Vega Americas Enhances Efficiency and Space Utilization with Modula VLMs
Case Study Summary
The Challenge
Vega Americas faced significant challenges with their existing storage systems, which required employees to traverse large distances to locate parts. This inefficiency not only affected productivity but also led to errors in part retrieval. Additionally, with a need to maximize storage capacity within their existing footprint, the company required a solution that would consolidate their inventory and improve overall operational efficiency.
The Solution
To address these challenges, Vega America implemented Modula VLMs, initially purchasing three units in 2023 and adding two more in 2024. The VLMs were deployed in areas such as waveguide and repair, significantly optimizing storage and retrieval processes. All units are equipped with alphanumeric LED bars, laser pointers, and Copilot Operator-Sliding Consoles. Additionally, the VLMs utilize the WMS Premium package.
The integration of these systems has enabled Vega Americas to store up to 3,040 ft³ (86 m³) of inventory within a compact footprint of 664 sq. ft. Vega Americas’ investment in Modula VLMs has proven highly effective in enhancing storage capabilities, improving operational efficiency, and supporting the company’s continued growth.
Key Features of the Vega Americas Case Study:
- Space Efficiency: The VLMs allowed the company to store a substantial volume of inventory within a minimized footprint, effectively optimizing the use of their existing space.
- Improved Productivity: The compact footprint of the Modula VLMs allowed Vega to store approximately $2.5 million worth of inventory within just 308 sq.ft2, maximizing storage capacity and minimizing floor space usage.
- Space Optimization: By consolidating inventory into one central location, employees significantly reduced the time spent searching for parts, which enhanced overall productivity.
- Increased Accuracy: The VLMs’ features, such as the alphanumeric LED bar and laser pointer, have reduced retrieval errors, ensuring higher accuracy in order fulfillment.
- Enhanced Operational Flexibility: The VLMs support various functions, including storing components, finished goods, and repair products, making them versatile tools in Vega Americas’ operations.
Technical Information:
- 2 ML50D Units: Each with 66 trays, a height of 23.29’ (7,100 mm), and a tray load capacity of 1,102 lbs (500 kg).
- 1 ML50D Unit: With 36 trays, a height of 27.89’ (8,500 mm), and a tray load capacity of 1,102 lbs (500 kg).
- 1 ML50 Unit: Featuring 47 trays, a height of 23.29’ (7,100 mm), and a tray load capacity of 1,102 lbs (500 kg).
- 1 MA50D Unit: With 35 trays, a height of 27.89’ (8,500 mm), and a tray load capacity of 1,102 lbs (500 kg).
“The Modula VLMs have significantly improved our operations. Storing inventory in a compact footprint has been a game-changer for us.” – Bill Shereve, Manufacturing Process Manager
“Initially, we were focused on solving space problems, but the real benefit of the VLMs is how they reduce the need for employees to walk around looking for parts. They stay in one spot, and the parts come to them.” – Ron Foltz, Vice President of Manufacturing
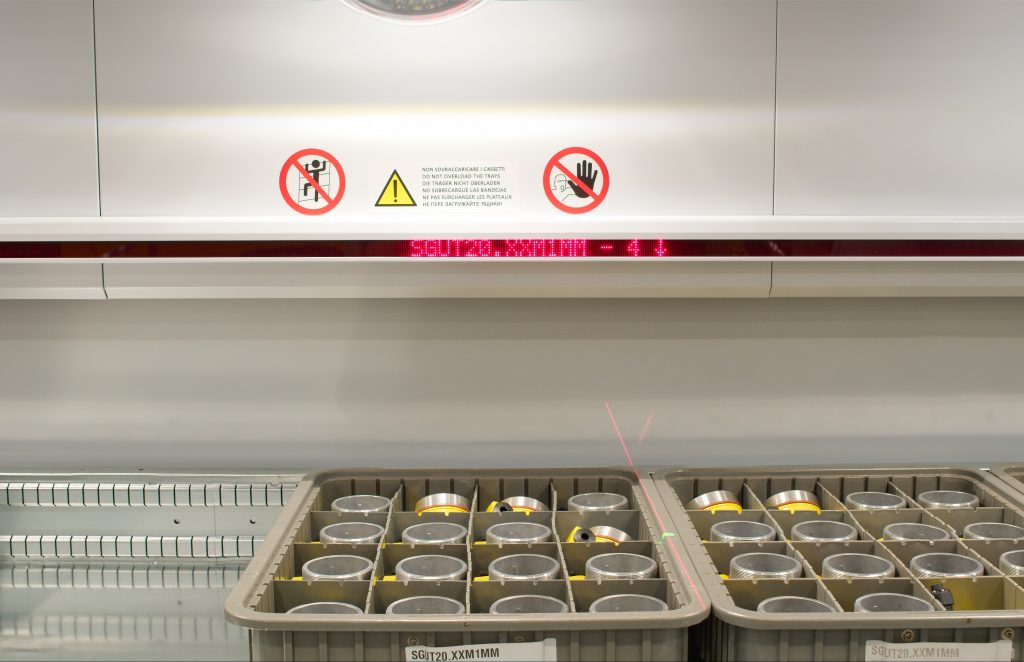
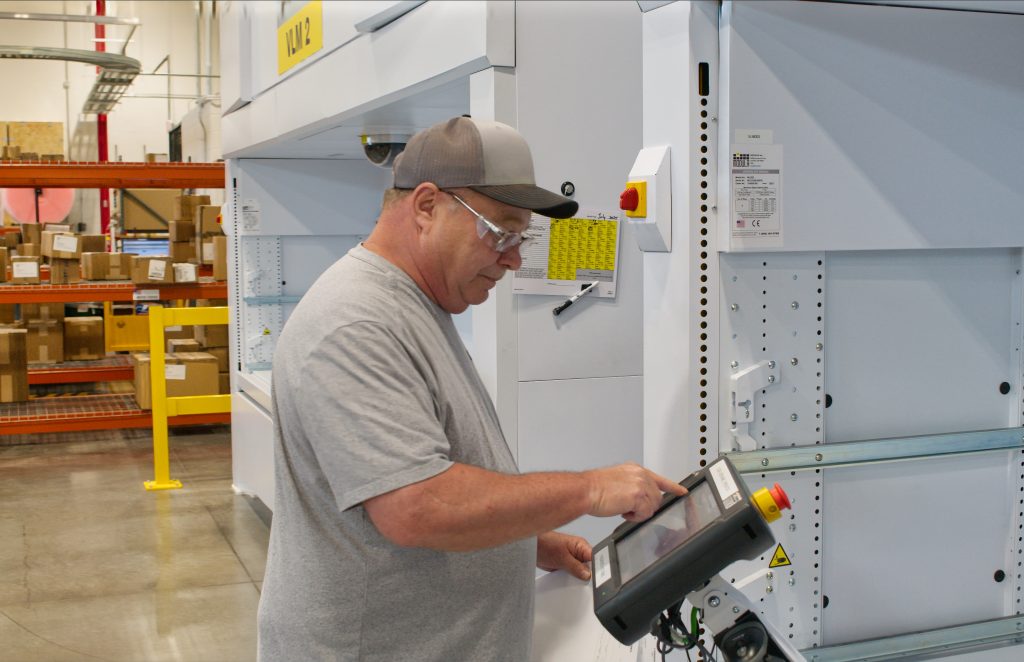

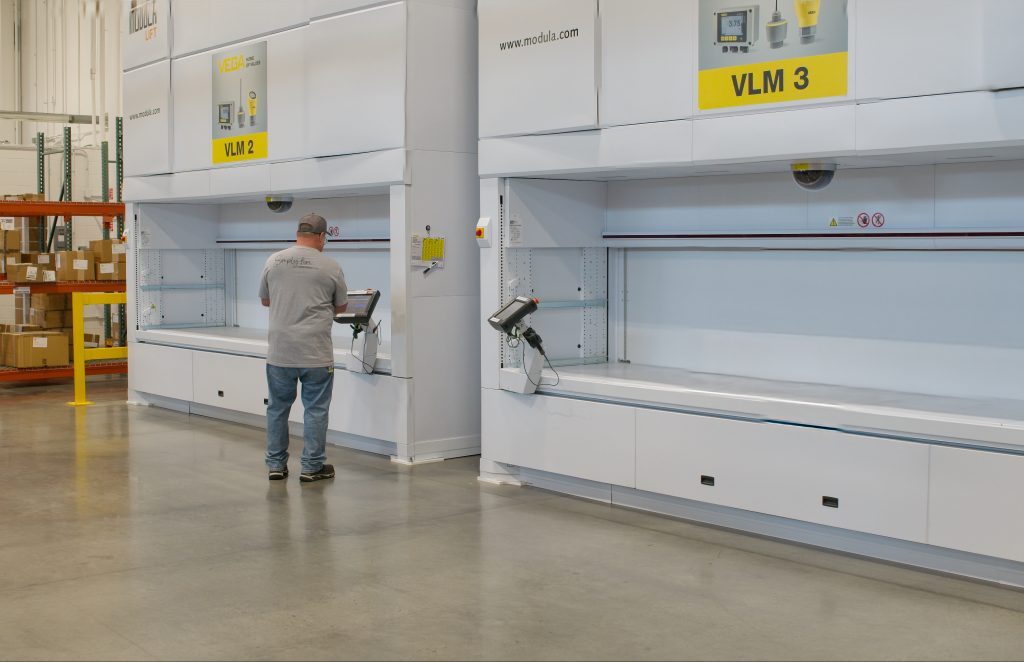
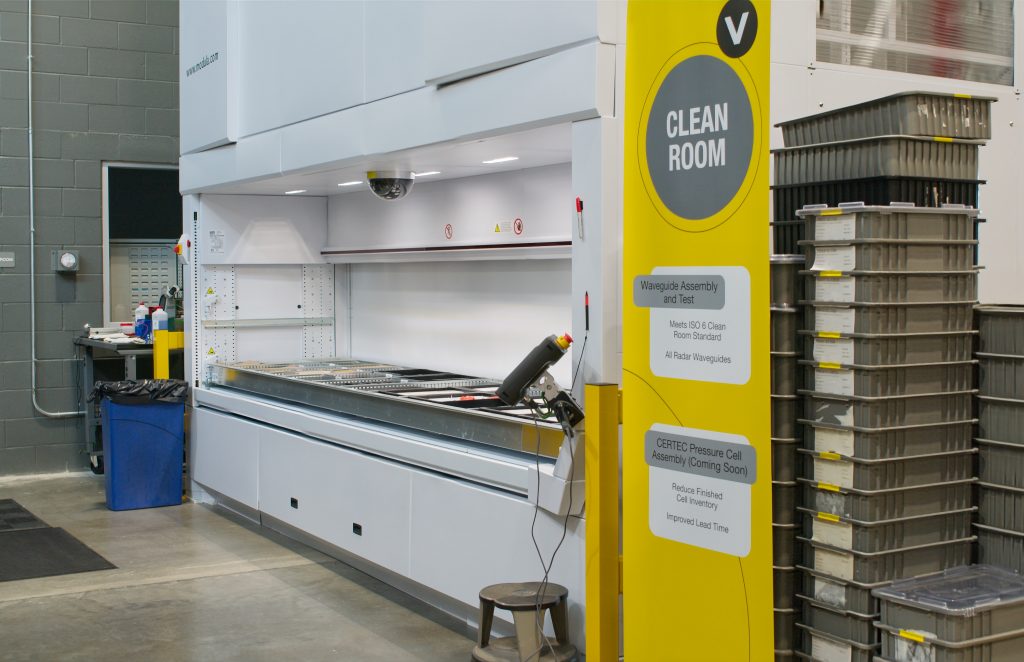