Farmaenlace Optimizes Pharma Distribution with Modula Vertical Lift Modules
Farmaenlace Case Study Summary
Farmaenlace is a national pharmaceutical distributor committed to efficiency, safety, and precision in every step of its logistics chain. Operating out of a centralized distribution center, the company has significantly improved productivity and ergonomics by integrating two Modula Lift ML25D units. Each unit is 23.29 feet high and equipped with 45 trays, a laser pointer, an alphanumeric LED bar, and a sliding console. This implementation allowed Farmaenlace to reclaim more than 6,000 square feet of warehouse space while boosting order preparation efficiency and reducing operator fatigue.
The Challenge
Before adopting Modula systems, Farmaenlace relied on traditional picking methods that required large storage areas and intensive manual labor. Operators covered long distances between 260 and 490 feet per task to locate and retrieve products. This not only slowed down fulfillment but also caused physical strain on employees.
Storage inefficiency was another major concern. The picking area previously consumed approximately 7,750 square feet. Managing 4,000–5,000 SKUs daily across 130 order lines required up to 16 people to handle 500–600 tasks per shift. This model could not scale sustainably or guarantee accuracy as demand increased.
The company needed a solution that would streamline operations, reduce errors, improve employee working conditions, and maximize the use of space within the distribution center.
The Solution
To address these challenges, Farmaenlace implemented two Modula Lift ML25D vertical lift modules. Each unit is 23.29 feet high with 45 trays and features an Internal Dual Delivery Bay, allowing two trays to be presented simultaneously to reduce picking time.
To further optimize accuracy and speed, the units are equipped with a laser pointer, an alphanumeric LED bar, and a user-friendly sliding console (Co-Pilot). These tools guide operators to the correct item and quantity while eliminating guesswork.
In addition, the Modula units are integrated with a Put-to-Light system, enabling the preparation of 40 orders per section simultaneously. The system guides operators through visual cues, reducing the likelihood of picking errors.
The impact has been substantial.
The new setup enables picking operations to be completed within a compact area of just 43 to 110 square feet, drastically reducing operator movement and physical strain. As a result, the same volume of work that previously required 15–16 employees is now managed by only two operators.
Modula also significantly improved storage efficiency: medium- and low-rotation items, totaling 1,087 SKUs, are now handled within a vertical footprint of just 1,720 square feet, compared to 7,750 square feet used previously.
Thanks to this automation, Farmaenlace maintains a fast and accurate picking process, completing up to 560 operations daily and preparing 40 orders per Modula section. Replenishment workflows have also been streamlined: items are requested from the back storage area and stocked directly into the Modula units, ready for picking
Operators now benefit from reduced walking distances, improved task ergonomics, and an intuitive system that simplifies training and execution. Overall, Modula has helped Farmaenlace boost productivity, improve working conditions, and optimize space usage in a demanding pharmaceutical environment..
Key Benefits Highlighted in the Farmaenlace Case Study:
- Scalability: The Modula system easily adapts to future growth without requiring additional floor space.
- Space Optimization: The warehouse footprint for picking has been reduced by nearly 80%, from 7,750 to just 1,720 square feet.
- Increased Productivity: From 15–16 employees to just 2 for the same order volume. The system processes approximately 560 operations per day across 130 order lines.
- Improved Ergonomics: Walking requirements cut by over 80%, significantly reducing fatigue, from up to 490 feet to just 43 square feet of movement per task.
- Order Accuracy: Laser guidance and put-to-light systems ensure precision.
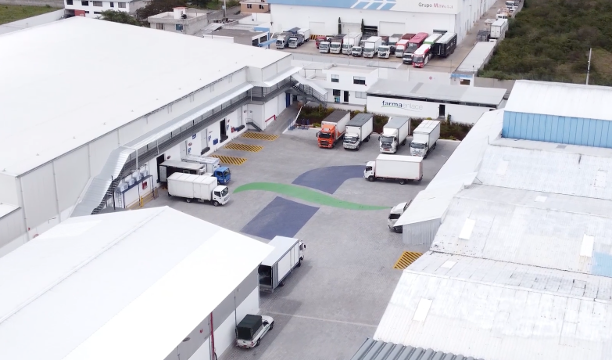
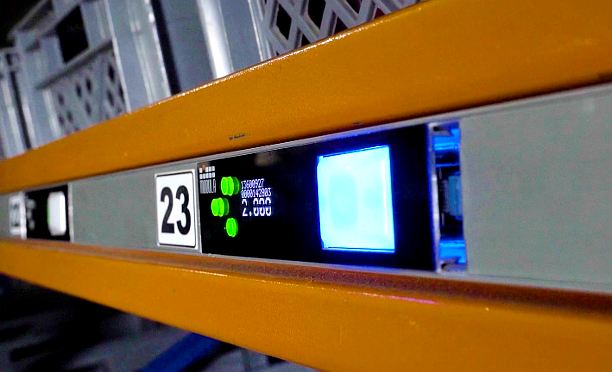
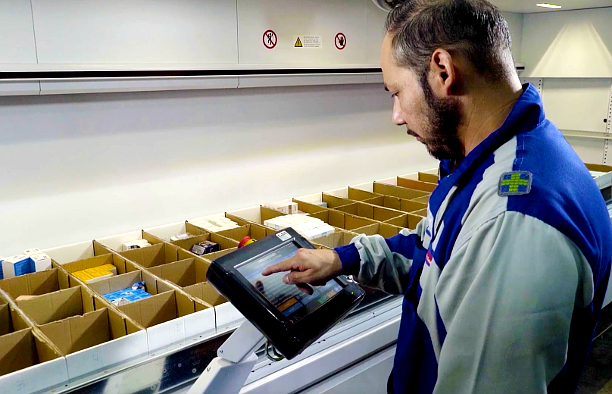
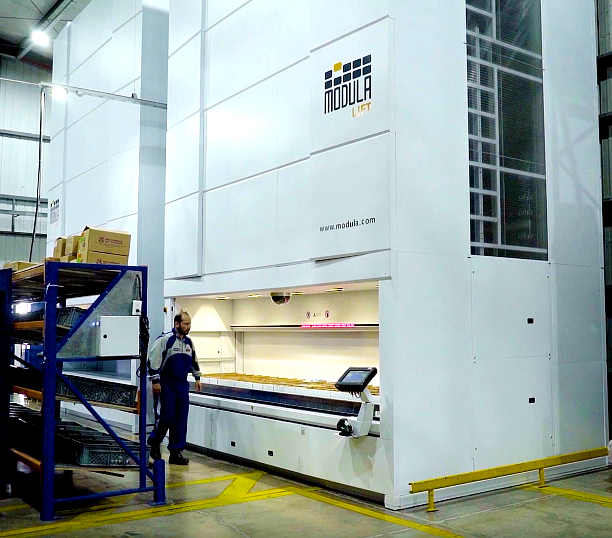
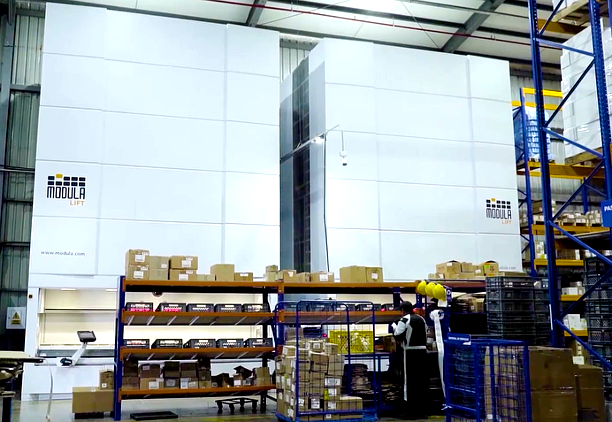