GAI Automates Material Handling and Enhances Efficiency with Modula VLMs
Case Study Summary
GAI, a family-owned bottling equipment manufacturer, faced logistical challenges in managing their expanding product range and optimizing after-sales service. By integrating 20 Modula vertical lift modules connected to a stacker crane and AGV shuttles, GAI has completely automated their material handling. This comprehensive automation has revolutionized their logistics operations, improved efficiency, and enhanced real-time inventory control. The transformation has enabled better responsiveness in assembly and service operations.
The Challenge
Founded in 1946, GAI is a family-run company specializing in high-quality bottling equipment. Over three generations, the product range expanded to include sparkling beverages, spirits, oily liquids, wines, beers, and even cans. This growth required substantial investments in logistics to optimize production and better manage service and after-sales support. Previously, the company relied on the expertise of warehouse staff to manually retrieve materials from shelves and supply them to assembly stations, which was time-consuming and inefficient. As the product range grew, GAI needed a more efficient system to handle a large variety of components and maintain real-time inventory control.
The Solution
To address these challenges, GAI implemented Modula vertical lift modules several years ago, which marked a significant shift in their logistics approach. The Modula systems delivered materials directly to the operators, counted, organized, and labeled, which required a change in mindset from manual retrieval to automated delivery. The number of Modula units has grown year by year, enhancing the efficiency of their logistics operations.
In 2015, GAI further integrated these Modula systems with a stacker crane to store and handle pallets, allowing smaller items to be stored in the Modula units while larger, heavier items were managed by the stacker crane. Thanks to Modula WMS, these systems communicate through an interface that exchanges data automatically, integrating seamlessly with GAI’s management software. This integration provided real-time control over stock levels and the flow of items in and out of the warehouse.
The material retrieval process evolved with the adoption of preparing necessary materials for assembly in advance. Office colleagues create picking lists, which are processed by the Modula systems, systematically distributing materials onto picking carts. The warehouse team then retrieves bulkier parts from the stacker crane, ensuring no production stoppages and efficient task execution.
At the beginning of 2023, GAI added two new Modula units with larger trays to handle metal sheets and very long bars, which were previously managed with conventional shelving. This allowed for better management of picking operations and improved responsiveness in assembly service.
Today, GAI operates with 20 Modula Lift units, including 16 MX75, 2 MX75D, and 2 MX1000DD units, alongside the stacker crane and AGV shuttles. This comprehensive system ensures materials move efficiently toward operators, perfectly labeled, precise, and tidy, significantly enhancing GAI’s logistics and production capabilities.
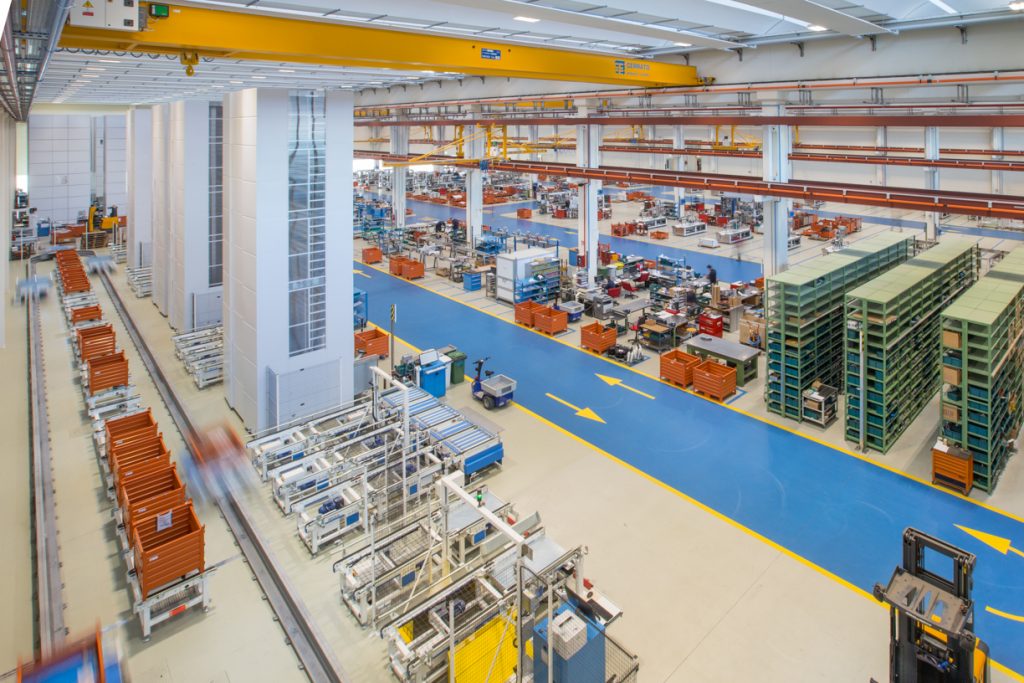
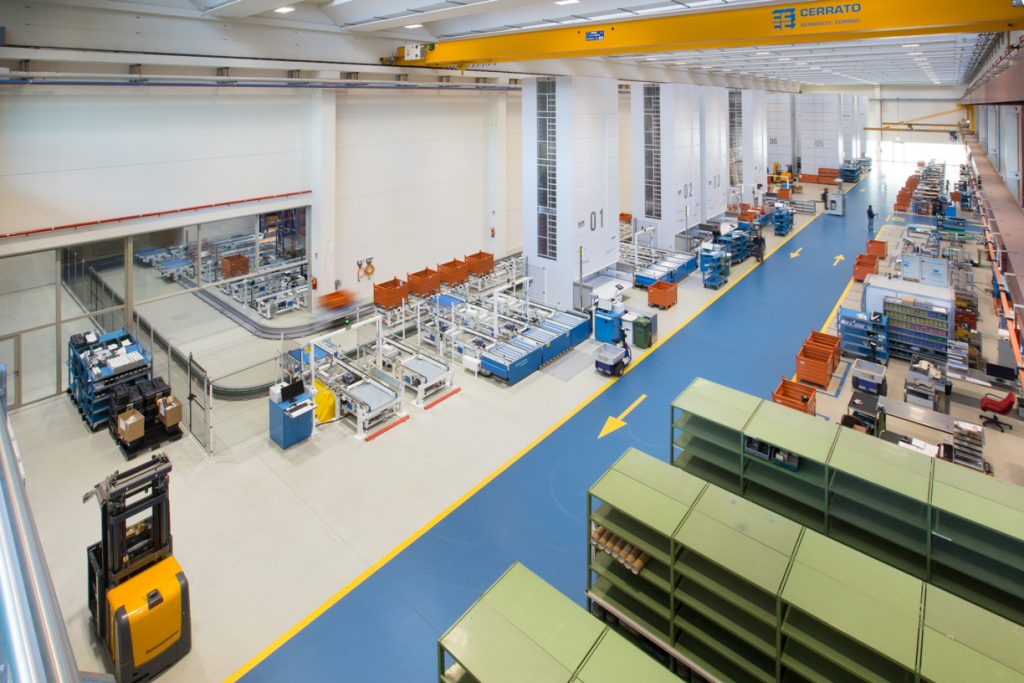

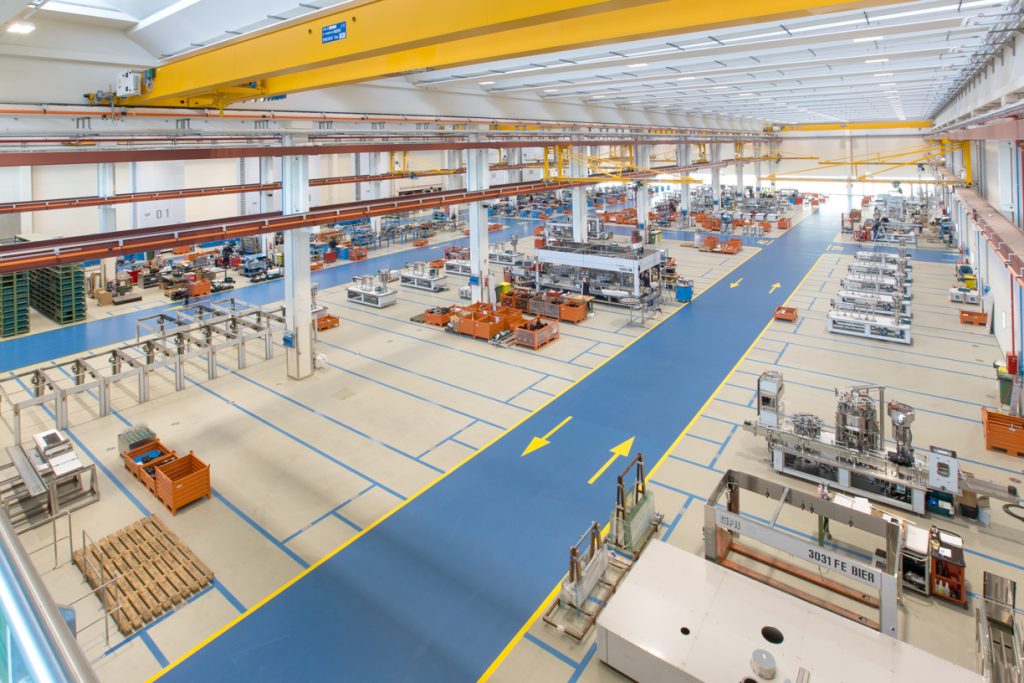
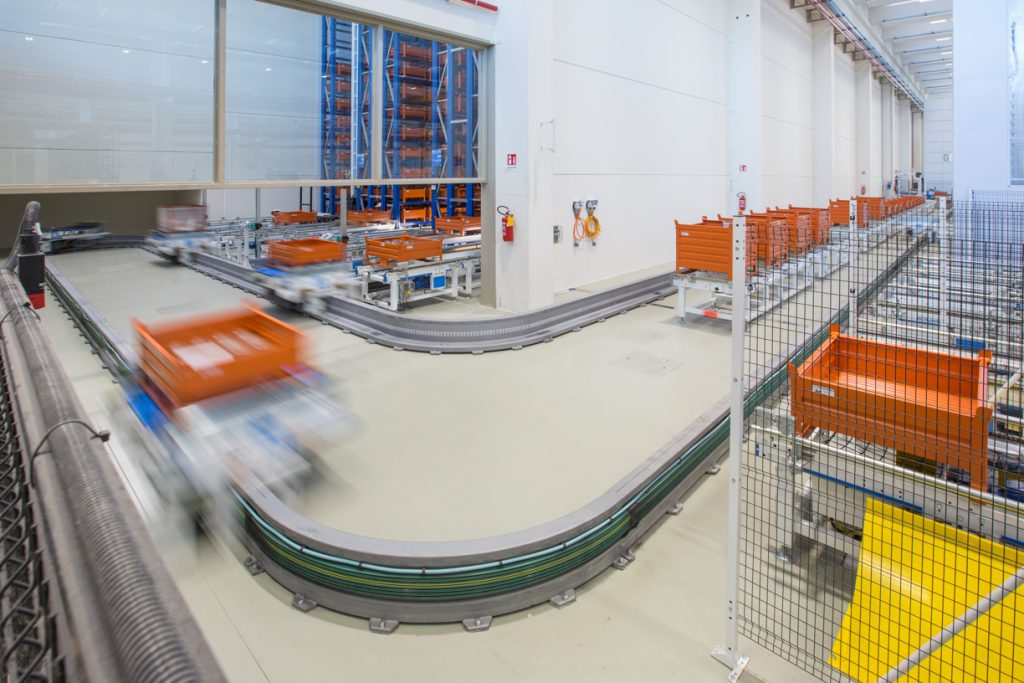
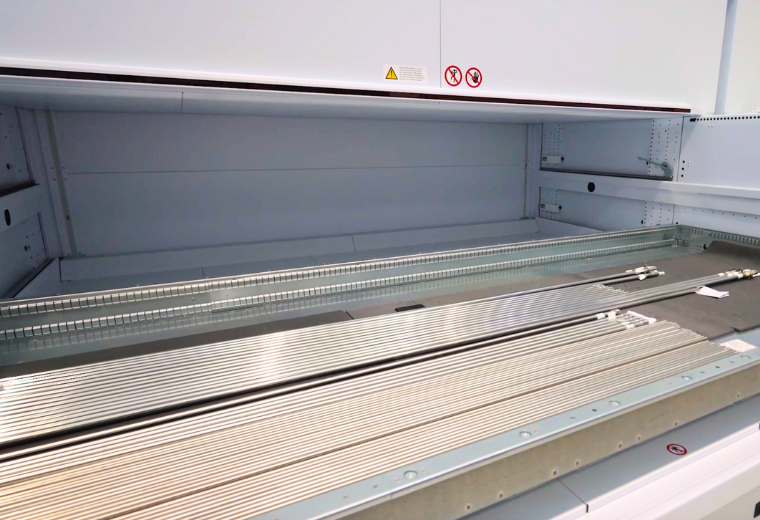
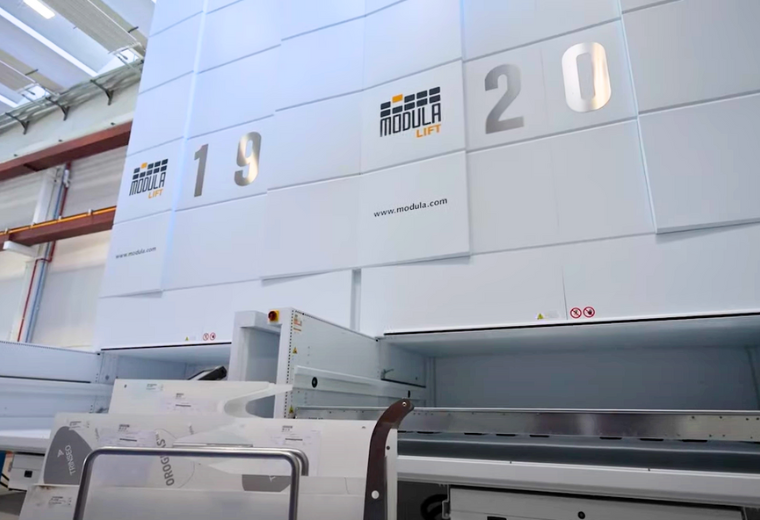