Tassalini Spa Transforms its Warehouse with Modula VLMs
Case Study Summary
Tassalini Spa, with over a century of expertise in manufacturing valves and fittings for industries like food, wine, pharmaceuticals, beverages, and cosmetics, has revolutionized its warehouse operations through automation.
With a need to organize materials based on form, quality, and appearance, Tassalini initially adopted Modula Lift units to improve space efficiency. Since then, they have expanded their use of Modula systems, including the recent addition of the Modula Slim units, to enhance operational speed, reduce errors, and ensure compliance with strict regulations. The company now boasts a total of 14 Modula units, optimizing their logistics while significantly improving efficiency.
The Challenge
Tassalini Spa, specializing in highly regulated industries faced challenges managing their inventory with traditional storage solutions. The manual process of sorting components by form, material, and quality was time-consuming. Additionally, it was prone to errors and made compliance with food contact regulations difficult.
Relying on traditional shelving also required frequent physical stock checks. This was taking up valuable resources and leading to inefficiencies in production and fulfillment. The company needed a solution to streamline inventory management, minimize errors, and optimize its workspace.
The Solution
To tackle these challenges, Tassalini began by installing 1 Modula Lift unit, which quickly proved successful by optimizing space and reducing picking errors. Building on that success, they expanded their automation with a total of 14 Modula units: 5 Modula Lift units and 9 Modula Slim units.
The compact design of the Modula Slim units allows multiple machines to operate simultaneously. This setup enables several operators to work at once, significantly boosting productivity.
The Modula WMS provides real-time tracking of stock levels and locations. This feature eliminates the need for regular inventory checks and greatly reduces discrepancies. This precision helps avoid overproduction, saving both time and money.
Operators now use a user-friendly Copilot interface with a touchscreen to streamline the retrieval process. The alphanumeric LED bar directs them to the correct items, showing precise quantities and locations, which ensures accuracy and efficiency in picking. This system also allows flexibility in staffing, as any operator can use the units without needing specialized training.
The implementation of Modula units also allowed Tassalini to reorganize its production floor. By centralizing storage in vertical modules, they saved considerable space that was previously occupied by traditional shelving, paving the way for new production lines.
Tassalini Spa Case Study – Key Features:
- Space Optimization: 14 Modula units, including 5 Lift and 9 Slim models, drastically reduced the warehouse footprint by utilizing vertical storage.
- Enhanced Efficiency: Operators retrieve materials quickly using the LED bar and Copilot interface, which minimizes errors and boosts picking speed.
- Real-Time Inventory Management: The Modula WMS tracks stock levels and locations precisely, eliminating the need for manual inventory checks.
- Compliance with Regulations: Accurate material management ensures compliance with food contact regulations, crucial for Tassalini’s industries.
- Flexibility and Scalability: Modula’s modular design allowed Tassalini to start with one unit and scale to 14 over time, supporting their growth seamlessly.
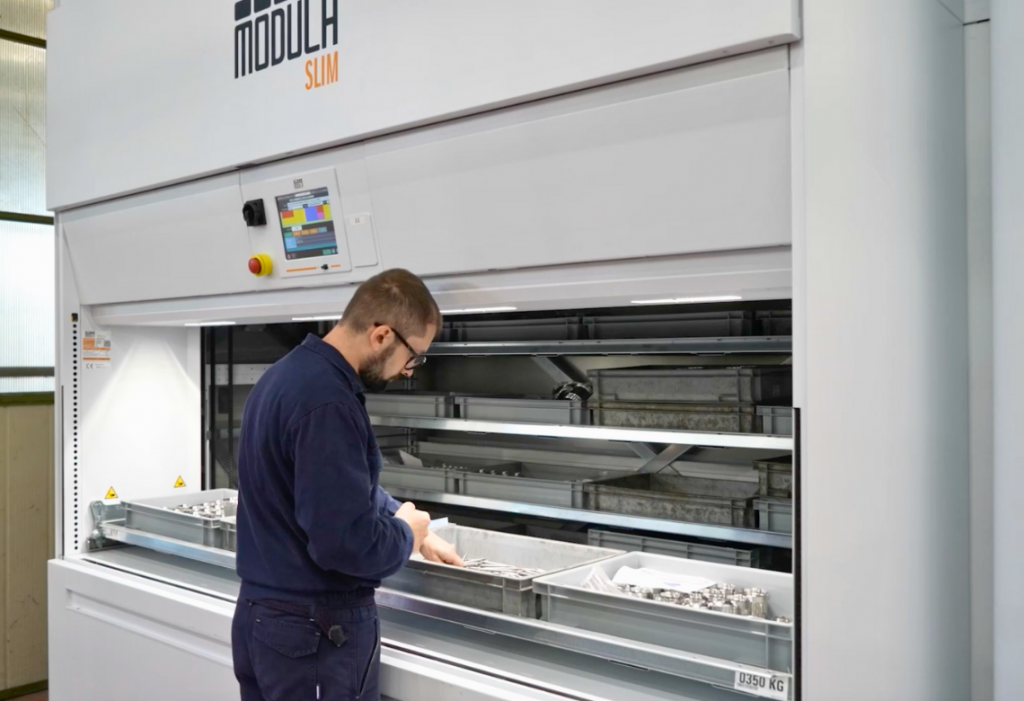
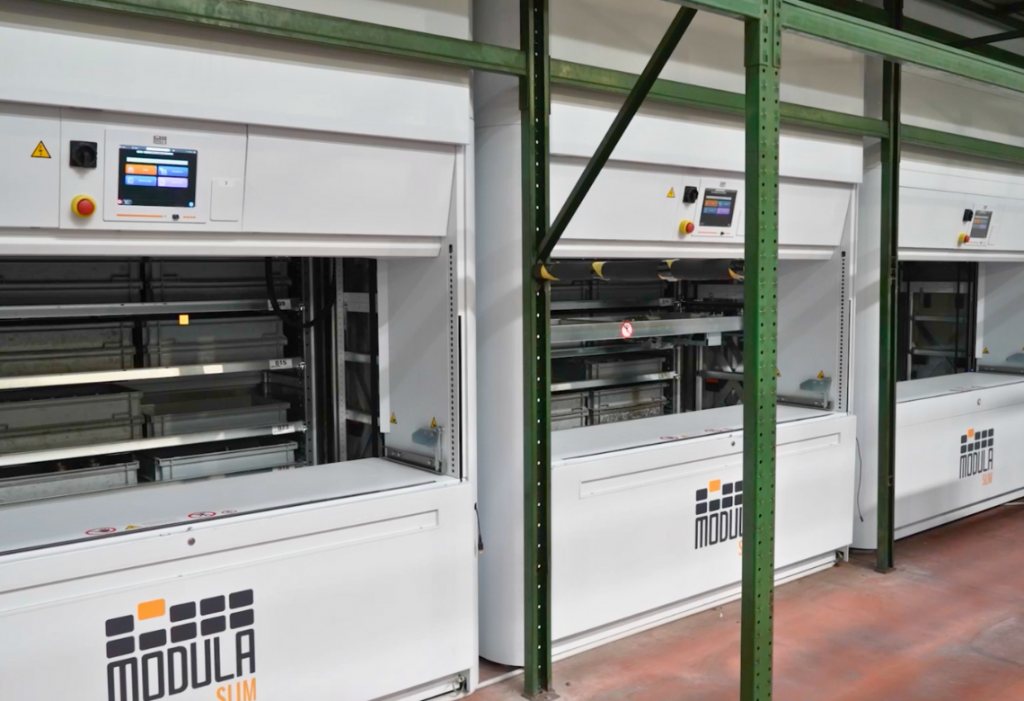
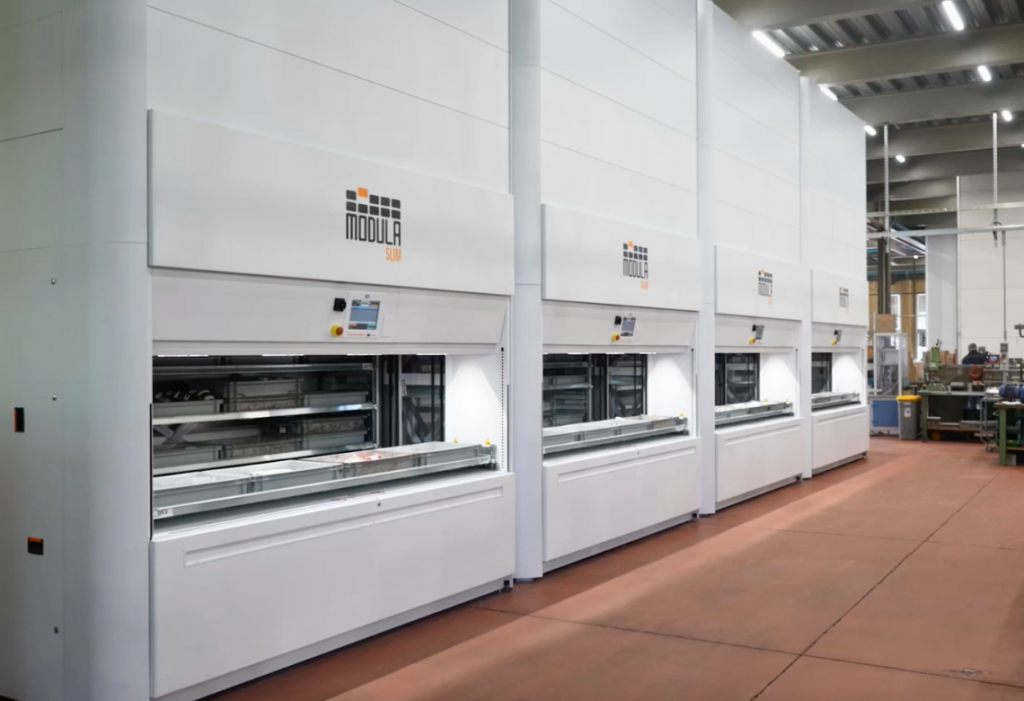
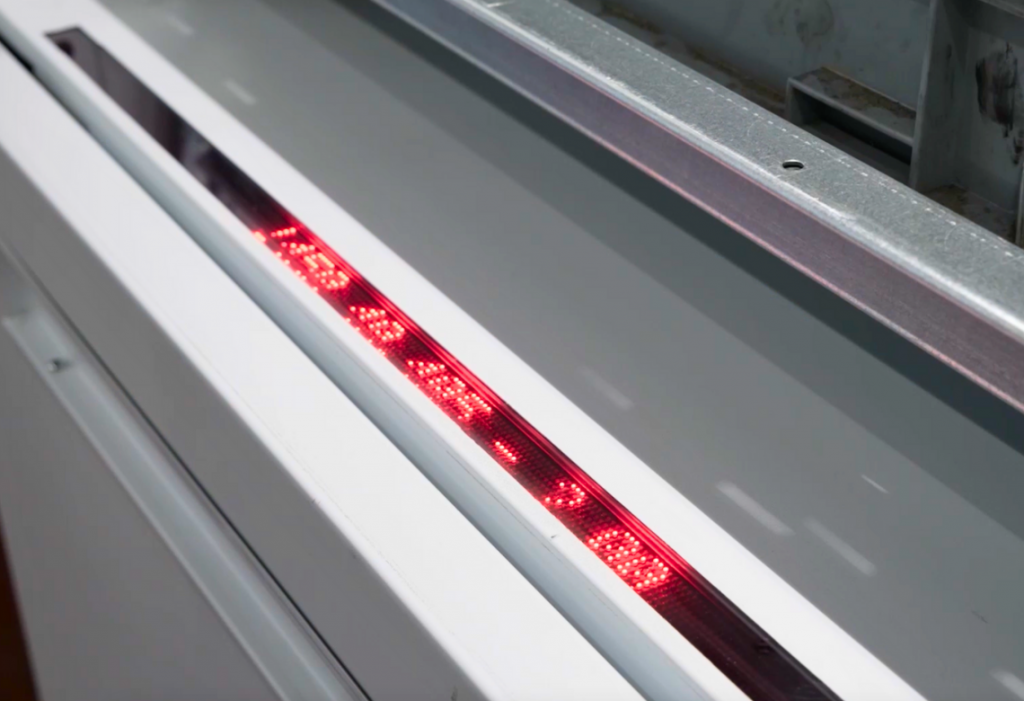
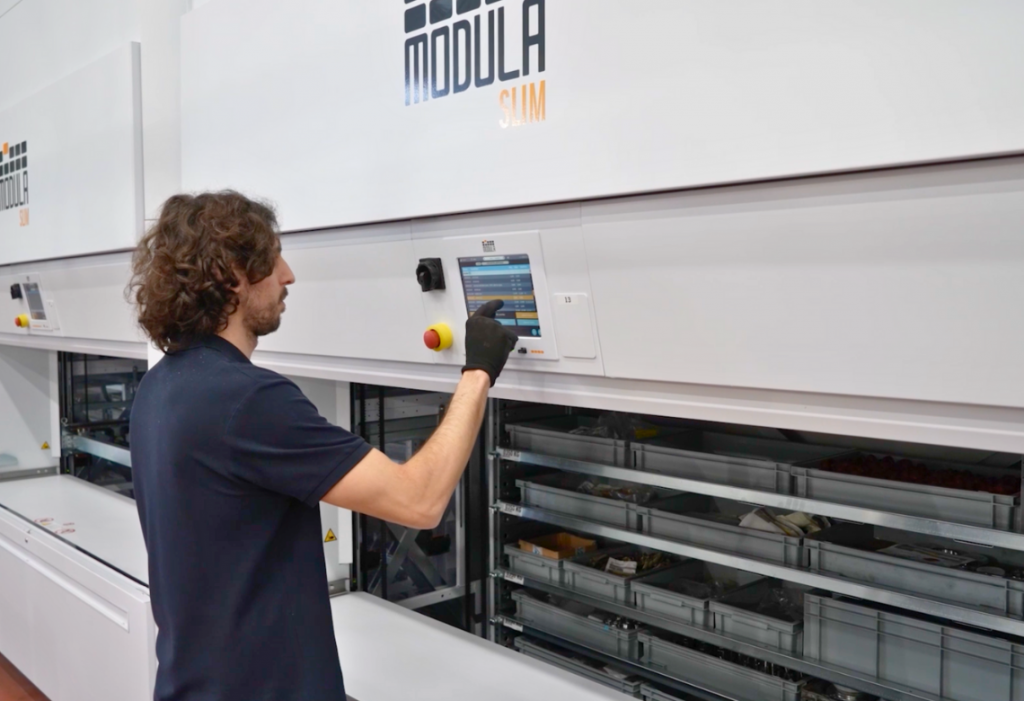