Order Pickers vs. Vertical Lift Modules: Which Is Better?
Order pickers and vertical lift modules (VLMs) are machines used to retrieve items in the warehouse.
However, they differ in terms of components, operational mechanisms, and methods of storing inventory.
We’ll compare order pickers vs. vertical lift modules to help you make an informed decision about which system best suits your warehouse needs. Optimize storage, improve picking accuracy and boost employee safety with the right solution.
What Is an Order Picker?
An order picker, also known as cherry picker or picker lift, is a human-operated machine that can perform different warehouse tasks such as retrieving, handling and transporting inventory from point A to point B.
These machines lift operators to the level of the racks where goods are stored, allowing warehouse employees to pick the specific products needed to fulfill orders, without the need to bring the entire pallet or box down to the floor.
Order pickers are useful in environments in which goods are stored at multiple levels and in different configurations, as they provide an efficient way to access goods from the ground level to high shelves. These machines help reduce the need for manual lifting and climbing.
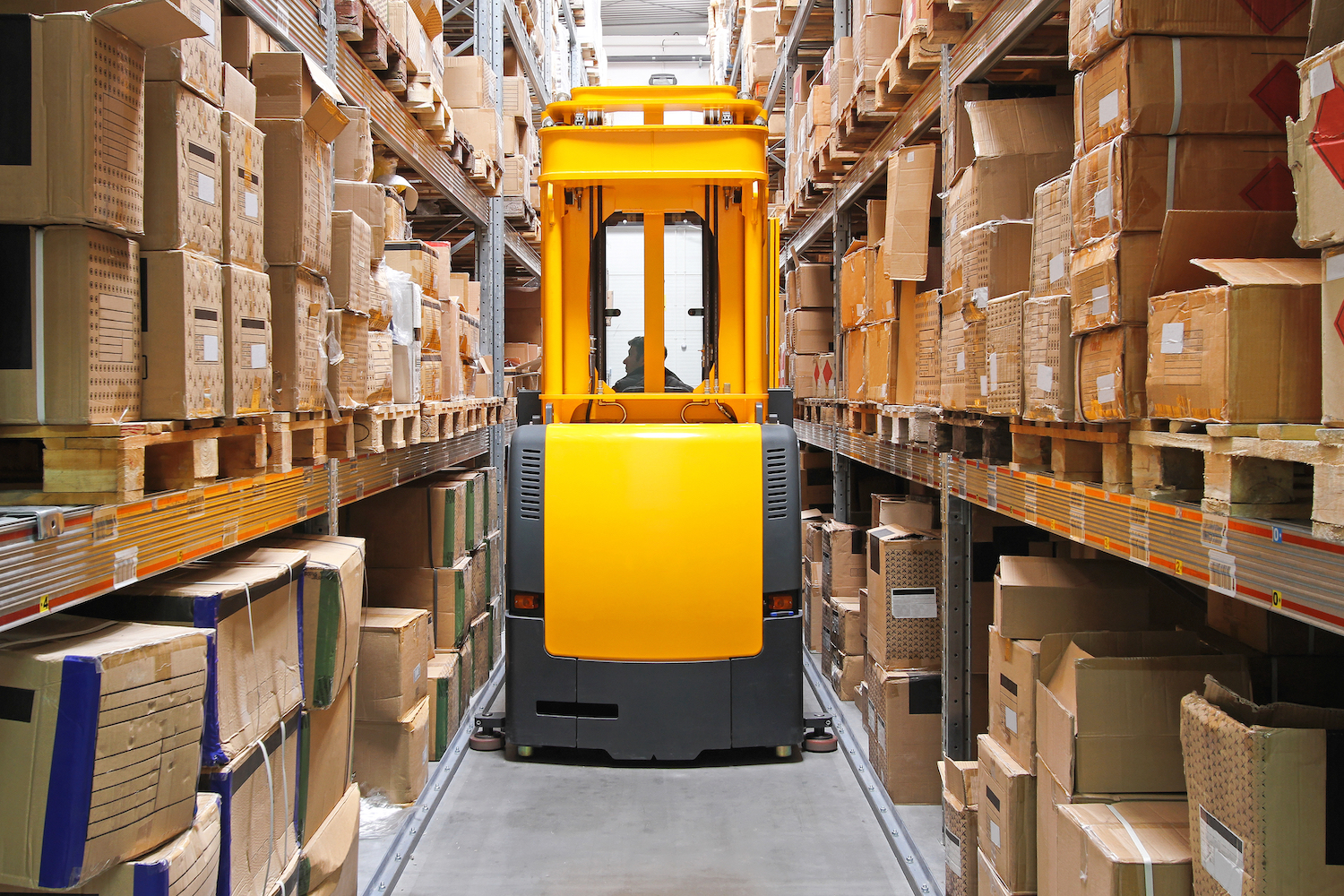
Types of Order Pickers
Order pickers can be grouped into four main types, including:
- Ground-level pickers: These machines are designed for picking items at ground level or on the first level of racking units. They are typically manual or semi-automated and are ideal for areas where goods are stored at reachable heights.
- Low-level pickers: These machines are built for selecting items at lower shelf levels, usually up to a height of around 2.5 meters. They are often electrically powered and are suitable for picking smaller items. Operators can typically ride on these pickers to move quickly along warehouse aisles.
- Mid-level pickers: These machines are designed for reaching items stored at medium heights, mid-level pickers can access shelves up to about six meters high. They usually feature a rising platform where the operator can stand and drive the picker to the desired location. These are more advanced in terms of control and safety features.
- High-level pickers: These are used for picking items from high storage areas, reaching up to 12 meters or more. They are equipped with a secure, enclosed platform for the operator and are essential in warehouses with high-stacking shelves. These pickers often have advanced safety features and require specialized training to operate.
What Are Vertical Lift Modules?
Vertical lift modules (VLMs) are automated storage and retrieval systems (ASRS) that deliver inventory directly to the warehouse employee, following the goods to person principle.
Unlike an order picker, a vertical lift module operates like a vending machine, where goods can be retrieved without moving everything inside.
When a warehouse operator requests an SKU, an extractor gathers individual trays from the machine, then delivers it to the warehouse operator at a comfortable height.
Order Pickers vs. Vertical Lift Modules
While both order pickers and vertical lift modules provide their own sets of advantages in automated storage solutions, VLMs are the better option for several reasons.
Space Utilization
A vertical lift module makes the most out of your existing space when compared to an order picker.
Order pickers can navigate through narrow aisles that are as small as 66 inches wide using special guidance mechanisms. However, when considering multiple aisles, this can lead to a significant amount of unused horizontal and vertical storage space.
On the other hand, a vertical lift module can optimize both horizontal and vertical space in a warehouse. It takes up less space than traditional shelving systems, potentially reducing your facility’s storage footprint by up to 90%.
It allows for more efficient use of warehouse space as it stores items in a compact, vertically stacked manner. This helps free up areas for other operations or additional storage, such as areas for quality assurance.
Storage
A vertical lift module offers more storage capacity compared to an order picker.
And while an order picking forklift can reach impressive heights of up to 32 feet above the floor, a vertical lift module can store goods more than 46 feet.
Vertical lift modules are ideal for picking individual parts as needed. They can hold a great number of items — both by quantity and weight — on their internal shelves, providing more storage flexibility.
Productivity
A vertical lift module allows your warehouse operators to perform more pressing tasks than an order picker.
For example, when using an order picking forklift, your warehouse operator must drive the machine from aisle to aisle. At each stop, they have to raise the forklift to get the item, place it in a storage area, then lower the forklift before moving to the next item.
This process can be slow, especially when operators need to do split-case picking — also known as piece picking — from each shelf.
As they move from shelf to shelf, they have to reduce their speed to avoid hitting people walking down the aisles. At best, this results in a throughput of 30 to 50 items per hour.
On the other hand, a vertical lift module can significantly increase efficiency, as it has picking speeds of 300 lines per hour.
It retrieves items automatically and delivers them directly to your warehouse operator, eliminating the need to drive back and forth between shelves. This not only speeds up the picking process but also reduces the risk of accidents in the aisles.
As a result, a vertical lift module can often handle a much higher throughput than manual order pickers.
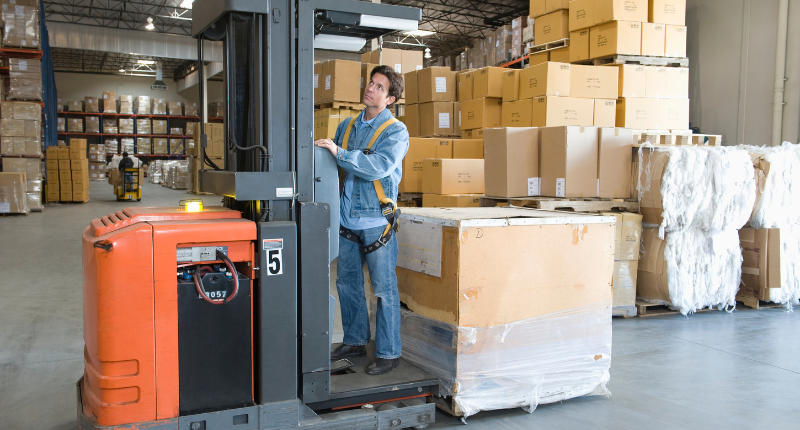
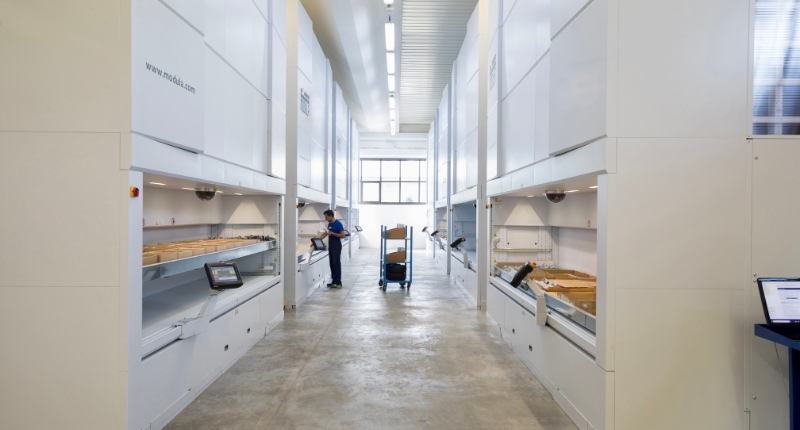
Employee Safety
A vertical lift module provides a more ergonomic work environment when compared to an order picker.
Warehouse employees who operate order pickers can encounter safety risks, as they often work at heights and in tight spaces. This environment increases the chance of falls or collisions, especially if the workers don’t follow the proper safety measures.
In addition, it’s physically demanding to repeatedly retrieve boxes weighing up to 60 pounds, which can lead to injuries, such as back strains or a herniated disc.
On the other hand, a vertical lift module can help your warehouse employees stay safe on the job by eliminating the need to reach high and low areas. This automated system retrieves and delivers items at an easily accessible height, reducing the risk of falls or strains associated with manual picking.
The Ideal Alternative To Order Pickers: Automated Storage Solutions at Modula
Modula is the leader in manufacturing automated warehouse storage solutions in the United States. Modula’s VLMs can be ordered and set up by Modula specialists much more rapidly. If you need training and service, Modula has a team of experts throughout North America, ready to help at a moment’s notice.
Whatever your needs, there’s a Modula Vertical Lift Module that can fit your warehouse requirements.
Modula Vertical Lift Modules
Modula Vertical Lift Modules are fully automated, vertical storage systems designed to minimize floor space usage while leveraging available ceiling height.
Choose from the VLM modules:
- Modula Lift: Perfect for storing industrial components and spare parts, the Modula Lift comes in various sizes and capacities to fit different inventory types.
- Modula Slim: Created for spaces with limited floor area, the Modula Slim occupies just 32.29 square feet. It’s an excellent option for optimizing storage in tight spaces.
Modula VLMs enable you to:
- Speed up picking and achieve more than 200 lines per hour
- Fully utilize your ceiling height, saving up to 90% of floor space
- Enhance order processing with a capacity of handling 140 trays per hour
- Increase employee safety by removing the need for high and low reaching
- Automatically receive goods using the intuitive Copilot controller
- Keep your inventory secure within an enclosed system
Modula Horizontal Carousel
Modula’s horizontal carousels (HCs) maximize storage, productivity and picking accuracy in low-ceiling facilities.
Modula HCs enable you to:
- Eliminate the need to travel the warehouse to find items
- Boost productivity with picking rates reaching up to 550 lines per hour
- Easily pinpoint the correct item and quantity to be picked, thanks to simple visual picking aids
- Foster safe working conditions by minimizing physical exertion and eliminating unnecessary movement across the warehouse
- Track item movement to ensure complete traceability of orders and real-time monitoring of stock levels
- Easily adjust shelf spacing to accommodate different inventory
- Reconfigure the HC’s pods to meet seasonal demands
Modula Order Picking Solutions
Modula picking solutions streamline the picking process, minimizing the search time needed for picking inventory and boosting picking accuracy for both large and individual orders.
Modula picking solutions enable you to:
- Improve picking accuracy and speed using light devices that guide your warehouse operators to the right picking location
- Enhance inventory management with a comprehensive view of your current and forecasted stock
- Further drive order accuracy and efficiency when paired with our advanced automated storage solutions
Wrapping Up on Order Picker vs. Vertical Lift Module
Vertical lift modules stand out as the superior choice compared to traditional order pickers, especially in terms of space efficiency and safety. These storage solutions maximize warehouse storage by utilizing vertical space, significantly reducing the floor area required.
In addition, vertical lift modules can help improve worker safety by automating the retrieval process, minimizing the physical strain and risks associated with manual picking.
Modula provides advanced automated warehouse storage solutions designed to optimize your existing warehouse space, boost productivity and picking accuracy, and adapt to changing consumer demands.
Contact our material handling experts for advice on the best storage solutions for your warehouse. We’ll perform a thorough warehouse audit to ensure you get the most suitable solutions that fit your operational needs.