South Coast Controls Optimizes Production with Modula Vertical Lift Modules
Case Study Summary
The Challenge
With products stored on traditional racking systems within a 6,000-square-foot facility, South Coast Controls needed a solution to optimize its storage space and enhance its inventory management processes. The company faced the prospect of either purchasing additional real estate at a significant cost or finding a more cost-effective solution to accommodate its growing inventory.
The Solution
Recognizing the need for a more efficient storage solution, South Coast Controls invested in 2 Modula Vertical Lift Modules with integrated Modula WMS software. These automated storage systems allowed the company to consolidate its inventory within a smaller footprint while improving security and accessibility. With the ability to securely inventory products and restrict access to authorized personnel, the Modula systems provided enhanced control over inventory management processes.
Since implementing the 2 Modula VLMs, South Coast Controls has experienced significant improvements in productivity and efficiency. With all inventory stored in one central location, the company has reduced the risk of material loss and minimized downtime associated with searching for items. The Modula system has become an invaluable tool in streamlining operations, providing a substantial return on investment and positioning South Coast Controls for future growth.
“We would definitely recommend Modula units to another company whether they are looking to save floor space, or they are looking to save time pulling and picking parts. It’s been a huge help.”
Harry Ellis III – President of Coast Pneumatics
Key Features of the South Coast Controls Case Study:
- Space Optimization: The compact footprint of the Modula VLMs allowed South Coast Controls to store approximately $2.5 million worth of inventory within just 308 sq.ft2, maximizing storage capacity and minimizing floor space usage.
- Improved Efficiency: By centralizing inventory storage, the Modula system streamlined the retrieval process, reducing downtime and increasing productivity.
- Enhanced Security: The ability to restrict access to inventory until it was ready for use provided added security and accountability.
- Operator-Friendly Design: Quick and easy training for employees ensured seamless integration of the Modula system into daily operations.
- Responsive Support: With a dedicated local support team, South Coast Controls received timely assistance in resolving any technical issues, minimizing downtime, and optimizing system performance.
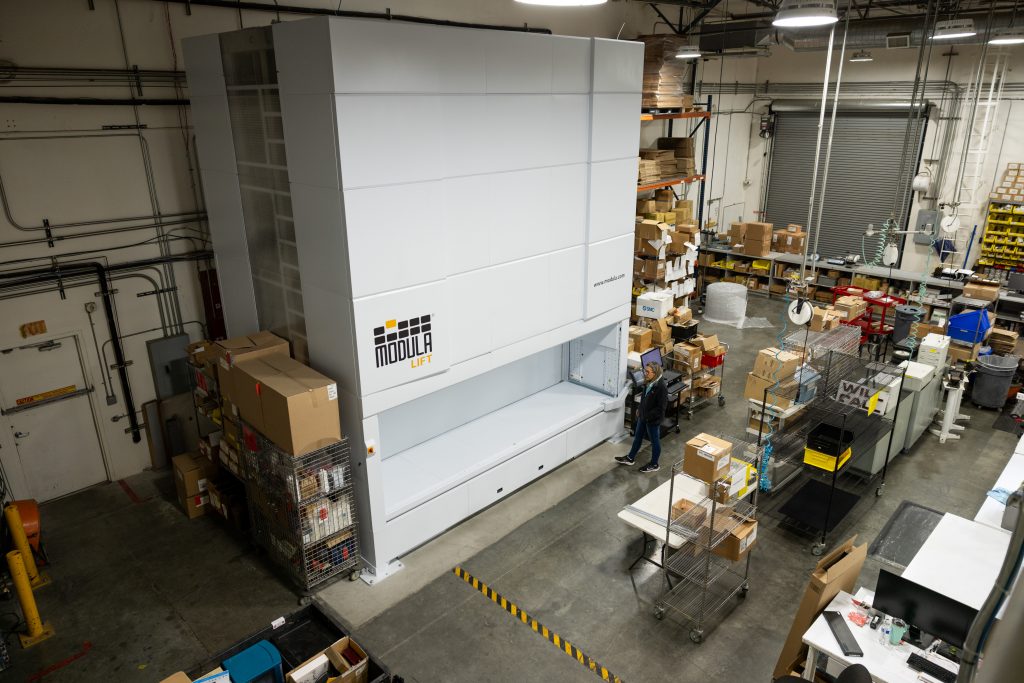
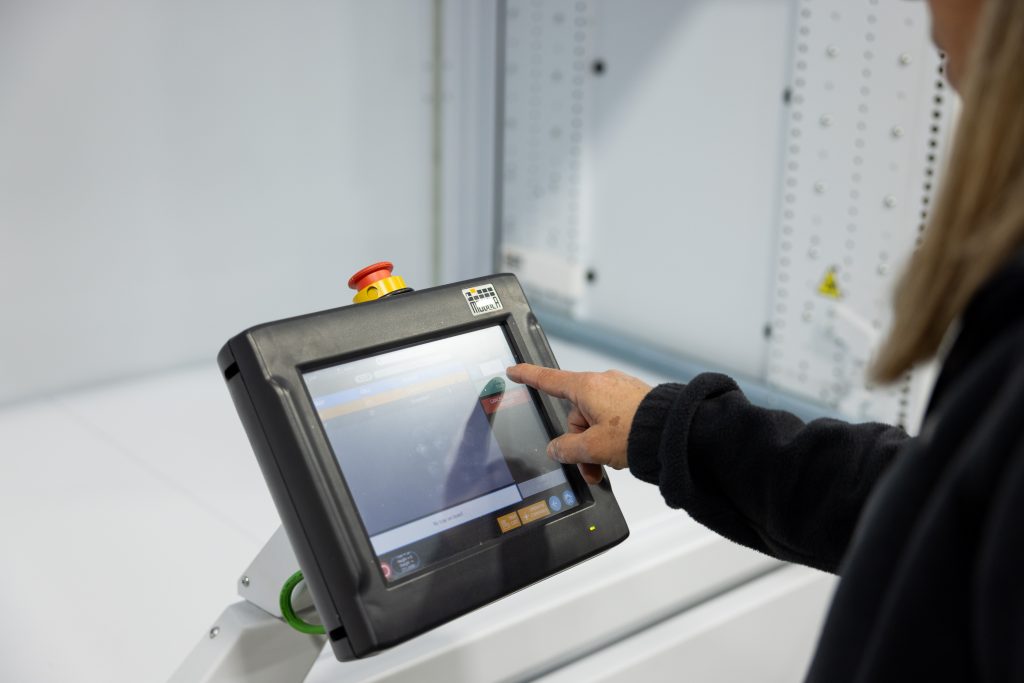
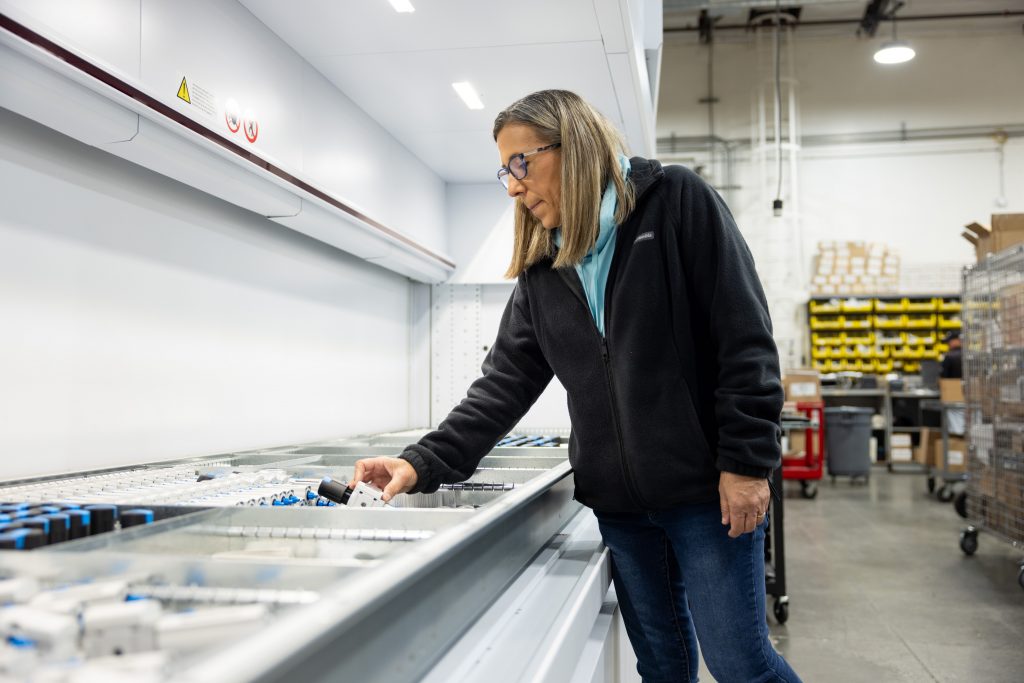

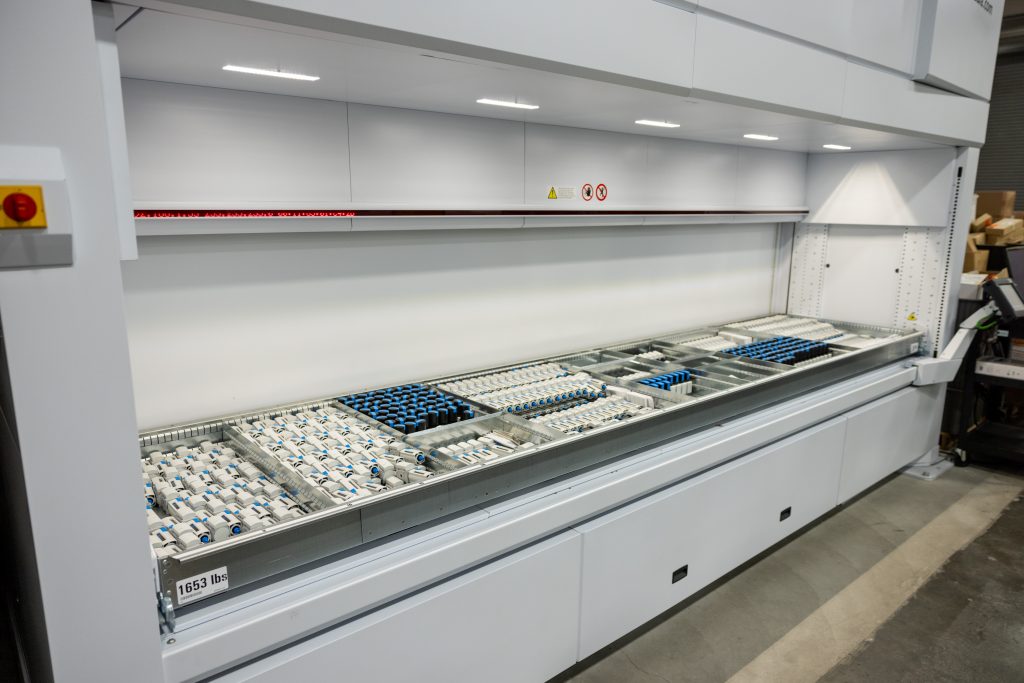