Expert Guide To Automated Warehouse Picking + Top Solutions
With the exponential growth of eCommerce and the increasing demand for quick order fulfillment, traditional manual picking methods are no longer sufficient. This has led to the rise of automation in the logistics industry — particularly in the form of automated warehouse picking.
In this article, we’ll share all you need to know about automated warehouse picking, including types of picking systems and benefits of each, and introduce you to the leading automated warehouse picking systems at Modula.
What is Automated Warehouse Picking?
Automated warehouse picking is the process of leveraging advanced technologies, including robotics, pick-to-light systems, put-to-light systems, and voice picking, to efficiently select and retrieve items within a warehouse environment.
Through the integration of these technologies, businesses can enhance their picking accuracy and efficiency, leading to improved overall warehouse performance.

Types of Automated Picking Systems
The various types of automated order-picking systems can be grouped based on their level of automation, including:
1. Assisted Picking Systems for Assisted Automation
Assisted picking systems, such as pick-to-light systems and voice-picking systems, provide warehouse operators with picking instructions to reduce mispicks and improve throughput.
2. Goods-to-Person (GTP) Picking Systems for Partial Automation
Goods-to-person picking systems deliver the picked items directly to the warehouse worker, rather than the worker navigating through the warehouse aisles to find and pick items
Goods-to-person picking systems include conveyor belts, stacker cranes, and AMRs. This type of automated picking system is particularly effective in large warehouses that process large volumes of orders.
3. Automated Picking Systems for Full Automation
Fully automated picking systems utilize technology to perform the picking process from start to finish, eliminating the need for human intervention.
Automated picking systems include:
- Picker robots: Robots can identify and pick items from shelves or bins. They can work in environments of different temperatures and light levels and can operate around the clock, increasing productivity.
- Automated Storage and Retrieval Systems (ASRS): These systems are used in large warehouses where high volumes of goods are stored. They automatically place and retrieve items from specified locations in the warehouse. They can work in conjunction with conveyor systems to move goods around the warehouse.
- Layer-picking machines: These machines, also known as full-case or full-pallet picking machines, are used to pick full layers or cases of products. They are commonly used in distribution centers dealing with high volumes of identical products.
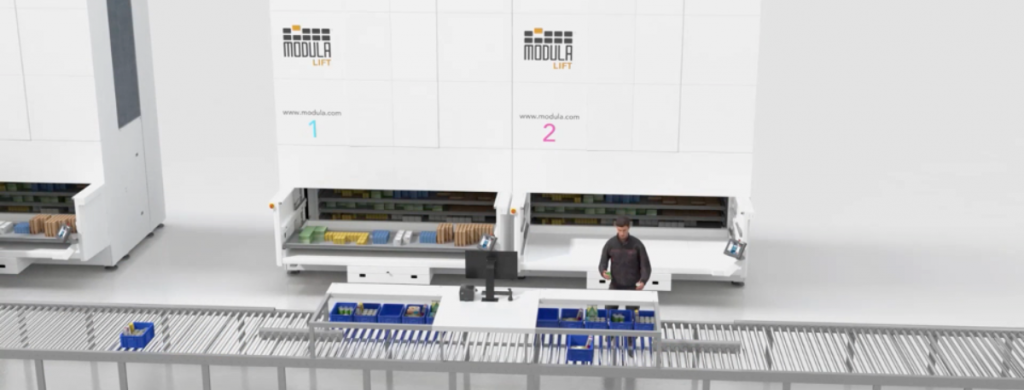
How Does Automated Warehouse Picking Work?
Automated warehouse picking systems optimize the process of picking items in a warehouse by using advanced technology to locate and pick inventory.
Here’s a general overview of how these systems work:
- Warehouse management system integration: The picking process begins when an order is placed and enters the warehouse management system (WMS). The WMS is integrated with the automated picking system and sends the order details, such as SKU and product quantity, to the picking system.
- Order processing: The automated system processes the order details and determines the most efficient way to pick the items. This includes optimizing the route the robots should take to reduce travel time and sequencing picks to minimize empty travel.
- Picking: Robots, automated guided vehicles (AGVs) or autonomous mobile robots (AMRs) are sent to retrieve the goods. These automated warehouse picking systems can range from simple automated carts that follow pre-defined routes to more sophisticated robots equipped with sensors and software that allow them to navigate the warehouse independently.
- In a goods-to-person system, the robots bring the entire shelf or bin to a stationary human picker, who then picks the required item.
- In a person-to-goods system, the robots lead human pickers from item to item along an optimized route.
- In a fully automated system, robots or robotic arms also perform the picking.
- Sorting and packing: Once the items have been picked, they are transported to a sorting area. A warehouse can use conveyor belts and sortation systems to organize the items for packing, as well as robots or cobots (collaborative robots) to assist human packers. The system’s software keeps track of every item, ensuring that the correct items go into their designated packages.
- Data synchronization and shipping: The automated picking systems communicate with the central WMS or ERP system to update the inventory levels, confirm successful picks and provide real-time visibility of the warehouse operations. Once an order is packed, it’s dispatched for shipping.
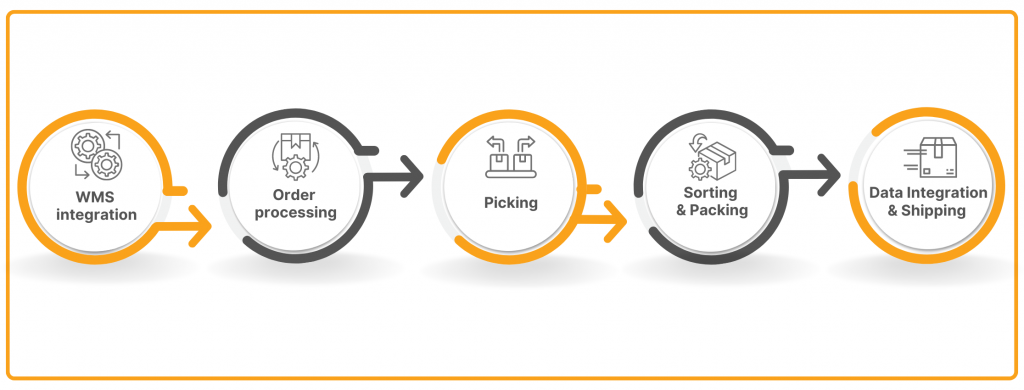
Benefits of Automated Warehouse Picking
Automated warehouse picking offers numerous advantages, from preventing costly product returns to boosting picking throughput.
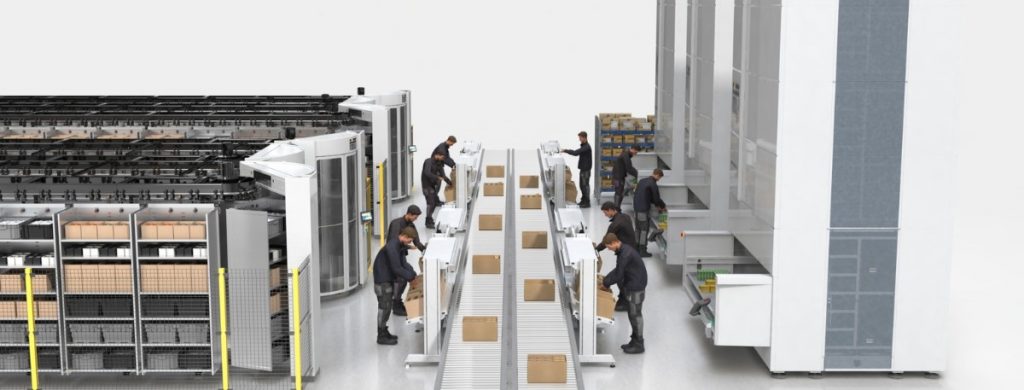
Automated Warehouse Picking Systems at Modula
As a leading provider of automated warehouse solutions, including automated warehouse picking systems, Modula reimagines warehouses across industries to improve picking speed and accuracy.
Modula’s automated picking systems are designed to optimize the picking process, reducing time and labor while maximizing accuracy and throughput. These systems combine advanced picking aids, easy-to-use technology, and intelligent software to create a seamless and efficient workflow.
Our order-picking solutions include:
Modula Put to Light System
The Put to Light System (which operates in batch or multi-order modes) boosts your throughput by enabling the simultaneous picking of multiple orders.
This system replaces traditional paper-based methods, such as traditional pick tickets and shipping lists, reducing errors, improving inventory accuracy and enhancing productivity.
The Modula Put to Light system can function independently or can be paired with a Modula Picking Station or Picking Cart to further optimize the picking, putting and sorting processes.
Here’s how the Put to Light System works:
The Put to Light system uses lights and digital displays to guide your warehouse operators through the order fulfillment process.
It directs operators to the right area on a station or cart to “put” items using light signals. Each spot corresponds to a specific order and features a light display showing where and how many items should be placed.
After placing an item in its designated area, the operator presses a confirmation button to complete the task. This sequence continues until all orders are fulfilled.
Modula Picking Station
The Modula Picking Station is designed to efficiently manage batch or multiple order processes, maintaining a smooth workflow. It can be used individually or in multiples at predetermined positions.
The Picking Station offers a versatile and accurate solution to complete more orders in less time. With its paperless picking system, it eliminates the need for order lists, speeding up the picking process.
Suitable for all warehouse operations, the Picking Station can easily integrate with both manual and automated handling systems, such as belt conveyors.
Here’s how the Picking Station works:
The Picking Station is a workstation that can be modified thanks to adjustable shelves that hold bins or totes to store goods.
Each bin or order is linked with a put-to-light display that has its own control unit and power supply.
For a larger operating area, multiple picking stations can be combined, with operators on one or both sides. The station can also be paired with additional modules to install monitors, label printers, or barcode readers.
Modula Picking Cart
The Modula Picking Cart is the ideal solution for paperless batch or multiple order processes that require mobility.
The Cart features a put-to-light display to guide operators and a wireless connection to the WMS for optimal batch processing and route planning.
Moreover, it seamlessly integrates with both manual and automated handling systems, making it suitable for any warehouse operation.
Here’s how the Picking Cart works:
The Picking Cart comes with shelves, put-to-light displays, backup batteries and WiFi for wireless connections.
The Put To Light System guides warehouse operators during the picking process, while the WMS calculates the best routes, boosting efficiency and productivity.
Modula Picking App
Mobility is key in a warehouse, as your operators spend most of their day navigating their way through warehouse aisles.
The Picking App is a user-friendly tool that helps your operators move around the warehouse while maintaining real-time updates and control of all processes.
Say goodbye to paper and bulky printouts. You can access real-time updates and information directly on your smartphone or tablet, making the picking operations seamless and organized.
Here’s how the Picking App works:
The Modula Picking App, available for Android devices, features a user-friendly interface, enabling operators to handle all picking and replenishment operations with ease.
Integrating seamlessly with the Modula WMS, the app offers immediate access to real-time information, no matter where the operator is.
The app includes a built-in barcode reader, allowing inventory to be scanned and monitored directly from the mobile device, eliminating the need for paper.
Final Notes on Automated Warehouse Picking Systems
Automated warehouse picking systems offer numerous benefits including reduced product returns and a faster order fulfillment process.
By combining these picking stations with Modula’s Automated Storage & Retrieval Systems (AS/RS), such as Modula Lift or Modula Horizontal Carousel, businesses can experience significant improvements in order accuracy, efficiency and reliability.
These technologies seamlessly integrate through Modula WMS, providing an end-to-end solution for optimized warehouse operations.
One standout feature of automated warehouse picking systems is their capacity to boost productivity.
As these systems can operate continuously without breaks, they increase the volume of orders that can be processed. As a result, warehouse operators have time for tasks that require human intervention, such as quality checks.
Additionally, these systems contribute to improved warehouse safety by reducing the risk of workplace injuries associated with lifting heavy inventory.
At Modula, our automated picking systems are easy to set up with an intuitive learning curve. You can boost your batch and multi-order picking processes in no time. Explore our automated solutions and get in touch with our team to find out how we can help you transform your warehouse.