Questions
Horizontal Carousel Storage Systems: Answers to the Most Common Questions
The Modula HC New Generation is the most up-to-date and reliable horizontal carousel available on the market today. While horizontal carousels have been around for many years, deciding whether to buy one, a vertical lift module or another automated storage system can require a careful analysis. Both technologies offer similar efficiency gains: better storage density, higher productivity, fewer picking errors and a far better inventory control compared to shelving and racks.
There’s a lot to know about the topic, so we’ve divided these FAQs into two parts.
In the first part, we’ll compare horizontal carousels with vertical lift modules. In the second part, we’ll take a look at how the Modula HC can be employed to address varying applications where an automated storage and retrieval solution may be useful.
While we provide an extensive amount of detail in these two parts, we advise talking to a Modula sales representative to get a more definitive answer for your specific application.
Modula HC configurations and special storage applications
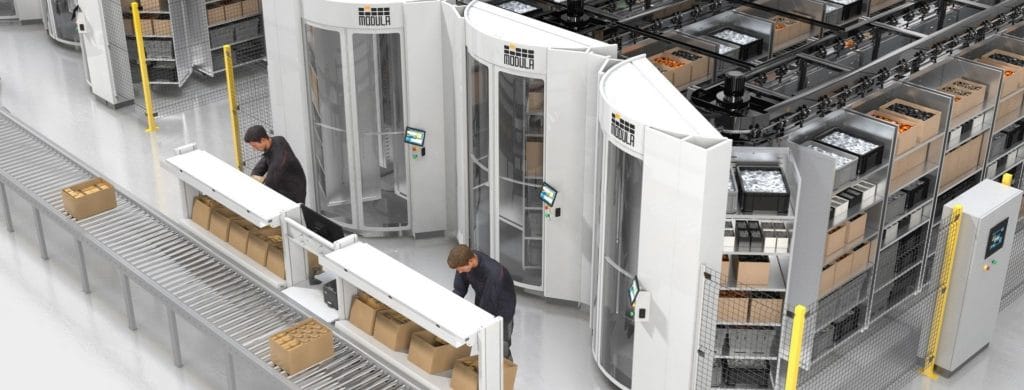
For which applications is the horizontal carousel a better choice than a vertical lift module?
The biggest factor is the ceiling height in your facility. Choose a horizontal carousel if your ceiling is below 10 feet. For higher ceilings, a vertical lift module is a better choice. But there are other key factors to keep into consideration such as the size and weight of the parts being handled as well as the business cycle and fulfillment requirements.
How does a horizontal carousel compare to a VLM in pick speeds?
Pick speeds vary highly, depending on the distribution of material within the storage system, the line item per order density, and any self-imposed process times, like bagging, tagging, or weigh counting items. Both systems can pick 130-550 items picks per hour if configured to do so. Again, ceiling height should be the main consideration, together with other logistical and operational aspects.
Does a horizontal carousel have imbalance issues similar to those on a vertical carousel?
No. Each bin/carrier is independently supported on the Modula Horizontal Carousel and the operation is not affected whether a bin is at its maximum weight or empty. It is recommended to avoid loading the unit to its 1,200 pound (544 kg) maximum capacity regularly because this will cause premature wear.
Which technology is best in terms of storage density – a vertical storage solution or a horizontal carousel?
Horizontal carousels do not utilize the vertical cube as well as vertical storage solutions, therefore they require more floor space to operate. Vertical lift modules utilize the vertical air space so their footprint is relatively small. Both offer much better storage density compared to traditional racks or shelves.
Is it true that horizontal carousels are great for picking, but they require a great deal of time to replenish?
Not if the operator slots products and sizes properly, which would result in only replenishing 5-10% of the operation’s SKUs daily and require an hour to complete.
What is the ROI on a horizontal carousel or VLM?
Implementing a horizontal carousel warehouse or a vertical lift module into your operation is an investment that can create an effective ROI in as little as six months. This is due to the improved floor space utilization, reduced labor costs, increased picking accuracy, and better inventory control.
Which type of products/parts cannot be stored in a horizontal carousel?
Single items that would be strenuous to move by a single operator, weighing around 25kg (55 lbs), are better stored in a system that allows work aids to be involved such as a vertical lift module. The Modula HC is designed for human retrieval, not machines.
VLMs are also a better fit for special products that require a secure and clean environment. In an HC, products are stored in open bins/shelves subject to airborne contaminants. By contrast, a vertical lift module is fully enclosed with an automatic door. This prevents goods from being damaged and minimizes exposure to the warehouse environment.
Is there an ideal item size for storage?
A horizontal carousel is best used when picking slow- to medium-moving split case items as well as slow-moving small boxes and with high retrieval rates in which the product mix doesn’t change much. This is because the shelves in a horizontal carousel bin are vertically adjustable on 2” centers. The location is set during the installation. If the product height changes, you would need to readjust the location within the bin.
Is it possible to store liquids?
It depends on local jurisdiction. Typically, if you can ship it over the road without requiring the use of special accommodations you can store it in a horizontal carousel.
Can horizontal carousels be used in cold room applications?
The answer depends on certification requirements, but the minimum permissible temperature inside a building with an operator is 41° F (5° C). Ask your representative about installations in colder environments.
How many horizontal machines can be used for one operator?
In times of low throughput, a single operator can operate multiple pods. However, traditionally a single operator would operate a pod of carousels. A pod would be sized to meet the storage capacity and the throughput requirements of the business. Carousel pods of two, three, and four carousels can be handled by a single operator.
How does the picking process work with horizontal carousels in pods?
To speed picking times, horizontal carousels are often used in an integrated workstation called a “pod.” Software and pick-to-light technology allows the carousels to work in conjunction with each other. As the worker picks from one horizontal carousel in the pod, the other carousel is pre-positioning the next pick. This minimizes worker downtime and increases throughput. Moreover, horizontal carousels arranged in pods offer great flexibility. With a simple software adjustment, the pods can be easily reconfigured to meet seasonal peak order times. A pod of four horizontal carousels can operate as one pod with one operator.
Does a horizontal carousel have imbalance issues similar to those on a vertical carousel?
No. Each bin/carrier is independently supported on the Modula Horizontal Carousel and the operation is not affected whether a bin is at its maximum weight or empty. It is recommended to avoid loading the unit to its 1,200 pound (544 kg) maximum capacity regularly because this will cause premature wear.
Can you stack the Modula HC?
No. Stacked carousels pose safety risks due to picking from ladders and platforms, so the Modula Horizontal Carousel is designed to be operated safely from the ground by human operators. If ceilings are high, a VLM may be a better choice.
How do I get to the product if the carousel is down?
One of the main benefits of a horizontal carousel is that it is still accessible when the power fails. Thanks to the new technology and improvements to the product, this is rarely an issue. HCs are traditionally a reliable storage solution that rarely encounter total system shutdown.
Is it possible to modify the size of the Modula Horizontal Carousel (increase or decrease) once it is installed?
Yes. Just as a Modula VLM can be adjusted for height after installation, a Modula HC can be adjusted for length and pods can be easily reconfigured to meet seasonal peak. Moreover, the control panel’s position and the safety fence can be customized anytime to meet different site requirements.
How does it work the batch picking with horizontal carousels?
One of the most common applications with horizontal carousels is batch picking. To speed picking times, horizontal carousels are often used in pods. A pod is two or more horizontal carousels used in an integrated workstation with software and pick to light technology.
Using Modula WMS software, an operator can create a batch of orders and fill them all at one time. When the horizontal carousel presents an SKU for picking, the operator picks the total SKU quantity for all orders. The batch picking lights, located at each order position, will then direct the picker to the correct location and indicate the quantity that needs to be placed in each order.
By using batch picking, the operator only visits an SKU location one time during picking. This increases accuracy, reduces picking errors and retrieval time while increasing productivity by up to 65%. The put-away process can be automated much like the picking process in reverse. Multiple displays can be integrated in each order position to facilitate multiple picking operators (up to three). This can help meet higher throughput rates during peak times.
Moreover, the WMS software provides the operator a graphical representation of the orders in the active batch, as well as information on the item that is being picked and the orders the item is associated with.
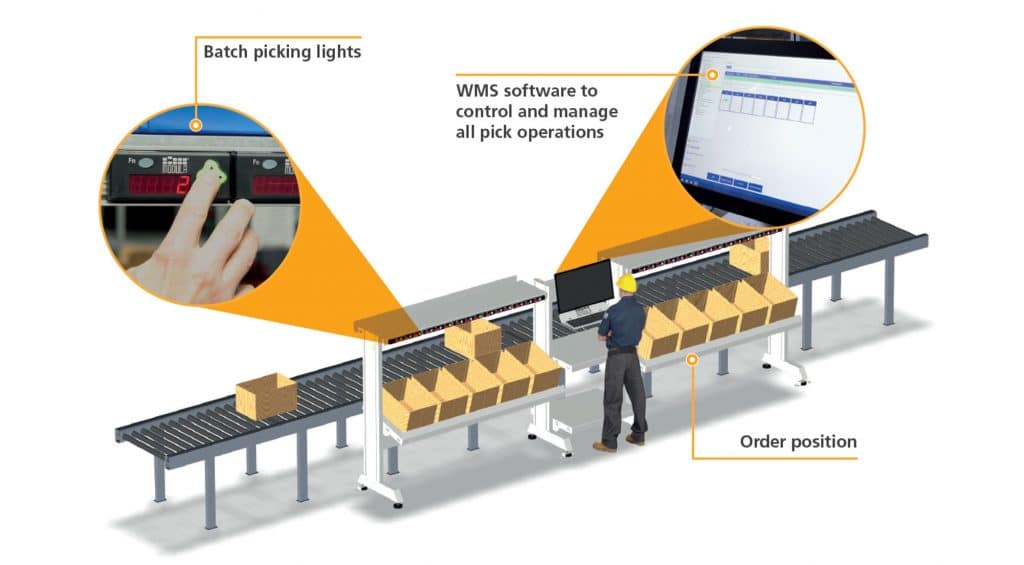
Why is a top drive carousel the best design?
Maintenance is easier with the motors on top rather than inside the carousel because accessing the middle of the carousel can be difficult or impossible in the event of a failure. Modula has incorporated both a top drive as well as gear-motor design into its new model, As a result, there are no chains or belts to adjust, lubricate or replace. If ceiling height is limited, we also offer the option of inverted drives.
Why do you use doors instead of safety floor mats?
The benefits of doors are many: Compared to oversized safety floor mats, the additional cost of the door system is marginal. The level of safety protection afforded by doors is far superior to mats. Judging by cost alone, one injury to a worker would instantly undo any savings a floor mat would offer. Moreover, the curved design of the doors provides optimal use of the space and more efficient pod-picking configurations. The door panels are made of Lexan, a highly impact-resistant material that offers clear visibility of the products and carousel activities while keeping the operator safely away from the moving components until the bin has come to a complete stop.
Can these horizontal carousel warehouses be used in areas with high seismic activity?
Local jurisdictions will specify the modifications required to meet their local regulations. Each case requires review. Modula works with local seismic engineers to determine the best solution when a customer is considering any Modula automated storage solution to be operated in a region subject to seismic activity.
Does the Modula HC require any specific software or does it run with the same WMS as other Modula solutions?
The Modula Horizontal Carousel will work seamlessly with the Modula WMS, allowing it to be connected with any other Modula products within the same application. Thanks to the WMS, it is also easy to integrate additional options. For example, the WMS can be connected to security devices such as badge readers to control access to the inventory, as well as productivity aids, including batch pick stations, label printers, barcode readers and piece counting scales.
What is the maintenance cycle of an horizontal carousel storage system?
Most machine maintenance can be done through regular operator inspections, and annual inspections. Stocking key spare parts can also reduce down time. Additionally, the majority of the components are accessible from outside the horizontal carousel, simplifying repairs and speeding maintenance. This also minimizes downtime and repair costs.
How long does the installation take?
This varies based on the operation and the installation requirements but normally takes a minimum of five working days. Requirements include a forklift and a clear area for assembling the carousel. The subcomponents of a carousel are assembled at the factory and the unit frames – modular in design – are assembled at the installation site.
If you have any other questions or would like to learn more about this technology, contact our Modula HC team of specialists.