Grocery E-Commerce & Supply Chain – Do More with Less
As more than 70% of U.S. households reported buying groceries online in 2021, food retailers are increasingly focusing on their Grocery E-Commerce & Supply Chain. The main goal is to streamline their warehouses, distribution centers, and micro-fulfillment centers. If time is money in meeting shoppers’ demands for home delivery and curbside/in-store pick up, it’s also crucial for retailers to have systems in place that allow for rapid, accurate order picking in a way that maximizes space and minimizes labor. To sort out challenges and opportunities in storage solutions and material handling, David Lind, Business Development Director for Modula recently spoke with Progressive Grocer, a publication that has been the voice of the food retail industry since 1922.
PG: What are some top things on grocers’ e-commerce priority lists when it comes to storage and handling?
David Lind: Whether they are revamping existing facilities or starting from the ground up on a new warehouse, DC or micro-fulfillment center, grocers want to optimize everything — floor space, time, productivity, energy usage, product integrity and availability. On top of that, they are seeking solutions that assure worker safety and less stressful working conditions.
PG: How does an infrastructure with vertical lift modules (VLMs) and/or horizontal carousels help food retailers with their grocery supply chain?
DL: VLMs are fully automated storage and picking systems that take up a minimum footprint by utilizing the available height of the facility. Items can be stored up to 53 feet high in a safe and secure unit that automatically delivers them to an operator. Horizontal carousels are ideal for low-ceiling environments, as well as those seeking maximum throughput. Thanks to the easy integration of the WMS software with any existing ERP or DMS systems, a retailer can automate the picking and storage process. Workers don’t need to search for products on shelves or lengthy racking systems, they just press a button activating the WMS and let the VLM bring the products to them. This feature ensures that the right part is delivered to the right person. As such, productivity and efficiency are increased while picking errors are drastically reduced.
It’s also fast: Modula’s Lift VLM, for example, has a picking speed of 300 lines per hour. The faster products get to the bay, the quicker they get to the store or the shopper’s home. Grocers can also get peace of mind knowing that inventory stored in these enclosed modules stays secure and clean, and is kept at the proper temperature.
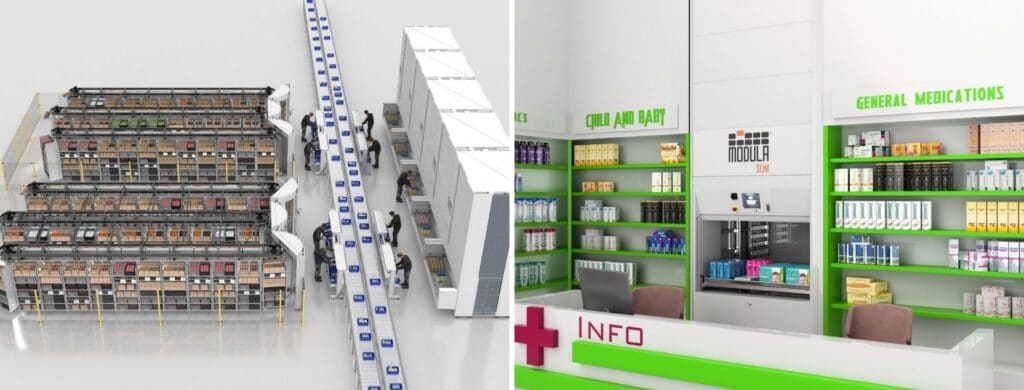
PG: How do these systems also help the flow within a facility and improve their supply chain?
DL: Offering a good experience to customers, while ensuring profitability is a big challenge. In the e-grocery supply chain, you need to keep into consideration many key factors. From the high expenses of grocery e-commerce fulfillment to the need to ensure that the inventory matches demand across all your channels, to the current high costs of transportation and labor.
As grocers scale up or adjust their warehouses and DCs in light of the evolving e-commerce channel, they are looking to design spaces that can help them do more with less and optimize their processes. Because VLMs can store inventory essentially up to the ceiling for robotic picking, the high-density automated storage and retrieval towers require up to 90% less room than traditional picking systems, opening up floor space and reducing needed footprints. In addition, because items are picked when needed, there’s no accumulation of extra products that would otherwise take up space and cause hazards, delays, or waste.
PG: What are some benefits when it comes to labor?
DL: In addition to optimizing labor through automation — a major consideration at a time of ongoing labor challenges — this system helps enhance workplace safety. Workers don’t have as great a risk of injury when removing inventory from storage, and because trays come out at hip height, employees don’t have to strain or move or reach them.
PG: What other advice do you have for retailers to take storage and handling to the next level at a time of increased competition?
DL: Evaluate not just your current needs but your potential future needs for order fulfillment. Are you mainly using central distribution warehouses, or would you benefit from adding fully functioning micro-fulfillment centers? Do you need a buffering solution for completed orders? What are your temperature requirements? Consider automated solutions to reduce errors across your fulfillment areas and make the best use of labor and space. You can start small, even with just one module and one robot, and expand your system as you grow.
Modula can help you transition in an immediate or gradual way with our series of VLMs or horizontal carousels that can be installed based on your needs. You can also streamline your order fulfillment with other best practices, such as storing popular items near each other, regularly replenishing fast-moving inventory and leveraging technologies like barcode scanners and camera-based imaging for better verification.
Whether they are revamping existing facilities or starting from the ground up on a new warehouse, DC or micro-fulfillment center, grocers want to optimize everything — floor space, time, productivity, energy usage, product integrity and availability.
David Lind – Business Development Director at Modula